Measuring the thermal efficiency of an industrial oil-fired boiler is essential for understanding how effectively your system converts fuel energy into usable steam or hot water. Many operators focus on output without closely monitoring efficiency, which can lead to excessive fuel consumption, higher emissions, and avoidable operational costs. An accurate efficiency assessment helps uncover hidden losses, optimize combustion, and improve your bottom line.
Thermal efficiency of an industrial oil-fired boiler is calculated by comparing the useful heat output (typically in the form of steam or hot water) to the energy content of the input fuel. This is commonly done using two methods: the Direct Method, which evaluates the ratio of heat output to fuel input, and the Indirect Method, which estimates efficiency by subtracting various heat losses (flue gas, radiation, blowdown, etc.) from 100%. Accurate measurement involves tracking boiler output, fuel consumption, flue gas composition, and excess air levels.
Let’s break down the methods and tools needed to evaluate your boiler’s true performance.
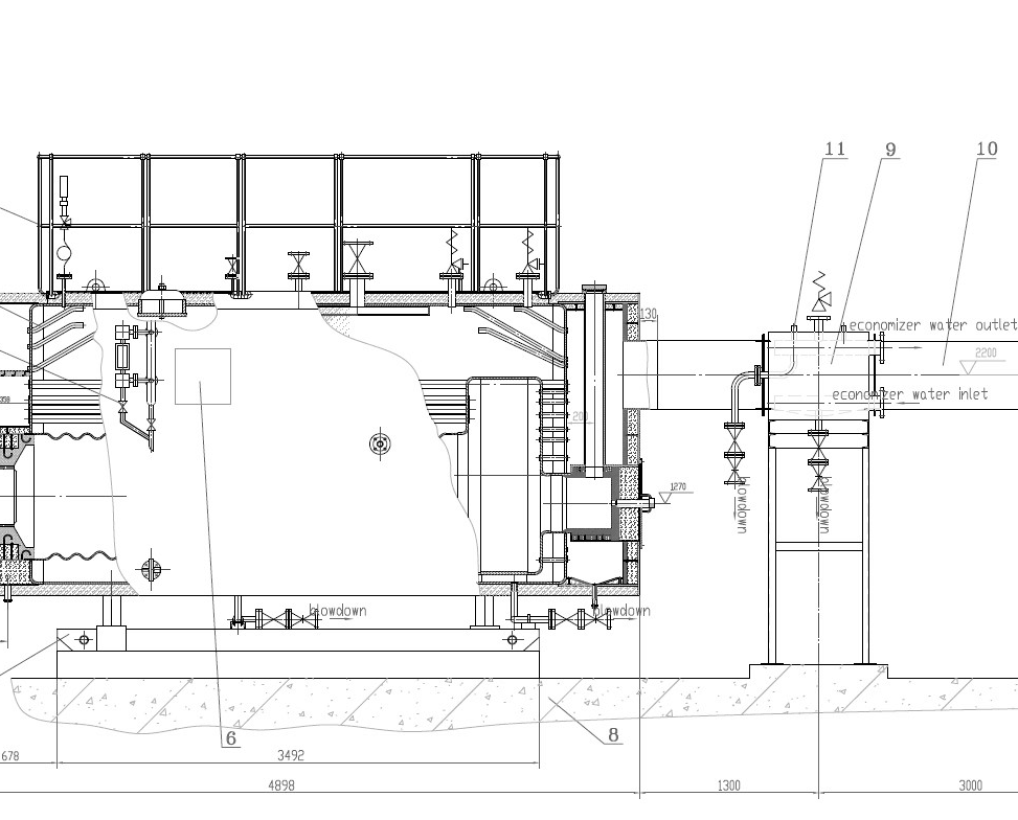
What Is Thermal Efficiency and Why Is It Critical for Oil-Fired Boiler Performance?
In oil-fired boiler systems, even a 1–2% drop in thermal efficiency can mean thousands of dollars lost annually in wasted fuel. Yet, many facilities lack clarity on what thermal efficiency actually means—or how it directly impacts fuel consumption, emissions, and long-term reliability. Without accurate monitoring and optimization, oil-fired boilers can quietly bleed energy, inflate operating costs, and fall short of regulatory targets. Understanding and improving thermal efficiency is not just a technical advantage—it’s an operational imperative.
Thermal efficiency in an oil-fired boiler refers to the ratio of useful heat output (such as steam or hot water) to the total energy content of the fuel consumed. It indicates how effectively the boiler converts the chemical energy in oil into usable thermal energy. High thermal efficiency means less fuel is wasted and more heat is delivered per unit of oil, directly improving performance, fuel economy, and environmental compliance.
Whether you operate in manufacturing, chemical processing, or power generation, maximizing thermal efficiency ensures optimal return on fuel investment while reducing emissions and equipment wear.
Thermal efficiency measures how much of the fuel’s energy is converted into usable heat.True
It compares the output of the boiler to the total fuel energy input, providing a performance benchmark.
Oil-fired boilers always operate at high thermal efficiency without adjustments.False
Efficiency depends on air-fuel ratio, combustion tuning, heat recovery systems, and maintenance. It must be actively managed.
🔍 How Is Thermal Efficiency Calculated in Oil-Fired Boilers?
Thermal efficiency is typically determined using two methods:
Method | Key Inputs | Application |
---|---|---|
Direct Method | Fuel consumption, steam output, steam enthalpy | Quick estimation during operation |
Indirect Method | Flue gas temperature, O₂/CO₂ levels, unburned fuel, radiation loss | Diagnostic, detailed analysis |
The Direct Method is fast but less detailed. The Indirect Method identifies losses due to:
Stack gas heat loss
Incomplete combustion (CO, unburned carbon)
Moisture from fuel
Radiation and convection
🧪 Typical Efficiency Ranges for Oil-Fired Boilers
Boiler Type | Thermal Efficiency (%) |
---|---|
Basic fire-tube boiler | 80–84% |
Condensing oil boiler | 88–94% |
High-efficiency water-tube | 85–90% |
Poorly tuned or fouled system | <78% |
Even at full load, over-ventilation or fouled heat transfer surfaces can silently drag efficiency down.
⚙️ Why Thermal Efficiency Is Critical to Oil-Fired Boiler Performance
1. Fuel Cost Control
Oil is a high-cost fuel. A 2% gain in efficiency can yield substantial fuel savings over time.
Example: A 10 TPH oil-fired boiler running 7,500 hours/year with 82% efficiency can save ~$36,000/year in fuel costs by improving to 85%.
2. Combustion Quality
High thermal efficiency reflects well-controlled combustion:
Correct air-fuel ratio (minimizing excess air)
Minimal CO and soot emissions
Stable flame with complete burnout
This reduces fouling, acidic corrosion, and unburned fuel waste.
3. Heat Transfer Optimization
Oil boilers rely on:
Clean fire-side and water-side surfaces
Efficient economizer and air preheater operation
Proper steam pressure/temperature tuning
Thermal efficiency helps spot when fouling or scaling is degrading performance.
4. Emissions and Compliance
Inefficient combustion increases:
NOx and CO emissions
Black smoke from incomplete fuel burn
Regulatory non-compliance risk
Optimizing efficiency is often tied to emissions permits and carbon reporting.
5. System Longevity and Maintenance
Efficient boilers experience:
Lower thermal stress
Less soot and scale buildup
Fewer emergency shutdowns
Which leads to lower maintenance costs and longer life.
📊 Real-World Efficiency Improvement Impacts
Parameter | Before Optimization | After Optimization | Improvement |
---|---|---|---|
Thermal Efficiency (%) | 82 | 87 | +5% |
Annual Fuel Use (tons) | 2,200 | 2,070 | -130 tons |
Fuel Cost ($/ton) | $650 | — | — |
Annual Fuel Cost ($) | $1,430,000 | $1,345,500 | $84,500 saved |
🛠 How to Improve Thermal Efficiency in Oil-Fired Boilers
Area | Action |
---|---|
Combustion System | Install O₂ trim controls, tune burners, reduce excess air |
Heat Recovery | Upgrade economizers, add air preheaters |
Surface Cleanliness | Implement regular sootblowing and water-side descaling |
Condensate Return & Feedwater | Use economizers to preheat, improve deaeration systems |
Fuel Quality | Use pre-heated heavy fuel oil, prevent sludge in storage |
Instrumentation | Use real-time efficiency monitoring via SCADA or PLC systems |
🧠 Summary
Thermal efficiency in oil-fired boilers is the foundational metric that links fuel economy, emissions compliance, and equipment performance. By accurately measuring and actively optimizing thermal efficiency, plant operators can reduce operating costs, improve combustion quality, extend boiler life, and stay within environmental limits. In today’s energy landscape, efficient oil-fired boiler operation isn’t optional—it’s essential for both profitability and sustainability.
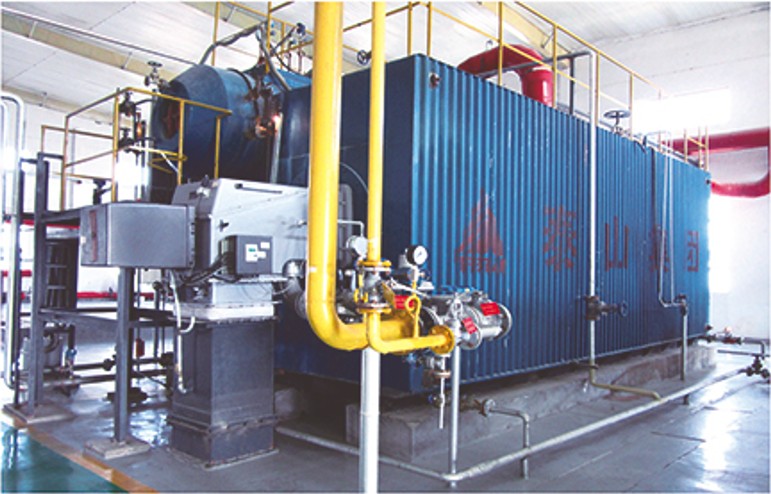
How Is the Direct Method Used to Measure Thermal Efficiency in Oil-Fired Boilers?
For oil-fired boiler systems, especially in industries where fuel costs are a significant operating expense, understanding thermal efficiency is key to controlling consumption and maintaining profitability. Many plants rely on rough estimates or historical norms, not realizing that real-time efficiency tracking using the Direct Method can expose hidden losses, justify tuning or upgrades, and prevent fuel waste. This method is the most accessible and operator-friendly approach to evaluate how effectively a boiler converts oil energy into usable steam or hot water.
The Direct Method measures thermal efficiency in oil-fired boilers by calculating the ratio of the heat output in the form of steam to the total heat input provided by the fuel. It requires measurements of steam output (flow and enthalpy), feedwater temperature, fuel consumption, and fuel calorific value. The method provides a quick and practical estimate of efficiency for routine monitoring and performance comparisons.
While it doesn’t pinpoint specific loss categories like flue gas or radiation loss, it’s an excellent tool for operational diagnostics and efficiency tracking over time.
The Direct Method provides a quick estimate of boiler efficiency by comparing output heat to input fuel energy.True
It calculates efficiency by measuring steam energy output against the energy content of consumed fuel.
The Direct Method requires complex heat loss breakdowns for accurate results.False
Unlike the Indirect Method, the Direct Method skips detailed loss components and relies on simple output vs. input values.
🔍 Key Parameters Required for the Direct Method
To apply the Direct Method in an oil-fired boiler, you need four main values:
Parameter | Purpose |
---|---|
Steam Output Rate (kg/hr) | Measures total heat produced by the boiler |
Steam Enthalpy (kcal/kg) | Based on steam pressure and temperature |
Feedwater Temperature (°C) | Used to determine the net heat added |
Fuel Consumption Rate (kg/hr or L/hr) | Total oil burned per hour |
Calorific Value of Fuel (kcal/kg or kcal/L) | Energy content of the oil |
🧩 Note: Fuel calorific value should ideally be the Lower Heating Value (LHV), especially for oil fuels, which produce water vapor during combustion.
🧮 Simplified Efficiency Estimation: Direct Method (No Complex Formulas)
Let’s walk through a practical, formula-free example of how the Direct Method is applied to an oil-fired boiler:
✅ Example Scenario:
Steam Output: 8,000 kg/h
Steam Enthalpy: 670 kcal/kg
Feedwater Temp: 105°C (Enthalpy ≈ 105 kcal/kg)
Net Heat per kg Steam: 670 – 105 = 565 kcal/kg
Total Useful Heat Output: 8,000 × 565 = 4,520,000 kcal/h
🔥 Fuel Input:
Fuel Used: 525 kg/h of heavy fuel oil
Calorific Value (LHV): 9,800 kcal/kg
Total Fuel Energy Input: 525 × 9,800 = 5,145,000 kcal/h
📊 Efficiency:
Thermal Efficiency = Useful Output / Fuel Input =
4,520,000 ÷ 5,145,000 ≈ 87.8%
This quick method helps identify whether your boiler is within acceptable performance ranges or losing energy through poor combustion, fouling, or bad air-fuel balance.
📘 Application Tips and Best Practices
Best Practice | Why It Matters |
---|---|
Use real-time flowmeters | Manual readings introduce errors; automated logging is better |
Ensure accurate fuel CV values | Variability in fuel quality skews the result |
Use condensate return data | Helps refine feedwater enthalpy and improve accuracy |
Integrate into SCADA/DCS | Enables trend tracking and alarm setup |
Compare over time and across loads | Identifies seasonal trends, part-load inefficiencies |
🧪 Benefits and Limitations
✅ Advantages:
Simple and quick
Requires minimal instrumentation
Ideal for daily monitoring and routine checks
❌ Limitations:
Doesn’t explain why efficiency is low (no breakdown of losses)
Sensitive to meter and calorific value accuracy
Not useful when the boiler load fluctuates rapidly
📊 Common Efficiency Ranges for Oil-Fired Boilers Using Direct Method
Boiler Type | Typical Efficiency (%) |
---|---|
Standard fire-tube | 82–85% |
Water-tube (well-tuned) | 85–88% |
Condensing boiler | 88–94% (if designed properly) |
Poorly maintained boiler | <80% |
🧠 Summary
The Direct Method is a simple, effective way to measure thermal efficiency in oil-fired boilers by comparing the energy output in steam to the energy input from oil fuel. It requires basic but accurate data on steam generation and fuel usage, making it ideal for daily operational monitoring, benchmarking, and fuel cost control. While it lacks the depth of diagnostic analysis provided by the Indirect Method, it remains one of the most practical tools for managing boiler efficiency in real-time industrial environments.

What is the Indirect Method and How Does It Help Identify Heat Losses?
In industrial energy systems, especially combustion systems like boilers or furnaces, inefficiency translates directly into wasted fuel and higher operational costs. Yet, one of the most critical challenges for plant managers and engineers is accurately pinpointing where these energy losses occur. Without a structured approach, identifying inefficiencies is like searching in the dark—leading to guesswork, suboptimal retrofits, or overlooked problems. Fortunately, the Indirect Method—also known as the Heat Loss Method—offers a systematic, data-driven way to quantify and understand various heat losses in thermal systems. This helps companies optimize combustion, improve boiler efficiency, and significantly cut down on wasted energy.
The Indirect Method, or Heat Loss Method, is a technique used to determine the efficiency of combustion systems by accounting for all measurable heat losses individually—such as dry flue gas loss, moisture loss, radiation, and unburnt fuel—so that their total can be subtracted from 100% to find system efficiency. This method is crucial for identifying specific inefficiencies in energy systems and guiding targeted corrective actions.
The simplicity and logic behind the Indirect Method make it extremely effective for practical diagnostics. Instead of trying to measure total energy output directly, which is often complex and error-prone, this method focuses on what is lost. By quantifying losses like flue gas temperature, excess air, or incomplete combustion, engineers gain a full picture of where fuel energy goes. If you’re a plant operator, energy auditor, or system designer, understanding this approach will allow you to precisely diagnose system inefficiencies, validate performance improvements, and make well-informed operational decisions.
The indirect method provides a more detailed analysis of heat losses than the direct method.True
The indirect method identifies individual loss components such as flue gas loss, radiation loss, and unburnt fuel loss, offering deeper diagnostic insights.
How Does the Indirect Method Work?
The Indirect Method calculates efficiency using the formula:
Boiler Efficiency (%) = 100 – (Sum of All Heat Losses)
These losses are derived from actual measurable parameters such as flue gas temperature, ambient air temperature, fuel composition, and oxygen content in flue gases.
🔍 Major Heat Loss Components
Heat Loss Type | Description | Typical Share of Total Losses |
---|---|---|
Dry Flue Gas Loss | Heat carried by hot exhaust gases | 5%–15% |
Moisture in Fuel Loss | Latent heat lost in vaporizing moisture in fuel | 1%–3% |
Moisture in Air Loss | Loss from vaporization of moisture in combustion air | 0.5%–1.5% |
Unburnt Fuel Loss | Heat lost due to unburnt carbon in fly ash or bottom ash | 0.2%–3% |
Radiation and Convection | Surface heat loss to surroundings | 0.5%–2% |
Hydrogen Combustion Loss | Heat lost through vaporization of water formed by hydrogen in fuel | 3%–5% |
📊 Example Heat Loss Calculation
Let’s consider a solid fuel boiler burning bituminous coal:
Parameter | Value |
---|---|
Flue gas temp (°C) | 200 |
Ambient temp (°C) | 25 |
% CO₂ in flue gas | 10.5 |
% O₂ in flue gas | 6.5 |
Moisture content in fuel (%) | 12 |
Unburnt carbon in ash (%) | 2.5 |
Hydrogen in fuel (%) | 4 |
Using empirical heat loss equations from ASME PTC 4.1 or BS 845-1:1987 standards, we can estimate:
Dry Flue Gas Loss ≈ 11%
Moisture Loss in Fuel ≈ 2.4%
Hydrogen Combustion Loss ≈ 3.6%
Radiation and Convection Loss ≈ 1.2%
Unburnt Carbon Loss ≈ 1.8%
Efficiency = 100 – (11 + 2.4 + 3.6 + 1.2 + 1.8) = 80%
This granular analysis is powerful because each component points to a specific system inefficiency: excess air, poor insulation, or suboptimal fuel handling.
Why Choose the Indirect Method?
✅ Diagnostic Power
Unlike the Direct Method—which only tells you the overall efficiency based on heat input vs output—the Indirect Method breaks it down. If your flue gas losses are high, you might reduce excess air. If unburnt carbon is high, you could optimize combustion settings or upgrade your burners.
✅ Fuel-Specific Customization
Whether you’re burning coal, oil, biomass, or gas, the Indirect Method accommodates differences in fuel properties and combustion chemistry. It provides tailored feedback rather than generic efficiency figures.
✅ Essential for Retrofits and Upgrades
When retrofitting a boiler or burner system, identifying which losses dominate is crucial. Reducing radiation losses might justify better insulation, while high moisture losses might warrant fuel drying solutions.
✅ Regulatory and Compliance Advantage
Many energy audits and environmental compliance processes require detailed breakdowns of losses. The Indirect Method’s detailed output aligns with ISO 50001, ASME standards, and energy-saving mandates.
Advanced Analytical Tools and Software Integration
Modern combustion monitoring systems integrate the Indirect Method into digital dashboards, allowing real-time tracking. SCADA and DCS systems now embed algorithms that continuously recalculate heat losses using sensor input, enabling automated diagnostics and alerts.
Tool/Software | Functionality | Benefit |
---|---|---|
Flue Gas Analyzer (e.g. Testo) | Measures O₂, CO₂, temperature | Key input for flue gas and moisture loss |
Smart SCADA Systems | Real-time heat loss calculation | Proactive maintenance |
ASME/BS-based Boiler Monitors | Compliance with industrial standards | Audit-readiness |
MATLAB or Python Scripts | Custom loss modeling and reporting | Advanced diagnostics |
Real-World Case Study
📍 Industrial Textile Mill (India)
Problem: High fuel cost and unverified boiler performance
Solution: Applied Indirect Method using portable flue gas analyzers and lab-analyzed fuel samples
Initial Efficiency | 72% |
---|---|
Dominant Loss | Dry Flue Gas (13%) |
Action Taken | Reduced excess air and improved burner tuning |
Result | Final Efficiency = 82% |
Fuel Savings | ₹3.8 million annually |
This level of targeted improvement would not be possible using only the Direct Method.
Future Trends: AI and Machine Learning for Heat Loss Diagnostics
AI models trained on combustion data sets are now capable of predicting loss patterns based on operational variables. Combined with IoT-enabled sensors, the Indirect Method is being automated high-frequency diagnostics, paving the way for autonomous energy optimization systems.
In summary, the Indirect Method stands out as an indispensable tool for any professional looking to reduce heat losses and improve thermal system efficiency. It not only pinpoints losses but offers actionable insights into how to reduce them, making it far superior to simpler output-only efficiency calculations.
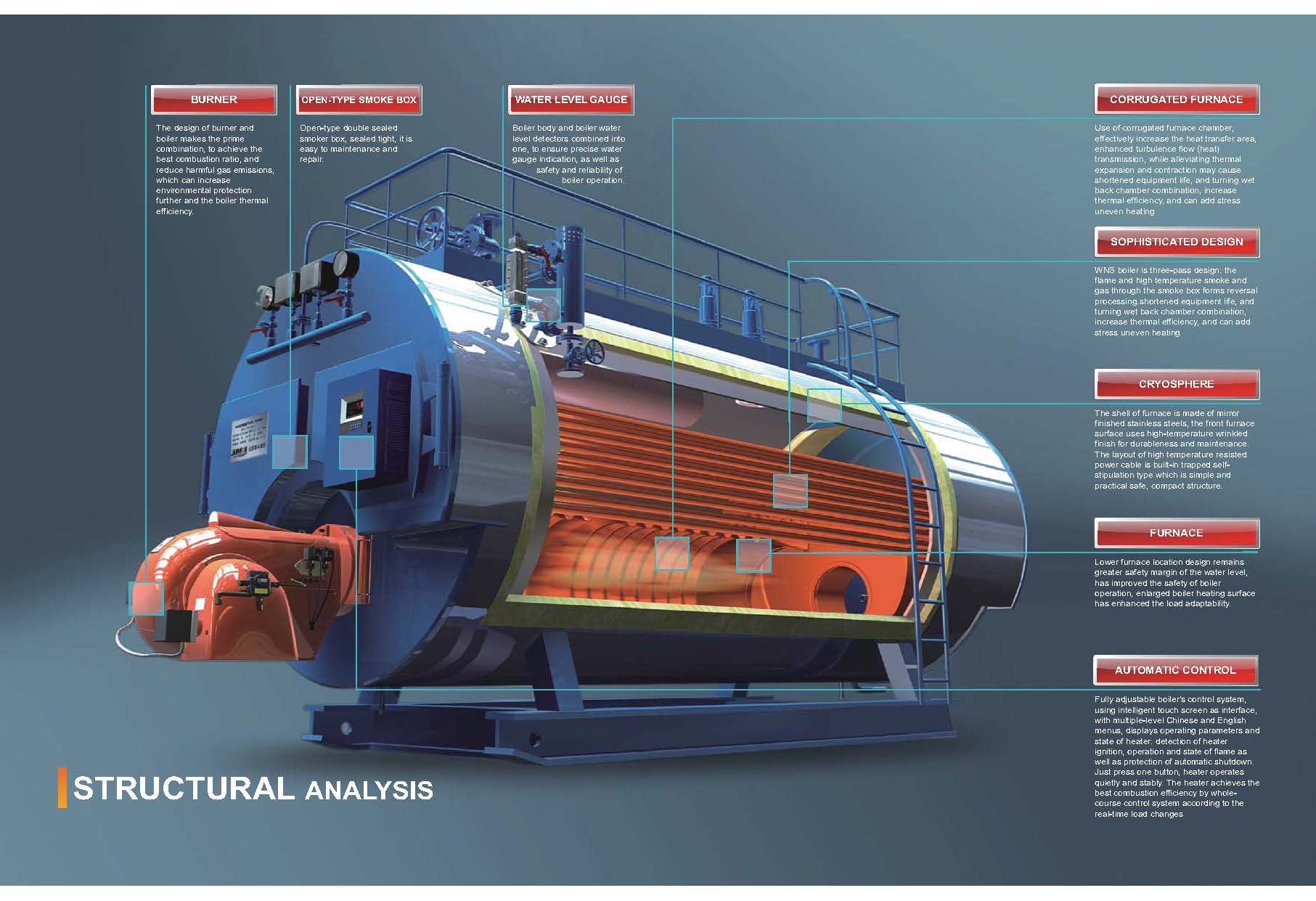
What Parameters Are Needed for an Accurate Efficiency Calculation?
In any industrial energy system—be it a power plant, manufacturing furnace, or commercial boiler—the efficiency of fuel-to-heat conversion is paramount. Poorly calculated efficiency not only leads to erroneous performance assumptions but also hinders fuel-saving initiatives and regulatory compliance. Unfortunately, many facilities rely on outdated, incomplete, or oversimplified methods that yield inaccurate results. The consequence? Wasted fuel, uncontrolled emissions, and loss of competitive advantage. To prevent this, you must ensure that all relevant and precise parameters are measured and used in the calculation. Understanding which inputs matter and why is the key to improving accuracy and optimizing operations.
Accurate efficiency calculation—particularly when using the indirect (heat loss) method—requires comprehensive and precise measurement of multiple parameters including flue gas composition (O₂, CO₂, CO), flue gas temperature, ambient air temperature, excess air, fuel composition (carbon, hydrogen, moisture, ash content), feedwater temperature, steam temperature and pressure, and losses due to unburnt fuel and radiation. These parameters must be measured using calibrated instruments under steady-state conditions to ensure reliable results.
To get the most out of your efficiency analysis, especially in a combustion system, you need to go beyond generic formulas and capture the real operating conditions of your system. Let’s walk through the critical parameters and explore how each directly influences the accuracy of efficiency calculations.
Flue gas oxygen content is a necessary parameter for calculating boiler efficiency using the indirect method.True
Oxygen content in flue gas is directly related to excess air levels, which significantly affect flue gas heat loss and combustion efficiency.
Accurate efficiency determination begins with capturing the most essential combustion and thermal performance parameters. Here is a breakdown of the parameters and their significance:
🔧 Key Parameters for Indirect Efficiency Calculation
Parameter | Description | Influence on Efficiency Calculation | Measurement Tool |
---|---|---|---|
Flue Gas Temperature (°C) | Temperature of gases exiting the boiler stack | Higher temps = higher heat loss | Thermocouple or IR sensors |
Ambient Air Temperature (°C) | Temperature of combustion air before entering the system | Reference for heat differential | Temperature sensor |
Flue Gas O₂ Content (%) | Indicates excess air used in combustion | Higher O₂ = higher dry flue gas loss | Flue gas analyzer |
CO₂ and CO in Flue Gas (%) | Reflects combustion quality and completeness | Helps validate air-fuel ratio and unburnt losses | Flue gas analyzer |
Fuel Composition | Includes %C, %H, %O, %S, %Moisture, %Ash | Determines potential heat output and latent losses | Lab analysis or fuel datasheet |
Moisture in Fuel (%) | Water content vaporized during combustion | Increases latent heat loss | Gravimetric or Karl Fischer |
Hydrogen in Fuel (%) | Forms water vapor upon combustion, creating latent heat losses | Directly contributes to H₂ loss | Fuel lab analysis |
Unburnt Carbon in Ash (%) | Carbon particles not burned during combustion | Indicates unburnt fuel loss | Ash testing |
Radiation and Convection Losses (%) | Heat lost from the boiler surface to the atmosphere | Fixed, but can be minimized via insulation | Empirical estimation (standards) |
Steam Temperature (°C) | Temperature of generated steam | Needed for direct method (heat output) | Pressure-temperature gauges |
Steam Pressure (bar) | Indicates enthalpy and energy content of steam | Direct method input | Steam pressure gauge |
Feedwater Temperature (°C) | Affects the amount of heat input needed to generate steam | Directly reduces energy requirement | Digital thermometer |
📊 Efficiency Sensitivity: How Variations in Parameters Impact Results
Parameter Varied | Efficiency Impact When Misestimated | Real-World Example |
---|---|---|
Flue Gas Temp +10°C | ↓ Efficiency by ~0.5–1.0% | Poor insulation in ducting |
O₂ Reading Error +2% | ↓ Efficiency by ~2–3% | Faulty gas analyzer calibration |
Moisture in Fuel +5% | ↓ Efficiency by ~1.5% | Wet biomass feed |
Hydrogen Error +1% | ↓ Efficiency by ~1.0% | Overlooked in lab report |
These variations show how even small inaccuracies in parameter collection can significantly distort the final efficiency value. This is why automated systems with data logging are often used in advanced facilities.
🛠️ Indirect vs. Direct Method Parameters
Parameter | Indirect Method | Direct Method |
---|---|---|
Flue gas O₂, CO₂, CO | ✅ | ❌ |
Fuel elemental composition | ✅ | ❌ |
Steam mass flow rate | ❌ | ✅ |
Enthalpy of steam | ❌ | ✅ |
Feedwater enthalpy | ❌ | ✅ |
Heat losses from surfaces | ✅ | ❌ |
Real Case: Cement Plant Combustion System Audit
Situation:
The plant reported only 68% efficiency using the direct method, while actual fuel costs were unusually high.
Action:
Using the Indirect Method and full parameter acquisition:
Measured Parameter | Observation |
---|---|
Flue Gas Temp | 245°C – too high |
O₂ in Flue Gas | 8.5% – excess air too high |
Moisture in Coal | 14% – high latent loss |
Carbon in Fly Ash | 3.2% – poor combustion |
Result:
Efficiency recalculated: 61%
Action Taken: Combustion air adjustment, fuel drying
Post-improvement Efficiency: 77%
Fuel Cost Savings: 16% annually
Tools Required for Accurate Measurement
Instrument | Purpose | Calibration Needed? |
---|---|---|
Flue Gas Analyzer | CO₂, O₂, CO, NOx readings | Yes (bi-annually) |
Thermocouples | Temperature measurements | Yes (annually) |
Gas Chromatograph | Fuel composition | Optional |
Moisture Analyzer | Fuel water content | Yes (monthly) |
Steam Flow Meter | Mass flow rate of steam | Yes (quarterly) |
Precision instruments must be maintained and calibrated regularly. Otherwise, even the best efficiency calculation model will fail due to poor data input.
In conclusion, accuracy in boiler or combustion system efficiency hinges on the quality, comprehensiveness, and correctness of input parameters. Whether you’re using the direct or indirect method, investing in proper instrumentation, routine calibration, and complete parameter logging is essential for actionable efficiency insights.
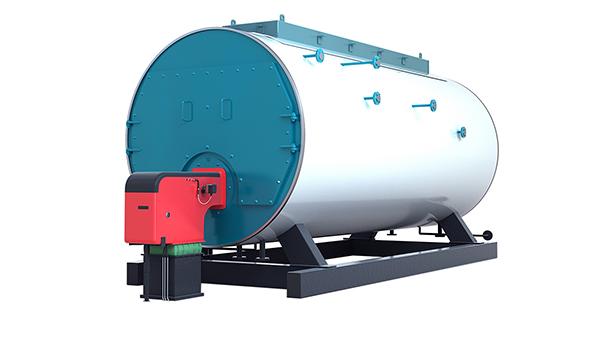
How Do Fuel Quality and Combustion Air Ratio Impact Measured Efficiency?
Industrial combustion systems, such as boilers and furnaces, are heavily influenced by two critical parameters: fuel quality and combustion air ratio. A slight deviation in either can create a domino effect—leading to unburnt fuel, excessive flue gas heat loss, soot formation, or even unsafe operations. These inefficiencies not only reduce your fuel-to-energy conversion rates but also inflate operational costs and carbon emissions. Yet many facilities overlook the significance of properly characterizing fuel properties or fail to optimize air input, assuming all fuels burn the same way. That misconception leads to hidden performance losses. By understanding and controlling these two factors, you can make a major impact on efficiency, sustainability, and bottom-line savings.
Fuel quality and combustion air ratio are two of the most significant variables affecting measured combustion efficiency. Low-quality fuel—due to high moisture, low calorific value, or high ash content—results in increased latent and unburnt fuel losses. Meanwhile, an incorrect air-to-fuel ratio (especially excess air) leads to higher dry flue gas losses due to the energy required to heat unused air, lowering the system’s thermal efficiency. Precise control and monitoring of both fuel characteristics and combustion air optimize combustion completeness and reduce measurable losses.
Whether you operate coal-fired boilers, biomass gasifiers, or gas turbines, the interplay between fuel quality and combustion air delivery directly determines how much useful heat you actually recover from the input fuel. Let’s explore the technical details and quantify their influence on efficiency in industrial systems.
Excess combustion air always improves boiler efficiency.False
Too much excess air increases flue gas losses by carrying heat out of the system, reducing overall boiler efficiency.
🔬 Fuel Quality: The Foundation of Combustion Performance
Fuel quality encompasses several factors that determine how efficiently and completely a fuel can combust. The most important ones include:
Fuel Property | Impact on Efficiency | Ideal Range |
---|---|---|
Moisture Content | Requires latent heat to vaporize, which escapes through flue gases | <10% for coal; <15% for biomass |
Ash Content | Increases unburnt carbon and slagging risk | <10% |
Volatile Matter | Affects ignition and flame stability | 15–30% |
Fixed Carbon | Represents usable energy potential | Higher is better |
Calorific Value | Determines total energy released per kg of fuel | >4500 kcal/kg (for coal) |
Size Distribution | Influences burnout time and airflow mixing | Uniform, 6–20 mm |
Real Example: Bituminous vs. Lignite Coal
Parameter | Bituminous Coal | Lignite Coal |
---|---|---|
Moisture (%) | 5–10 | 30–45 |
Calorific Value (kcal/kg) | 6000–7500 | 2500–3500 |
Ash Content (%) | 10–15 | 20–30 |
Typical Efficiency | ~82% | ~68–72% |
Higher moisture and ash in lignite lower combustion temperature and increase flue gas heat loss. The result is significantly lower efficiency even when combustion air is optimized.
🌬️ Combustion Air Ratio: The Balancing Act
Combustion air ratio is the ratio of actual air supplied to the stoichiometric air required for complete combustion. It’s typically expressed as excess air (%).
Excess Air (%) | O₂ in Flue Gas (%) | Efficiency Impact |
---|---|---|
<10% | <2% | Risk of incomplete combustion, CO, soot formation |
10–25% | 3–6% | Optimal range—stable flame, high efficiency |
>30% | >7% | Heat loss via excess dry flue gas, reduced efficiency |
The Impact of Too Much Air
Parameter | Effect |
---|---|
Flue Gas Volume ↑ | More heat carried away in exhaust |
Combustion Temperature ↓ | Less thermal intensity |
Fan Power Consumption ↑ | Higher electricity usage for air movement |
Boiler Efficiency ↓ | Typically 1–3% lower with every 10% excess air above optimum |
The graph below illustrates the relation between excess air and efficiency for a coal-fired boiler:
Efficiency peaks at around 15–20% excess air. Beyond this, additional air simply absorbs heat and carries it out of the stack, wasting energy.
🧪 Fuel Quality and Air Ratio: Interaction Effects
Scenario | Effect on Efficiency | Corrective Action |
---|---|---|
High-moisture biomass + low air ratio | Incomplete combustion, high CO, low flame temp | Increase drying or increase air slightly |
Low-ash coal + high excess air | Clean burn, but excessive dry flue gas loss | Reduce air to 15–20% excess |
Variable fuel size + fixed air flow | Inconsistent burn, fluctuating heat output | Use dynamic airflow control system |
Wet coal + insufficient combustion air | Unstable flame, unburnt carbon in ash | Pre-dry fuel and recalibrate air controls |
🔧 Measurement Tools and Instruments
Tool | Measurement | Why It Matters |
---|---|---|
Flue Gas Analyzer | O₂, CO₂, CO levels | Determine air ratio and combustion quality |
Moisture Analyzer | Fuel water content | Influences latent heat loss |
Bomb Calorimeter | Fuel calorific value | Establishes energy potential |
Thermographic Camera | Flame profile, heat zones | Visualize combustion uniformity |
Air Flow Meter | Mass or volume of air | Ensures proper air-fuel ratio |
📊 Efficiency Drop Based on Poor Fuel and Air Ratio
Fault Condition | Efficiency Drop (%) |
---|---|
Moisture in fuel from 10% → 25% | 4–6% |
Excess air from 20% → 40% | 3–4% |
Ash in fuel from 8% → 20% | 2–3% |
Uncontrolled combustion air | 5–8% |
Case Study: Biomass Boiler in European Paper Mill
Fuel Used: Wood chips (moisture = 35%)
Initial Efficiency: 68%
Problem: High flue gas temperature, low flame stability
Solution: Installed dryer for chips (reduced moisture to 15%), recalibrated VFD fans for 18% excess air
Resulting Efficiency: 82%
ROI: 10 months from fuel savings alone
To maximize combustion efficiency, you must start with fuel characterization and precise control of combustion air ratio. Poor-quality fuel and excessive or insufficient air can independently cause losses, but when both are mismanaged, the impact is compounded. Accurate measurement, consistent fuel supply, and intelligent control systems are key to achieving high thermal efficiency in real-world operations.
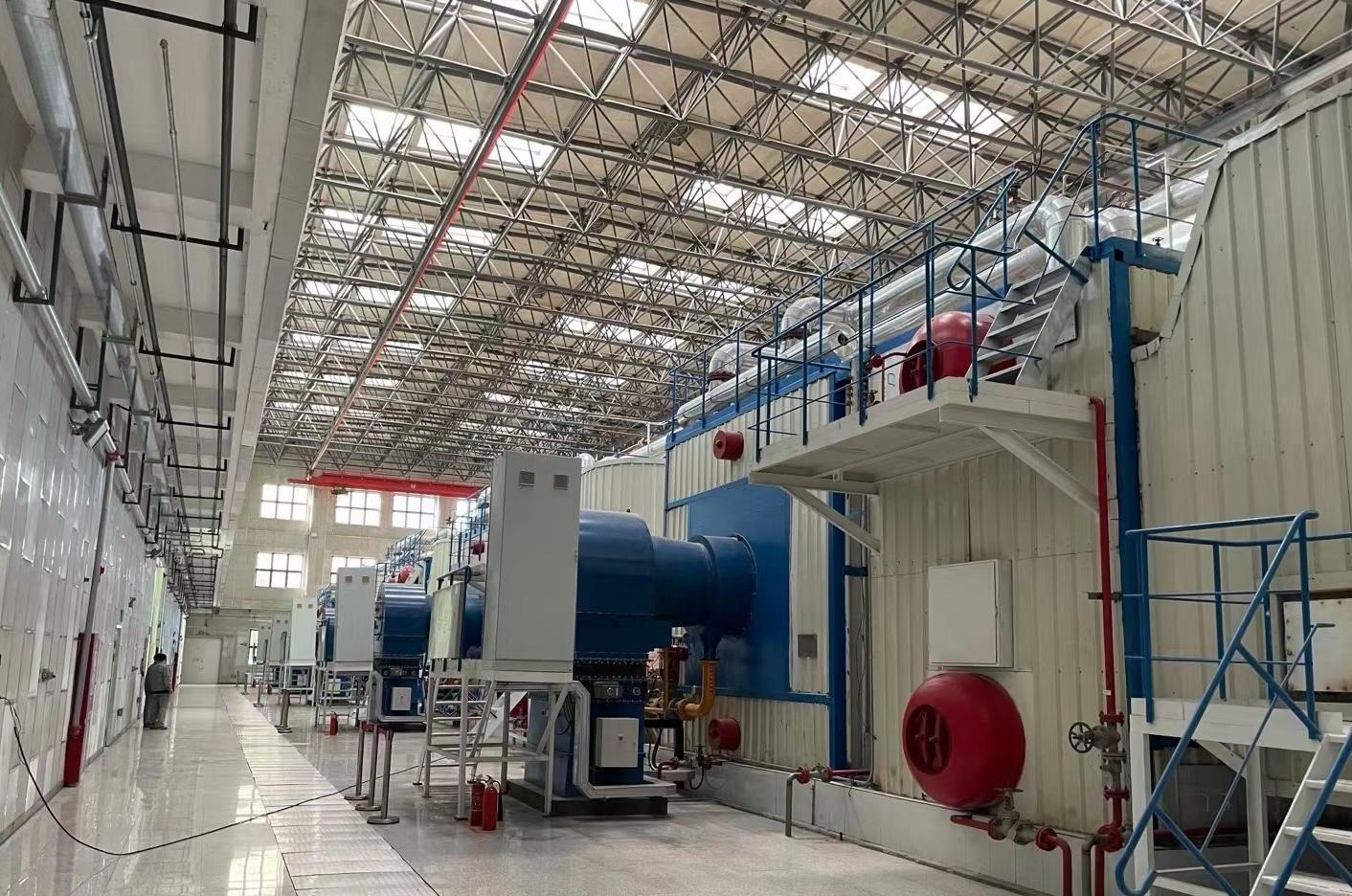
How Can Regular Efficiency Monitoring Improve Long-Term Performance and Savings?
In the realm of industrial thermal systems, operating under the illusion of high efficiency without ongoing validation is a dangerous—and expensive—assumption. Boilers, furnaces, and other combustion equipment inevitably suffer from drift in performance due to fouling, component wear, fuel variability, or control system misalignment. These seemingly small degradations accumulate unnoticed, silently draining resources and eroding profitability over months or years. However, regular efficiency monitoring transforms this reactive landscape into a proactive one—enabling timely detection of performance drops, guided maintenance, and sustained cost savings. Without continuous monitoring, even the most well-designed system can become inefficient and costly over time.
Regular efficiency monitoring improves long-term performance and savings by enabling early detection of performance deterioration, optimizing fuel use, identifying heat losses in real-time, and supporting data-driven maintenance strategies. By tracking key parameters such as flue gas composition, combustion air ratio, and fuel quality over time, facilities can prevent efficiency drift, reduce fuel costs by 5–15%, and extend equipment lifespan significantly.
Efficiency isn’t a fixed property of a boiler or furnace—it’s a dynamic measure that reflects the current health and operating condition of the system. That’s why a one-time measurement, no matter how accurate, isn’t enough. Sustained efficiency requires ongoing oversight using precise monitoring tools, data analysis, and corrective interventions based on real performance data.
Efficiency monitoring only needs to be performed annually for optimal performance.False
Annual monitoring may miss seasonal fuel variations, equipment degradation, or control drift. Continuous or monthly monitoring ensures early detection of issues.
📈 The Lifecycle Impact of Continuous Efficiency Monitoring
Efficiency tends to decline over time due to scaling, burner drift, fan degradation, or control calibration loss. The chart below illustrates this phenomenon:
Boiler Efficiency Degradation Over Time (Without Monitoring)
Time (Months) | Efficiency (%) – No Monitoring | Efficiency (%) – With Monitoring |
---|---|---|
0 | 85 | 85 |
6 | 82 | 84.5 |
12 | 79 | 84 |
18 | 76 | 83.5 |
24 | 74 | 83 |
With no monitoring, the efficiency drops by 11 percentage points in two years, equating to a fuel loss of over 13%. Regular monitoring helps catch small inefficiencies early—before they become chronic.
🛠️ Key Monitoring Parameters and Their Role
Parameter | Monitoring Frequency | Purpose | Tool |
---|---|---|---|
Flue Gas O₂ and CO₂ | Weekly/Daily | Identifies excess air and combustion quality | Flue Gas Analyzer |
Flue Gas Temperature | Continuous | Detects fouling or poor heat transfer | IR or thermocouple sensors |
Steam Output per kg of Fuel | Monthly | Indicates real-world thermal conversion performance | SCADA-logged mass flow |
Fuel Moisture and CV | Weekly | Reflects energy potential and variability | Moisture analyzer, calorimeter |
Unburnt Carbon in Ash | Monthly | Reveals combustion completeness | Manual sampling |
Radiation Surface Temperature | Quarterly | Highlights insulation or jacket heat losses | Thermographic camera |
When these parameters are monitored over time, deviations are easy to detect. Maintenance teams can correlate changes to operational events, enabling root cause analysis instead of guesswork.
💡 Efficiency Monitoring as a Strategic Tool
1. Preventative Maintenance Scheduling
By observing trends in oxygen levels and flue gas temperature, facilities can predict when cleaning or burner adjustment is necessary. This prevents unplanned shutdowns and maintains optimal heat transfer.
2. Real-Time Alerts for Critical Failures
Modern DCS/SCADA systems can trigger alarms when combustion becomes unstable, flue temperatures spike, or CO levels exceed safe thresholds. This minimizes the risk of catastrophic failure or prolonged inefficiency.
3. Fuel Procurement Optimization
Long-term data enables better fuel selection. For instance, if two coal lots differ in efficiency impact by 5%, procurement can favor the more efficient batch, even at higher upfront cost—leading to net savings.
4. Emissions Reduction
Continuous monitoring aligns combustion with environmental targets by reducing CO, NOx, and unburnt hydrocarbons. Efficiency and compliance go hand-in-hand.
Benefit | Measurable Impact |
---|---|
Fuel Savings | 5–15% per year |
CO₂ Emission Reduction | 50–120 kg CO₂/ton of fuel |
Maintenance Cost Reduction | 10–25% via predictive actions |
Downtime Reduction | 20–30% by catching early issues |
Equipment Life Extension | 2–4 years longer average boiler life |
🧪 Case Study: Petrochemical Plant – Saudi Arabia
System: Natural gas-fired steam boiler, 45 TPH
Issue: Fuel cost per ton of steam rising despite “stable” operations
Action: Installed real-time flue gas analyzers and digital monitoring system
Findings: Flue gas O₂ was averaging 8.2% (excess air >40%)
Intervention: Re-calibrated burners and optimized fan damper controls
Result:
Efficiency improved from 80.3% to 87.1%
Monthly gas savings: 14,800 m³
Payback period for monitoring equipment: <6 months
🔄 Integration with Automation and AI Systems
Smart factories are moving toward predictive combustion analytics. By leveraging AI algorithms trained on historical performance data, companies are now:
Forecasting efficiency decline trends
Receiving AI-suggested parameter setpoints
Auto-tuning air-fuel ratios dynamically
Benchmarking across multiple units in real-time
This goes beyond monitoring—into the realm of self-optimizing combustion systems.
📊 Efficiency Tracking Dashboard Example
Date | O₂ (%) | Flue Temp (°C) | Efficiency (%) | Action Triggered |
---|---|---|---|---|
01-Jan | 3.5 | 185 | 86.2 | None |
15-Jan | 5.5 | 215 | 82.4 | Excess air alert |
01-Feb | 4.2 | 195 | 84.7 | Burner tune-up |
01-Mar | 3.8 | 188 | 85.8 | Stable |
Such dashboards facilitate management-level energy reporting and audit-readiness, critical for ISO 50001 compliance.
In conclusion, regular efficiency monitoring is not just a good practice—it is a strategic imperative for any operation relying on combustion or thermal processes. By continuously tracking key performance indicators and acting on real-time insights, facilities can prevent performance degradation, ensure consistent output, reduce costs, and stay competitive in a fuel-sensitive economy.
🔍 Conclusion
Knowing how to measure the thermal efficiency of your industrial oil-fired boiler is key to maximizing energy usage, reducing operational costs, and extending equipment life. Whether using the Direct or Indirect Method, accurate tracking of fuel input, steam output, and combustion losses enables informed decision-making and targeted performance improvements. A consistent measurement program ensures your boiler remains efficient, compliant, and cost-effective.
📞 Contact Us
💡 Need help assessing your oil-fired boiler’s efficiency? Our technical team provides onsite diagnostics, combustion tuning, and performance optimization services to help you reduce fuel costs and improve system reliability.
🔹 Reach out today and start unlocking greater efficiency from your oil-fired boiler system! 🛢🔥📊
FAQ
What is thermal efficiency in an industrial oil-fired boiler?
Thermal efficiency represents the ratio of useful heat output (in the form of steam or hot water) to the total energy input from fuel combustion. Higher efficiency means more fuel is converted to useful energy, reducing waste and operational cost.
What are the methods to measure thermal efficiency in oil-fired boilers?
Two standard methods are used:
Direct Method (Input-Output Method)
Indirect Method (Heat Loss Method)
Both are recognized by global standards like ASME and ISO for industrial boiler energy auditing.
How is the Direct Method applied in oil-fired boilers?
The Direct Method calculates efficiency using:
Efficiency (%) = (Steam Output × Enthalpy Gain) / (Fuel Input × Calorific Value) × 100
This method is quick and practical but does not show where losses occur within the system.
What does the Indirect Method reveal?
The Indirect Method determines boiler efficiency by calculating individual heat losses—such as flue gas loss, unburned fuel, radiation, and blowdown—and subtracting the total from 100%.
Efficiency (%) = 100 – (Sum of All Measured Losses)
This offers more diagnostic value for optimizing combustion and reducing fuel consumption.
Why is it important to monitor oil-fired boiler efficiency?
Monitoring thermal efficiency ensures fuel is used effectively, helps lower greenhouse gas emissions, reduces maintenance costs, and meets regulatory standards. It also supports decision-making for upgrades and retrofits to enhance performance.
References
Boiler Efficiency Calculation Methods – https://www.energy.gov
ASME Boiler Efficiency Standards – https://www.asme.org
Direct vs. Indirect Efficiency Measurement – https://www.sciencedirect.com
Fuel Oil Combustion and Boiler Performance – https://www.researchgate.net
Heat Losses in Industrial Boilers – https://www.epa.gov
Energy Audits for Oil-Fired Boilers – https://www.bioenergyconsult.com
Thermal Performance of Oil-Fired Systems – https://www.mdpi.com
Industrial Boiler Optimization Techniques – https://www.iea.org
Reducing Fuel Costs in Oil Boilers – https://www.energysavingtrust.org.uk
Boiler Monitoring and Control Systems – https://www.automation.com
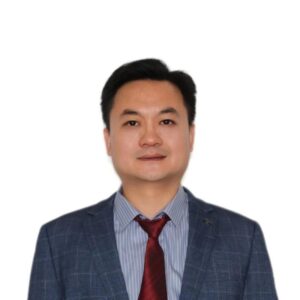