Environmental and Emission Regulations Impacting Industrial Biomass Boiler Selection
Industrial biomass boilers are widely promoted as a sustainable and renewable energy solution, but that doesn’t exempt them from strict environmental and emission regulations. While biomass combustion generally produces lower net carbon emissions than fossil fuels, it can still generate pollutants like particulate matter (PM), nitrogen oxides (NOx), sulfur oxides (SOx), and volatile organic compounds (VOCs). Failure to comply with regulatory standards may result in penalties, project delays, or forced system modifications, making environmental compliance a critical factor in biomass boiler selection.
Environmental and emission regulations impact industrial biomass boiler selection by imposing strict limits on air pollutants, fuel handling practices, ash disposal, and greenhouse gas reporting. These regulations influence decisions related to combustion technology (e.g., grate vs. fluidized bed), emission control systems (such as electrostatic precipitators and bag filters), boiler size, and even allowable fuel types. Selecting a biomass boiler that meets local and international standards—such as EPA, EU Industrial Emissions Directive (IED), or country-specific clean air laws—is essential for legal compliance and long-term operational viability.
Understanding the regulatory landscape is crucial to choosing a biomass boiler that balances performance, sustainability, and compliance.

What Pollutants Are Regulated in Biomass Combustion and How Do They Affect Boiler Selection?
Biomass combustion has become a favored alternative to fossil fuels due to its renewable nature and lower net carbon footprint. However, this environmental benefit can be undermined if the combustion process emits significant levels of regulated air pollutants such as particulate matter, nitrogen oxides, carbon monoxide, sulfur compounds, or volatile organic compounds. These emissions are not only harmful to human health and the environment but are also subject to strict regulatory limits that vary by country and region. Failure to comply can lead to fines, shutdowns, or revoked operating permits. Therefore, understanding the types of pollutants produced in biomass combustion—and their implications for boiler selection—is essential for designing compliant, efficient, and sustainable energy systems.
The primary regulated pollutants in biomass combustion include particulate matter (PM), nitrogen oxides (NOₓ), sulfur oxides (SOₓ), carbon monoxide (CO), volatile organic compounds (VOCs), and heavy metals such as mercury and cadmium. These emissions are regulated under national and international air quality standards such as the EU Industrial Emissions Directive, US EPA regulations, and local environmental authority limits. The presence and concentration of these pollutants significantly influence boiler selection, requiring decisions on combustion type, fuel preparation, emission control technologies, and automation systems to ensure compliance and operational efficiency.
Choosing the right biomass boiler isn’t just about fuel type and capacity—it’s also about whether the boiler can burn cleanly and be integrated with the appropriate emission control technologies to meet legal and environmental standards. Whether you’re selecting a moving grate boiler, bubbling fluidized bed (BFB), or circulating fluidized bed (CFB), the pollutant profile and compliance requirements must be front and center in the decision-making process.
Biomass combustion is always clean and free of harmful emissions.False
While biomass is renewable, its combustion can emit regulated pollutants like PM, NOₓ, and CO if not properly managed.
🧪 Key Pollutants Generated by Biomass Combustion
Pollutant | Source in Biomass Combustion | Health/Environmental Impact | Typical Regulation Limit (mg/Nm³) |
---|---|---|---|
Particulate Matter (PM10/PM2.5) | Incomplete combustion, ash carryover | Respiratory diseases, environmental deposition | 20–50 (EU), 30–100 (US EPA) |
NOₓ (NO + NO₂) | High-temperature combustion, nitrogen in fuel/air | Smog, acid rain, lung damage | 150–200 |
CO (Carbon Monoxide) | Incomplete combustion due to poor oxygen mixing | Toxic gas, indoor safety hazard | 100–200 |
SO₂ (Sulfur Dioxide) | Sulfur compounds in biomass (mainly bark, peat) | Respiratory irritation, acidification | 50–200 |
VOCs | Unburnt hydrocarbons from resinous biomass | Ozone formation, carcinogenic | 20–100 |
Heavy Metals (Hg, Cd, Pb) | Contaminated biomass or paints in wood waste | Neurotoxicity, environmental accumulation | Mercury < 0.05, Cadmium < 0.1 |
Dioxins/Furans | Chlorinated organics in fuel (treated wood) | Carcinogenic, endocrine disruptors | <0.1 ng/Nm³ |
These pollutant levels vary significantly based on biomass type, moisture content, combustion temperature, and airflow control.
🔍 Influence of Pollutants on Boiler Technology Selection
Boiler Type | Emission Characteristics | Pollution Control Needs | Best Used For |
---|---|---|---|
Moving Grate Boiler | Higher PM and CO, moderate NOₓ | Needs ESPs or bag filters, CO monitor | Wood chips, bark, agriculture waste |
Bubbling Fluidized Bed (BFB) | Better mixing, lower CO and PM | Needs NOₓ control, optional SO₂ scrubbers | Mixed biomass, RDF |
Circulating Fluidized Bed (CFB) | Uniform combustion, lowest NOₓ and CO emissions | Integrated multi-pollutant control | Industrial-scale operations |
Pellet Boiler | Cleanest burn if high-grade fuel used | Minimal controls if operated properly | Small-medium commercial buildings |
Fixed Bed Gasifier | Can emit high tar/VOCs without gas cleanup | Requires syngas filters and thermal oxidizers | CHP systems using syngas |
Boiler selection must match the fuel characteristics and targeted emission limits. For example, burning straw (high in chlorine and potassium) will require more aggressive corrosion and emission control strategies than clean wood pellets.
📊 Pollutant Emission Comparison by Fuel Type
Biomass Type | PM (mg/Nm³) | NOₓ (mg/Nm³) | CO (mg/Nm³) | SO₂ (mg/Nm³) |
---|---|---|---|---|
Wood Chips | 30–80 | 100–150 | 50–200 | <20 |
Bark | 40–120 | 120–180 | 100–300 | 30–80 |
Straw | 50–200 | 150–250 | 100–400 | 100–250 |
Pellet (Class A1) | <30 | <100 | <50 | <10 |
RDF/Wood Waste | 150–300 | 200–300 | 250–500 | 150–500 |
The cleaner the fuel, the simpler and cheaper the emission control. For contaminated or heterogeneous fuels, the boiler must include advanced systems like staged combustion, SCR (selective catalytic reduction), or dry/wet scrubbers.
🔧 Emission Control Technologies Matched to Pollutants
Pollutant | Control Technology | Boiler Integration Strategy |
---|---|---|
PM | ESP (Electrostatic Precipitator), Bag Filter | Downstream flue gas cleaning |
NOₓ | Flue Gas Recirculation, SNCR, SCR | Burner design, staged combustion |
SO₂ | Dry sorbent injection, Wet scrubbers | Fuel pre-treatment, lime/limestone injection |
CO | Oxygen trim control, staged air zones | Real-time monitoring and air modulation |
VOCs/Dioxins | Afterburners, Activated carbon injection | Avoid fuel contamination, thermal oxidation zones |
Heavy Metals | Activated carbon filter, filter ash handling | Biomass fuel quality inspection and sorting |
The cost of these technologies and their operational complexity should be factored into total project cost and long-term O&M plans.
🏛️ Regulatory Frameworks That Govern Biomass Emissions
Region | Standard/Directive | Key Pollutants Regulated |
---|---|---|
European Union | Industrial Emissions Directive (IED) | PM, NOₓ, SO₂, CO, VOCs, Hg, dioxins |
United States | EPA 40 CFR Part 60 Subpart Db/Dc | PM, SO₂, NOₓ, CO, Hg |
China | GB13271-2014 | PM, NOₓ, SO₂ |
India | CPCB Emission Norms for Biomass Boilers | PM, NOₓ, CO, SO₂ |
Canada | CCME Guidelines and Provincial Regulations | Varies by province |
Non-compliance can lead to penalties, emissions-based taxes, or operational shutdowns. Thus, pre-approval planning with regulators and detailed emissions modeling is critical before selecting boiler equipment.
🧪 Case Study: European Biomass CHP Facility
Fuel: Mixed wood waste and bark
Initial Problem: PM emissions exceeded EU IED limits (65 mg/Nm³)
Boiler Used: Moving Grate 20 MW
Action Taken: Upgraded ESP with a multistage filtration system and added FGR
Result:
PM reduced to 28 mg/Nm³
NOₓ reduced from 180 to 130 mg/Nm³
Compliance achieved under new operating permit
Avoided €1.2 million in potential penalties over 3 years
In conclusion, understanding the emission profile of biomass combustion is essential to ensure boiler selection aligns with environmental regulations. The type of biomass fuel, combustion technique, and required pollutant control technologies all contribute to a safe, legal, and efficient energy solution. Selecting the right boiler means selecting one that not only meets your thermal demands but also complies with pollution control mandates—today and for the lifetime of the plant.
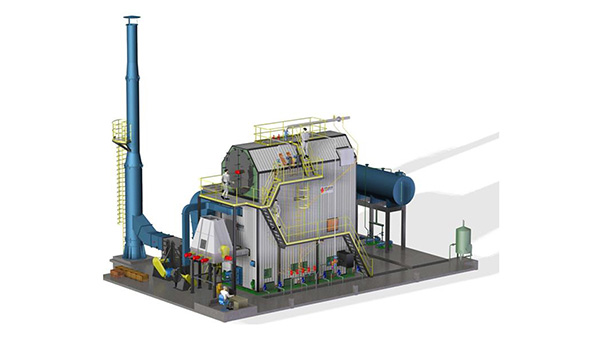
Which International and Regional Emission Standards Apply to Industrial Biomass Boilers?
Biomass combustion may be a renewable energy solution, but it’s far from exempt from environmental scrutiny. As industries shift from fossil fuels to biomass, regulators across the globe are tightening emissions thresholds to ensure that the climate benefits of biomass aren’t offset by harmful air pollution. Industrial biomass boilers, especially those used in power generation and manufacturing, must adhere to stringent emission standards—both international frameworks and local laws. These govern the allowable limits for pollutants like particulate matter, nitrogen oxides (NOₓ), sulfur oxides (SO₂), carbon monoxide (CO), heavy metals, and even dioxins. Understanding which regulations apply is essential for selecting the right combustion technology, emission control systems, and for maintaining operational permits and environmental compliance.
Industrial biomass boilers must comply with a combination of international, national, and regional emission standards, including the European Union’s Industrial Emissions Directive (IED), the United States EPA New Source Performance Standards (NSPS), China’s GB13271-2014 standard, India’s CPCB norms, and local authority guidelines. These regulations define allowable limits for key pollutants such as PM, NOₓ, SO₂, CO, VOCs, and heavy metals. Compliance determines not only boiler design and emission control systems but also affects permitting, operational practices, and environmental reporting.
Failing to align with these standards can lead to steep fines, permit revocations, production delays, or even long-term reputational damage. Whether you’re designing a new biomass boiler installation or upgrading an existing plant, a solid grasp of applicable regulations is not optional—it’s fundamental.
There is a single global emission standard for industrial biomass boilers.False
Emission standards vary by country and region. While global frameworks like IPCC and ISO offer guidelines, enforcement is based on local laws such as the EU IED, US EPA standards, or China's GB13271.
🌍 Overview of Global Emission Standards for Biomass Boilers
Region/Country | Key Standard/Directive | Enforcing Body | Pollutants Regulated |
---|---|---|---|
European Union | Industrial Emissions Directive (IED) 2010/75/EU | European Commission/Local Authorities | PM, NOₓ, SO₂, CO, VOCs, heavy metals, dioxins |
United States | EPA NSPS Subparts Db, Dc (40 CFR Part 60) | Environmental Protection Agency | PM, NOₓ, SO₂, CO, Hg |
China | GB13271-2014 | Ministry of Ecology and Environment | PM, NOₓ, SO₂ |
India | CPCB Emission Norms for Boilers (2018) | Central Pollution Control Board | PM, NOₓ, CO, SO₂ |
Canada | Provincial Standards + CCME Guidelines | Provincial Ministries of Environment | Varies by province |
Australia | NEPM Air Toxics and Local EPA Regulations | State EPAs | PM, NOₓ, CO, VOCs |
South Africa | National Environmental Management: Air Quality Act | Department of Environment | PM, NOₓ, SO₂, CO |
📏 Typical Emission Limits for Biomass Boilers
Pollutant | EU IED (mg/Nm³) | US EPA (mg/Nm³) | China GB13271 (mg/Nm³) | India CPCB (mg/Nm³) |
---|---|---|---|---|
PM | 10–30 | 30–50 | 30–80 | 50 |
NOₓ | 150–200 | 200 | 150–300 | 400 |
SO₂ | 50–150 | 150 | 200–400 | 600 |
CO | 100–150 | 180 | 200–300 | 150 |
Hg (Mercury) | 0.05 | 0.02 | <0.05 | – |
Dioxins/Furans | 0.1 ng/Nm³ | – | 0.1 ng/Nm³ | – |
Limits vary depending on plant size, fuel type, and output capacity (e.g., <50 MWth vs. >100 MWth). Advanced technologies like fluidized bed combustion and staged combustion with real-time air modulation are often necessary to meet these standards.
🧰 Regulatory Impact on Boiler Design and Selection
Regulation Requirement | Design Implication | Compliance Strategy |
---|---|---|
PM < 30 mg/Nm³ | Requires advanced filtration (ESP, bag filters) | Include multi-stage PM capture system |
NOₓ < 200 mg/Nm³ | Needs low-NOₓ burner or staged combustion | Integrate SNCR/SCR or FGR |
SO₂ < 150 mg/Nm³ | Depends on sulfur content in fuel | Use limestone injection or scrubber |
CO < 150 mg/Nm³ | Requires precise air-fuel ratio control | Oxygen trim system, real-time monitoring |
Continuous emissions monitoring (CEMS) | System for real-time compliance tracking | Install CEMS unit with DCS/SCADA |
These requirements influence the choice of boiler (grate, fluidized bed, gasifier), fuel preparation systems, and emission controls—all of which must be planned at the design stage.
📊 Real-World Compliance Strategy Comparison
Boiler Type | Base Emissions (PM/NOₓ/CO mg/Nm³) | Upgraded Controls | Final Emissions Achieved |
---|---|---|---|
Grate-Fired, Wood | 100 / 300 / 200 | ESP + FGR + O₂ Trim | 20 / 180 / 90 |
BFB, Mixed Biomass | 60 / 220 / 150 | SNCR + Bag Filter | 25 / 130 / 80 |
Pellet Boiler, CHP | 30 / 100 / 50 | Minimal upgrades | 20 / 90 / 40 |
These adjustments ensured full compliance with EU IED limits and improved combustion efficiency by ~5% across systems.
🏛️ Certification, Audits, and Reporting Requirements
Requirement | Who Requires It | Key Components |
---|---|---|
Emission Permit | Local environmental authority | Pre-installation modeling + limits |
Continuous Emission Monitoring (CEMS) | EU, US, China (certain cases) | Real-time measurement, calibration logs |
Annual Compliance Reporting | All major jurisdictions | Includes fuel data, emissions, downtime |
Third-Party Stack Testing | Random or annual audits | Confirms self-reported emissions |
ISO 14001/50001 Alignment | Optional but recommended | Systematic environmental management |
Many facilities also align with voluntary frameworks like the World Bank’s Environmental Health and Safety (EHS) Guidelines or the IFC Performance Standards for ESG alignment in financing.
🧪 Case Study: China-Based Biomass Power Plant
Location: Shandong Province
Boiler Type: 35 TPH BFB boiler using rice husk
Regulation: GB13271-2014
Initial Challenge: PM and NOₓ exceeded local limits
Action Taken: Installed bag filters, urea-based SNCR, and real-time CEMS
Result:
PM reduced from 95 to 28 mg/Nm³
NOₓ cut from 320 to 170 mg/Nm³
Received Green Enterprise Certification
Qualified for carbon credit trading under ETS
🔍 What to Consider When Planning Compliance
Understand regional baseline and future tightening trends. E.g., India may soon adopt tighter SO₂ limits.
Model emissions at design stage using simulation tools like FLUENT or proprietary OEM software.
Ensure fuel quality consistency (chlorine, sulfur, moisture) to avoid uncontrolled emissions.
Plan for CEMS integration from the start, especially in EU, China, or large US facilities.
Factor in O&M costs for SNCR/SCR reagents, filter bags, and calibration.
In conclusion, industrial biomass boilers are subject to a diverse and evolving set of international and regional emission standards. These regulations shape not only the design and technology selection but also the daily operation, maintenance, and reporting requirements of biomass combustion systems. Navigating this regulatory matrix requires a proactive, well-informed strategy that combines engineering excellence with environmental compliance.
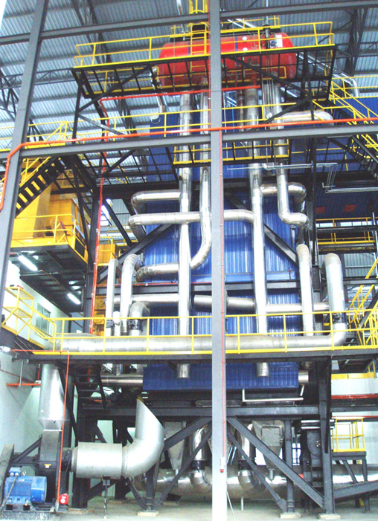
How Do Particulate and NOₓ Limits Influence Combustion Technology and Filter Selection?
Stricter air quality regulations worldwide are pushing industrial biomass combustion systems to drastically reduce two of the most problematic pollutants: particulate matter (PM) and nitrogen oxides (NOₓ). Both are tightly controlled due to their direct impact on human health, environmental degradation, and urban air quality indices. But while many manufacturers focus on fuel or boiler sizing, it is these emission limits that most decisively shape the combustion technology, filter design, and control systems. Without the right technology pairing, even the most efficient boiler can be deemed non-compliant, risking fines, shutdowns, or loss of operating permits. Therefore, the interdependence between emission thresholds and system architecture must be considered from the earliest design phase.
Particulate and NOₓ emission limits directly influence the choice of combustion technology and emission control systems in biomass boilers. Low NOₓ limits require staged combustion designs or post-combustion controls such as selective non-catalytic reduction (SNCR) or selective catalytic reduction (SCR). Similarly, strict particulate matter standards necessitate advanced filtration systems like electrostatic precipitators (ESPs) or fabric bag filters. Together, these requirements determine boiler type (grate, BFB, CFB), fuel preparation needs, and the selection and sizing of emission control equipment to ensure legal compliance and efficient performance.
In modern boiler projects, emissions compliance is no longer an optional afterthought—it’s a design constraint that dictates everything from airflow geometry to ash handling systems. Understanding this influence is vital to making the right technology decisions upfront and avoiding costly retrofits later.
All combustion technologies automatically meet modern PM and NOₓ limits without additional filtration or control.False
Most combustion systems, especially grate-type and older designs, require advanced emission control devices to meet current particulate and NOₓ standards.
🔍 Regulatory Pressure: Typical Emission Thresholds
Pollutant | Common Regulatory Limit (mg/Nm³) | Regions Applying Limit |
---|---|---|
PM | 10–30 | EU, China, India, US EPA |
NOₓ | 150–200 | EU, US, China, India |
These tight standards are especially challenging for biomass combustion, where fuel variability, ash content, and combustion temperature fluctuations make stable emissions control more complex than in gas-fired systems.
🔥 NOₓ Emission Limits: Influence on Combustion Technology
NOₓ is formed at high temperatures from the oxidation of atmospheric nitrogen and nitrogen in the fuel. High flame temperatures, excess air, and uneven fuel mixing all increase NOₓ formation.
🔧 Combustion Design Strategies for NOₓ Reduction
Strategy | Description | NOₓ Reduction Efficiency | Applied In |
---|---|---|---|
Staged Combustion | Fuel and air introduced in stages to lower peak temperatures | 30–50% | Grate boilers, BFB, CFB |
Flue Gas Recirculation (FGR) | Recirculates cooled exhaust to combustion zone | 20–40% | Medium-scale pellet systems |
Low-NOₓ Burners | Optimize fuel/air mix and reduce hot spots | 40–60% | Larger industrial units |
Selective Non-Catalytic Reduction (SNCR) | Inject urea/ammonia into flue gas at 850–1050°C | 40–70% | Retrofit-friendly option |
Selective Catalytic Reduction (SCR) | Ammonia injection over catalyst at 300–400°C | 80–95% | High-capex, low-NOₓ designs |
Choosing between SNCR and SCR depends on the boiler’s flue gas temperature profile, size, and budget. For example:
SNCR is cost-effective for mid-size systems but limited by narrow temperature windows.
SCR is highly efficient but requires large space and higher capex, making it ideal for high-capacity plants.
🧱 Particulate Limits: Filter and Boiler Design Implications
Biomass fuels contain ash and unburnt char, which form fine particulates during combustion. These are harmful when inhaled and visible as smoke or haze. Meeting PM limits requires multi-stage filtration and fine ash management.
🧰 Filtration Technologies for PM Control
Technology | Efficiency | Particle Size Captured | Suitable for |
---|---|---|---|
Cyclones | 60–85% | >10 µm | Pre-cleaning, low-cost |
Multicyclones | 80–90% | >5 µm | Grate boilers |
Electrostatic Precipitators (ESP) | 95–99.9% | 0.1–10 µm | Large-scale systems |
Fabric Baghouse Filters | 99–99.9% | 0.01–5 µm | Strict PM requirements |
Wet Scrubbers | 90–99% | Wide range, acidic gases | High-moisture fuels |
Filter Selection Based on PM Standard
PM Standard (mg/Nm³) | Recommended Control System | Common Application |
---|---|---|
>50 | Multicyclone + ESP (optional) | Older local standards |
30–50 | ESP or Bag Filter (basic) | Indian/Central EU boiler systems |
<30 | Bag Filter or High-Efficiency ESP | EU IED or US NSPS compliance |
<10 | Hybrid ESP + Bag Filter | Ultra-low emission urban areas |
Proper sizing and ash disposal system integration are critical for long-term filter efficiency and maintenance.
🔧 Boiler Type vs. Emissions Flexibility
Boiler Type | PM Emission (Raw) | NOₓ Emission (Raw) | Emission Control Needs |
---|---|---|---|
Fixed/Moving Grate | High (80–150) | Moderate (150–250) | Cyclone + Bag Filter + SNCR |
Bubbling Fluidized Bed | Medium (40–80) | Lower (130–200) | Bag Filter + SNCR |
Circulating Fluidized Bed | Low (30–60) | Low (90–160) | ESP or SCR |
Pellet Condensing Boiler | Low (<30) | Low (<120) | Compact filters or cyclones |
Fluidized bed boilers (BFB, CFB) offer better in-situ control of emissions due to their fuel mixing and combustion uniformity, reducing the load on external control systems.
📊 Real-World Impact of Emissions Compliance on Capex
Configuration | Base Capex (€) | Emission Controls Capex (%) | Notes |
---|---|---|---|
Grate Boiler + Cyclone | 1.5 million | +10–15% | Moderate PM compliance |
Grate + Bag Filter + SNCR | 1.5 million | +30–40% | Meets NOₓ and PM for EU level |
BFB + ESP + SCR | 3.2 million | +50–60% | High-end solution for large-scale CHP |
Pellet Boiler + Cyclone | 0.8 million | +5–10% | Residential/low-regulatory markets |
Although the capital cost increases with stricter emissions, long-term savings arise from:
Reduced fuel losses (better combustion)
Emission-related tax avoidance
Permit and insurance advantages
Lower maintenance downtime
🧪 Case Study: 25 MW Biomass Power Plant in Spain
Original Plan: Grate boiler with cyclone only
Challenge: Required PM < 20 mg/Nm³ and NOₓ < 150 mg/Nm³ (EU IED)
Adaptation: Upgraded to BFB boiler with Bag Filter and SNCR
Results:
PM = 14 mg/Nm³
NOₓ = 128 mg/Nm³
Annual compliance cost: €75,000
Avoided fine risk: €420,000/year
Payback: 1.8 years
In conclusion, PM and NOₓ emission limits are not peripheral concerns—they are central design drivers in biomass combustion projects. These regulatory thresholds dictate combustion temperature control, air staging, filtration systems, and post-combustion emission technologies. To ensure long-term compliance, operational safety, and environmental responsibility, industrial boiler designers and operators must treat emissions management as a core component of system architecture, not as an afterthought.
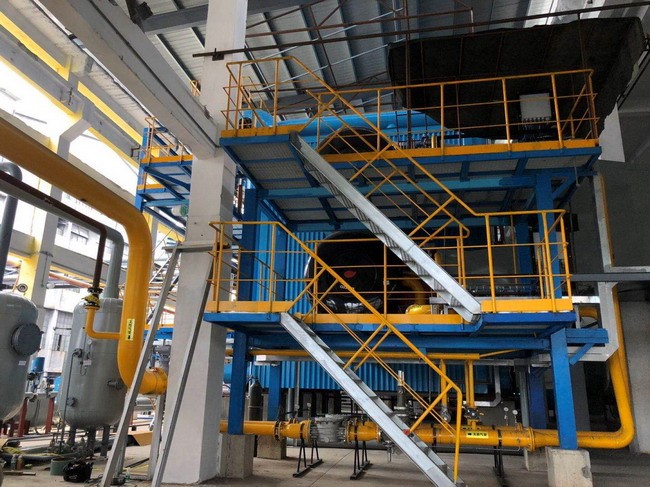
What Role Does Fuel Type (Wood Chips, Pellets, Agri-Residue) Play in Emissions Compliance?
The performance of a biomass boiler isn’t determined solely by its engineering or combustion technology—the type of fuel used plays a decisive role in its emissions profile. Many biomass projects begin with ambitious emissions targets, only to face non-compliance due to poor fuel selection or lack of understanding of how fuel composition impacts pollutant formation. Whether you burn wood chips, wood pellets, or agricultural residues, each fuel type introduces different levels of ash, moisture, chlorine, nitrogen, sulfur, and volatiles that directly influence the formation of particulate matter (PM), NOₓ, SO₂, CO, and even dioxins or heavy metals. Emissions compliance, therefore, starts not at the stack—but at the fuel storage yard.
Fuel type has a fundamental impact on emissions compliance because each biomass category—wood chips, pellets, and agricultural residues—differs in composition, moisture, ash content, and contaminants. These differences influence combustion characteristics, particulate generation, and formation of regulated pollutants like NOₓ, SO₂, and dioxins. Choosing the appropriate fuel type based on regulatory limits is essential for selecting suitable boiler technologies and designing effective emissions control systems that achieve legal compliance and environmental performance goals.
Many emission control challenges arise not from combustion failure but from the wrong fuel-furnace pairing. Understanding these fuel-specific emissions behaviors helps facility managers, boiler designers, and environmental officers make smarter, more compliant decisions from the start.
All biomass fuels, regardless of type, emit similar levels of pollutants during combustion.False
Different biomass fuels vary significantly in ash, nitrogen, sulfur, chlorine, and moisture content, which directly affect emissions such as PM, NOₓ, SO₂, and dioxins.
🌿 Fuel Type Characteristics and Emission Tendencies
Fuel Type | Ash (%) | Moisture (%) | Nitrogen (%) | Sulfur (%) | Chlorine (%) | PM Risk | NOₓ Risk | SO₂ Risk | Dioxin Risk |
---|---|---|---|---|---|---|---|---|---|
Wood Pellets | 0.2–1 | 6–10 | <0.2 | <0.05 | <0.01 | Low | Low | Very Low | Very Low |
Wood Chips | 1–3 | 20–50 | 0.2–0.4 | 0.05–0.1 | 0.02–0.05 | Medium | Medium | Low | Low |
Agri-Residue (e.g., rice husk, straw) | 10–25 | 10–20 | 0.4–1.2 | 0.1–0.3 | 0.05–0.3 | High | High | Medium–High | High |
Bark/Wood Waste | 3–8 | 30–60 | 0.5–1.0 | 0.1–0.3 | 0.1–0.2 | High | High | Medium | High |
These differences create a vastly different emissions control burden depending on the fuel source and preparation quality.
🔥 How Fuel Type Affects Pollutant Formation
1. Particulate Matter (PM)
Agri-residue contains high silica and potassium → forms fine, sticky ash → high PM
Wood chips generate moderate PM, especially with bark
Pellets, being densified and low in ash, have minimal PM emissions
2. Nitrogen Oxides (NOₓ)
Higher nitrogen in fuel → more fuel-bound NOₓ
Straw and husks typically have 3–5× nitrogen content of wood pellets
NOₓ emissions are higher in fluidized bed combustion of agri-residue unless SNCR/SCR is applied
3. Sulfur Oxides (SO₂)
Most wood-based fuels have negligible sulfur
Some agri-wastes and bark contain up to 0.3% sulfur
SO₂ may require lime injection or scrubbers in high-S fuels
4. Chlorine, Dioxins, and Corrosion
High chlorine fuels (e.g., wheat straw, certain bark) emit chlorinated hydrocarbons and accelerate corrosion
Dioxins form under poor combustion at 250–450°C
Waste wood and RDF must be screened for halogenated compounds
📊 Fuel Type vs. Emission Control Requirements
Fuel Type | Emission Concern | Required Controls | Boiler Compatibility |
---|---|---|---|
Wood Pellets | Minimal PM/NOₓ/SO₂ | Cyclone or simple bag filter | Pellet burner, condensing |
Wood Chips | Medium PM, moderate NOₓ | Multicyclone + SNCR or low-NOₓ burner | Grate, BFB |
Agri-Residue | High PM, high NOₓ, dioxin | Bag filter + SNCR + lime injection + FGR | BFB, CFB |
Waste Wood | PM, heavy metals, dioxins | Bag filter + activated carbon + thermal oxidizer | Advanced CFB with filtration |
🏛️ Regulatory Examples Linked to Fuel Types
Jurisdiction | Fuel-Specific Regulation/Guideline | Example Compliance Measures |
---|---|---|
EU IED | Stricter for high-ash/agri fuels | Bag filter + SCR required |
US EPA | Differentiates between clean wood and treated wood | Waste wood requires VOC and Hg controls |
China GB13271 | Stricter PM limits for straw and rice husk | ESP + SNCR + fuel pre-treatment |
India CPCB | Agri-fuel boilers must add cyclones and PM capture | Cyclone + FGR mandatory |
Some regions incentivize the use of clean biomass by streamlining permitting or offering tax breaks—provided emissions are kept within defined boundaries.
🧪 Case Study: Industrial Paper Mill Using Mixed Biomass
Fuel: 50% eucalyptus chips, 50% rice husk
Issue: Excessive PM (85 mg/Nm³) and NOₓ (250 mg/Nm³), above EU limits
Solution:
Installed bag filter with ash recirculation
SNCR system for NOₓ reduction
Adjusted air/fuel ratio and added fuel screening
Result:
PM reduced to 22 mg/Nm³
NOₓ reduced to 160 mg/Nm³
Compliance achieved under IED
ROI: 1.6 years
🔍 Strategies for Emissions-Compliant Fuel Use
Strategy | Benefit | Application |
---|---|---|
Fuel Pre-Screening (N, Cl, Ash) | Avoids unsuitable high-emission batches | Agri-residue and wood waste |
Densification (Pelleting) | Reduces PM and improves combustion control | Forest residues |
Fuel Blending | Dilutes high-risk fuels to meet thresholds | Chips + pellets or husk |
Low-NOₓ Combustion Control | Prevents costly post-combustion upgrades | All biomass types |
Pre-Drying (≤15% moisture) | Reduces CO and PM emissions | Wet wood chips and bark |
Combining clean fuel input with targeted combustion optimization can cut emissions 30–50% without excessive capital costs.
In summary, fuel type is a first-tier determinant of emissions compliance in biomass combustion. Each category—wood chips, pellets, agri-residues—brings distinct combustion chemistry and ash behavior that influence pollutant formation. Proper fuel selection, blending, and treatment not only reduce the burden on filtration systems but are essential to choosing the correct combustion technology. An emissions-compliant boiler starts with a clean, consistent, and well-understood fuel strategy.
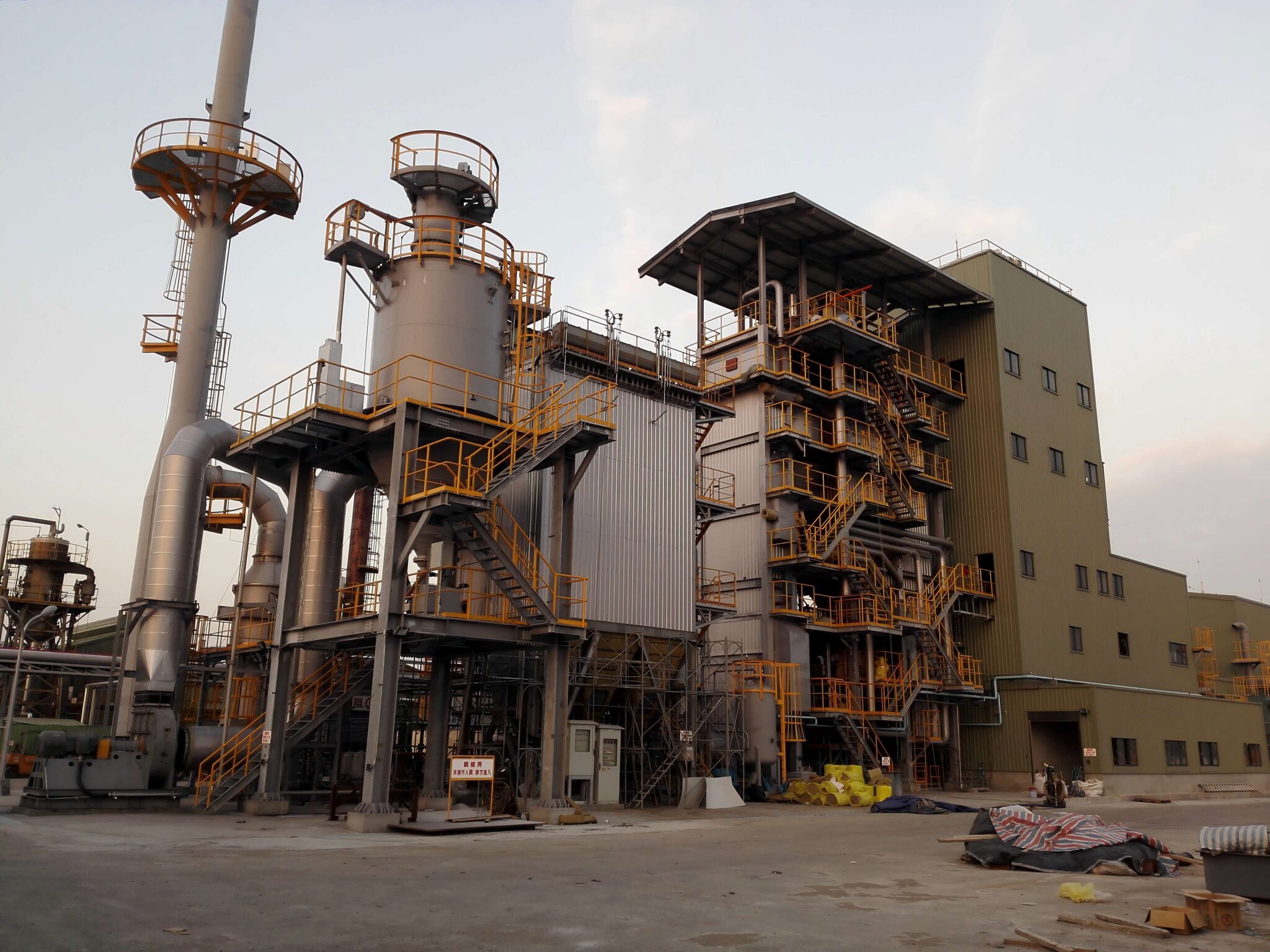
What Emission Control Technologies Are Commonly Used in Biomass Boiler Systems?
Even though biomass is a renewable and carbon-neutral energy source, it doesn’t automatically qualify as “clean.” In fact, biomass combustion—especially when using wood waste, agricultural residues, or mixed fuels—can emit significant levels of particulate matter (PM), nitrogen oxides (NOₓ), carbon monoxide (CO), sulfur oxides (SO₂), volatile organic compounds (VOCs), heavy metals, and even dioxins. These emissions are subject to strict environmental regulations globally, and failure to meet them can lead to fines, permit denials, or forced shutdowns. This is where emission control technologies come into play. They are essential components of biomass boiler systems, strategically selected to capture or neutralize pollutants before they reach the atmosphere—ensuring compliance, safety, and sustainability.
The most commonly used emission control technologies in biomass boiler systems include mechanical dust collectors (cyclones), electrostatic precipitators (ESPs), baghouse filters, selective non-catalytic reduction (SNCR), selective catalytic reduction (SCR), dry and wet scrubbers, and activated carbon injection systems. These technologies are used to control particulate matter, NOₓ, SO₂, heavy metals, VOCs, and dioxins, and are selected based on fuel type, combustion conditions, pollutant levels, regulatory requirements, and boiler size.
An efficient biomass boiler system isn’t just about generating heat—it’s about doing so within the constraints of emissions compliance, which requires the correct stack of control technologies tailored to the pollutants being produced.
Electrostatic precipitators are effective in removing fine particulate matter from biomass boiler emissions.True
ESPs use electric fields to charge and collect fine particulates with over 99% efficiency, making them ideal for high-ash biomass combustion.
🧰 Overview of Major Emission Control Technologies in Biomass Boilers
Pollutant Controlled | Control Technology | Typical Efficiency (%) | Best For |
---|---|---|---|
Particulate Matter (PM) | Cyclone Dust Collectors | 60–85 | Coarse ash, low regulation |
Multicyclones | 80–90 | Moderate emission zones | |
Electrostatic Precipitators (ESPs) | 95–99.9 | High-ash fuels, large boilers | |
Baghouse Filters | 99–99.9 | Ultra-low PM standards | |
Nitrogen Oxides (NOₓ) | Flue Gas Recirculation (FGR) | 20–30 | Small-medium boilers |
Selective Non-Catalytic Reduction (SNCR) | 40–70 | Medium-scale plants | |
Selective Catalytic Reduction (SCR) | 80–95 | Large systems, strict limits | |
Sulfur Oxides (SO₂) | Dry Sorbent Injection (DSI) | 50–75 | Low-medium sulfur fuels |
Wet Scrubbers | 90–98 | High sulfur/agri residues | |
VOCs & Dioxins | Afterburners (thermal oxidizers) | >95 | VOC-rich or chlorinated fuel |
Activated Carbon Injection (ACI) | 80–95 (Hg/VOCs) | Treated wood, RDF | |
Heavy Metals (Hg, Cd, Pb) | Baghouse + ACI | 90–99 | Contaminated biomass |
Each technology must be tailored to the specific emissions profile generated by the boiler-fuel combination and local air quality limits.
🔥 Particulate Matter (PM) Control Technologies
1. Cyclones and Multicyclones
Use centrifugal force to separate large ash particles
Often used as pre-filters
Inexpensive, low-maintenance, but limited for fine PM
2. Electrostatic Precipitators (ESPs)
Electrically charges ash particles which are attracted to oppositely charged plates
High efficiency for PM <10 µm
Best suited for large-scale, high-ash biomass plants
3. Baghouse Filters
Fabric filters that trap even ultra-fine particles
Efficiency >99.9%
Require regular cleaning and pressure monitoring
Ideal for systems under <30 mg/Nm³ PM limits
| Comparison of PM Control Systems |
System | PM Efficiency (%) | Space Requirement | Maintenance | Suitability |
---|---|---|---|---|
Cyclone | 60–85 | Small | Low | Coarse ash, low budget |
ESP | 95–99.9 | Large | Medium | High-ash, large systems |
Bag Filter | 99–99.9 | Medium | High | Fine ash, low PM limits |
🌬️ NOₓ Control Technologies
1. Flue Gas Recirculation (FGR)
Reduces peak combustion temperatures
Simple but limited effectiveness
2. Selective Non-Catalytic Reduction (SNCR)
Urea or ammonia injected into flue gas at 850–1050°C
Reduces NOₓ to N₂ and H₂O
Less efficient at low temperatures
3. Selective Catalytic Reduction (SCR)
Same reactants as SNCR but with a catalyst at 300–400°C
Up to 95% NOₓ reduction
Requires significant capital and maintenance
| NOₓ Control System Comparison |
System | NOₓ Reduction (%) | CAPEX Impact | Fuel Flexibility | Temperature Range |
---|---|---|---|---|
FGR | 20–30 | Low | High | Combustion zone |
SNCR | 40–70 | Moderate | Medium | 850–1050°C (post-burner) |
SCR | 80–95 | High | Medium | 300–400°C (flue gas stream) |
💧 SO₂ and Acid Gas Control Technologies
1. Dry Sorbent Injection (DSI)
Injects lime or sodium bicarbonate into flue gas
Moderate efficiency for medium sulfur levels
2. Wet Scrubbers
Absorb SO₂ and acid gases in a liquid medium
Very high removal efficiency
Require water treatment and mist eliminators
System | SO₂ Reduction (%) | O&M Complexity | Water Use | Common in |
---|---|---|---|---|
DSI | 50–75 | Low | None | Medium-sulfur biomass |
Wet Scrubber | 90–98 | High | High | High-S fuels, agri-residue |
🧪 VOCs, Dioxins, and Heavy Metal Control
1. Afterburners/Thermal Oxidizers
Secondary combustion chamber burns off VOCs and dioxins
Requires >850°C and residence time
2. Activated Carbon Injection (ACI)
Binds mercury, cadmium, dioxins, and VOCs
Injected before bag filter or ESP
3. Combined Systems
Bag Filter + ACI provides high total removal of fine and toxic pollutants
📊 Emission Control Systems Integration Example
Boiler Size | Fuel Type | PM Control | NOₓ Control | Acid Gas Control | Advanced Controls Needed |
---|---|---|---|---|---|
2 MW | Wood Chips | Multicyclone | FGR | None | None |
5 MW | Agri-residue | Bag Filter | SNCR | DSI | CEMS |
15 MW | Mixed Biomass | ESP + ACI | SCR | Wet Scrubber | O₂ trim, ash re-injection |
30 MW | Wood Waste | Bag Filter | SNCR | Lime Injection | Activated carbon system |
🔍 Selecting the Right Emission Control Stack
When choosing emission control technologies for a biomass boiler, consider:
Fuel properties: Ash, moisture, sulfur, nitrogen, chlorine
Boiler type: Grate, BFB, CFB, pellet
Emission limits: National and regional standards
Operation hours: Continuous vs. batch systems
Footprint & cost constraints
A customized control system designed from actual fuel analysis and emissions modeling offers the best path to cost-effective compliance.
In conclusion, emission control technologies are the critical backbone of any compliant biomass boiler system. From simple cyclones to advanced catalytic systems, each technology targets specific pollutants and must be carefully selected based on the fuel type, combustion conditions, and regulatory environment. With stricter emissions standards globally, integrating the right technologies from the start is not just smart—it’s essential for long-term operation, sustainability, and legal compliance.

Why Is Continuous Emission Monitoring Important for Regulatory Compliance?
In today’s heavily regulated industrial environment, merely installing pollution control equipment isn’t enough to prove environmental responsibility or legal compliance. Governments and regulatory bodies worldwide now demand proof of emissions performance—continuously and in real time. For operators of biomass boilers, this means deploying Continuous Emission Monitoring Systems (CEMS) that not only track key pollutants but also document and report emissions data with absolute transparency. Failure to monitor emissions continuously can result in legal penalties, plant shutdowns, loss of operational permits, and reputational harm. Therefore, investing in reliable, calibrated, and regulation-compliant CEMS is a strategic necessity for long-term success.
Continuous Emission Monitoring is essential for regulatory compliance because it provides real-time, verifiable data on pollutant emissions such as particulate matter, NOₓ, SO₂, CO, and O₂. Regulatory authorities in regions such as the EU, US, China, and India require CEMS to ensure that biomass boiler operators remain within legal emission limits. CEMS also supports automated reporting, alarm triggering, performance verification, and timely interventions that help facilities avoid fines, non-compliance notices, and permit violations.
Whether you’re operating a 5 MW boiler in India or a 50 MW CHP plant in Germany, CEMS ensures that emission levels are continuously recorded, validated, and reported—meeting the standards of regulators, investors, insurers, and auditors alike.
CEMS is only required for fossil fuel plants, not for biomass combustion systems.False
Biomass combustion can also emit regulated pollutants such as PM, NOₓ, and CO. In many jurisdictions, CEMS is required for any combustion system above a specific capacity, regardless of fuel type.
🔍 What Is a Continuous Emission Monitoring System (CEMS)?
A CEMS is a complete suite of instruments, analyzers, data acquisition software, and reporting tools designed to continuously measure and record emissions from combustion processes.
Component | Function |
---|---|
Gas Analyzers | Measure NOₓ, SO₂, CO, O₂, CO₂, HCl, NH₃ |
Particulate Monitors | Track PM10, PM2.5 levels |
Sample Conditioning Units | Remove moisture/impurities for accurate readings |
Data Acquisition System (DAS) | Collects, logs, and reports emissions data |
Stack Probes & Extractors | Collect samples from the flue gas stream |
Calibration Module | Ensures measurement accuracy per ISO/EPA standards |
CEMS systems can be extractive (hot/wet or dry) or in-situ (laser or optical) depending on regulatory requirements and site-specific conditions.
🌍 Regulatory Drivers for CEMS Installation
Jurisdiction | Legal Basis for CEMS Requirement | Applicability |
---|---|---|
EU | Industrial Emissions Directive (2010/75/EU) | >20 MWth boilers, waste co-firing |
USA | EPA 40 CFR Part 60 (NSPS), Part 75 (Acid Rain Program) | All major combustion units |
China | GB 13271-2014, HJ/T 212-2017 | All boilers >10 tph |
India | CPCB Emission Norms, CREP Guidelines | Boilers >5 tph |
Canada | Provincial Guidelines (e.g., Ontario Regulation 419) | Case-by-case |
These regulations often mandate hourly, daily, and annual reporting via online portals—data that must come directly from CEMS without manual intervention.
📈 How CEMS Enhances Compliance and Operational Efficiency
Benefit | Description |
---|---|
Regulatory Compliance | Meets legal reporting requirements for pollutants |
Real-Time Alerts | Notifies operators of limit exceedances instantly |
Audit Readiness | Stores verified data logs for inspections and external audits |
O&M Optimization | Helps identify efficiency loss or pollution spikes |
Emission Trend Analysis | Enables proactive maintenance and fuel adjustment |
Permit Renewal Support | Facilitates emission certificate renewals and ISO 14001/50001 audits |
🧪 CEMS-Measured Pollutants in Biomass Boilers
Pollutant | Common CEMS Monitoring Method | Reason for Monitoring |
---|---|---|
NOₓ | Chemiluminescence or NDIR | Regulatory compliance, combustion tuning |
SO₂ | UV Fluorescence | High-sulfur fuels or bark |
CO | NDIR | Incomplete combustion detection |
O₂ | Zirconia or Paramagnetic sensor | Air-fuel ratio validation |
PM | Opacity or Triboelectric sensor | Emission cap enforcement |
Hg/VOCs | Sorbent traps or FTIR (if required) | Waste wood or contaminated fuels |
🛠️ CEMS Implementation Example
Scenario:
Biomass cogeneration plant in Italy, 15 MWth, firing mixed wood chips and olive pomace
Regulatory Limit (per EU IED):
PM: <20 mg/Nm³
NOₓ: <180 mg/Nm³
CO: <100 mg/Nm³
CEMS Installed:
Opacity monitor (PM)
NDIR gas analyzers for CO, NOₓ, SO₂
O₂ zirconia probe
DAS with real-time limit alarms
Remote reporting interface to Italian environmental agency (ARPA)
Results:
Avoided €250,000 in non-compliance fines over 3 years
Reduced combustion losses by optimizing excess air
Gained ISO 14001 certification
🧩 Common CEMS Integration Challenges and Solutions
Challenge | Solution |
---|---|
High Dust in Flue Gas | Use probe filters and pre-cleaning stages |
Moisture in Biomass Combustion | Heated sample lines or hot-wet extractive systems |
Fuel Variability | Dynamic calibration and AI-based controls |
Limited Space in Retrofit | Use compact in-situ analyzers |
Facilities must also establish quality assurance protocols (QAL1, QAL2, QAL3 in EU) or EPA Method 21, 30B, 9 in the US for system calibration and data validation.
In conclusion, Continuous Emission Monitoring is a regulatory and operational cornerstone of any modern biomass boiler system. With increasing pressure from governments, financiers, and communities for transparent and environmentally responsible energy use, real-time emission monitoring is not just a tool—it’s a requirement. Whether for compliance, optimization, or corporate sustainability, CEMS ensures that emissions stay within limits, performance remains high, and your operations stay future-proof.
🔍 Conclusion
While biomass boilers offer a green alternative to fossil fuels, they must still comply with a wide range of air quality and environmental regulations. Fuel selection, combustion design, and emission control strategies must all be aligned with legal standards to ensure safe, efficient, and compliant operation. Understanding these regulatory drivers from the start helps you avoid costly redesigns, penalties, or operational interruptions—paving the way for a truly sustainable and compliant biomass energy system.
📞 Contact Us
💡 Need help selecting an environmentally compliant biomass boiler? Our experts specialize in low-emission system design, regulatory consulting, and turnkey biomass boiler solutions for a wide range of industries.
🔹 Get in touch today to ensure your biomass boiler system meets environmental standards and delivers clean, reliable energy! 🌱🔥✅
FAQ
What environmental regulations affect industrial biomass boiler selection?
Industrial biomass boilers must comply with local, national, and international air quality regulations such as the U.S. EPA Clean Air Act, EU Industrial Emissions Directive (IED), and regional rules targeting PM, CO, NOx, SO₂, and VOC emissions.
Why are particulate matter (PM) limits critical for biomass boilers?
Biomass combustion can release fine particulate matter (PM2.5 and PM10), which affects air quality and human health. Regulations often require multi-cyclones, baghouse filters, or electrostatic precipitators (ESP) to control emissions.
How do emission limits for NOx and CO influence boiler design?
Biomass combustion can produce NOx and CO depending on combustion temperature and oxygen levels. Low-NOx burner designs, staged combustion, and oxygen trim systems are often required to meet stringent limits.
What role does fuel quality play in regulatory compliance?
High-moisture or high-ash biomass can increase emissions and affect combustion efficiency. Regulatory compliance may depend on selecting standardized, clean fuels (e.g., certified pellets) and ensuring consistent fuel characteristics.
Are biomass boilers eligible for regulatory incentives or credits?
Yes. Many regions provide incentives, tax credits, or renewable energy certificates (RECs) for biomass systems that meet environmental standards, helping offset compliance and technology investment costs.
References
EPA Emission Standards for Biomass Boilers – https://www.epa.gov
EU Industrial Emissions Directive (IED) – https://www.europa.eu
Air Quality Regulations for Combustion Systems – https://www.energy.gov
Particulate Emissions from Biomass Combustion – https://www.sciencedirect.com
Best Available Techniques (BAT) for Biomass Boilers – https://www.researchgate.net
Emission Control in Biomass Systems – https://www.bioenergyconsult.com
Renewable Energy Incentives for Biomass – https://www.energysavingtrust.org.uk
Low-NOx Technologies for Biomass Boilers – https://www.mdpi.com
Fuel Standards and Emissions in Biomass Systems – https://www.iea.org
Monitoring and Compliance for Industrial Boilers – https://www.automation.com
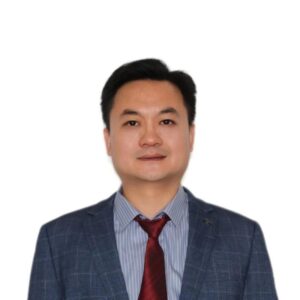