Environmental and Emission Regulations Impacting Industrial Oil-Fired Boiler Selection
In today’s industrial landscape, selecting an oil-fired boiler involves more than just focusing on capacity, efficiency, and price. Increasingly stringent environmental and emission regulations worldwide require businesses to factor in compliance with air quality standards, greenhouse gas (GHG) reduction targets, and sustainability mandates. Failing to consider these regulations during boiler selection can lead to heavy fines, legal penalties, forced shutdowns, and expensive retrofits. Therefore, understanding the regulatory environment is critical to making a smart, future-proof boiler investment.
Environmental and emission regulations impact industrial oil-fired boiler selection by setting strict limits on pollutants such as nitrogen oxides (NOx), sulfur oxides (SOx), carbon dioxide (CO₂), particulate matter (PM), and unburned hydrocarbons. Compliance affects burner design, combustion technology, exhaust gas treatment systems (e.g., scrubbers, selective catalytic reduction), fuel quality requirements, and monitoring instrumentation. Choosing a boiler that aligns with applicable local, national, and international regulations ensures long-term operational legality, energy efficiency, and environmental responsibility.
Here’s what you need to know when evaluating compliance requirements for your oil-fired boiler.
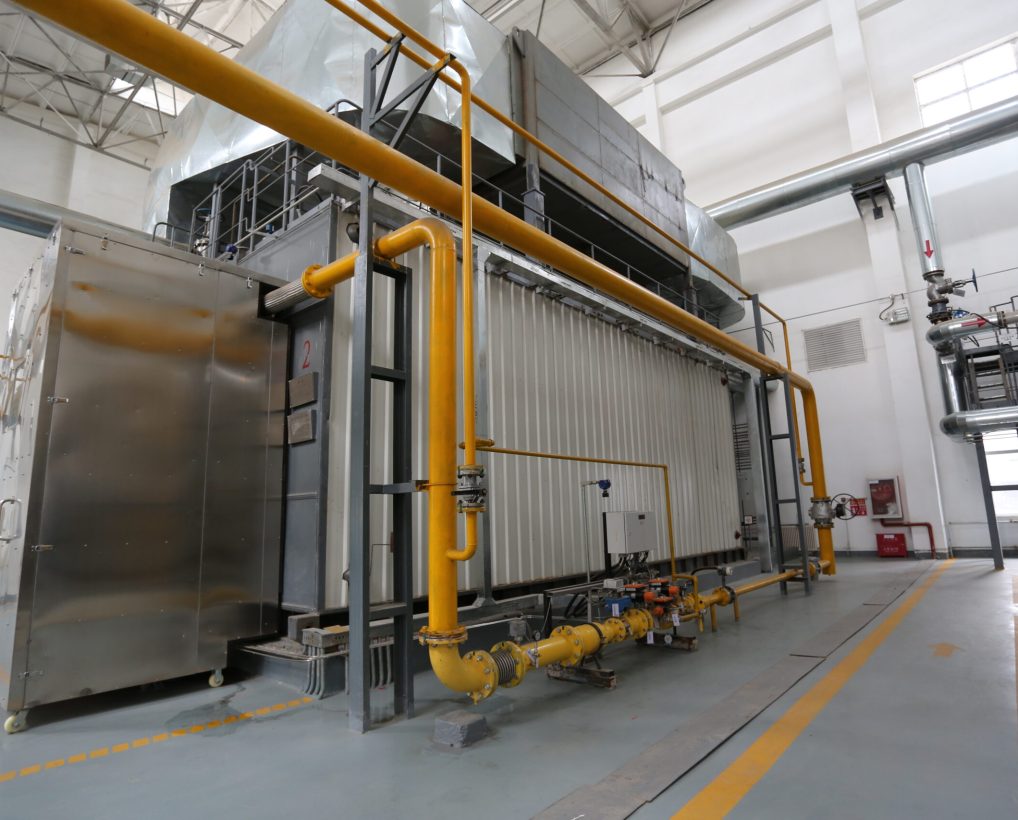
What Are the Main Pollutants Regulated for Industrial Oil-Fired Boilers?
Industrial oil-fired boilers are widely used across sectors like manufacturing, chemical processing, food production, and power generation. However, their operation generates several air pollutants that are tightly regulated by environmental authorities around the world. Compliance with these emission standards is crucial not only to avoid fines but also to protect air quality, public health, and environmental sustainability. Understanding the main pollutants and their sources allows industries to engineer proper emissions control strategies from the outset.
The main pollutants regulated for industrial oil-fired boilers are nitrogen oxides (NOₓ), sulfur dioxide (SO₂), particulate matter (PM), carbon monoxide (CO), and unburned hydrocarbons or volatile organic compounds (VOCs). Each of these emissions originates from combustion processes, fuel impurities, or incomplete combustion, and they are regulated under national and international air quality standards. Effective emissions control technologies are required to meet regulatory limits and ensure sustainable boiler operation.
Compliance starts with knowing what you emit, how it forms, and how to control it effectively.
Industrial oil-fired boilers must control emissions of NOₓ, SO₂, PM, and CO to meet environmental regulations.True
Oil combustion produces significant levels of nitrogen oxides, sulfur dioxide, particulate matter, and carbon monoxide, which must be minimized using proper combustion control and flue gas treatment technologies.
1. Nitrogen Oxides (NOₓ)
Source | Formation Mechanism |
---|---|
High flame temperatures | Thermal NOₓ formation from nitrogen in air |
Nitrogen in fuel oils | Fuel-bound NOₓ formed during combustion |
Environmental Impact:
Forms ground-level ozone (smog)
Causes respiratory problems
Contributes to acid rain
Typical Emission Limits:
Region | NOₓ Limit (mg/Nm³) |
---|---|
EU Industrial Emissions Directive | 100–200 |
US EPA (NSPS) | 115–185 |
China GB Standard | 150–300 |
Control Methods:
Low-NOₓ burners
Flue gas recirculation (FGR)
Selective Non-Catalytic Reduction (SNCR)
Selective Catalytic Reduction (SCR)
2. Sulfur Dioxide (SO₂)
Source | Formation Mechanism |
---|---|
Sulfur in fuel oils | Converts to SO₂ and SO₃ during combustion |
Environmental Impact:
Causes acid rain
Corrodes infrastructure
Damages ecosystems
Typical Emission Limits:
Region | SO₂ Limit (mg/Nm³) |
---|---|
EU IED | 35–200 |
US EPA | 26–520 (depends on fuel sulfur) |
China GB | 50–400 |
Control Methods:
Use of low-sulfur fuel oils
Flue gas desulfurization (FGD)
Dry sorbent injection (DSI) systems
Wet scrubbers (limestone, seawater)
Using low-sulfur oil significantly reduces SO₂ emissions from industrial oil-fired boilers.True
The sulfur content in fuel oil is the main determinant of SO₂ emissions; using fuels with lower sulfur percentages directly lowers SO₂ output.
3. Particulate Matter (PM)
Source | Formation Mechanism |
---|---|
Incomplete combustion | Unburned carbon particles (soot) |
Fuel impurities (ash) | Metal oxides, sulfates formed during burning |
Environmental Impact:
Penetrates lungs causing respiratory and cardiovascular diseases
Contributes to atmospheric haze
Typical Emission Limits:
Region | PM Limit (mg/Nm³) |
---|---|
EU IED | 10–30 |
US EPA | 30–50 |
China GB | 20–30 |
Control Methods:
Proper burner tuning (excess air control)
Cyclone separators
Baghouse filters
Electrostatic precipitators (ESPs)
4. Carbon Monoxide (CO)
Source | Formation Mechanism |
---|---|
Incomplete combustion | Insufficient oxygen during fuel burning |
Environmental Impact:
Toxic gas harmful to human health
Contributes indirectly to greenhouse gas formation
Typical Emission Limits:
Region | CO Limit (mg/Nm³) |
---|---|
EU (non-specific) | Typically 100–250 |
US EPA | 150 ppm (~180 mg/Nm³) |
Local regulations | Vary widely |
Control Methods:
Proper combustion air management (O₂ trim control)
Burner maintenance and tuning
Use of staged combustion
5. Volatile Organic Compounds (VOCs) and Unburned Hydrocarbons (UHC)
Source | Formation Mechanism |
---|---|
Incomplete vaporization or oxidation of hydrocarbons | Inefficient burner performance |
Environmental Impact:
Forms ground-level ozone
Causes smog formation
Some VOCs are toxic or carcinogenic
Control Methods:
Efficient atomization of oil
High-temperature, well-mixed combustion zones
Post-combustion oxidation catalysts (optional in sensitive zones)
Summary Table: Main Pollutants in Oil-Fired Boilers
Pollutant | Primary Cause | Environmental Effect | Typical Controls |
---|---|---|---|
NOₓ | High flame temp, fuel N | Smog, acid rain, health issues | Low-NOₓ burners, SCR, SNCR |
SO₂ | Sulfur in fuel | Acid rain, corrosion | Low-sulfur fuel, scrubbers |
PM | Unburned carbon, ash | Respiratory harm, haze | Cyclones, bag filters, ESP |
CO | Incomplete combustion | Toxicity, indirect greenhouse effect | Combustion air tuning |
VOCs/UHC | Poor combustion, fuel vapors | Smog, health hazards | Burner optimization, oxidation catalysts |
Real-World Compliance Strategy Example
Facility: Oil-fired industrial power boiler (30 TPH)
Fuel: Low-sulfur No. 2 oil (0.3% S)
Emission Controls Installed:
Low-NOₓ burners with flue gas recirculation
Cyclone + baghouse for PM control
Wet scrubber for SO₂ reduction
O₂ trim system for optimal air-fuel ratio
Outcome:
NOₓ reduced by 65%
SO₂ emissions compliant with EU IED standards
PM emissions <20 mg/Nm³
CO emissions kept under 100 ppm
Summary
Industrial oil-fired boilers must control and manage emissions of NOₓ, SO₂, PM, CO, and VOCs to meet stringent environmental regulations. Each pollutant has specific formation mechanisms during combustion and unique environmental and health impacts. Effective emission control requires fuel quality management, precise combustion control, and appropriate flue gas treatment technologies. Regulatory compliance isn’t just a legal requirement—it’s essential for sustainable operation, community health, and corporate reputation. In modern boiler engineering, controlling what leaves your stack defines your success.

How Do NOₓ, SOₓ, CO₂, and PM Emission Limits Affect Boiler Design and Selection?
Today’s industrial boiler projects must do more than simply meet production demands—they must also strictly comply with emission limits set by national and international environmental standards. Limits on nitrogen oxides (NOₓ), sulfur oxides (SOₓ), carbon dioxide (CO₂), and particulate matter (PM) are driving major changes in boiler design, material selection, fuel choices, and combustion control technologies. If emissions considerations are not integrated early into the boiler selection and engineering process, projects risk non-compliance penalties, expensive retrofits, delayed approvals, and reputational damage.
NOₓ, SOₓ, CO₂, and PM emission limits critically influence boiler design and selection by determining the required combustion technology, material choices, auxiliary systems, and even fuel types. Boilers must incorporate low-NOₓ burners, flue gas desulfurization, high-efficiency combustion, low-carbon fuels, and particulate capture systems to meet these regulations. Emission limits reshape every key decision in modern boiler projects—from basic configuration to final operational strategies.
In boiler design today, compliance isn’t an option—it’s the blueprint.
Strict emission limits for NOₓ, SOₓ, CO₂, and PM directly influence industrial boiler design and technology selection.True
Emission regulations require specific combustion technologies, flue gas treatment systems, and fuel choices, fundamentally impacting how boilers are designed and selected.
1. NOₓ Emissions and Their Influence on Boiler Design
Emission Concern | Effect on Boiler Design |
---|---|
Nitrogen Oxides (NOₓ) | Produced by high-temperature combustion |
Regulatory Limits:
EU Industrial Emissions Directive (IED): <100–200 mg/Nm³
US EPA NSPS: 115–185 mg/Nm³
Design Adjustments:
Design Feature | Impact |
---|---|
Low-NOₓ Burners | Reduce flame temperature and NOₓ formation |
Flue Gas Recirculation (FGR) | Dilutes combustion air with flue gases |
Staged Combustion/Air Staging | Controls combustion zones to limit NOₓ |
Selective Non-Catalytic Reduction (SNCR) | Post-combustion NOₓ control |
Selective Catalytic Reduction (SCR) | Deep NOₓ reduction, especially in large units |
2. SOₓ Emissions and Their Impact on Boiler Design
Emission Concern | Effect on Boiler Design |
---|---|
Sulfur Oxides (SO₂, SO₃) | Produced from sulfur in fuel oils, coal, biomass |
Regulatory Limits:
EU IED: <35–200 mg/Nm³
US EPA: Dependent on sulfur content limits
Design Adjustments:
Design Feature | Impact |
---|---|
Low-Sulfur Fuels (ULS Oil, Washed Coal) | Reduces source emissions |
Limestone Injection (CFB/FBC Systems) | Captures SO₂ in-bed |
Flue Gas Desulfurization (FGD) | Scrubbers to remove SO₂ post-combustion |
Dry Sorbent Injection (DSI) Systems | Flexible retrofit for moderate SO₂ reductions |
3. CO₂ Emissions and Their Role in Boiler Selection
Emission Concern | Effect on Boiler Design and Operation |
---|---|
Carbon Dioxide (CO₂) | Produced by burning any carbon-based fuel |
Global Context:
Global drive for carbon neutrality (Net-Zero by 2050 goals)
Regional CO₂ pricing and carbon tax systems growing
Design and Selection Responses:
Strategy | Impact |
---|---|
Choose high-efficiency boilers | Less fuel burned per ton of steam → lower CO₂ |
Switch to low-carbon fuels (natural gas, biomass) | Reduces carbon emissions intensity |
Hybrid systems (solar + biomass) | Integrate renewable sources to offset carbon |
Carbon Capture Integration (CCUS ready) | Design plants with future CO₂ capture capability |
4. PM (Particulate Matter) and Boiler Technology Implications
Emission Concern | Effect on Boiler Design |
---|---|
Particulate Matter (PM) | Solid ash, soot particles formed during combustion |
Regulatory Limits:
EU IED: <10–30 mg/Nm³
US EPA MACT standards: 30–50 mg/Nm³
Design Adjustments:
Design Feature | Impact |
---|---|
Cyclone Separators | Remove coarse particulates pre-flue gas system |
Electrostatic Precipitators (ESP) | Capture fine PM for larger systems |
Baghouse Filters | Achieve very low PM emissions (<10 mg/Nm³) |
Optimized Combustion Control | Minimize soot and incomplete burning |
Low-NOₓ burners, scrubbers, and particulate filters are critical components of modern industrial boiler designs to comply with emission limits.True
Each major pollutant requires specific combustion or post-combustion control technologies integrated into the boiler system design.
5. Real-World Example: Boiler Design Shift Due to Tight Emission Regulations
Industry: Pulp and paper mill (biomass + oil backup boilers)
Original Plan: Conventional biomass boiler with cyclone separator
Regulatory Requirement:
NOₓ < 200 mg/Nm³
PM < 10 mg/Nm³
SO₂ very low (biomass fuel)
Design Adjustments:
Installed Low-NOₓ staged combustion burners
Added baghouse filter system instead of cyclone
Installed flue gas recirculation for NOₓ suppression
Results:
Emissions well within EU IED limits
Plant received environmental certification (ISO 14001)
Improved combustion efficiency by 5%
Boiler Design and Selection Checklist for Emission Compliance
Checklist Item | Done? (✔/✖) |
---|---|
Confirm local and national emission limits (NOₓ, SOₓ, PM, CO₂) | |
Choose appropriate fuel type and quality | |
Specify low-emission combustion systems (burners, staging) | |
Integrate flue gas treatment systems as needed | |
Plan for future tightening of regulations (design flexibility) | |
Model expected emissions under all operating scenarios |
Summary
NOₓ, SOₓ, CO₂, and PM emission regulations fundamentally reshape the design, selection, and operation of industrial boilers. Combustion systems, material choices, fuel selections, and auxiliary emissions controls must be precisely engineered to meet today’s—and tomorrow’s—standards. Designing for compliance from the start avoids regulatory risks, operating inefficiencies, and costly retrofits. In the modern industrial world, a boiler isn’t just judged by the steam it produces—it’s judged by the air it leaves behind.
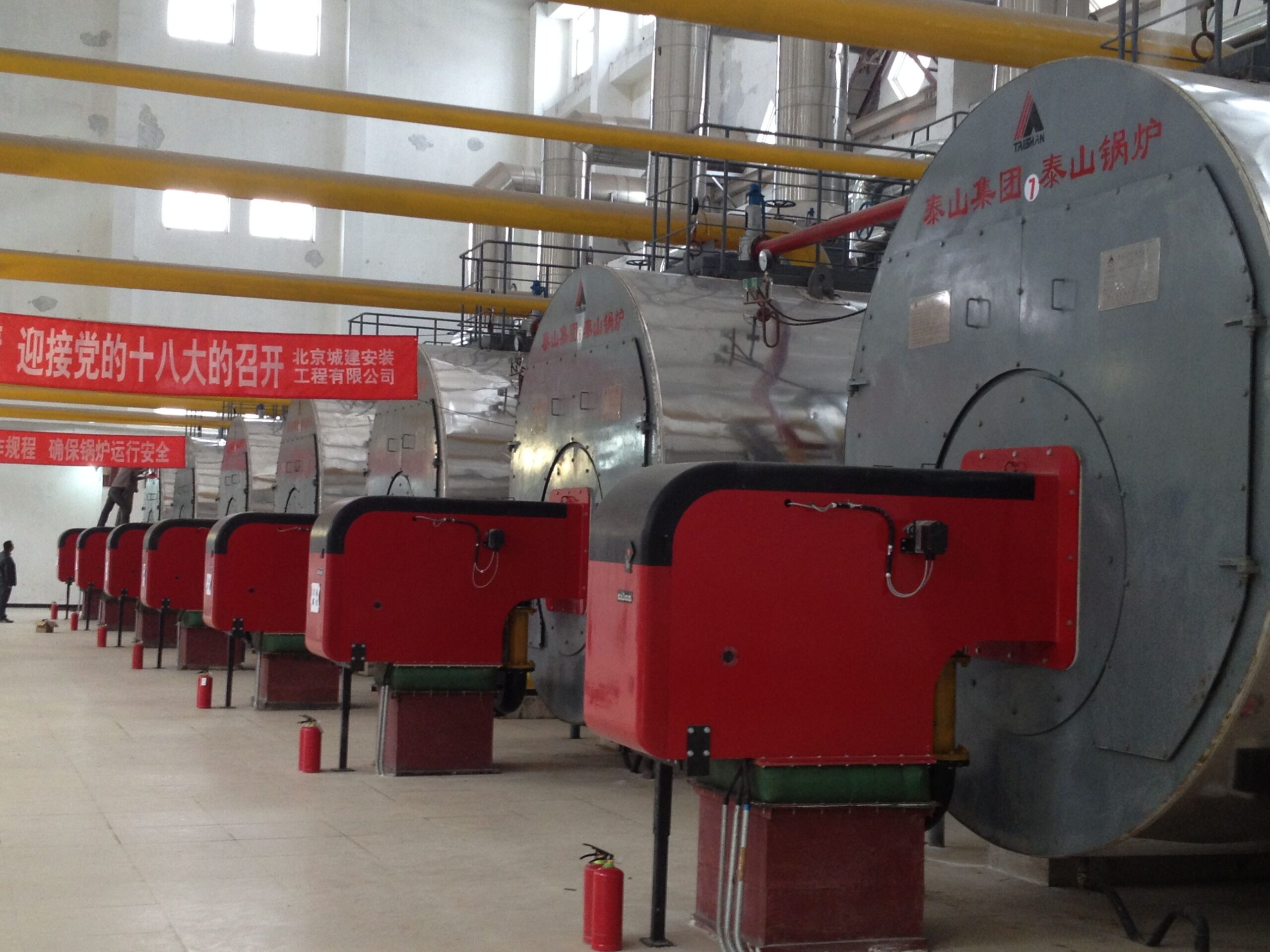
What Global and Regional Environmental Regulations Must Oil-Fired Boilers Comply With?
Oil-fired boilers are still widely used across industries for process heating, power generation, and district energy. However, they face strict environmental scrutiny due to the emissions they generate—especially NOₓ, SO₂, PM, CO, and CO₂. Around the world, global protocols and regional regulations set detailed standards for air emissions, fuel sulfur content, and sometimes greenhouse gas intensity. Industrial facilities must comply with these rules to obtain permits, avoid heavy fines, meet corporate sustainability targets, and protect their operational reputation.
Oil-fired boilers must comply with global agreements such as the Paris Climate Accord and with regional environmental regulations like the U.S. EPA NSPS, EU Industrial Emissions Directive (IED), China’s GB standards, and local emissions control acts. These regulations set limits on NOₓ, SO₂, particulate matter (PM), CO, and CO₂ emissions, as well as fuel quality and flue gas treatment requirements. Non-compliance can lead to operational shutdowns, penalties, or mandatory retrofits.
In today’s industrial world, environmental compliance is not optional—it’s operational survival.
Industrial oil-fired boilers must meet specific emissions standards set by international agreements and regional regulatory agencies to operate legally.True
Environmental laws set limits on pollutants such as NOₓ, SO₂, PM, CO, and CO₂ for oil-fired boilers, requiring operators to implement combustion and post-combustion control technologies.
1. Global Environmental Agreements
Agreement | Impact on Oil-Fired Boilers |
---|---|
Paris Climate Agreement (2015) | Encourages reduction of CO₂ emissions, transition to lower-carbon energy |
Kyoto Protocol (1997) | Set the first legally binding CO₂ targets for industrial nations |
Minamata Convention on Mercury | Indirectly affects boiler systems using mercury-laden fuels |
Although global agreements do not set direct emission limits, they drive national policies to enforce stricter controls.
2. United States: U.S. EPA Standards
Regulation | Scope and Key Points |
---|---|
NSPS (New Source Performance Standards) | Limits for NOₓ, SO₂, PM for new and modified boilers |
MACT (Maximum Achievable Control Technology) | National Emissions Standards for Hazardous Air Pollutants (NESHAP) |
Title V Permits | Comprehensive air operating permits for large units |
Example Emission Limits (Oil-Fired Boilers >10 MMBtu/hr):
Pollutant | Limit |
---|---|
NOₓ | 0.10–0.20 lb/MMBtu (about 115–230 mg/Nm³) |
SO₂ | Depends on fuel sulfur content, often <0.5% sulfur allowed |
PM | 0.03 lb/MMBtu (about 35 mg/Nm³) |
In the U.S., oil-fired industrial boilers must comply with EPA NSPS and MACT standards for emissions control.True
EPA regulations set binding limits for emissions such as NOₓ, SO₂, PM, and hazardous air pollutants for oil-fired boilers.
3. European Union: Industrial Emissions Directive (IED)
Directive | Scope and Key Points |
---|---|
IED 2010/75/EU | Integrated pollution prevention and control framework for large combustion plants (LCPs) |
BREF Documents | Best Available Techniques (BAT) Reference documents guide technology selection |
Example Emission Limits (Post-2021 for Oil-Fired LCPs):
Pollutant | Limit (mg/Nm³) |
---|---|
NOₓ | 100–150 |
SO₂ | 35–200 |
PM | 10–20 |
Monitoring: Continuous Emissions Monitoring Systems (CEMS) often required.
Scope: Plants >50 MW thermal input primarily, but some national laws apply IED principles to smaller units too.
4. China: GB Standards
Regulation | Scope and Key Points |
---|---|
GB 13271-2014 (Boilers) | Limits for emissions from industrial boilers |
GB 13223-2011 (Power Plants) | Controls for larger oil-fired power boilers |
Example Emission Limits:
Pollutant | Standard Limit (mg/Nm³) |
---|---|
NOₓ | 150–300 |
SO₂ | 50–400 |
PM | 20–30 |
China has recently tightened emissions at the provincial level, especially in major industrial hubs like Beijing, Tianjin, and Shanghai.
5. Other Regional Highlights
Region | Regulatory Focus |
---|---|
Japan (Air Pollution Control Act) | Very strict PM and SO₂ limits for urban boilers |
Canada (CCME Guidelines) | Provincial and federal standards, focus on GHG reduction |
India (CPCB Guidelines) | Emission limits similar to EU/China for new oil-fired installations |
Middle East (KSA, UAE) | Focus on NOₓ and PM for refinery-associated boilers |
6. Compliance Technologies in Boiler Design
Pollutant | Main Compliance Methods |
---|---|
NOₓ | Low-NOₓ burners, staged combustion, SCR systems |
SO₂ | Low-sulfur fuels, wet/dry scrubbers |
PM | ESPs, baghouse filters, optimized combustion |
CO₂ | High-efficiency boilers, low-carbon fuel switching, carbon capture readiness |
Real-World Example: Compliance Strategy for Oil-Fired Boiler Retrofit
Facility: Industrial park heating system (15 MWth oil boiler)
Objective: Meet EU IED post-2021 limits
Actions:
Installed low-NOₓ burners with FGR
Switched to ultra-low sulfur (ULS) heating oil (0.1% S)
Retrofitted baghouse filter for PM control
Results:
NOₓ reduced by 45%
SO₂ reduced by 80%
PM emissions lowered to 8 mg/Nm³
Full regulatory compliance achieved
Boiler Compliance Checklist
Checklist Item | Done? (✔/✖) |
---|---|
Identify applicable local and national standards | |
Confirm emission limits for NOₓ, SO₂, PM, CO₂ | |
Specify appropriate combustion and flue gas treatment technologies | |
Plan for CEMS or periodic monitoring requirements | |
Choose fuels that meet sulfur and carbon standards | |
Future-proof design for upcoming tighter regulations |
Summary
Global and regional environmental regulations play a decisive role in the design, selection, and operation of industrial oil-fired boilers. Boilers must meet strict emission limits for NOₓ, SO₂, PM, and increasingly CO₂, enforced by agencies like the U.S. EPA, EU Commission (IED), and Chinese Ministry of Ecology and Environment (MEE). Compliance demands advanced combustion technologies, cleaner fuels, emission capture systems, and often continuous monitoring infrastructure. Successful projects build regulatory compliance into the design from the beginning—because in the world of industrial steam, you must breathe as cleanly as you burn.
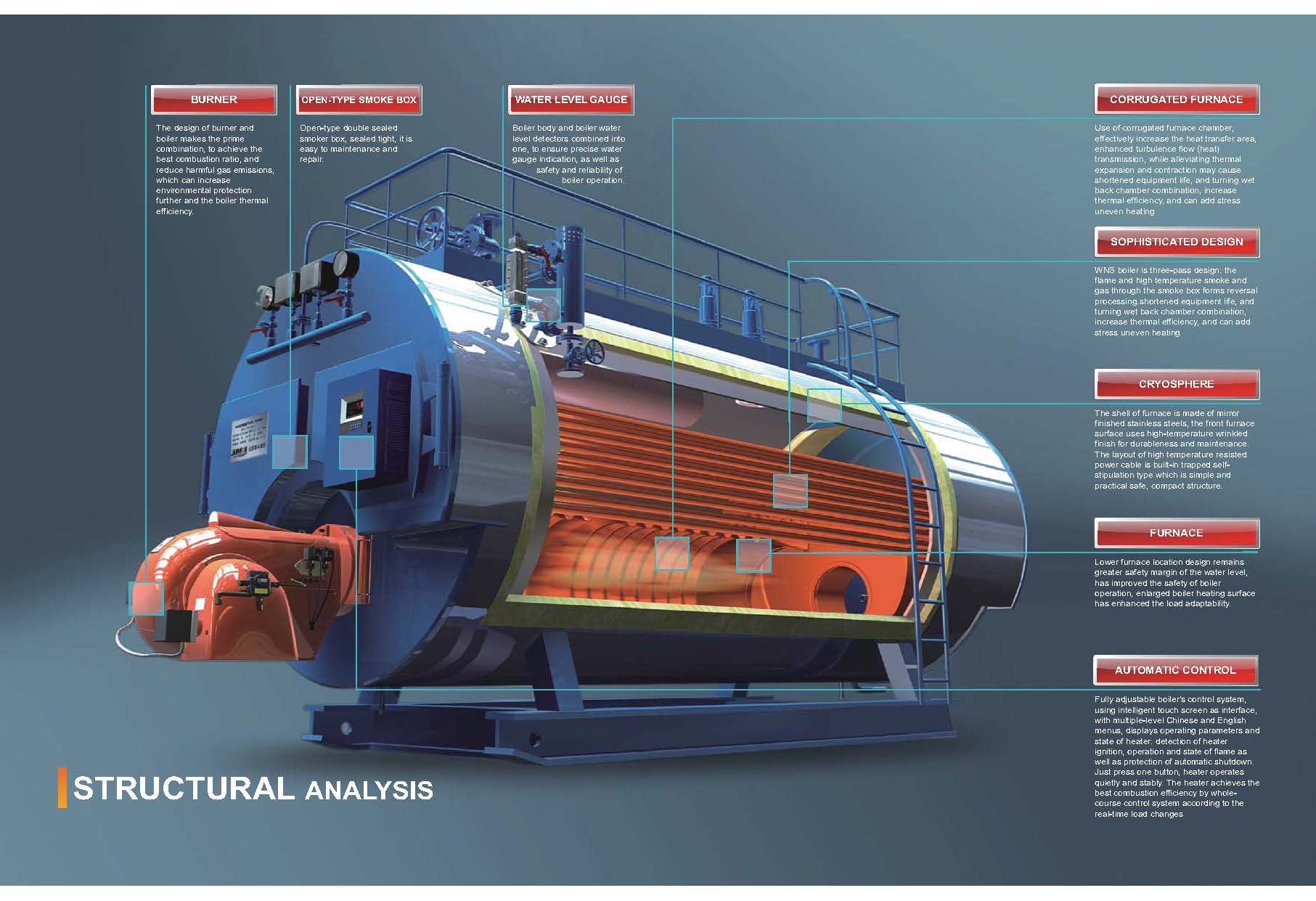
How Do Fuel Sulfur Content and Burner Technology Impact Emissions Compliance?
Meeting emissions compliance in industrial oil-fired boilers requires a dual strategy: control the pollutants formed from fuel properties and optimize combustion conditions. Two major variables—fuel sulfur content and burner technology—have a profound effect on emissions like SO₂, NOₓ, PM, and CO. Choosing the wrong fuel or burner design can instantly put a boiler out of regulatory compliance, leading to heavy penalties, forced retrofits, and environmental permitting delays. Designing properly around these two factors ensures the boiler stays clean, compliant, and cost-efficient over its entire life.
Fuel sulfur content directly impacts SO₂ emissions because sulfur in the fuel burns to form sulfur oxides, while burner technology controls NOₓ and CO emissions by managing flame temperature, air-fuel mixing, and combustion staging. Using low-sulfur fuels minimizes SO₂ output, and advanced low-NOₓ burners reduce NOₓ formation. Together, proper fuel selection and burner design are essential to achieving full emissions compliance in industrial boiler systems.
You can’t control what your boiler emits without first controlling what you feed it and how you burn it.
Fuel sulfur content and burner technology are two critical factors that determine whether an industrial boiler can meet emissions regulations.True
Sulfur content governs SO₂ emissions, while burner technology governs NOₓ and CO formation; both must be engineered correctly to achieve regulatory compliance.
1. Impact of Fuel Sulfur Content on Emissions Compliance
Factor | Impact |
---|---|
Sulfur % in fuel | Directly proportional to SO₂ emissions output |
How Sulfur Translates to SO₂:
Fuel Sulfur Content | SO₂ Emissions Impact |
---|---|
0.1% (Ultra-low sulfur oil) | Very low SO₂ emissions, easy compliance |
0.5% (Typical No. 2 heating oil) | Moderate SO₂ output, may need mild controls |
2.0–3.5% (Heavy fuel oil) | High SO₂ emissions, requires FGD systems |
Rule of Thumb: Every 1% sulfur in fuel produces about 20,000 ppmv SO₂ in raw flue gas.
Regulatory Pressure on Sulfur Content:
Region | Sulfur Limits |
---|---|
EU IED | <0.1–0.2% sulfur for heating oils |
US EPA (marine/industrial) | ULS fuel <0.5% sulfur |
China GB/T 25209 | 0.5% sulfur (urban industrial areas) |
Compliance Solutions for High-Sulfur Fuels:
Switch to low-sulfur or ultra-low sulfur (ULS) fuels
Install flue gas desulfurization (FGD) systems
Blend high-sulfur oils with cleaner fuels if allowed
2. Impact of Burner Technology on NOₓ and CO Emissions
Burner Type | NOₓ Control Capability |
---|---|
Standard burners (basic atomization) | High NOₓ formation due to high flame temp |
Low-NOₓ burners (LNBs) | 30–60% NOₓ reduction by staging combustion |
Ultra-low NOₓ burners (ULNBs) | Up to 80% NOₓ reduction, sensitive to tuning |
How Low-NOₓ Burners Work:
Technique | Effect |
---|---|
Staged air injection | Reduces peak flame temperature |
Flue gas recirculation (FGR) | Dilutes oxygen, cools combustion zone |
Fuel-air pre-mixing | Uniform temperature distribution, low hotspots |
Burner Technology and CO Formation:
Poor burner design or tuning → Excessive CO due to incomplete combustion
Proper low-NOₓ design with O₂ control → Balanced reduction of both NOₓ and CO
Challenge | Solution |
---|---|
Reducing NOₓ without spiking CO | Use staged burners + real-time O₂ trim |
3. Combined Influence: Fuel + Burner Synergy
Scenario | Compliance Risk |
---|---|
High-sulfur oil + standard burner | High SO₂, high NOₓ → Non-compliance likely |
Low-sulfur oil + standard burner | Acceptable SO₂, but potential NOₓ issues |
Low-sulfur oil + low-NOₓ burner | Best combination for meeting full emissions limits |
Switching to low-sulfur fuels and installing low-NOₓ burners simultaneously achieves the greatest emissions compliance improvements for industrial oil-fired boilers.True
Combining clean fuels with advanced burner technologies minimizes both sulfur dioxide and nitrogen oxide emissions, supporting full regulatory compliance.
4. Real-World Case: Emissions Compliance Upgrade
Facility: Chemical production plant (oil-fired steam boiler, 20 TPH)
Initial Situation:
Using 2.5% sulfur heavy oil
Standard pressure-jet burner
Non-compliant on SO₂ and NOₓ
Compliance Strategy:
Switched to 0.3% sulfur ULS oil
Retrofitted with a low-NOₓ burner + partial flue gas recirculation
Added O₂ trim control system
Results:
SO₂ emissions reduced by 88%
NOₓ emissions reduced by 55%
CO emissions below 100 ppm
Full EPA and EU IED compliance achieved
Best Practices for Emissions Compliance Through Fuel and Burner Management
Best Practice | Reason |
---|---|
Specify fuel sulfur content early in project design | Align fuel quality with SO₂ targets |
Choose advanced low-NOₓ burners for all new installations | Meet modern NOₓ limits without retrofits |
Tune burner systems with real-time O₂ monitoring | Maintain low NOₓ and low CO simultaneously |
Design flue gas treatment flexibility into large systems | Adapt to future stricter standards |
Verify compliance performance with stack testing | Ensure real-world results match design targets |
5. Summary Table: Fuel and Burner Impact on Major Emissions
Pollutant | Main Influencing Factor | Control Strategy |
---|---|---|
SO₂ | Fuel sulfur content | Use low-sulfur fuels or scrubbers |
NOₓ | Burner flame temperature and staging | Install low-NOₓ or ultra-low NOₓ burners |
CO | Burner tuning and O₂ control | Use advanced combustion control systems |
PM | Fuel impurities, incomplete combustion | Improve burner design and atomization |
Summary
Fuel sulfur content and burner technology are two of the most decisive factors determining whether an industrial oil-fired boiler can meet emissions compliance targets. High-sulfur fuels drive up SO₂ emissions, while poor burner designs create excess NOₓ and CO. By choosing low-sulfur fuels and specifying modern low-NOₓ burners with precise combustion control, operators can consistently meet regulatory limits, minimize environmental impact, and operate boilers efficiently and reliably. In emissions compliance, you can’t fake it—you have to engineer it right from the start.
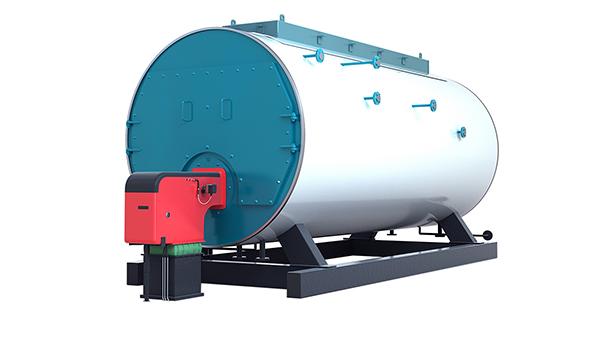
What Emission Control Technologies Are Available for Oil-Fired Boilers?
As environmental regulations for industrial boilers grow increasingly stringent, oil-fired boiler operators must implement effective emission control technologies to meet limits on NOₓ, SO₂, PM, CO, and even CO₂. Choosing the right combination of combustion optimization, flue gas treatment, and fuel management strategies is essential for ensuring regulatory compliance, long-term operational efficiency, and sustainability goals. Each pollutant requires specific technologies tailored to the characteristics of oil combustion and the plant’s size, load, and environmental permit requirements.
Emission control technologies for oil-fired boilers include low-NOₓ burners, flue gas recirculation (FGR), selective catalytic reduction (SCR), selective non-catalytic reduction (SNCR), flue gas desulfurization (wet scrubbers and dry sorbent injection), particulate removal systems like baghouse filters and ESPs, and combustion optimization systems like O₂ trim controls. These technologies are deployed individually or in combination depending on the targeted emissions and compliance limits.
When it comes to emissions control, there’s no single fix—only integrated solutions built on deep engineering expertise.
Industrial oil-fired boilers require a combination of combustion control and flue gas treatment technologies to effectively meet emission regulations for NOₓ, SO₂, PM, and CO.True
Different pollutants originate from different combustion and fuel characteristics; controlling emissions requires specific engineered solutions for each pollutant.
1. NOₓ Control Technologies
Technology | Description | NOₓ Reduction Efficiency |
---|---|---|
Low-NOₓ Burners | Stage fuel and air to lower flame temperature | 30–60% |
Flue Gas Recirculation (FGR) | Recirculates cooled flue gas into combustion air | 20–50% |
Selective Non-Catalytic Reduction (SNCR) | Injects urea/ammonia into hot flue gas | 30–50% |
Selective Catalytic Reduction (SCR) | Catalytic reaction with urea/ammonia in flue gas | 70–95% |
Note: SCR provides the deepest NOₓ reductions but requires more investment and careful temperature control (typically 250–450°C optimal range).
2. SO₂ Control Technologies
Technology | Description | SO₂ Reduction Efficiency |
---|---|---|
Fuel Switching to Low-Sulfur Oil | Use oils with <0.1% sulfur | 80–99% (by fuel selection) |
Dry Sorbent Injection (DSI) | Inject sodium bicarbonate or lime into flue gas | 50–70% |
Wet Flue Gas Desulfurization (Wet FGD) | Scrubbers using limestone slurry to absorb SO₂ | 90–99% |
Wet Scrubber Details:
Absorption reaction forms calcium sulfate (gypsum) waste.
Highly effective but needs water treatment, sludge handling.
3. Particulate Matter (PM) Control Technologies
Technology | Description | PM Reduction Efficiency |
---|---|---|
Cyclone Separators | Centrifugal separation of large ash particles | 70–90% (coarse PM only) |
Electrostatic Precipitators (ESP) | Use electrostatic charge to trap fine particles | 90–99% |
Baghouse Filters | Fabric filters trap very fine particulate matter | 99–99.9% |
Baghouses are the preferred choice for very low PM emission standards (<10 mg/Nm³), particularly in urban or sensitive environments.
4. CO and VOC Control Technologies
Technology | Description | CO/VOC Reduction Efficiency |
---|---|---|
O₂ Trim Systems | Real-time control of combustion air based on oxygen level feedback | 10–25% CO reduction |
Proper Burner Tuning and Maintenance | Adjust burner settings to achieve complete combustion | 10–30% |
Catalytic Oxidation Systems | Post-combustion oxidation of CO and VOCs | 85–95% (rarely needed for standard oil boilers) |
5. Integrated Emission Control Strategies
Scenario | Technology Combination |
---|---|
High NOₓ focus (tight urban standards) | Low-NOₓ burners + SCR + O₂ trim control |
High SO₂ and PM focus (heavy oil fuels) | Low-sulfur fuel + Wet FGD + Baghouse |
Balanced multi-pollutant compliance | Low-NOₓ burners + DSI + ESP + real-time monitoring |
Combining multiple emission control technologies tailored to specific pollutants offers the most effective strategy for achieving regulatory compliance in industrial oil-fired boilers.True
Each emission type requires a targeted control method; integrated systems provide comprehensive compliance across all major pollutants.
6. Real-World Compliance Example: Oil-Fired Boiler Upgrade
Facility: Large food processing plant
Boiler: 25 TPH oil-fired steam generator
Original Situation:
NOₓ >250 mg/Nm³
SO₂ ~500 mg/Nm³ (1.5% sulfur oil)
PM ~70 mg/Nm³
Upgrades Installed:
Switched to 0.1% sulfur oil
Retrofitted with low-NOₓ burner and 20% FGR
Installed dry sorbent injection (DSI) for SO₂
Installed an ESP for PM control
Outcome:
NOₓ reduced to <100 mg/Nm³
SO₂ reduced by 85%
PM emissions below 15 mg/Nm³
Full compliance with EU IED and local EPA standards
7. Emission Control Technology Selection Guide
Pollutant to Control | Preferred Technologies |
---|---|
NOₓ | Low-NOₓ burners, FGR, SCR |
SO₂ | Low-sulfur fuels, DSI, Wet FGD |
PM | ESP, baghouse filters, cyclones |
CO/VOCs | O₂ trim systems, catalytic oxidation |
Summary
Achieving emissions compliance for oil-fired boilers requires a carefully selected suite of control technologies tailored to specific pollutants. By applying low-NOₓ combustion systems, flue gas desulfurization, particulate capture devices, and real-time combustion optimization, industrial operators can meet even the toughest environmental standards. Successful emissions strategies are integrated at the design stage, not bolted on afterward. In modern industrial steam generation, you don’t just design for capacity—you engineer for clean air.
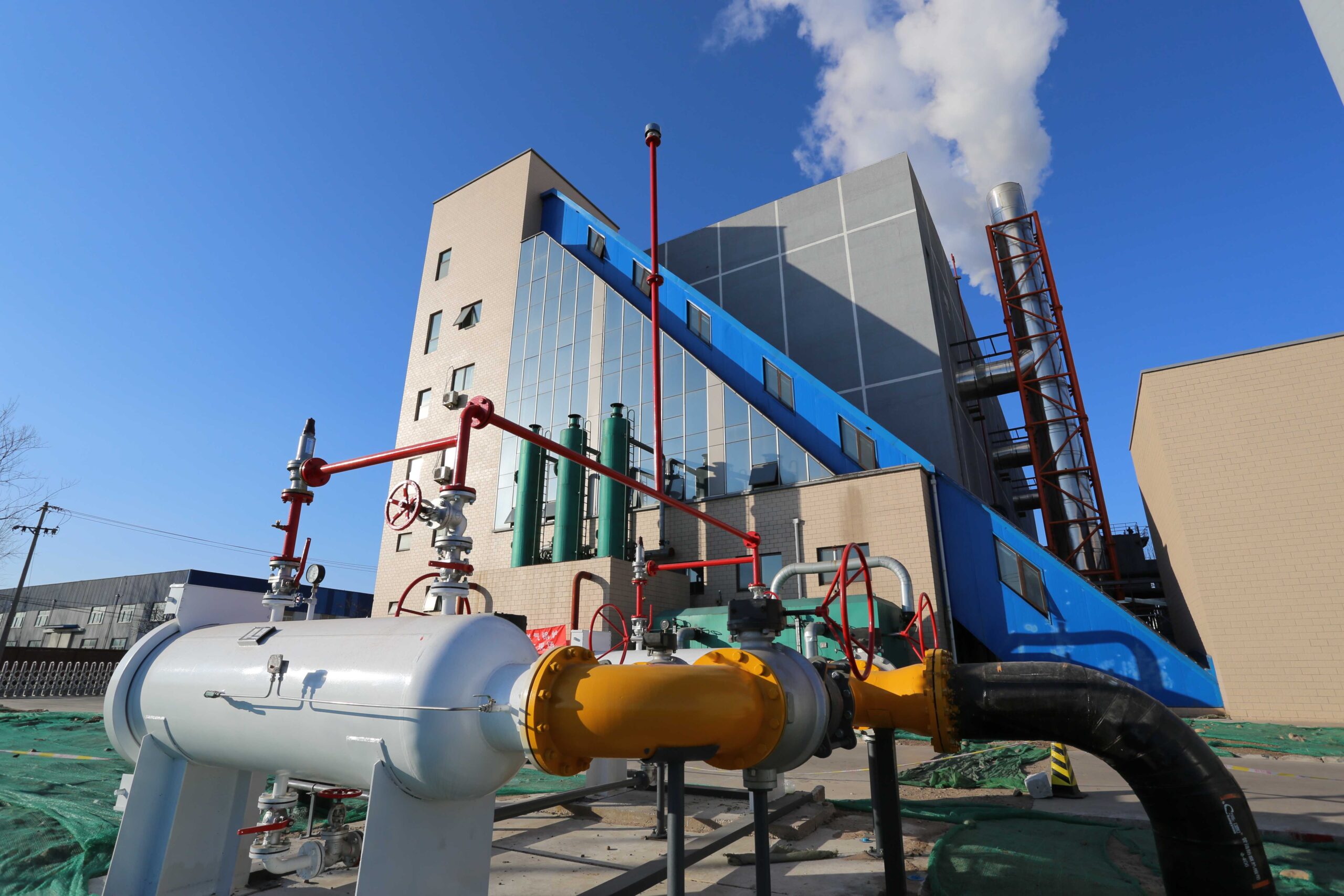
Why Is Continuous Emission Monitoring (CEMS) Important for Regulatory Compliance?
In today’s strict environmental landscape, regulators no longer accept manual or occasional emissions measurements for major industrial sources like oil-fired boilers. Instead, Continuous Emission Monitoring Systems (CEMS) have become the gold standard for demonstrating that facilities consistently comply with pollutant limits. Without CEMS, operators risk permit violations, fines, forced shutdowns, or loss of public trust. Properly implemented CEMS not only satisfies legal requirements but also provides operational insights that help optimize combustion, reduce fuel consumption, and prevent future compliance issues.
Continuous Emission Monitoring Systems (CEMS) are important for regulatory compliance because they provide real-time, continuous measurement and reporting of critical pollutants like NOₓ, SO₂, CO₂, CO, and PM, ensuring that industrial boilers consistently operate within permitted emission limits. CEMS offer transparent, verifiable data that regulatory agencies require to prove compliance, prevent environmental violations, and maintain operating permits.
In emissions compliance, if you can’t prove it every second—you’re not compliant.
Continuous Emission Monitoring Systems (CEMS) are legally required for many large industrial boilers to continuously verify emissions compliance.True
Many regulations require real-time emissions data recording to confirm ongoing compliance, and CEMS provide the verifiable, continuous proof regulators demand.
1. What Is a Continuous Emission Monitoring System (CEMS)?
Component | Function |
---|---|
Gas Analyzers | Measure concentrations of NOₓ, SO₂, CO₂, CO, O₂ |
Particulate Monitors | Measure PM concentrations |
Sample Conditioning Systems | Filter, dry, and prepare gas for accurate analysis |
Data Acquisition and Handling System (DAHS) | Collects and stores emission data |
Calibration Systems | Automatically verify measurement accuracy |
2. Key Pollutants Measured by CEMS
Pollutant | Why It’s Monitored |
---|---|
NOₓ | Smog formation, acid rain |
SO₂ | Acid rain, corrosion |
CO₂ | Greenhouse gas reporting (carbon footprint) |
CO | Toxicity, incomplete combustion indicator |
PM (optional in some systems) | Respiratory health impact |
O₂ | Helps calculate combustion efficiency and verify proper burner tuning |
3. Regulatory Requirements for CEMS
Region | CEMS Requirement for Boilers |
---|---|
U.S. EPA (NSPS, MACT Rules) | CEMS mandatory for boilers >100 MMBtu/hr or regulated under MACT |
EU Industrial Emissions Directive (IED) | Mandatory for LCPs (>50 MWth input), NOₓ, SO₂, dust |
China GB Standards | Increasingly require CEMS for industrial boilers >20 t/h |
Other Countries (Japan, Canada, India) | Similar requirements based on size and location |
4. Why CEMS Is Critical for Compliance
Reason | Importance |
---|---|
Real-Time Proof of Compliance | Regulators require minute-by-minute data |
Early Detection of Problems | Quickly identify combustion issues or system malfunctions |
Penalty Avoidance | Missed manual tests can lead to fines, shutdowns |
Data Transparency | Publicly accessible emissions records in many regions |
Support for Carbon Reporting | CO₂ monitoring supports ESG and sustainability reporting |
5. Real-World Example: CEMS Saving a Plant from Non-Compliance
Facility: Industrial oil-fired power boiler (40 MW)
Issue: Temporary NOₓ spike due to burner misfire
CEMS Action:
Detected spike within 2 minutes
Triggered alarm to operators
Allowed immediate burner shutdown and retuning
Result:
Incident recorded, corrective action documented
Regulatory violation avoided
No penalty assessed because the CEMS log showed fast corrective action
Without CEMS, the plant would have faced automatic violation and a $250,000 fine.
6. Best Practices for CEMS Installation and Operation
Best Practice | Reason |
---|---|
Install at correct sampling points (after control devices) | Reflect true stack emissions |
Use certified, regulatory-approved analyzers | Ensure data validity and regulatory acceptance |
Maintain continuous calibration routines | Ensure data accuracy and compliance trustworthiness |
Integrate with plant control systems | Enable automatic alarms, reporting, and shutdowns |
Archive and protect historical CEMS data for audits | Prove long-term compliance during inspections |
Proper CEMS calibration and maintenance are necessary to ensure accurate emissions reporting and regulatory acceptance.True
Without regular calibration and system checks, CEMS data can become unreliable, risking invalid compliance records and regulatory penalties.
7. CEMS Data Reporting and Use
Data Type | Usage |
---|---|
1-minute averages | Real-time monitoring and alarm triggering |
1-hour rolling averages | Regulatory reporting (compliance tests) |
Daily/Monthly Summaries | Emissions trend analysis, permit compliance |
Alarm Logs and Event Reports | Root cause analysis for non-compliance events |
8. CEMS Technology Overview
Technology | Typical Applications |
---|---|
Infrared (IR) Gas Analyzers | CO, CO₂, SO₂ monitoring |
Chemiluminescence Detectors (CLD) | NOₓ analysis |
Paramagnetic Sensors | O₂ analysis |
Beta Attenuation Monitors | PM measurement |
Summary
Continuous Emission Monitoring Systems (CEMS) are essential for real-time, transparent, verifiable regulatory compliance for industrial oil-fired boilers. Without CEMS, operators have no credible proof that emissions remain within permitted limits every second of operation. CEMS not only protects the facility legally but also supports operational excellence by detecting problems early, reducing downtime, and optimizing combustion efficiency. In modern boiler operation, CEMS isn’t a luxury—it’s the legal lifeline that keeps your plant running.
🔍 Conclusion
Environmental and emission regulations are non-negotiable factors in the selection of an industrial oil-fired boiler. Choosing a boiler designed for low emissions, high combustion efficiency, and regulatory compliance not only protects your business from legal risks but also contributes to energy savings, corporate sustainability goals, and positive brand reputation. Smart boiler selection ensures that your operation remains competitive and future-ready in an increasingly eco-conscious industrial world.
📞 Contact Us
💡 Need help selecting a compliant oil-fired boiler for your facility? Our technical experts specialize in low-emission boiler systems, emission control integration, and regulatory consulting tailored to your industry and location.
🔹 Reach out today and ensure your next boiler investment meets all environmental and regulatory standards! 🛢️🌎✅
FAQ
What environmental regulations affect industrial oil-fired boiler selection?
Key regulations include limits on NOx, SO₂, particulate matter, and CO₂ emissions set by agencies like the EPA, EU, and local environmental authorities. These rules dictate boiler design, burner technology, and required emission control systems.
Why is NOx emission control important for oil-fired boilers?
Nitrogen oxides (NOx) contribute to smog and acid rain. Industrial oil-fired boilers must often incorporate low-NOx burners, flue gas recirculation (FGR), or selective catalytic reduction (SCR) systems to meet legal NOx limits.
How do sulfur content and SO₂ regulations impact boiler selection?
High sulfur fuel oils produce more SO₂ emissions, requiring the use of scrubbers or switching to low-sulfur fuel oils (LSFO) to comply with increasingly strict air quality standards like the EPA’s Clean Air Act or Euro VI standards.
What emission control technologies are used in oil-fired boilers?
Technologies include low-NOx burners, FGR, particulate filters, electrostatic precipitators (ESP), wet scrubbers, and SCR systems to minimize pollutant release and achieve regulatory compliance.
How do environmental regulations influence operational costs?
Compliance often increases upfront investment for advanced burners and emission control systems. However, efficient, low-emission boilers can reduce fuel consumption, avoid regulatory fines, and qualify for environmental incentives, lowering long-term operating costs.
References
EPA Boiler Emissions Standards – https://www.epa.gov
Clean Air Act Guidelines for Boilers – https://www.energy.gov
European Union Industrial Emissions Directive (IED) – https://www.europa.eu
NOx Control Technologies for Boilers – https://www.sciencedirect.com
SO₂ and Sulfur Content Regulations – https://www.bioenergyconsult.com
Emission Compliance Strategies – https://www.researchgate.net
Low-Sulfur Fuel Oil Requirements – https://www.mdpi.com
Advanced Burner Technology for Emission Reduction – https://www.energysavingtrust.org.uk
Impact of Environmental Regulations on Industrial Boilers – https://www.iea.org
Emission Control Systems in Boilers – https://www.automation.com
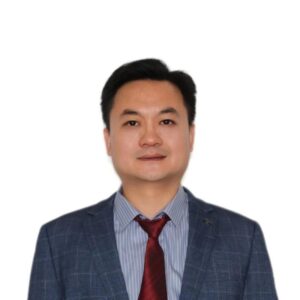