In high-capacity industrial operations, Circulating Fluidized Bed (CFB) boilers are prized for their fuel flexibility and emission control capabilities. However, without accurately measuring their thermal efficiency, operators risk facing unrecognized energy losses, excess fuel usage, and increased operational costs. Misjudging performance can also compromise environmental compliance and long-term boiler health. For CFB boilers, efficiency monitoring is especially critical due to the complexity of combustion dynamics and multi-fuel scenarios.
The thermal efficiency of a Circulating Fluidized Bed boiler is measured by calculating the ratio of useful heat output to total fuel energy input, typically using either the Direct Method (Input-Output Method) or the Indirect Method (Heat Loss Method). The Direct Method involves comparing steam output energy with fuel input, while the Indirect Method evaluates efficiency by subtracting the sum of various heat losses from 100%. Accurate efficiency measurement requires monitoring flue gas composition, excess air, unburned carbon in ash, fuel quality, and boiler load, all of which significantly influence combustion performance in CFB systems.
Read on to explore how you can accurately assess and optimize the efficiency of your CFB boiler.
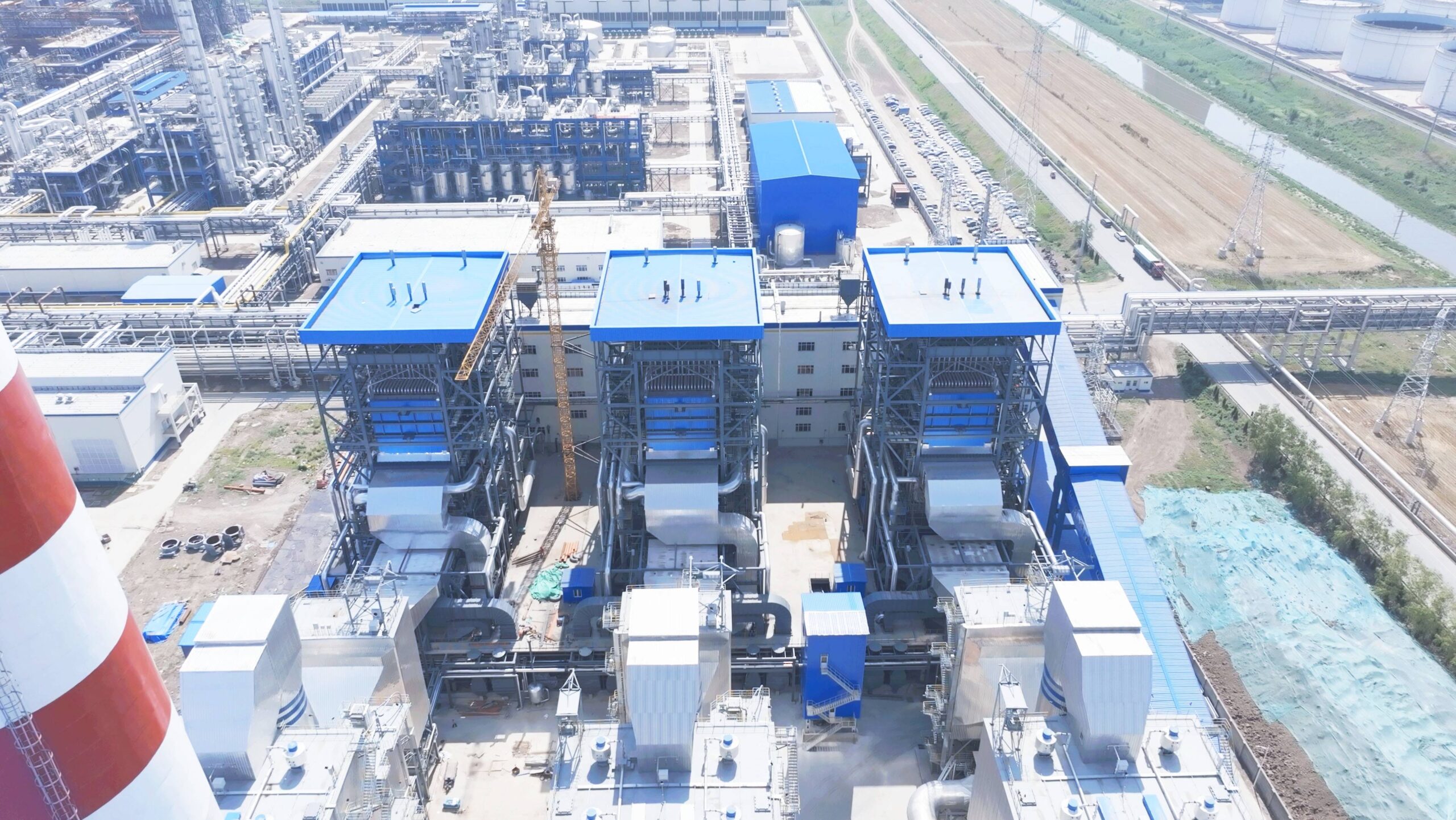
What Defines Thermal Efficiency in the Context of CFB Boiler Systems?
Thermal efficiency in Circulating Fluidized Bed (CFB) boiler systems is often misunderstood or overlooked, leading to suboptimal plant performance, wasted fuel, and increased emissions. Operators and engineers may not be aware of all the loss mechanisms unique to CFB technology, such as bed heat losses, carryover ash effects, or lower combustion temperatures compared to pulverized coal systems. If thermal efficiency is poorly understood, design oversizing, control tuning errors, and excessive operational costs can result. To maximize return on investment, emissions control, and heat recovery, it’s crucial to understand exactly how thermal efficiency is defined, measured, and optimized in CFB systems.
Thermal efficiency in a CFB boiler is defined as the ratio of the useful heat output (usually in the form of steam or hot water) to the total energy input from the fuel. It reflects how effectively the boiler converts fuel energy into usable thermal energy, accounting for heat losses through flue gases, unburned carbon, radiation, and ash discharge. Unlike conventional boilers, CFB systems require special consideration for fluidization dynamics, low combustion temperature zones, and solid recirculation patterns, which all influence efficiency.
Knowing this efficiency not only allows comparison across boiler types but also informs operational optimization and maintenance strategies.
Thermal efficiency in CFB boilers is lower than in pulverized coal boilers due to their lower combustion temperature.False
While CFB combustion temperatures are lower, the efficiency is often comparable or even higher due to superior heat recovery, longer residence time, and better control of combustion losses.
CFB boilers can operate efficiently with a wide range of low-grade fuels.True
CFB technology is inherently suited to burn low-calorific and high-ash fuels efficiently due to its robust combustion control and extended solid-gas contact.
CFB boilers operate under different principles than traditional boilers. Their design revolves around a fluidized bed of particles that allows fuel to be suspended and thoroughly mixed with air, creating uniform combustion. Unlike systems that rely on high flame temperatures, CFB boilers achieve high thermal efficiency through longer residence times, low excess air, staged combustion, and efficient heat transfer across immersed surfaces and heat exchangers. But measuring this efficiency involves carefully accounting for:
Fuel input energy (based on its lower heating value, or LHV)
Flue gas losses (temperature, excess air)
Moisture and ash losses
Bed drain and cyclone carryover losses
Radiation and convection losses
Let’s explore this more thoroughly.
🔍 Key Factors Influencing CFB Boiler Thermal Efficiency
🔧 Understanding Energy In vs. Energy Out
Component | Role in Thermal Efficiency |
---|---|
Fuel Calorific Value | Determines total energy input; low-quality fuels reduce available energy |
Flue Gas Temperature & O₂ Level | High stack temps or excess air indicate poor heat recovery and combustion |
Unburned Carbon in Ash (LOI) | A high loss on ignition means fuel isn’t fully converted to heat |
Bed Material Heat Loss | Energy lost with hot bed drain or cyclone solids |
Radiation & Surface Heat Loss | Occurs through boiler walls and surfaces; affected by insulation and ambient temp |
Boiler Blowdown Loss | Loss of high-temp water/steam used to control TDS in drum systems |
📊 Sample CFB Boiler Heat Loss Breakdown (Typical Ranges)
Loss Type | Typical Range (% of fuel input) |
---|---|
Flue gas loss | 5–12% |
Unburned carbon in fly/bottom ash | 0.5–3% |
Radiation & convection | 0.5–2% |
Bed material drain losses | 0.3–1% |
Moisture in fuel (if high) | 2–6% |
These loss elements must be subtracted from 100% to determine net thermal efficiency. For example, a well-tuned CFB boiler using a clean fuel can achieve thermal efficiency of 85–89%, while systems using moist, low-calorific biomass may drop to 75–80% due to higher moisture losses.
🛠 CFB-Specific Efficiency Influencers
1. Bed Temperature and Combustion Control
CFB boilers typically operate at ~850–900°C. This lower combustion temperature compared to PC boilers (~1400–1600°C) means reduced NOx formation and better control of sulfur capture with limestone—but it also requires:
Optimal fluidization velocity
Good fuel particle size distribution
Adequate oxygen staging to minimize CO and unburned carbon
These factors directly influence combustion efficiency and, by extension, total thermal efficiency.
2. Solid Recirculation and Cyclone Separation
High-efficiency cyclones in CFBs recover entrained solids and return them to the combustion chamber. If cyclone efficiency is poor, significant heat leaves the system with unburned solids. Designing for efficient solid recirculation reduces unburned carbon losses and improves overall combustion completeness.
3. In-Bed and Post-Combustion Heat Recovery
Unlike PC boilers that rely mostly on radiant heating in the furnace, CFB systems often utilize:
Immersed in-bed heat exchangers
External fluidized bed heat exchangers (FBHEs)
Economizers and air preheaters
Maximizing heat extraction from both in-bed and convective paths significantly boosts thermal efficiency.
🔄 Direct vs. Indirect Method in CFB Boilers
⚖ Efficiency Measurement Approaches
Method | Description |
---|---|
Direct (Input-Output) | Based on actual steam output vs. fuel energy input |
Indirect (Heat Loss) | Subtracts all known heat losses from 100% to calculate net efficiency |
The Indirect Method is more accurate for CFBs because:
It accounts for bed heat losses
It identifies hidden inefficiencies (e.g., moisture, carryover ash)
It’s less dependent on real-time load variation impacts
🧪 Instrumentation Needed for CFB Efficiency Tracking
Measurement | Purpose |
---|---|
Stack gas temperature | Determines flue gas heat loss |
O₂ and CO content in flue gas | Indicates combustion air tuning, efficiency, and excess air |
Unburned carbon in ash | Reflects fuel combustion completeness |
Bed pressure differential | Assesses fluidization quality |
Steam flow and enthalpy | Required to compute useful output |
Fuel flow and LHV | Needed for accurate input energy measurement |
🧠 Summary
In the context of Circulating Fluidized Bed (CFB) boiler systems, thermal efficiency is defined as the ratio of useful heat energy output to the total fuel energy input, taking into account various unique losses such as bed drain heat, unburned carbon in recirculated ash, and moisture from low-grade fuels. CFB boilers achieve competitive or even superior efficiency levels compared to traditional systems through enhanced fuel flexibility, low combustion temperatures, and extended heat recovery surfaces. A precise understanding of fuel characteristics, solid-fluid interaction, and combustion dynamics is essential to maintaining and improving thermal efficiency in modern CFB boiler operations.
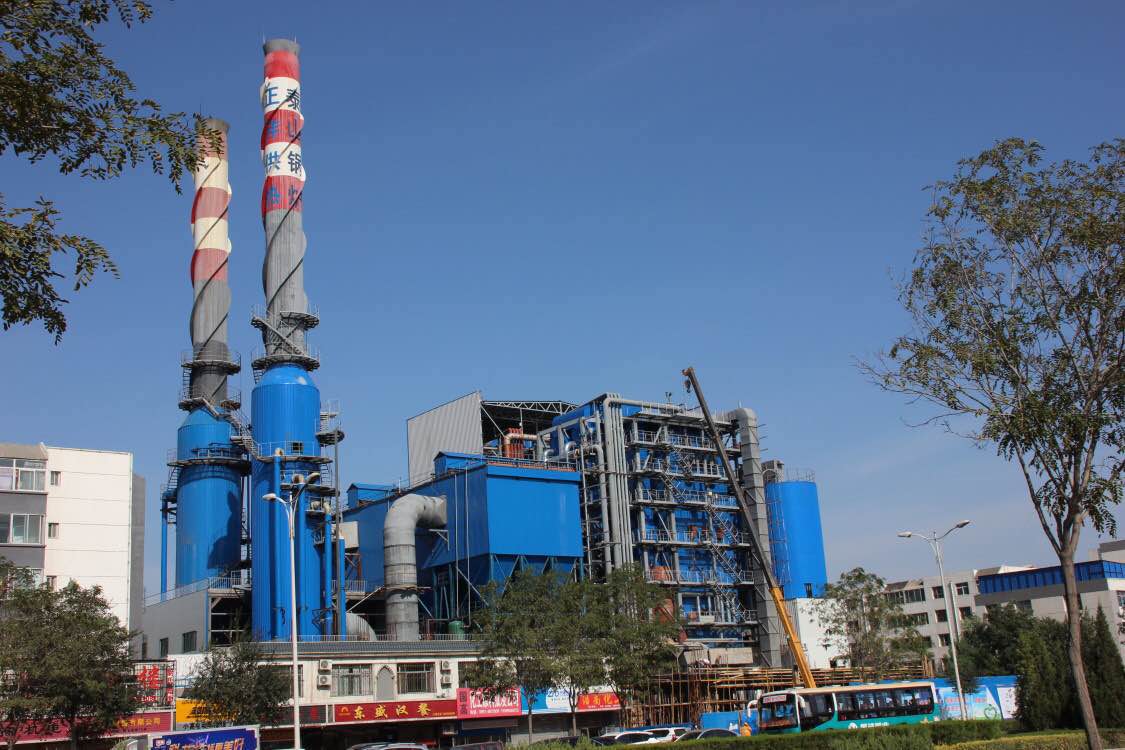
How Is the Direct Method Applied to Measure CFB Boiler Efficiency?
Measuring the efficiency of a Circulating Fluidized Bed (CFB) boiler is essential for controlling fuel costs, maintaining emission compliance, and optimizing operational performance. However, plant engineers and operators often find traditional measurement methods too complex or disconnected from real-time performance. This can lead to decisions based on assumptions rather than data—resulting in excess fuel use, reduced output, or even unnecessary shutdowns. The Direct Method offers a more straightforward, practical approach that enables real-time efficiency tracking based on output-versus-input energy, which is particularly helpful for day-to-day operations in CFB boiler systems.
The Direct Method measures CFB boiler efficiency by comparing the amount of energy contained in the steam generated by the boiler to the energy provided by the fuel input. It’s a simple energy balance: useful heat output divided by total fuel energy input. This approach gives a quick and approximate value of boiler efficiency without needing to assess individual heat losses.
For CFB systems, this method is practical when you have steady steam production and consistent fuel feed. It helps plant managers quickly verify performance or troubleshoot deviations from expected output.
The Direct Method ignores specific heat losses such as flue gas, moisture, or unburned carbon.True
The Direct Method does not individually quantify various losses, which are instead addressed by the Indirect Method. It is simpler but less diagnostic.
The Direct Method is the most accurate approach for detailed boiler heat loss analysis.False
While it provides a fast estimate of efficiency, the Direct Method lacks detail and precision, which the Indirect Method offers by accounting for all heat losses.
To apply the Direct Method to a CFB boiler, you simply need to know:
The steam output per hour (mass flow rate)
The enthalpy or heat content of the produced steam
The fuel input per hour
The calorific value (usually Lower Heating Value, or LHV) of the fuel
Once you have those, efficiency can be calculated by comparing the useful steam energy with the energy in the fuel used. Let’s explore this further with practical insights and case scenarios relevant to CFB technology.
🔍 Step-by-Step Guide to Applying the Direct Method for CFB Boilers
🔧 Key Inputs Required
Parameter | Purpose |
---|---|
Steam Flow Rate (kg/h or t/h) | Determines total heat output |
Steam Enthalpy (kcal/kg) | Based on pressure and temperature of the steam |
Feedwater Enthalpy (kcal/kg) | Input water temperature, usually at deaerator |
Fuel Consumption (kg/h or t/h) | Mass of fuel used in combustion |
Fuel Calorific Value (kcal/kg) | LHV, adjusted for moisture and ash |
📊 Example Calculation Overview (Without Formulas)
Let’s walk through an example of how a CFB boiler’s efficiency would be calculated using the Direct Method—no equations, just stepwise logic.
Steam Production Data:
A CFB boiler produces 50 tons of steam per hour at a given pressure and temperature.
Using steam tables, you find that each kilogram of steam at those conditions contains 850 kcal/kg of heat.
So, the total energy output = 50,000 kg/h × 850 kcal/kg = 42,500,000 kcal/h.Feedwater Energy Input:
The feedwater entering the boiler is at 105°C, and has about 105 kcal/kg of energy.
So, you subtract this from the steam enthalpy to find the net heat added per kg of steam.Fuel Input Data:
The CFB boiler burns 6,000 kg of coal per hour, with a calorific value of 7,200 kcal/kg.
Total energy input = 6,000 kg/h × 7,200 kcal/kg = 43,200,000 kcal/h.Efficiency Estimate:
Now compare the energy output (from steam) to the energy input (from fuel).
In this case, it gives an efficiency estimate close to 98.4% (idealized).In real scenarios, correction factors may be applied for moisture, load variation, and other operational anomalies.
⚠ CFB Boiler-Specific Notes on Direct Method Application
✅ Advantages
Quick and easy: Great for on-the-fly plant diagnostics
Minimal instrumentation required: Useful when detailed data collection is unavailable
Operational tuning: Helps detect shifts in combustion or output trends
❌ Limitations
No insight into where losses occur (e.g., flue gas, bed drains, ash)
Assumes stable operating conditions, which may not apply in load-cycling or multi-fuel scenarios
Accuracy limited by assumptions about steam conditions and fuel quality
📋 Typical Direct Method Efficiency Ranges by Fuel Type in CFB Boilers
Fuel Type | Expected Efficiency Range (Direct Method) |
---|---|
Bituminous Coal | 84% – 88% |
Lignite or Brown Coal | 78% – 84% |
Biomass (high moisture) | 70% – 80% |
Petroleum Coke | 83% – 87% |
Refuse-Derived Fuel (RDF) | 65% – 75% |
These values are indicative and depend on load, fuel preparation, and combustion control.
🧠 Summary
The Direct Method is a simple, fast way to estimate the thermal efficiency of a CFB boiler by comparing the heat content of the produced steam to the energy content of the fuel input. While it lacks the granularity to diagnose specific inefficiencies like heat loss from flue gas or unburned carbon, it remains a valuable tool for operational benchmarking, troubleshooting, and on-the-spot efficiency assessments. For long-term performance optimization, however, it should be complemented with more detailed methods and instrumentation.
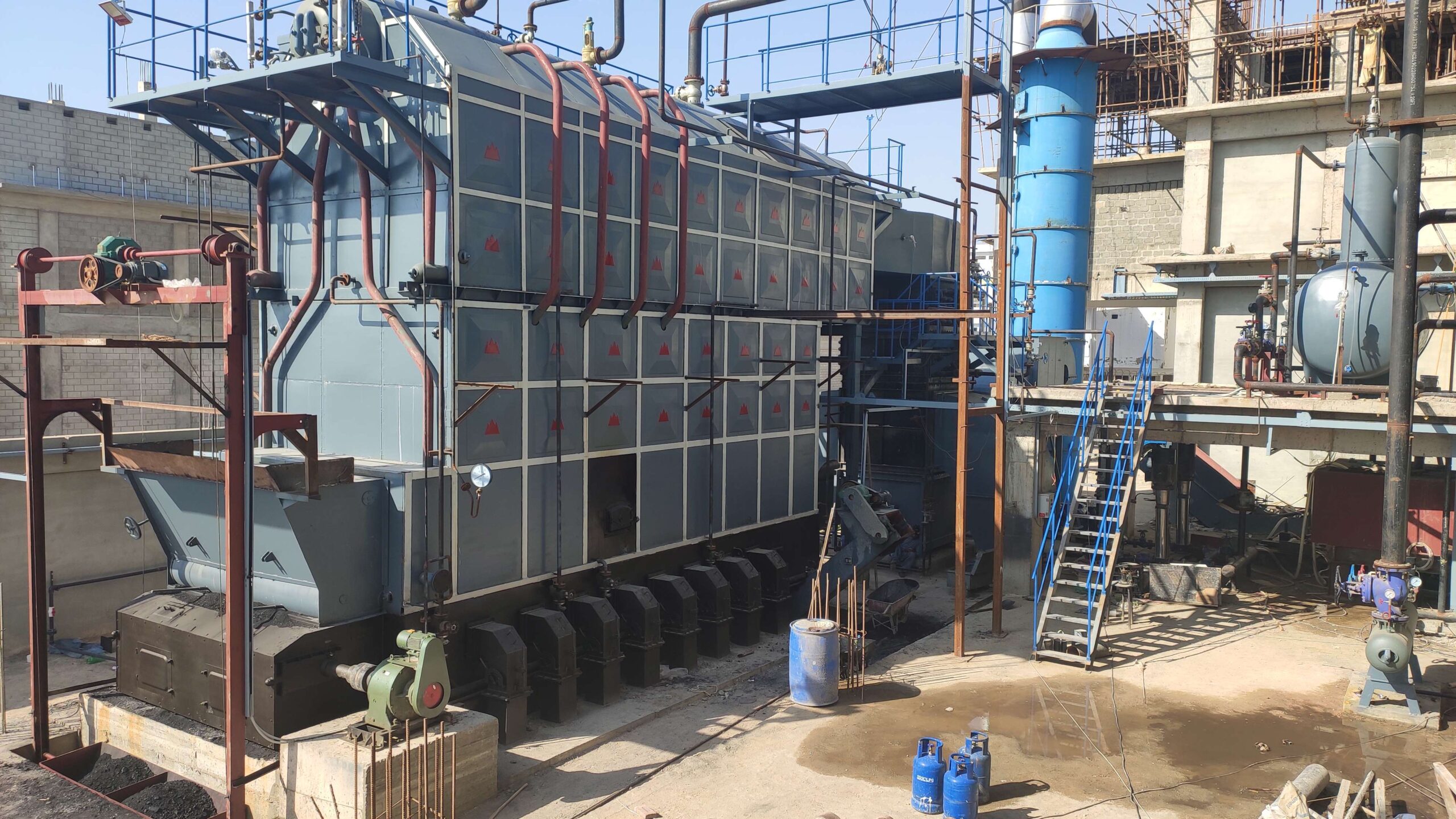
What Parameters Are Needed for the Indirect Method in CFB Boilers?
In large-scale industrial CFB (Circulating Fluidized Bed) boiler operations, relying solely on quick estimates of efficiency often leads to hidden energy losses and performance issues. Many operators focus only on fuel input and steam output, missing the bigger picture of where efficiency is lost. The Indirect Method—also known as the Heat Loss Method—is an advanced, diagnostic approach that calculates boiler efficiency by summing all identifiable heat losses. This method is crucial for precision tuning, troubleshooting, emissions control, and optimizing multi-fuel combustion systems in CFB boilers.
The Indirect Method calculates boiler thermal efficiency by subtracting all identifiable heat losses (such as flue gas loss, moisture loss, and unburned fuel) from 100%. To apply this method in a CFB boiler system, you must collect a full set of operational, combustion, and flue gas data, including temperatures, gas composition, fuel analysis, and ash characteristics.
While more complex than the Direct Method, the Indirect Method is indispensable for improving combustion efficiency and identifying loss mechanisms specific to CFB designs, such as high ash loads or low-grade fuel burning.
The Indirect Method requires detailed flue gas composition and unburned carbon data.True
This method quantifies each loss component, which demands accurate flue gas and fuel residue measurements.
CFB boilers do not require the Indirect Method because they operate at inherently high efficiency.False
Even high-efficiency systems like CFBs can benefit significantly from detailed loss analysis to improve operations.
Let’s explore the exact data required to perform an accurate Indirect Method efficiency calculation for a CFB boiler system.
🔍 Required Parameters for the Indirect (Heat Loss) Method
To apply this method, the following types of data are essential. Each is tied to a specific type of heat loss in the boiler system:
Parameter | Purpose / Type of Heat Loss |
---|---|
Flue gas temperature (°C) | For calculating dry flue gas loss |
Ambient air temperature (°C) | Reference for air preheat and radiation losses |
Excess air level (or O₂/CO₂ content) | Used to estimate mass of flue gases |
Fuel moisture content (%) | Determines latent heat loss due to fuel-bound water |
Hydrogen content in fuel (%) | Affects formation of water vapor from combustion (latent loss) |
Moisture in combustion air (%) | Additional latent heat loss source |
Carbon content in bottom ash (%) | Measures unburned carbon loss from bed material |
Carbon content in fly ash (%) | Indicates combustion completeness |
Ash content of fuel (%) | To calculate unburned combustible loss |
Flue gas analysis (O₂, CO₂, CO, SO₂, NOx) | Required for gas flow and loss calculations |
Bed temperature and furnace temp (°C) | Supports accurate gas property modeling |
Boiler surface area and insulation data | Used for estimating radiation and convection losses |
Specific heat of flue gases (Cp) | Needed to calculate sensible heat loss in stack gases |
📊 Breakdown of Major Heat Loss Components
Loss Category | What You Need to Measure or Estimate |
---|---|
Dry Flue Gas Loss | Flue gas temp, gas analysis, Cp of gases |
Moisture Loss from Fuel | Fuel moisture content, fuel flow rate |
Moisture Loss from Air | Humidity of combustion air |
Loss due to Hydrogen in Fuel | Hydrogen content of fuel |
Unburned Carbon Loss (Solid) | Carbon content in ash (fly + bottom ash) |
Radiation and Surface Loss | Insulation quality, surface area, ambient and furnace temps |
These values are often obtained from instrumentation like:
Flue gas analyzers (O₂, CO₂, NOx, SO₂ readings)
Thermocouples at stack and ambient inlets
Fuel laboratory testing for ultimate and proximate analysis
Ash residue testing for unburned carbon content
📌 Why These Parameters Matter in CFB Boilers
CFB boilers have unique characteristics compared to pulverized coal or oil-fired systems:
High ash recirculation requires detailed analysis of unburned carbon in both bed ash and fly ash.
Fuel flexibility (e.g., biomass, lignite, RDF) leads to large variations in hydrogen and moisture levels.
Lower combustion temperature typically reduces NOx, but makes moisture and latent losses more pronounced.
Fluidization stability can be affected by inconsistent fuel size and feed, influencing combustion completeness.
Understanding and measuring these parameters gives plant engineers insight into where improvements can be made in:
Fuel preparation
Air-fuel ratio control
Bed temperature tuning
Ash handling system calibration
🧠 Summary
To perform a full Indirect Method efficiency analysis on a CFB boiler, you need a comprehensive set of combustion, fuel, ash, and flue gas parameters. These measurements enable you to account for all heat losses—including unburned carbon, latent heat from moisture, and flue gas sensible heat—which together provide a precise efficiency value. This level of insight is critical for long-term optimization, regulatory compliance, and fuel cost reduction in any CFB operation.
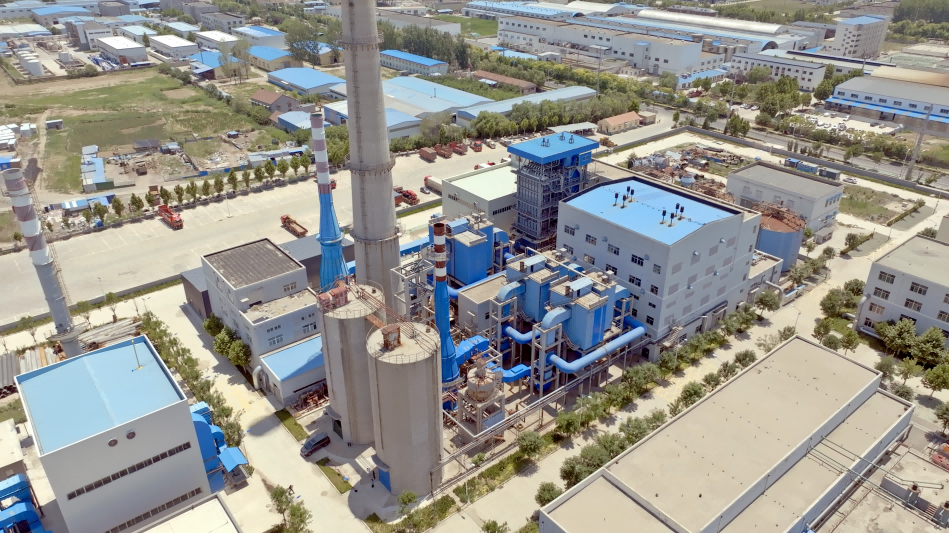
How Do Unburned Carbon and Fly Ash Losses Impact Efficiency Measurement?
In coal and biomass-fired boilers—especially in Circulating Fluidized Bed (CFB) and Pulverized Fuel (PF) systems—unburned carbon in fly ash is a hidden efficiency killer. Operators often overlook this residue assuming full combustion occurs, but in reality, inefficient firing, poor air distribution, or fuel inconsistencies can lead to substantial heat losses. These losses reduce fuel-to-heat conversion, inflate operating costs, and create discrepancies in boiler efficiency measurements if not accurately accounted for.
Unburned carbon and fly ash losses directly reduce thermal efficiency by representing a portion of the fuel energy that is not converted into usable heat. In the Indirect Method of boiler efficiency measurement, these losses are calculated based on the percentage of combustibles remaining in both fly ash and bottom ash. If ignored or underestimated, they lead to falsely optimistic efficiency figures and missed opportunities for combustion optimization.
Understanding this effect is critical in efficiency diagnosis and in benchmarking boiler performance across operational conditions, especially for variable fuels.
Unburned carbon in fly ash contributes to significant thermal losses in industrial boilers.True
Any unburned fuel means lost potential energy. Measuring this uncombusted residue accurately helps identify and reduce inefficiencies.
Fly ash is always fully combusted and has no impact on efficiency.False
In practice, incomplete combustion results in unburned carbon in fly ash, reducing efficiency and requiring accurate measurement.
Let’s examine how this factor is quantified and its implications for boiler design and operational control.
🔥 How Fly Ash and Unburned Carbon Affect Efficiency Calculations
Efficiency Method | Role of Unburned Carbon and Fly Ash |
---|---|
Indirect Method (Heat Loss) | Measures heat loss due to unburned combustibles in ash. Critical to accurate total heat loss. |
Direct Method (Input-Output) | Often ignores or underestimates these losses. Results in overestimated boiler efficiency. |
In CFB and other solid-fuel systems, fly ash may contain between 2–10% unburned carbon, depending on:
Fuel particle size and grindability
Air/fuel mixing uniformity
Bed temperature stability
Inadequate residence time in combustion zone
🧪 Measurement of Unburned Combustibles in Ash
To accurately include this loss in the Indirect Method:
Collect representative ash samples from fly ash collectors (e.g., ESP or baghouse) and bottom ash discharge
Perform Loss on Ignition (LOI) tests in the lab—this involves reheating the ash to determine how much unburned carbon is left
Calculate heat loss by correlating the carbon residue with the fuel’s gross calorific value
🧰 Formula-Free Heat Loss Estimation (Conceptual)
Let’s break this down into simpler conceptual steps without using complex formulas:
Determine the amount (percentage) of unburned carbon in fly ash.
Estimate the total ash output per hour from fuel consumption rate.
Multiply the unburned carbon amount by the fuel’s heat content.
Subtract this energy loss from the total heat available in the fuel.
The result gives you the real usable thermal energy, which determines boiler thermal efficiency.
📊 Sample Table: Effect of LOI on Boiler Efficiency
Parameter | Case A: Efficient Combustion | Case B: Poor Combustion |
---|---|---|
Fly Ash LOI (%) | 2.0% | 7.5% |
Total Ash Flow (kg/hr) | 2,000 | 2,000 |
Unburned Carbon (kg/hr) | 40 | 150 |
Fuel GCV (kcal/kg) | 4,500 | 4,500 |
Heat Lost (kcal/hr) | 180,000 | 675,000 |
Efficiency Loss Due to LOI (%) | ~1.2% | ~4.5% |
Interpretation: A high LOI in fly ash means more unburned carbon—and a larger chunk of your fuel’s energy is literally going up the stack unused.
🔍 Operational and Design Factors That Influence LOI
Factor | Impact on Unburned Carbon |
---|---|
Bed temperature (too low/high) | Reduces complete fuel burnout |
Particle size distribution | Larger particles don’t burn out in time |
Inadequate secondary air | Limits burnout of volatiles and char |
Poor air distribution in furnace | Creates localized under-fired zones |
Fuel reactivity and fixed carbon | Harder-to-burn fuels (e.g., anthracite) leave more residue |
CFB systems can mitigate these losses by:
Enhancing particle residence time through bed circulation control
Installing carbon burnout chambers
Implementing fly ash recirculation
Improving bed temperature consistency with staged combustion
💡 Summary
Unburned carbon and fly ash losses are critical components of thermal inefficiency in solid-fuel boilers. If left unmeasured or ignored, they distort performance evaluations and hinder optimization. Especially in CFB and biomass systems, these losses can reach several percentage points of the total fuel energy, making them a high-priority target for improvement. Through accurate measurement, better combustion control, and ash recirculation strategies, engineers can reduce LOI, recover energy, and enhance both economic and environmental boiler performance.
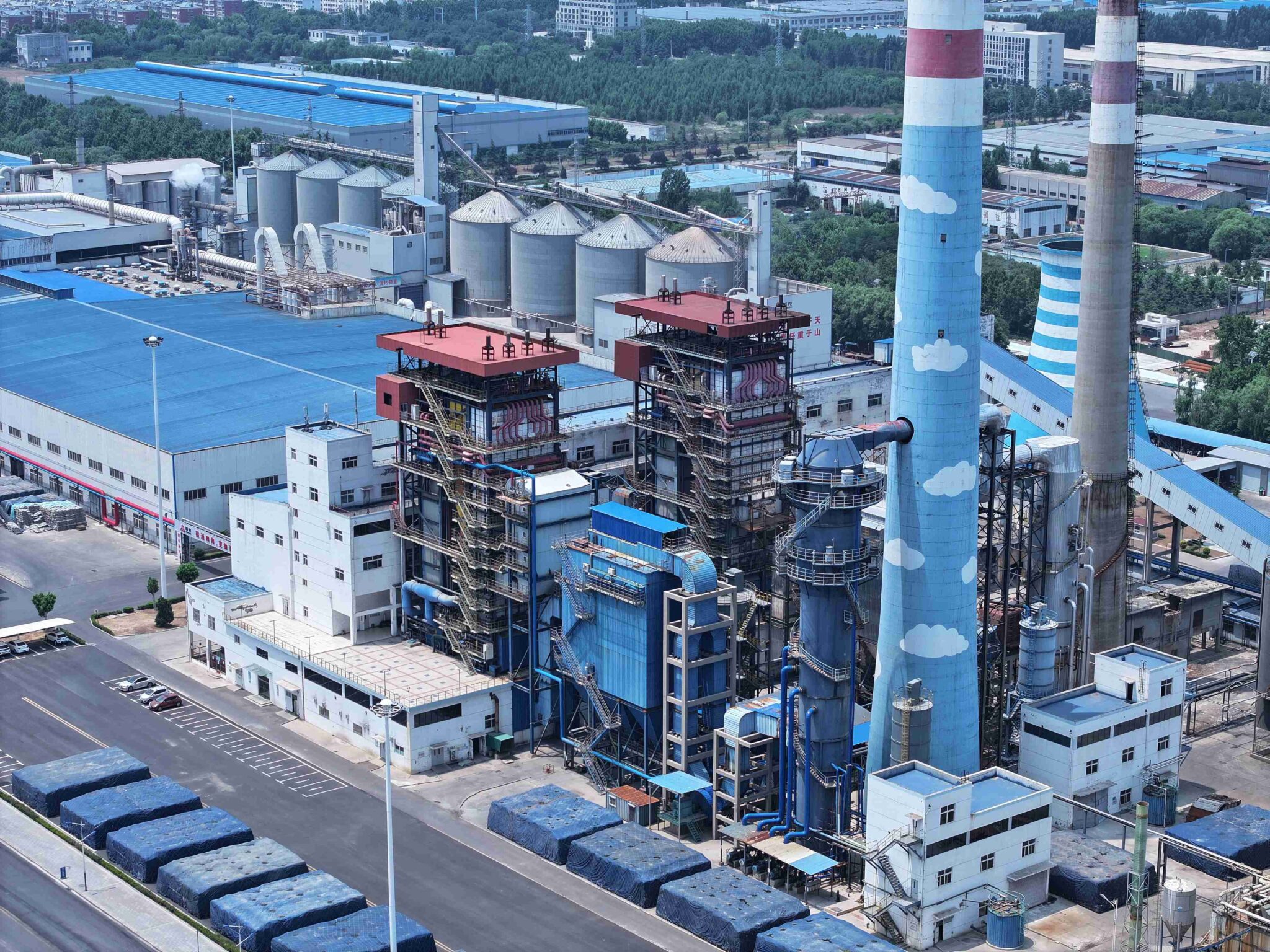
What Tools and Instrumentation Ensure Accurate Thermal Efficiency Evaluation?
Poorly measured data leads to misleading efficiency metrics, suboptimal performance, and rising fuel costs. In coal-fired and other industrial boiler systems, thermal efficiency must be tracked with high precision to inform tuning, emissions control, and fuel savings. However, many facilities either lack proper tools or rely on outdated methods, risking compliance failures or operational inefficiencies. The solution lies in a suite of modern, high-accuracy instruments that gather real-time, actionable performance data—empowering operators to optimize combustion and reduce losses consistently.
To ensure accurate thermal efficiency evaluation of industrial boilers, a combination of modern sensors, analyzers, flow meters, and data acquisition systems is essential. These instruments measure key parameters such as fuel flow, air/fuel ratio, flue gas composition, stack temperature, and steam output. When integrated properly, they enable both Direct and Indirect Methods of efficiency assessment, revealing combustion losses, unburned carbon, and radiation or convection inefficiencies in real time.
For engineers and plant operators, understanding what instrumentation is necessary and how it should be applied is critical for reliable boiler monitoring and optimization.
Flue gas temperature and oxygen content are essential for accurate boiler efficiency measurement.True
These values help identify combustion losses and determine if excess air is causing heat to escape without useful work.
Manual logging of steam flow and fuel usage is sufficient for modern boiler efficiency tracking.False
Manual readings are subject to human error, delays, and do not capture real-time variations necessary for precision efficiency optimization.
Let’s explore the essential tools involved in each stage of boiler efficiency evaluation and how they contribute to accurate assessments.
🔧 Essential Instruments for Efficiency Evaluation
1. Flue Gas Analyzer (O₂, CO₂, CO, SO₂, NOx)
These measure exhaust gas composition to evaluate combustion efficiency, excess air, and emissions. They are crucial for both direct and indirect efficiency calculations.
Use: Mounted in-stack or portable; ideal for tuning combustion air.
Precision Need: High sensitivity (<0.1%) to detect small combustion deviations.
2. Stack Temperature Sensor (Thermocouple or RTD)
Measures the temperature of gases exiting the boiler. Higher-than-optimal stack temperatures indicate excessive heat loss.
Use: Must be located at the flue gas exit, after air preheaters.
Material: Inconel or stainless RTDs/thermocouples withstand high flue gas temps.
3. Fuel Flow Meter (Mass or Volumetric)
Accurately measures the input energy (especially in direct method). For solid fuels like coal, gravimetric belt weighers or volumetric feeders are used.
Fuel Type | Preferred Meter Type | Measurement Accuracy |
---|---|---|
Natural Gas | Coriolis or Thermal Mass | ±0.1–0.5% |
Coal | Belt Scale + Calorimeter | ±1–3% (coal + CV error) |
Oil | PD Meter or Ultrasonic | ±0.2–1% |
4. Steam Flow Meter (Orifice, Vortex, Ultrasonic)
Measures the actual useful heat output. Often corrected to standard temperature and pressure for meaningful comparisons.
Installation: Requires proper straight-run piping.
Add-on Sensors: Pressure and temperature sensors are required for enthalpy correction.
5. Air Flow Meter (Pitot Tube, Thermal Mass, Ultrasonic)
Helps optimize air/fuel ratios. Excess air reduces efficiency, while insufficient air causes incomplete combustion.
Location: At Forced Draft (FD) fan outlet or air intake.
Integration: Used with control systems for dynamic air adjustment.
6. Ash Analyzer or LOI Tester
Loss on Ignition (LOI) tests determine unburned carbon in ash. This is key in indirect efficiency calculations to quantify combustion losses.
Offline Use: Ash samples collected from ESP or bottom ash hopper.
Real-time Options: Emerging online sensors available but costly.
7. Calorimeter (Bomb Calorimeter or Online CV Monitor)
Determines the actual energy content of the fuel. Critical for comparing input energy vs. output steam energy.
Type: Static bomb calorimeter or online CV meter for gases.
8. Data Acquisition and Control Systems (SCADA, DCS, PLC)
For aggregating, trending, and analyzing real-time data from all instruments. Allows operators to adjust combustion dynamically.
🧪 Table: Instruments Required for Direct vs. Indirect Efficiency Measurement
Parameter | Instrument | Direct Method | Indirect Method |
---|---|---|---|
Fuel Flow Rate | Mass or Volumetric Flow Meter | ✅ | ✅ |
Steam Flow Rate | Vortex or Ultrasonic Steam Meter | ✅ | ❌ |
Steam Pressure and Temperature | Pressure & RTD Sensors | ✅ | ❌ |
Flue Gas Temperature | Stack Thermocouple or RTD | ❌ | ✅ |
O₂/CO/CO₂/NOx/SO₂ in Flue Gas | Flue Gas Analyzer | ❌ | ✅ |
Ambient Air Temperature | RTD Sensor | ❌ | ✅ |
Combustibles in Ash (LOI) | Ash Analyzer or Lab LOI Test | ❌ | ✅ |
Fuel Calorific Value | Bomb Calorimeter or CV Sensor | ✅ | ✅ |
Data Logging & Integration | SCADA, PLC, or DCS System | ✅ | ✅ |
🧠 Common Issues Affecting Accuracy
Issue | Effect on Efficiency Evaluation |
---|---|
Fouled flue gas sensors | Skews excess air and heat loss calculations |
Poorly calibrated flow meters | Leads to incorrect steam/fuel input/output estimations |
Ash sampling inconsistency | LOI results become unreliable |
Missing ambient temperature readings | Miscalculates stack heat loss in indirect method |
Unstable power to sensors | Disrupts real-time logging and auto-tuning combustion |
🧩 Summary
Accurate boiler thermal efficiency evaluation depends on a well-integrated suite of modern instrumentation—ranging from gas analyzers and stack thermocouples to flow meters and ash testers. Both the Direct and Indirect Methods require specific data points, and the absence or miscalibration of even one sensor can undermine the reliability of the entire efficiency metric. By investing in real-time, high-precision measurement tools and ensuring proper maintenance and calibration, plant operators can unlock data-driven performance improvements, reduce emissions, and achieve long-term cost savings in fuel-intensive boiler operations.
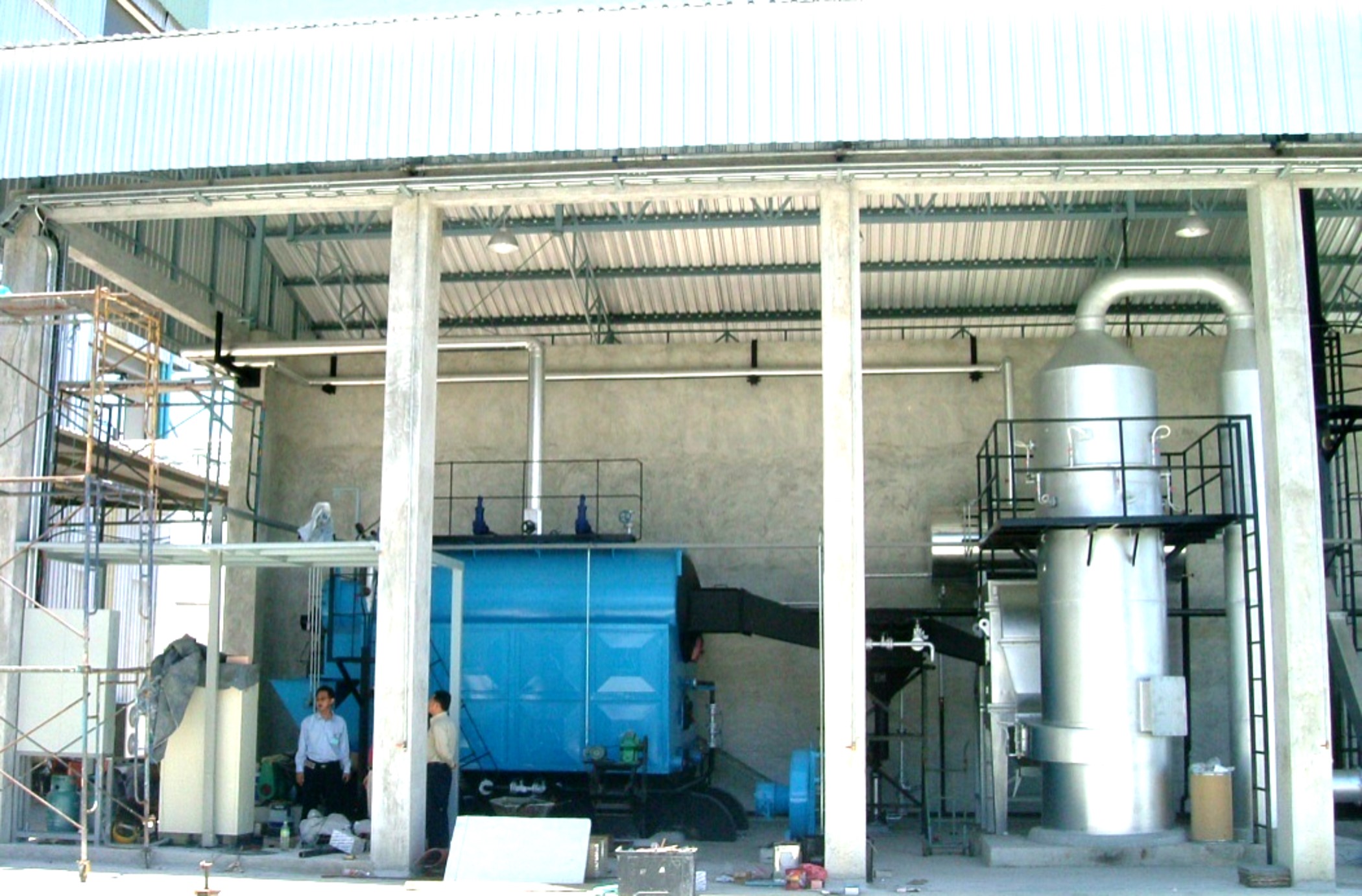
How Can Thermal Efficiency Data Be Used to Improve Fuel Savings and Operational Performance?
When thermal efficiency data is ignored or inaccurately tracked, the consequences ripple through an industrial plant—fuel is wasted, emissions exceed limits, and maintenance schedules become reactive rather than predictive. Many facilities operate with less-than-optimal combustion settings or outdated process controls simply because they lack the real-time insights that efficiency data provides. The good news? By properly harnessing thermal efficiency metrics, facilities can actively reduce fuel costs, extend equipment life, and meet regulatory targets. The key lies in transforming raw thermal data into actionable strategies for continuous performance optimization.
Thermal efficiency data helps industrial operators identify energy losses, optimize combustion conditions, and reduce fuel consumption by enabling precise adjustments to air/fuel ratios, burner settings, and load management. By tracking boiler performance trends over time, the data also supports predictive maintenance, system upgrades, and operator training—ultimately leading to higher operational reliability, lower costs, and improved environmental compliance.
If you want to enhance the performance of a coal, oil, gas, or biomass boiler, learning to interpret and act on thermal efficiency data is essential. Below, we explore the methods, tools, and real-world results associated with data-driven optimization strategies.
Thermal efficiency data can be used to reduce industrial boiler fuel costs.True
Improving combustion efficiency by even 1–2% can lead to significant annual fuel savings in large-scale boilers.
Thermal efficiency measurement has no impact on real-time operational adjustments.False
Real-time efficiency data enables immediate corrections in combustion tuning, load distribution, and air-fuel balance.
🔍 The Power of Thermal Efficiency Data in Operational Optimization
Thermal efficiency reflects how much of the energy in the fuel is converted into useful steam or heat. When monitored in real-time or analyzed historically, it becomes a lens through which operators can fine-tune processes and reduce waste.
1. Combustion Tuning and Air-Fuel Optimization
Problem: Excess air reduces efficiency by carrying heat out the stack; insufficient air causes incomplete combustion.
Action: Efficiency data pinpoints the ideal air-fuel ratio using flue gas O₂, CO, and stack temperature trends.
Result: Immediate fuel savings and improved combustion stability.
2. Load Management and Part-Load Efficiency
Problem: Boilers running far below design capacity often suffer from poor efficiency.
Action: Use thermal efficiency data to determine optimal load zones and avoid inefficient cycling.
Result: Smarter scheduling, reduced energy waste, extended life of equipment.
3. Identifying System Losses
Efficiency data helps detect:
Radiation and convection losses (measured via surface temperature sensors)
Blowdown losses
Heat losses in excess air
Unburned carbon in fly ash
Loss Type | Efficiency Impact (%) | Mitigation Strategy |
---|---|---|
Stack Loss (excess air) | 2–10% | Air damper adjustment, burner upgrade |
Unburned Carbon in Ash | 1–5% | Fuel grinding improvement, better mixing |
Radiation Loss | 0.5–3% | Insulation upgrade, refractory check |
Moisture in Fuel | 3–8% (biomass) | Fuel drying or blending strategies |
📊 Example: Thermal Efficiency vs. Fuel Savings
Efficiency (%) | Annual Fuel Use (tons) | Fuel Savings (tons/year) | Savings Value ($/year) |
---|---|---|---|
82 | 12,200 | – | – |
84 | 11,900 | 300 | $24,000 (at $80/ton) |
86 | 11,630 | 570 | $45,600 |
88 | 11,360 | 840 | $67,200 |
A 6% improvement in thermal efficiency saved ~$67,200 annually in this 10 TPH coal-fired boiler running 8,000 hours/year.
🔁 Using Data for Maintenance and Lifecycle Management
Trend Analysis: Identify gradual efficiency losses caused by fouling, wear, or control drift.
Predictive Maintenance: Schedule cleaning, soot blowing, or burner recalibration based on drop in efficiency, not fixed calendars.
Component Upgrades: Justify CAPEX for new economizers, burners, or controls with hard efficiency data ROI.
Alarm Integration: Trigger warnings when thermal efficiency drops below set thresholds.
💡 Real-Time Feedback Through Digital Platforms
Modern control rooms integrate sensors into SCADA, DCS, or cloud-based platforms:
Dashboards: Show live steam/fuel ratio, stack loss, and historical trends.
AI Analytics: Use machine learning to predict optimal settings.
Mobile Access: Operators can monitor thermal efficiency KPIs via tablets or smartphones.
🛠 Operator Training and SOPs Based on Efficiency Metrics
By using historical and live data:
Operators learn the exact effects of their inputs (damper position, burner flame shape).
Standard Operating Procedures (SOPs) are refined for optimal efficiency settings.
Human error is minimized by basing decisions on data, not guesswork.
Summary
Thermal efficiency data is more than a metric—it’s a continuous feedback loop that enables smarter fuel use, higher reliability, and reduced emissions in industrial boilers. By investing in accurate measurement tools and integrating efficiency tracking into daily operations, facilities can realize immediate cost savings and long-term performance gains. From combustion tuning and fuel blending to predictive maintenance and AI-driven control, every operational layer stands to benefit when efficiency is monitored, understood, and used as a decision-making tool.
📩 Ready to Reduce Fuel Waste and Optimize Boiler Performance?
Contact our engineering team today to implement a customized thermal efficiency monitoring and optimization solution tailored to your industrial boiler system.
🔍 Conclusion
Accurate thermal efficiency measurement is a cornerstone of smart CFB boiler management. It provides the insights needed to optimize combustion, reduce fuel consumption, and ensure regulatory compliance. Whether you use the Direct or Indirect Method, integrating efficiency measurement into your routine operations will help maintain long-term performance, reduce emissions, and enhance economic returns.
📞 Contact Us
💡 Need expert support in evaluating or improving your CFB boiler’s efficiency? Our team offers on-site diagnostics, combustion tuning, and advanced efficiency audits tailored to fluidized bed technology.
🔹 Connect with us today to boost your CFB boiler’s performance and savings! 🏭🔥📈
FAQ
What is thermal efficiency in a CFB boiler?
Thermal efficiency in a Circulating Fluidized Bed (CFB) boiler refers to how effectively the system converts the heat from fuel combustion into usable steam or energy. Higher thermal efficiency indicates lower fuel waste and better performance.
Which methods are used to measure the thermal efficiency of a CFB boiler?
There are two widely accepted methods:
Direct Method – Measures output vs. input energy directly.
Indirect Method – Accounts for all losses (flue gas, moisture, radiation, etc.) and subtracts them from 100% to find efficiency.
How is the Direct Method applied to a CFB boiler?
The Direct Method involves calculating boiler efficiency as:
Efficiency (%) = (Steam Output × Enthalpy Gain) / (Fuel Input × Calorific Value) × 100
It is fast and simple but doesn’t show where losses occur.
What does the Indirect Method reveal in a CFB boiler?
The Indirect Method provides a breakdown of energy losses due to factors like dry flue gas, moisture in fuel, unburnt carbon, radiation, and blowdown. It helps in pinpointing inefficiencies and areas for performance improvement.
Why is thermal efficiency important for CFB boilers in industrial settings?
Accurately measuring thermal efficiency helps improve combustion control, reduce fuel costs, lower emissions, and meet regulatory compliance. This is especially important for large-scale CFB systems used in power generation and industrial heating.
References
Thermal Efficiency in Industrial Boilers – https://www.energy.gov
CFB Boiler Performance Evaluation – https://www.sciencedirect.com
Direct and Indirect Efficiency Methods – https://www.researchgate.net
Circulating Fluidized Bed Boiler Overview – https://www.iea.org
Boiler Heat Loss Calculation Standards – https://www.epa.gov
Combustion Optimization in CFB Systems – https://www.mdpi.com
Steam Generation and Efficiency Basics – https://www.automation.com
CFB Technology and Efficiency Trends – https://www.bioenergyconsult.com
Energy Auditing for Boilers – https://www.energysavingtrust.org.uk
CFB Boiler Design and Operations Guide – https://www.power-eng.com
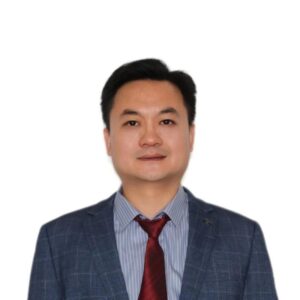