In large-scale power generation, selecting the right industrial power plant boiler hinges heavily on understanding the fuel source and its combustion behavior. Many facilities face high costs, frequent maintenance issues, or even compliance risks due to misalignment between the boiler system and the fuel characteristics. A poor fuel-boiler match can lead to low efficiency, excessive emissions, slagging, corrosion, and equipment failure. To avoid these outcomes, it’s essential to factor in fuel and combustion dynamics at the very beginning of the boiler selection process.
Fuel types and combustion characteristics affect your choice of industrial power plant boiler by determining the appropriate boiler design, combustion technology, furnace size, ash handling system, emission controls, and overall efficiency strategy. Different fuels—such as coal, biomass, oil, natural gas, or waste-derived fuels—have varying moisture content, calorific values, ash content, volatility, and emission profiles. Understanding these parameters helps ensure that the selected boiler achieves stable combustion, meets performance expectations, and complies with environmental standards.
Let’s explore how these critical fuel-related variables shape the design and selection of industrial power plant boilers.
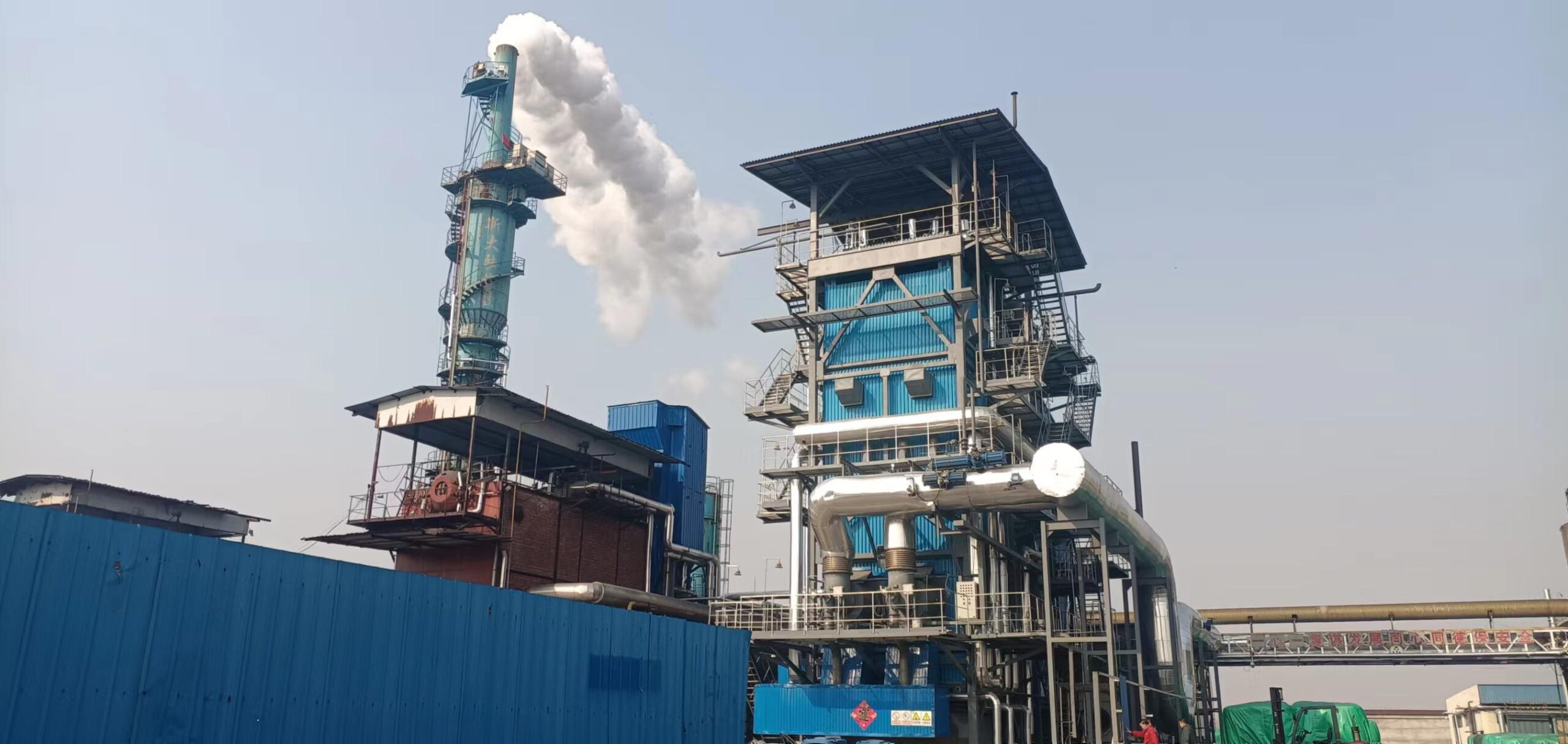
How Does Fuel Calorific Value Influence Boiler Capacity and Thermal Design?
In industrial boiler engineering, one of the most critical variables in thermal design and capacity planning is fuel calorific value (CV)—a measure of the heat energy available from the combustion of a given amount of fuel. Using a fuel with an inappropriate calorific value can lead to over- or undersized boilers, inefficient heat transfer, incomplete combustion, and increased emissions. Misalignment between fuel energy content and boiler configuration raises operational costs, shortens equipment lifespan, and compromises steam output reliability. Understanding how calorific value directly affects boiler capacity, heat transfer area, combustion chamber sizing, and auxiliary system integration is essential for optimizing system performance and achieving long-term reliability.
Fuel calorific value directly affects boiler capacity and thermal design because it determines how much fuel energy is available for conversion into usable heat. A low calorific value fuel requires more fuel volume and a larger furnace, while a high calorific value fuel demands robust heat transfer surfaces and careful combustion control to manage high thermal flux and efficiency.
Choosing a boiler design without matching it to the calorific value of the fuel can lead to underperformance or overheating.
Calorific value affects the thermal energy input, which defines the combustion chamber size and boiler capacity.True
Boiler design must balance heat input with required steam output. Higher or lower calorific value fuels change the required fuel flow rate and furnace size.
The relationship between calorific value and boiler design is not just about numbers—it’s about ensuring safe, consistent, and efficient energy transformation. Let’s explore how.
1. What Is Calorific Value?
Calorific value (CV), or heating value, is the amount of heat released when a specific amount of fuel is completely combusted. It is typically expressed in:
kJ/kg for solid fuels like coal or biomass
kJ/Nm³ or MJ/Nm³ for gaseous fuels like natural gas
kJ/L for liquid fuels such as fuel oil
There are two types:
Type | Definition | Common Use |
---|---|---|
Gross Calorific Value (GCV) | Includes latent heat of water vapor | Used in fuel specs |
Net Calorific Value (NCV) | Excludes latent heat | Used in boiler efficiency calculations |
2. Calorific Value vs Boiler Heat Input and Output
The thermal energy delivered by a fuel is calculated using:
Boiler Heat Input = Fuel Flow Rate × Calorific Value
Fuel Type | Typical NCV (kJ/kg or MJ/Nm³) | Implication |
---|---|---|
Natural Gas | 35–39 MJ/Nm³ | High-energy, low mass flow |
Bituminous Coal | 20,000–30,000 kJ/kg | Medium-high CV, standard furnace sizing |
Biomass (Wood Chips) | 8,000–16,000 kJ/kg | Larger volume needed for same heat |
Lignite | 7,000–14,000 kJ/kg | Requires large furnaces, longer residence time |
Heavy Fuel Oil | 38,000–41,000 kJ/kg | Compact furnace, high thermal density |
🔧 Design Impact:
Low CV Fuel → Larger Furnace → Slower Combustion
High CV Fuel → Smaller Furnace but High Heat Flux → Needs Better Cooling & Materials
3. How Calorific Value Affects Boiler Thermal Design
3.1 Furnace Volume and Residence Time
Calorific Value | Required Furnace Volume | Reason |
---|---|---|
Low | Large | Longer combustion duration, more air |
High | Small but intense | Higher flame temperature and shorter time needed |
🔥 Higher CV fuels produce hotter flames, requiring refractory linings, tube spacing optimization, and high-temperature-resistant steel alloys.
3.2 Heat Transfer Area
The total heat transfer surface depends on:
Available heat input (calorific value × mass flow)
Required steam or heat output
Boiler type (fire-tube, water-tube, etc.)
CV Effect | Design Response |
---|---|
Higher CV → Greater heat in smaller space → Needs denser tube layout | |
Lower CV → Larger gas flow & cooler gas → More surface area required |
4. Impact on Burner, Air-Fuel Ratio & Flue Gas Volume
Parameter | High CV Fuel | Low CV Fuel |
---|---|---|
Air Requirement | Lower per unit fuel | Higher per unit fuel |
Flue Gas Volume | Less overall volume | Higher due to more combustion air |
Burner Size | Smaller, more precise | Larger, robust |
Flame Temperature | High | Low |
O₂ Trim System Sensitivity | High | Medium |
📊 The burner must match the flame stability and mixing requirement of the fuel’s energy density.
5. Case Study: Biomass vs Natural Gas Boiler Design
Parameter | Biomass Boiler | Natural Gas Boiler |
---|---|---|
Calorific Value | ~10,000 kJ/kg | ~38 MJ/Nm³ |
Fuel Flow Rate (per MW) | High (100–120 kg/h) | Low (~90 Nm³/h) |
Furnace Size | Large, slow-burning | Small, fast combustion |
Heat Transfer Surface | Large to compensate | Compact and optimized |
Fuel Feeding System | Mechanical, batch-fed | Pressurized pipe system |
Emission Control | Ash and PM handling | Focus on NOx and CO |
✅ Designing for biomass requires larger combustion space, different feeding and ash handling, and greater insulation due to lower flame temperatures.
6. Implications for Boiler Selection and Efficiency
Aspect | Design Impact |
---|---|
Oversized Boiler (High CV Fuel in Low CV Furnace) | Causes overheating, high flue loss, metal stress |
Undersized Boiler (Low CV Fuel in High CV Furnace) | Fails to generate sufficient steam, low efficiency |
Wrong Burner Type | Flame instability, incomplete combustion |
Inefficient Heat Transfer | Lower thermal efficiency, high fuel use |
Boiler size and furnace geometry must be adjusted based on the calorific value of the intended fuel.True
Using a fuel with a different calorific value without adjusting boiler design can lead to thermal inefficiency and damage.
Summary
Fuel calorific value plays a foundational role in boiler sizing and thermal design. Whether you’re designing for coal, gas, oil, or biomass, the calorific value dictates everything from fuel flow rate to furnace dimensions, burner selection, heat transfer area, and efficiency performance. High CV fuels deliver more energy per unit mass or volume, which allows compact systems—but demands precise control and thermal protection. Low CV fuels require larger furnaces and more combustion air, but may offer cost or sustainability advantages.
Matching your boiler system to the fuel’s calorific value is not optional—it’s the key to reliable and efficient operation.
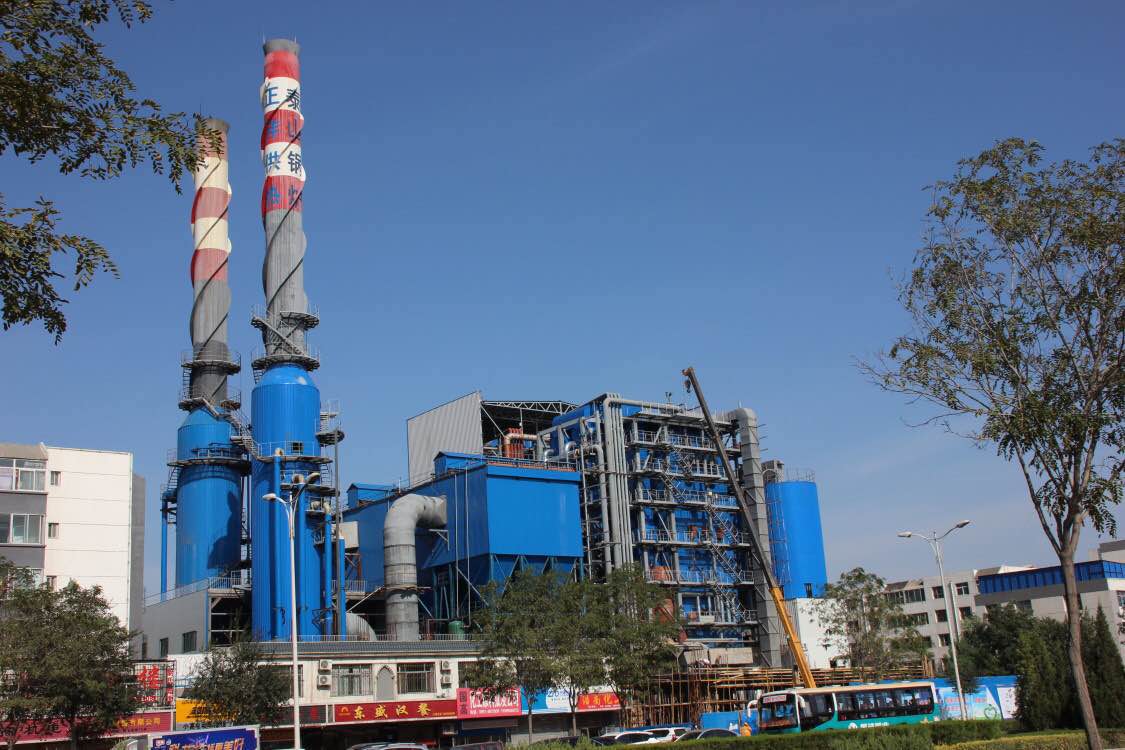
Why Do Fuel Moisture Content and Volatility Matter in Combustion Chamber Design?
Industrial boiler performance and efficiency are fundamentally shaped by the design of the combustion chamber, which must accommodate the physical and chemical characteristics of the fuel—particularly moisture content and volatile matter. Fuels with high moisture need more energy for drying, while fuels with high volatility ignite rapidly and may cause unstable combustion or even safety issues if the design is inadequate. If these properties are ignored, the boiler may suffer from poor flame stability, incomplete combustion, excessive emissions, clinker formation, or thermal damage to components. To achieve clean, efficient, and stable combustion, the chamber must be engineered to match how the fuel behaves during drying, pyrolysis (volatilization), and oxidation.
Fuel moisture content and volatility directly impact combustion chamber design by affecting the ignition delay, flame stability, burnout time, and heat release distribution. High moisture fuels require larger drying zones and longer residence time, while high volatility fuels need precise air staging and controlled ignition areas to prevent flame blow-off or instability.
If the combustion chamber doesn’t accommodate these fuel characteristics, performance, emissions, and safety suffer.
Fuel moisture content reduces the effective heating value and delays ignition.True
Moisture in fuel absorbs heat for evaporation before combustion can start, reducing thermal efficiency.
Volatile matter content influences the ignition point and flame behavior.True
Fuels high in volatile matter release flammable gases early, needing careful combustion zone design.
Let’s explore how both these parameters affect combustion chamber dimensions, air staging, flame control, and boiler efficiency.
1. Moisture Content: Why It Matters in Chamber Design
Moisture content is the percentage of water present in the fuel, either as:
Free moisture (surface or interstitial water)
Bound moisture (within plant fibers or structure)
Fuel Type | Typical Moisture (%) |
---|---|
Dry Coal | 2–10% |
Lignite | 20–45% |
Biomass (wood) | 15–55% |
Agricultural waste | 30–60% |
🔥 Impact on Combustion:
Delayed Ignition: Water must evaporate first, cooling the flame zone.
Reduced Flame Temperature: Evaporation absorbs latent heat.
Increased Flue Gas Volume: More steam increases fan energy demand.
Incomplete Combustion: Cold combustion zones lead to unburnt carbon.
Corrosion Risk: Low-temperature zones and high moisture promote acidic condensation.
🔧 Design Responses:
Challenge | Combustion Chamber Solution |
---|---|
Long drying time | Add pre-drying zones or extended grate/furnace length |
Flame instability | Design gradual air staging to avoid sudden cooling |
Low burnout | Provide longer residence time (large combustion chamber) |
Efficiency drop | Use waste heat to pre-dry fuel or recirculate flue gas |
2. Volatile Matter: Effects on Flame Dynamics
Volatile matter includes hydrocarbons, tars, CO, H₂, and light gases released when the fuel is heated before it forms char. High volatility means a large fraction of the fuel combusts in gas phase.
Fuel Type | Volatile Matter (%) |
---|---|
Anthracite Coal | 5–8% |
Bituminous Coal | 20–30% |
Lignite | 35–45% |
Wood/Biomass | 65–85% |
🔥 Impact on Combustion:
Rapid Ignition: Can lead to flashback or blow-off if uncontrolled.
Concentrated Heat Release: Creates hot spots near burners.
Emission Risk: Without full oxidation, CO and VOCs increase.
Soot Formation: Volatiles may condense and form particulates.
🔧 Design Responses:
Problem | Design Adjustment |
---|---|
Early flame flash | Staged air injection to spread combustion |
Local overheating | Use swirl burners and flame stabilizers |
Poor burnout of gases | Design for secondary air injection |
Particulate emissions | Long flame path to allow complete burn-out |
📌 The design must match volatile release timing with available oxygen to ensure clean and efficient combustion.
3. Combined Influence on Combustion Chamber Layout
Moisture and volatile content don’t act in isolation—they interact:
Condition | Combustion Response |
---|---|
High moisture + high volatiles | Delayed ignition + rapid gas combustion → turbulent flame |
Low moisture + low volatiles | Slow, stable flame → longer residence time required |
High moisture + low volatiles | Hard to ignite, needs higher start-up energy |
Low moisture + high volatiles | Easy ignition, risk of overheating at burner tip |
📐 Practical Chamber Design Adjustments
Parameter | Low Moisture & Low Volatile | High Moisture & High Volatile |
---|---|---|
Furnace Size | Small | Large to allow drying and devolatilization |
Burner Design | Simple | Complex with staged injection |
Air-Fuel Ratio Control | Less sensitive | Must be finely tuned |
Heat Transfer Surface | Higher downstream | More upstream for moisture evaporation |
4. Design Case Study: Bituminous Coal vs Biomass
Parameter | Bituminous Coal | Biomass (e.g., Wood Chips) |
---|---|---|
Moisture (%) | 10–15 | 30–55 |
Volatile Matter (%) | 20–30 | 65–80 |
Flame Type | Stable, compact | Fluctuating, elongated |
Chamber Length | Short–Medium | Long, staged |
Grate or Bed Design | Smaller, high-temp | Wider, for drying and uniform burn |
Air Staging | Minimal | Crucial for phased combustion |
🛠️ Biomass combustion chamber must combine drying, pyrolysis, and burnout zones seamlessly.
5. Effects on Boiler Efficiency and Maintenance
Attribute | Negative Effect of Poor Design |
---|---|
Thermal Efficiency | Heat loss in drying and incomplete combustion |
Emissions | CO, VOCs, NOx increase if flame is unstable |
Slagging/Fouling | Wet fuel causes clinkers and fouling |
Corrosion | Steam condensation can corrode low-temp surfaces |
Fuel Flexibility | Rigid design cannot accommodate variable fuels |
Boiler chambers not tailored to moisture and volatility can suffer from low efficiency and high emissions.True
Chamber design must match fuel drying and devolatilization behavior to prevent instability and energy loss.
Summary
Fuel moisture content and volatility are key thermal design parameters that shape how combustion chambers are dimensioned and engineered. High-moisture fuels demand long residence time and pre-drying capability, while high-volatile fuels require carefully managed ignition zones and air staging. Whether burning biomass, coal, or blends, a combustion chamber must be tailored to how the fuel evolves during heating, to ensure optimal flame stability, heat transfer, and emissions performance.
Failing to consider these properties can result in unstable flames, increased emissions, slagging, and reduced efficiency—leading to costly maintenance and regulatory challenges.

What Boiler Types Best Match Different Primary Fuels Used in Power Plants?
Power generation demands high efficiency, consistent performance, and low emissions—all of which hinge on selecting the right boiler type for the specific fuel used. A mismatch can lead to poor combustion, low thermal efficiency, or excessive emissions. Each fuel—whether coal, oil, gas, biomass, or waste—has unique combustion characteristics. Choosing the wrong boiler system can result in frequent failures, expensive retrofits, or non-compliance with regulations. To ensure reliable output and cost-effective operation, the boiler design must suit the fuel’s volatility, moisture, ash behavior, and calorific value.
Different boiler types are specifically optimized for distinct fuel types based on combustion behavior, efficiency goals, and emission constraints. Pulverized Coal (PC) boilers suit high-grade coal, Circulating Fluidized Bed (CFB) boilers handle low-grade and mixed fuels, biomass boilers are tailored for plant-based materials, and oil/gas-fired boilers use highly controllable fuels with clean combustion.
Matching boiler to fuel is critical to maximize efficiency, reduce emissions, and meet environmental regulations.
Different fuel types require specific boiler technologies for optimal performance.True
Boiler combustion systems must be engineered to handle the fuel's moisture, ash, and volatility to maintain efficiency and emissions compliance.
Let’s explore how key fuel categories align with the most suitable boiler types and what performance advantages or design differences each pairing brings.
🔥 1. Coal as Primary Fuel: Pulverized vs Fluidized Bed Boilers
Coal remains a major source of power generation. However, coal grade (ash content, moisture, volatility) determines the ideal boiler.
Coal Type | Best Boiler Type | Why It Matches |
---|---|---|
Bituminous/Sub-bituminous | Pulverized Coal (PC) Boiler | Fine pulverization allows efficient combustion in suspension |
Low-grade (Lignite, high ash) | CFB (Circulating Fluidized Bed) Boiler | Tolerant to low calorific value and ash variability |
✅ Pulverized Coal Boilers
High thermal efficiency (up to 45%)
Requires uniform high-grade coal
Suited for base-load operations
✅ Circulating Fluidized Bed (CFB) Boilers
Burn wide range of coals and even coal slurry
Lower NOx and SO₂ due to in-bed combustion and limestone injection
Ideal for waste coal and variable-quality fuel
💧 2. Natural Gas and Oil: Package and Modular Boilers
For plants relying on natural gas or liquid fuels, compact and responsive designs are preferred.
Fuel Type | Boiler Type | Benefits |
---|---|---|
Natural Gas | Water Tube or Once-Through Modular (OTM) | Rapid start-up, low emissions, high controllability |
Fuel Oil (LFO/HFO) | Fire-Tube or Packaged Steam Boilers | Flexible operation, easy maintenance |
✅ Water Tube Boilers (for gas)
High pressure and temperature capability
Compact footprint for high output
Low excess air requirements → high efficiency
✅ Fire-Tube/Packaged Boilers (for oil)
Simple construction for medium loads
Easy access for cleaning
Best for peaking or load-following
🌿 3. Biomass: Grate, CFB, and Gasification Boilers
Biomass fuels vary widely—from wood chips to bagasse to agricultural waste. Moisture and ash dictate the best boiler design.
Biomass Type | Recommended Boiler Type | Reasons |
---|---|---|
Woody Biomass | Fixed Grate or Moving Grate | Handles large particles and moisture variation |
Agricultural Waste | CFB or Bubbling Fluidized Bed (BFB) | Accommodates ash and volatile content |
Pelletized Biomass | Stoker or Chain Grate Boilers | Uniform size and energy density |
✅ Fixed/Moving Grate Boilers
Simple design for low-capacity systems
Slow-burning, ideal for wet wood
✅ CFB for Biomass
Handles mixed fuels
Effective emission control and ash utilization
✅ Gasification Systems (Advanced)
Converts biomass to syngas
Higher efficiency and lower emissions
Suited for CHP (combined heat and power) applications
🗑️ 4. Municipal and Industrial Waste: Fluidized Bed and Waste-to-Energy
For refuse-derived fuel (RDF) and other waste-based sources:
Waste Type | Best Boiler Match | Why |
---|---|---|
MSW / RDF | CFB or BFB Waste-to-Energy Boilers | Handles low CV, high variability, and moisture |
Industrial Sludge | Sludge Incinerator + Steam Boiler | Integrated combustion and heat recovery |
✅ CFB/BFB Waste Boilers
Large fuel tolerance
In-bed reaction minimizes NOx
Limestone bed for SO₂ control
🔁 5. Multi-Fuel Flexibility: Hybrid & Modular Boiler Systems
Some power plants need fuel flexibility due to seasonal supply, cost, or emissions regulations.
Scenario | Boiler Design | Advantages |
---|---|---|
Seasonal biomass + coal | Dual-fuel CFB Boiler | Shift between fuels without major retrofits |
Diesel backup for gas | Modular Dual-Fuel Package Boiler | Maintains reliability during gas outages |
Urban CHP system | Hybrid Biomass + Gas CHP Boiler | Combines low emissions with renewable energy |
📊 Fuel and Boiler Matching Matrix
Primary Fuel | PC Boiler | CFB Boiler | Water Tube | Fire Tube | Grate Boiler | Gasifier |
---|---|---|---|---|---|---|
Bituminous Coal | ✅ | ✅ | ❌ | ❌ | ❌ | ❌ |
Lignite/High Ash Coal | ❌ | ✅ | ❌ | ❌ | ❌ | ❌ |
Natural Gas | ❌ | ❌ | ✅ | ✅ | ❌ | ❌ |
Fuel Oil | ❌ | ❌ | ✅ | ✅ | ❌ | ❌ |
Wood Chips | ❌ | ✅ | ❌ | ❌ | ✅ | ✅ |
Agricultural Residue | ❌ | ✅ | ❌ | ❌ | ✅ | ✅ |
RDF/MSW | ❌ | ✅ | ❌ | ❌ | ❌ | ❌ |
🧪 Case Study: Multi-Fuel Power Plant in Southeast Asia
Plant Profile:
Fuels: Mix of biomass, coal, and RDF
Capacity: 100 MW
Emissions Cap: SOx < 50 mg/Nm³, NOx < 150 mg/Nm³
Solution:
Selected CFB boiler
Features: In-bed desulfurization, staged combustion, flexible feed system
Results: Achieved 90% availability across all fuels, 15% lower fuel cost per kWh
🧠 Summary
Selecting the correct boiler type for the fuel used in your power plant is non-negotiable for efficiency, emissions, and operational cost control. Pulverized coal boilers are perfect for high-grade coals, CFB boilers are flexible across fuels, while oil and gas units excel in control and compactness. Biomass and waste fuels need specialized combustion zones and ash handling systems. Hybrid and modular options expand operational reliability and adaptability in dynamic energy markets.
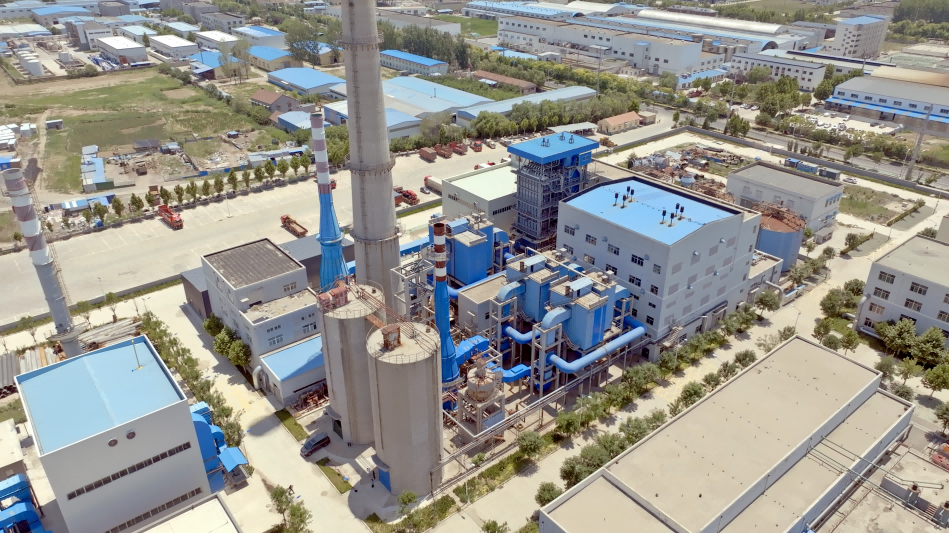
How Does Ash Content and Slagging Potential Impact Boiler Material Selection and Maintenance?
In coal and biomass combustion systems, the ash content and slagging behavior of the fuel are often underestimated—until damage occurs. Excessive ash or slag can cause corrosion, erosion, fouling, and unplanned shutdowns, compromising boiler longevity and performance. Plants using high-ash or variable fuels face constant challenges in material wear, refractory damage, and cleaning frequency. The good news? With the right material selection and boiler maintenance strategy, even ash-rich or slag-prone fuels can be managed without excessive cost or downtime.
High ash content and slagging potential directly impact the choice of boiler materials, especially in high-temperature areas like the furnace, superheater, and reheater tubes. Ash leads to fouling, erosion, or slag formation, which requires the use of corrosion-resistant alloys, wear-protective coatings, and proper sootblowing systems. Maintenance plans must also include frequent inspection, cleaning schedules, and replacement of wear-exposed surfaces.
Understanding your fuel’s ash chemistry is essential to designing a boiler that lasts and performs.
High ash and slagging fuels increase boiler wear and require stronger, more resistant materials.True
Ash components like silica, iron oxide, and calcium oxide can melt or fuse, forming slag that damages exposed boiler parts under high heat.
Read on to explore how ash and slag impact boiler design—and how to solve these challenges with material science, cleaning technologies, and predictive maintenance.
🔬 1. Understanding Ash Content and Slagging Tendency
Ash is the non-combustible residue left after fuel combustion. It can be present in solid form (bottom ash) or entrained in flue gases (fly ash).
Ash Parameter | Impact on Boiler |
---|---|
Ash Content (%) | Higher content → more fouling and slag buildup |
Ash Fusion Temperature | Low temperature → higher slagging risk |
Silica, Iron, Alkali Oxides | Promote sintering and adhesion on metal surfaces |
Particle Size | Fine particles → more erosion; coarse → blockage risk |
Ash slagging is the melting and sticking of ash particles to hot boiler surfaces. The slag layer can insulate heat transfer areas, corrode tubes, or even fall off in large chunks, damaging lower tube banks.
🏗️ 2. Material Selection for High-Ash and Slag-Prone Boilers
To survive harsh ash environments, boiler designers must select materials that:
Resist corrosion from acidic or basic slag layers
Withstand thermal shock from rapid slag detachment
Endure erosion from high-velocity ash particles
✅ Commonly Used Materials by Zone
Boiler Section | Recommended Materials | Why |
---|---|---|
Furnace Waterwall | SA-210, T91 (for subcritical), or Inconel overlays | High thermal strength, corrosion resistance |
Superheater / Reheater | T22, TP347H, or Incoloy 825 with weld cladding | Oxidation and chloride resistance |
Economizer | Carbon steel or 304 SS | Lower temperature, less slagging risk |
Air Preheater Tubes | Enamel-coated or corten steel | Resistant to acidic fly ash |
🔒 Use of Coatings and Overlays
Technique | Material/Method | Purpose |
---|---|---|
Weld Cladding | Inconel 625, Alloy 622 | Protects tubes from corrosive slag |
Ceramic Coating | High alumina/zirconia | Insulates against slag adhesion |
Thermal Spray Coating | Chrome carbide/nickel-based | Reduces erosion in high-velocity zones |
📊 3. Comparative Ash and Slagging Impact on Material Longevity
Fuel Type | Ash Content (%) | Slagging Risk | Required Material Grade |
---|---|---|---|
Bituminous Coal | 10–20 | Moderate | Carbon steel / T22 |
Lignite | 20–35 | High | T91 / Inconel overlay |
Biomass (e.g., straw) | 2–10 | Very High (alkali) | Stainless 310 / Ceramic coating |
Petroleum Coke | <1 but corrosive | Medium (low ash, high sulfur) | TP347H / High Cr-Ni alloys |
⚙️ 4. Ash Management Strategies to Minimize Material Degradation
Even the best materials can’t withstand unrelenting slagging without systematic ash handling and cleaning systems.
✅ Furnace and Heat Exchanger Cleaning Tools
Method | Application | Effectiveness |
---|---|---|
Sootblowers (Steam/Air) | Furnace, superheater | Removes soft/medium deposits |
Water lances | Economizer | For crusted ash layers |
Acoustic horns | Air preheater | Vibration loosens loose ash |
Explosive cleaning | Fouled tube banks | Removes hardened slag layers |
🧠 Predictive Monitoring
Ash deposit sensors detect slag growth and trigger cleaning
IR cameras identify hotspots indicating slag buildup
Boiler tube thickness mapping tracks erosion rates and schedules replacement
🧪 Case Study: Slag Control in a High-Ash Biomass Boiler
Background:
Boiler: 45 TPH biomass-fired stoker boiler
Fuel: Rice husk (12% ash, high silica, alkali metals)
Problem: Severe slagging on furnace tubes, unplanned outages every 30 days
Solution:
Upgraded waterwalls to T22 + ceramic spray coating
Installed high-pressure sootblowers on superheater
Switched from continuous feeding to batch feeding to manage flame temperature
Result:
Tube life extended by 2.5x
Cleaning interval increased to 75 days
8% increase in heat transfer efficiency
🧠 Summary
The ash content and slagging behavior of fuel directly determine how a boiler should be built and maintained. From material upgrades (such as Inconel overlays and ceramic coatings) to advanced cleaning systems, every aspect of high-temperature surface design must account for ash’s corrosive and adhesive nature. Regular inspection, deposit mapping, and sootblower automation can prolong the life of boiler components, reduce forced outages, and protect capital investment.
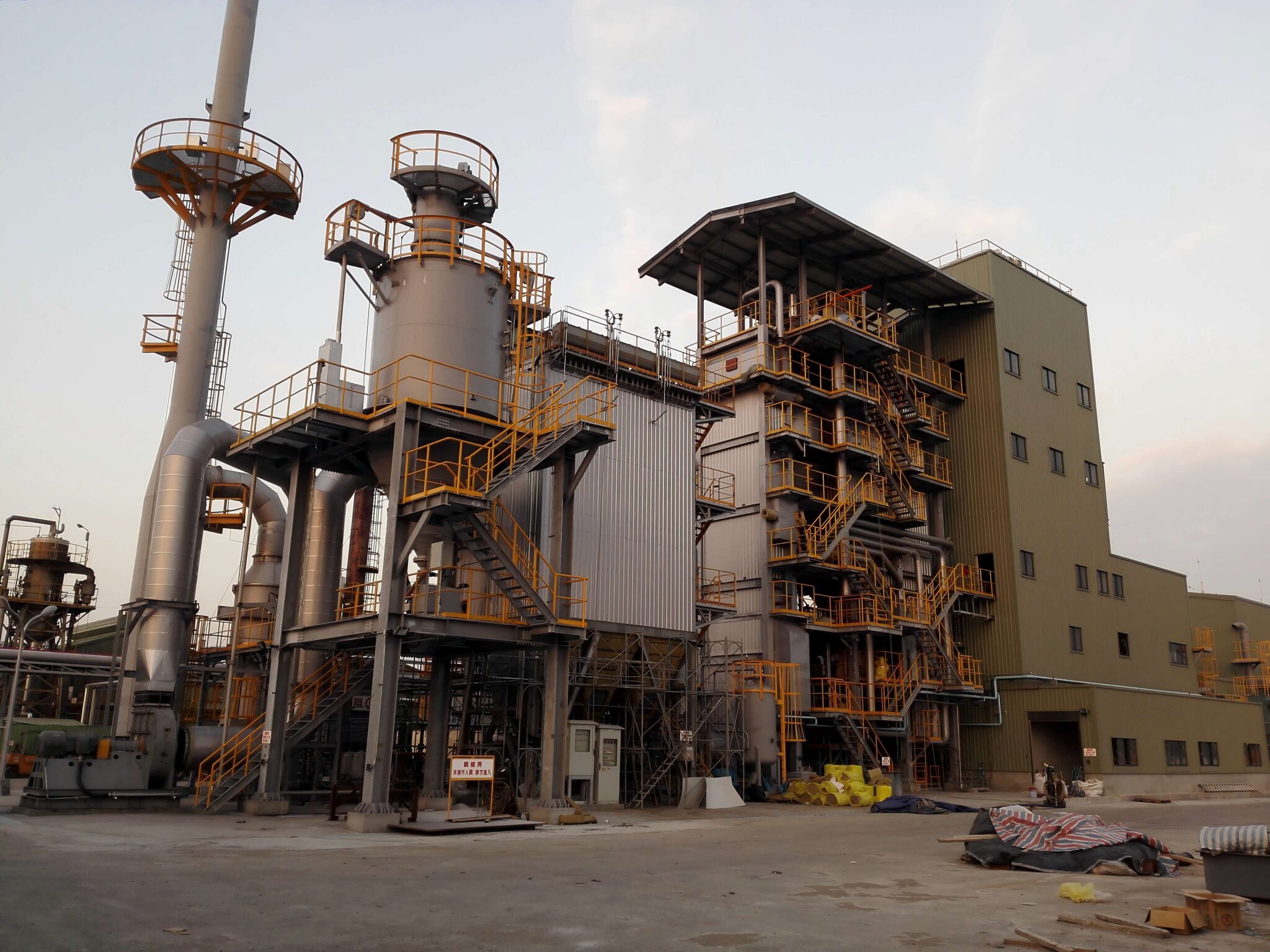
What Role Do Combustion Air Ratio and Flame Temperature Play in Efficiency and Emissions?
In industrial boiler systems, fine-tuning the air-fuel ratio and managing flame temperature are not just optional—they’re mission-critical. An incorrect air ratio leads to fuel wastage, unstable combustion, soot buildup, or worse, high levels of NOx or CO emissions. Meanwhile, flame temperature swings impact heat transfer rates, efficiency, and the formation of pollutants. These two variables—air and temperature—interact in complex ways, making them the focal point of combustion control strategies.
Combustion air ratio determines how efficiently fuel is burned, while flame temperature affects both heat transfer and pollutant formation. Too much excess air reduces efficiency by carrying heat out of the stack, while too little leads to incomplete combustion and high CO emissions. Flame temperatures that are too high increase NOx formation, while too low a temperature may reduce thermal efficiency and create unburned fuel residues. Balancing both parameters is essential to achieve optimal boiler performance and meet emissions regulations.
This article explores how these critical combustion parameters influence fuel usage, heat output, and air pollution—and how to optimize them in real-world industrial applications.
Too much excess air in a boiler reduces thermal efficiency.True
Excess air cools the combustion zone and carries unused heat out with the flue gases, lowering boiler efficiency.
Higher flame temperature always improves boiler performance.False
While higher flame temperatures can improve thermal efficiency, they significantly increase NOx emissions and may damage internal surfaces.
🔍 1. Understanding Combustion Air Ratio and Its Impact
The combustion air ratio (often referred to as lambda, or λ) is the actual air supplied divided by the theoretical air required for complete combustion.
Combustion Type | Air Ratio (λ) | Typical Outcome |
---|---|---|
Stoichiometric (Ideal) | 1.00 | Full combustion, but practically unstable |
Lean combustion (excess air) | 1.05–1.30 | Lower CO, safer operation, lower efficiency |
Rich combustion (air-deficient) | <1.00 | Higher CO/soot, incomplete combustion |
Too much excess air leads to:
Lower combustion temperature
Higher stack heat loss
Unstable flame if too lean
Too little air leads to:
Unburned hydrocarbons and CO
Soot formation
Potential flame instability
Modern burners use oxygen sensors and flue gas analyzers to adjust air in real time to optimize performance.
🔥 2. Flame Temperature and Its Double-Edged Role
Flame temperature affects:
Radiative heat transfer: Higher flame temperature means more radiant energy and faster heating.
Pollutant formation: NOx emissions are strongly linked to peak flame temperature.
Surface degradation: Excessive heat can damage refractories and tube metals.
Fuel Type | Typical Flame Temp (°C) | Notes |
---|---|---|
Natural Gas | 1950–2050 | Clean burn, high NOx risk |
Fuel Oil | 1850–1950 | More soot, moderate NOx |
Biomass | 1400–1600 | Lower NOx, variable flame profile |
Pulverized Coal | 1600–1750 | High ash fusion risk at elevated temps |
Zeldovich Mechanism: As flame temperature exceeds ~1500°C, thermal NOx formation increases rapidly.
📈 3. Flame Temp vs. Efficiency vs. Emissions Chart
Parameter | Low Temp (<1400°C) | Medium (1400–1650°C) | High (>1650°C) |
---|---|---|---|
Thermal Efficiency | Low | Optimal | May plateau/decrease |
Radiative Heat Transfer | Weak | Balanced | High but risky |
CO Emissions | High | Minimal | Minimal |
NOx Emissions | Low | Moderate | High |
Slagging/Material Stress | Low | Moderate | High risk |
⚙️ 4. Optimization Methods for Air and Flame Temperature
To achieve the ideal balance, modern boiler systems use a combination of control technologies:
✅ Key Technologies
Control System | Function |
---|---|
Oxygen Trim System | Adjusts combustion air based on O₂ readings |
Flue Gas Recirculation | Lowers flame temperature, reduces NOx |
Low-NOx Burners | Controls mixing to reduce peak temperatures |
Variable Speed Fans | Fine-tunes air delivery to match load |
Staged Combustion | Burns fuel in steps to control air/fuel zones |
Infrared Flame Sensors | Detects temperature variation for modulation |
📉 Real Example: Boiler Optimization with Air-Fuel Control
Boiler: 40 TPH gas-fired unit
Initial air ratio: 1.25 → Excess air loss = ~8%
Action: Installed O₂ trim + staged burner
Result: Air ratio reduced to 1.08; NOx cut by 28%, efficiency increased by 3.5%
🧠 Summary
Combustion air ratio and flame temperature are core parameters governing thermal efficiency, emissions, and equipment longevity in industrial boilers. While a lean air ratio minimizes CO and ensures full combustion, too much air reduces heat utilization. Similarly, while high flame temperatures improve heat transfer, they exacerbate NOx emissions and can damage equipment. The right solution lies in balanced combustion, achieved through real-time monitoring, intelligent burner design, and adaptive control systems.
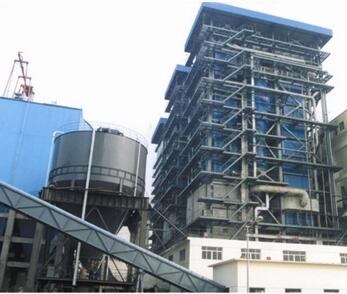
How Can Multi-Fuel Combustion Capability Future-Proof Your Power Plant Boiler Investment?
![High-efficiency industrial boiler system burning multiple fuels simultaneously with visual emission flow paths and automated control system dashboard]
Prompt: Multi-fuel industrial boiler system + high-tech style + diverse fuel feed mechanisms + emissions visualization + power plant environment + future-ready mood + clean white lighting
In today’s volatile global energy landscape, power plants that rely solely on a single fuel face increasing vulnerability. From price spikes and geopolitical disruptions to stricter carbon regulations and depleting local resources, fuel availability is becoming less predictable. Relying on a single-fuel boiler risks future downtime, higher operational costs, and even regulatory non-compliance. The solution? Design your boiler system with multi-fuel combustion capabilities from the outset. A multi-fuel-ready boiler not only secures energy supply but also gives you the operational flexibility to switch between conventional and renewable fuels as needed—future-proofing your power generation investment.
Multi-fuel combustion capability enables a boiler to operate efficiently and cleanly with more than one type of fuel—such as coal, natural gas, biomass, or RDF—either simultaneously or alternately. This flexibility helps plant operators manage fuel costs, ensure uninterrupted energy supply during fuel shortages, and comply with evolving emissions regulations. Multi-fuel boilers are designed with specialized burners, adaptable feeding systems, and combustion control logic to optimize performance across a range of fuel characteristics.
As fuel markets shift and sustainability requirements grow, investing in a multi-fuel-compatible boiler ensures long-term adaptability, competitiveness, and regulatory resilience.
Multi-fuel boilers are capable of switching between fossil and renewable fuels without major equipment changes.True
Modern multi-fuel boiler systems are engineered with flexible combustion zones, adaptable burners, and control logic to seamlessly transition between fuel types.
Multi-fuel combustion systems always reduce emissions.False
While multi-fuel capability offers flexibility, emissions vary depending on the fuels used and the system's emissions controls. Proper integration and tuning are essential.
🔍 Strategic Importance of Multi-Fuel Capability
Fuel flexibility allows a boiler to operate with:
Fossil fuels (e.g., coal, natural gas, oil)
Renewables (e.g., wood chips, agricultural waste, biogas)
Waste-derived fuels (e.g., RDF, plastics, sludge)
This flexibility is not just technical—it’s strategic:
Benefit | How It Future-Proofs Your Investment |
---|---|
Diversified fuel sourcing | Avoid over-dependence on any single market or political region |
Cost optimization | Switch to cheaper or locally available fuels during price hikes |
Renewable integration | Meet decarbonization targets without full system replacement |
Policy compliance | Respond faster to regional emissions or fuel use regulations |
Operational resilience | Maintain uptime during fuel shortages or disruptions |
⚙️ Boiler Design Features for Multi-Fuel Adaptability
🔧 Key System Adaptations
System Component | Adaptation for Multi-Fuel Use |
---|---|
Combustion Chamber | Designed for variable flame temperatures, slagging, and ash behaviors |
Burners | Multi-fuel or dual-fuel burners with automatic switching or mixing |
Fuel Feeding System | Multiple feeding lines for solid/liquid/gaseous fuels |
Air Supply & Mixing | Advanced air staging for varying fuel stoichiometry |
Flue Gas Treatment | SCR, baghouses, and wet scrubbers configurable for different fuel contaminants |
Control & Automation | Programmable logic for dynamic fuel changeover and combustion control |
📌 Case Example:
Plant: 120 MW Combined Heat & Power
Original Fuel: Natural Gas
Retrofitted For: Natural Gas + RDF + Wood Chips
Upgrades: Rotary grate + dual-feed injection + AI combustion logic
Result: 35% fossil fuel reduction, annual fuel cost savings of $2.1 million, reduced carbon intensity by 28%
📊 Multi-Fuel vs. Single-Fuel: Investment & ROI Comparison
Parameter | Single-Fuel Boiler | Multi-Fuel Boiler |
---|---|---|
Initial CAPEX | Lower | ~20–40% higher |
OPEX (over 10 years) | High fuel risk | Reduced due to flexibility |
ROI Timeline | Fixed on fuel stability | Resilient across market shifts |
Fuel Procurement Risk | High | Low to moderate |
Sustainability Rating | Limited | High |
Retrofitting Cost (future) | High | Minimal |
🌍 Regulatory Compliance and ESG Positioning
Governments worldwide are tightening fuel mandates:
EU: Fit-for-55 package mandates 55% CO₂ reduction by 2030
China: Dual-carbon goals push for hybrid and biomass fuel co-firing
India: Waste-to-energy integration required for urban industrial boilers
USA: EPA Clean Power Plan compliance with biomass blending
Multi-fuel readiness lets you meet regulations without massive retrofits.
🔁 Fuel Scenarios and Multi-Fuel Boiler Response
Scenario | How a Multi-Fuel Boiler Responds |
---|---|
LNG price spike | Shift to biomass or coal |
Government mandates 30% biomass blending | Adjust air-fuel ratio, auto-mix with gas |
Coal import disruption | Switch to RDF and local agri-residues |
ESG directive to lower CO₂ by 15% | Integrate biogas or pyrolysis gas |
These scenarios are becoming routine—not exceptional.
📘 Technical Design Considerations
H3: Fuel Variability Parameters That Must Be Addressed
Fuel Parameter | Design Consideration |
---|---|
Calorific Value | Variable heat input range |
Moisture Content | Pre-drying or excess air management |
Ash Content | Slag-resistant materials, frequent cleaning |
Volatile Matter | Burner tuning, staged combustion zones |
Fuel Particle Size | Custom feeding systems and turbulence control |
H4: Control and Monitoring Tools
Adaptive O₂ trim control
Multi-fuel PID combustion logic
Fuel blending ratio automation
Infrared flame analysis
Emission prediction AI modules
🧠 Conclusion
Designing your power plant boiler for multi-fuel combustion is not just a hedge against fuel cost volatility—it’s a strategic move to align with future energy trends, environmental regulations, and operational resilience. Whether you’re building new capacity or retrofitting old systems, multi-fuel capability ensures your capital investment remains viable across decades of evolving energy scenarios.
In a world that demands carbon cuts, flexible generation, and economic sustainability, multi-fuel adaptability isn’t optional—it’s the future-proofing key to success.
🔍 Conclusion
Fuel and combustion characteristics are foundational to making the right choice of industrial power plant boiler. A precise understanding of fuel behavior, combustion efficiency, and emission tendencies enables better decision-making that translates to lower operating costs, improved system reliability, and environmental compliance. By aligning boiler technology with fuel-specific demands, plant operators can ensure maximum output, long-term durability, and regulatory peace of mind.
📞 Contact Us
💡 Looking for expert advice on selecting a boiler based on your fuel type? Our engineering team specializes in fuel analysis, custom boiler design, and combustion optimization for industrial power plants.
🔹 Contact us today to ensure your power plant boiler is built to burn efficiently, cleanly, and profitably! ⚡🔥✅
FAQ
How do fuel types affect industrial power plant boiler selection?
The choice of fuel—coal, natural gas, oil, biomass, or waste heat—directly impacts boiler design, efficiency, emission controls, and cost. Different fuels require specific combustion chambers, feed systems, and emission management solutions.
Why is combustion efficiency important in power plant boilers?
Combustion efficiency determines how effectively fuel is converted into heat. Higher combustion efficiency reduces fuel consumption, lowers emissions, and increases overall boiler output, which is critical for power generation.
What role does fuel moisture and calorific value play in boiler design?
Fuels with low calorific value or high moisture (like biomass) need larger combustion chambers and pre-drying systems. High-energy fuels like oil or gas allow for compact, high-efficiency boiler designs.
How do combustion byproducts influence boiler choice?
Different fuels generate varying levels of ash, slag, or sulfur compounds. For instance, coal requires ash handling and flue gas desulfurization, while natural gas systems focus more on NOx control. These factors affect both capital and operating costs.
Can a power plant boiler be adapted to multiple fuel types?
Yes, multi-fuel boilers or hybrid designs can handle more than one fuel source, offering flexibility and energy security. However, they require complex control systems and must be designed for varying combustion properties.
References
Combustion Characteristics of Industrial Fuels – https://www.energy.gov
Fuel-Based Boiler Design Considerations – https://www.sciencedirect.com
Industrial Boiler Fuel Comparison – https://www.researchgate.net
Efficiency in Power Plant Boilers – https://www.iea.org
Fuel Moisture Impact on Boiler Performance – https://www.bioenergyconsult.com
Ash and Slag Management in Boilers – https://www.epa.gov
Multi-Fuel Boiler Technologies – https://www.mdpi.com
Boiler Fuel Selection Guide – https://www.energysavingtrust.org.uk
Combustion Efficiency and Boiler Sizing – https://www.automation.com
Flue Gas Emission Control in Power Plants – https://www.europa.eu
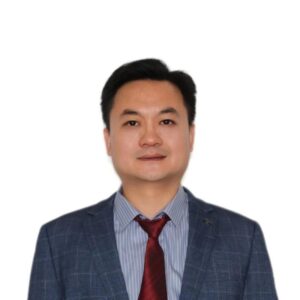