In industrial power generation, thermal efficiency is one of the most critical indicators of boiler performance. It reflects how effectively the boiler converts the chemical energy of fuel into usable steam energy for electricity production or industrial use. Failing to measure and monitor this metric can lead to fuel waste, reduced output, increased emissions, and even system degradation. Understanding how to accurately calculate thermal efficiency is key to optimizing energy usage and reducing operational costs.
The thermal efficiency of an industrial power plant boiler is measured by comparing the useful heat output (typically in the form of high-pressure steam) to the total energy input from the fuel source. This is typically done using either the Direct Method (input-output method) or the Indirect Method (heat loss method). Accurate thermal efficiency measurement requires data on steam production rate, fuel flow rate, flue gas temperature and composition, boiler pressure, and losses such as radiation and blowdown.
Let’s explore the standard methods and best practices used to calculate the real-world efficiency of power plant boilers.
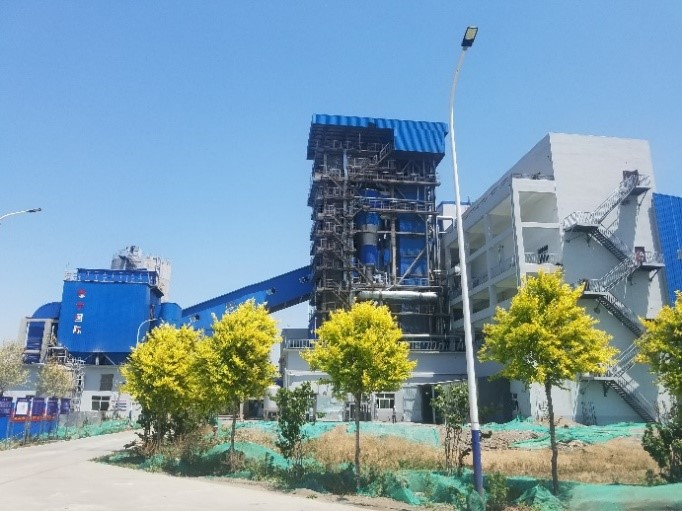
What Is Thermal Efficiency and Why Is It Critical in Power Plant Boilers?
Power plants run on heat—whether it’s from burning coal, biomass, natural gas, or using nuclear reactions. But not all the heat produced ends up as useful electricity or process steam. A large portion of that energy is lost through exhaust gases, radiation, unburned fuel, or moisture evaporation. The ratio of useful heat extracted to total fuel energy input is what we call thermal efficiency. In power plant boilers, where massive volumes of fuel are consumed daily, even a few percentage points in thermal efficiency make the difference between profit and loss, compliance and violation, or sustainability and waste. It’s the single most important metric for evaluating a boiler’s energy performance.
Thermal efficiency in power plant boilers is the percentage of heat from fuel combustion that is successfully converted into useful steam energy. It measures how effectively the boiler transforms fuel input into thermal output and is critical because it directly affects fuel consumption, operating costs, CO₂ emissions, and overall power generation efficiency. Higher thermal efficiency means more energy is extracted from each unit of fuel, while lower efficiency indicates heat losses and operational inefficiencies. Optimizing thermal efficiency is essential for economic viability and environmental compliance.
In power generation, thermal efficiency defines how much energy your plant delivers—and how much it wastes.
Thermal efficiency is a key indicator of how effectively a boiler converts fuel into usable steam or energy.True
It directly impacts fuel costs, emissions output, and power plant performance.
🔍 Understanding Thermal Efficiency in Boiler Systems
Term | Definition |
---|---|
Thermal Efficiency (%) | (Useful heat output / Fuel heat input) × 100 |
Useful Heat Output | Energy transferred to generate steam |
Fuel Heat Input | Total chemical energy in the fuel burned |
Inefficiencies | Heat lost via flue gas, radiation, unburned carbon, blowdown |
→ Power plant boilers typically have thermal efficiencies between 85–92%, depending on fuel type and system design.
📊 Example of Heat Balance in a Power Plant Boiler
Energy Flow | Approximate Share (%) |
---|---|
Heat absorbed to generate steam | 85–90 |
Flue gas heat loss | 5–8 |
Radiation and convection losses | 1–2 |
Unburned fuel and blowdown losses | 0.5–1.5 |
→ The goal is to minimize every form of loss and drive output closer to 100% of input.
🛠 Why Thermal Efficiency Matters in Power Plant Boilers
Factor | How It Relates to Thermal Efficiency |
---|---|
Fuel Costs | Higher efficiency = less fuel per unit of output |
Emissions Compliance | Lower fuel use = lower CO₂, NOx, SOx per MWh |
Steam Production | Efficient heat transfer = steady, reliable output |
Heat Rate (kJ/kWh) | Lower thermal efficiency = higher heat rate |
Maintenance and Life Cycle | Fouling and poor combustion reduce efficiency over time |
→ A 1% efficiency improvement can yield hundreds of thousands in annual fuel savings in large power stations.
📈 Thermal Efficiency vs. Boiler Operating Parameters
Operating Parameter | Efficiency Impact |
---|---|
Flue Gas Temperature | Higher temps = heat loss ↑, efficiency ↓ |
Oxygen (O₂) Level in Flue Gas | Excess air = efficiency ↓ if O₂ > 6% |
Carbon Monoxide (CO) | Indicates incomplete combustion = efficiency ↓ |
Steam Pressure/Temp Control | Deviations = lower energy conversion |
Soot and Ash Fouling | Insulates tubes = lowers heat transfer |
→ Monitoring these metrics ensures efficiency stays at optimal levels.
🧪 Case Study – 150 MW Pulverized Coal Boiler Efficiency Optimization
Initial Condition:
Thermal efficiency: 84.2%
Flue gas temperature: 270°C
O₂ in stack: 6.5%
CO: 180 ppm
Actions Taken:
Burner realignment and excess air reduced
Added soot blower cycles
Installed O₂ trim system
Results:
Flue gas temp reduced to 195°C
CO < 70 ppm
Thermal efficiency improved to 89.1%
Annual coal savings: >12,000 tons
📏 Benchmark Thermal Efficiency Values
Boiler Type | Typical Efficiency (%) | Remarks |
---|---|---|
Natural Gas Fired | 88–92 | Clean combustion, low ash |
Coal Fired (PC/CFB) | 84–89 | Higher losses due to ash and air fans |
Biomass Fired | 75–85 | Variable fuel, ash fouling risk |
Combined Cycle HRSG | 90–94 | High efficiency due to gas turbine waste heat |
→ Maintaining these levels requires ongoing performance tuning and maintenance.
🔧 How to Improve Thermal Efficiency
Improvement Area | Action |
---|---|
Air-Fuel Ratio Control | Install O₂ trim systems, tune burners |
Heat Recovery | Use economizer, air preheater, condensing economizer |
Surface Cleanliness | Schedule soot blowing, deslagging |
Fuel Quality Management | Ensure consistent calorific value and ash |
Instrumentation and Monitoring | Log flue gas temp, CO, O₂, efficiency trends |
→ Efficiency isn’t a one-time achievement—it’s a continuous optimization process.
In conclusion, thermal efficiency is the most critical performance metric in power plant boilers, as it determines how effectively fuel energy is converted into usable steam and electricity. Poor efficiency translates directly into fuel waste, higher emissions, and operational cost overruns. By actively monitoring combustion quality, heat recovery, and system cleanliness, plant operators can sustain high efficiency and unlock long-term economic and environmental gains. In power generation, every percentage point in thermal efficiency is a percentage point of competitive advantage.
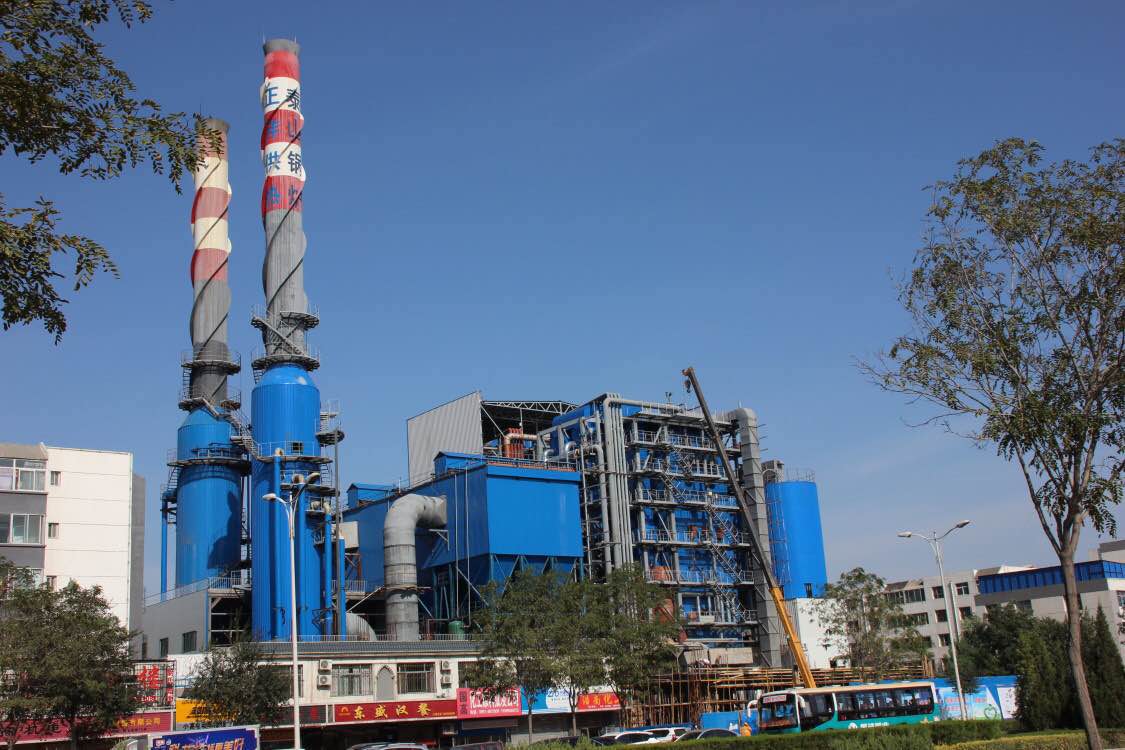
How Is the Direct Method Used to Measure Boiler Efficiency in Power Generation?
In large-scale power generation, knowing how effectively your boiler converts fuel into usable energy is essential for cost control and performance optimization. The Direct Method—also known as the input-output method—offers a simple and fast way to assess this efficiency. Unlike methods that require advanced gas analysis or detailed heat loss breakdowns, the Direct Method focuses on just two measurable values: the energy in the steam produced and the energy in the fuel consumed. This makes it a highly practical tool for operators to track boiler efficiency daily and identify changes in performance over time.
The Direct Method measures boiler efficiency by comparing the useful heat in the steam output with the total heat from the fuel burned. It involves calculating how much steam is generated per hour and determining how much fuel is used in that time. The heat energy in the steam is estimated using steam pressure and temperature, while the heat from the fuel is determined using the fuel’s calorific value. The ratio of these two values—useful output divided by fuel input—gives the boiler efficiency in percentage.
It’s a straightforward approach with high operational value—and no need for complex equations.
The Direct Method offers a fast and practical way to calculate boiler efficiency using only steam output and fuel input.True
It helps operators measure real-time performance without needing detailed combustion or flue gas data.
🔍 What Do You Need to Use the Direct Method?
Measurement Required | Description |
---|---|
Steam Flow Rate (kg/hr) | How much steam the boiler produces |
Steam Pressure & Temperature | Used to estimate energy content of the steam |
Feedwater Temperature | Needed to calculate net heat added to water |
Fuel Consumption (kg/hr or m³/hr) | Total amount of fuel used during measurement period |
Fuel Calorific Value (CV) | Energy content per unit of fuel (from lab test or datasheet) |
→ These are standard parameters already available in most power plant control rooms.
🛠 How the Direct Method Works (Without Complex Formulas)
Measure the steam output:
Use your steam flowmeter to find out how many kilograms of steam the boiler produces in one hour.Find the energy in that steam:
Use steam tables to get the energy (in kcal or MJ) contained in the steam based on its pressure and temperature. Then subtract the energy already in the feedwater to get the actual energy gained.Measure the fuel used:
Check how much fuel was consumed in that same hour—this could be coal in tons, gas in cubic meters, or biomass in kilograms.Know your fuel’s energy value:
Use a lab report or fuel datasheet to find out the calorific value (how much energy one unit of that fuel provides).Compare output to input:
Divide the energy delivered by the steam by the total energy supplied by the fuel. Multiply by 100 to get the efficiency percentage.
→ If your boiler generates more steam with less fuel, your efficiency is going up.
📊 Practical Example – Coal-Fired Power Boiler
Parameter | Value |
---|---|
Steam Produced | 120,000 kg/hr |
Steam Pressure / Temp | 65 bar / 480°C |
Feedwater Temperature | 105°C |
Fuel Used | 14,000 kg/hr (coal) |
Calorific Value of Coal | 4,200 kcal/kg |
Result:
Energy in steam is estimated based on steam conditions → let’s say ~66 kcal/kg of steam gained
Total steam energy = 120,000 × 66 = 7,920,000 kcal/hr
Energy from fuel = 14,000 × 4,200 = 58,800,000 kcal/hr
Efficiency = (7.92 ÷ 58.8) × 100 = ~86.5%
→ This means 86.5% of the fuel energy is being converted into useful steam.
📋 Benefits of Using the Direct Method
Advantage | Why It Matters |
---|---|
Simple and fast | No need for flue gas analyzers or lab setups |
Easy to automate | Can be built into daily SCADA/PLC reports |
Good for daily tracking | Identifies drops in performance immediately |
Works with all fuels | Whether it’s coal, gas, biomass, or oil |
Supports decision-making | Helps optimize burner settings and fuel strategies |
→ Ideal for real-time operational feedback.
🧪 Case Study – Daily Monitoring in a Biomass Boiler
System: 10 TPH biomass-fired boiler
Issue: Gradual drop in steam output despite same fuel use
Method Used: Direct Method daily over two weeks
Findings:
Efficiency dropped from 83.1% to 76.4%
Investigation showed soot buildup in economizer
Cleaning restored flue gas temp from 240°C to 185°C
Efficiency returned to 84.2%
→ Regular Direct Method checks helped avoid unplanned shutdown and fuel waste.
🔧 Best Practices When Using the Direct Method
Practice | Purpose |
---|---|
Use fresh fuel CV data | Fuel quality changes; don’t rely on old numbers |
Log steam and fuel hourly | Helps spot trends and anomalies |
Check feedwater temp accuracy | Essential for calculating true heat input |
Verify steam meter calibration | Incorrect readings distort efficiency |
Use during steady load conditions | Avoid measuring during load changes or trip events |
→ Good data = trustworthy results.
In conclusion, the Direct Method is an operator-friendly, fast, and effective way to measure boiler efficiency in power generation environments. It focuses on what comes in (fuel) and what goes out (steam), using only standard plant data to deliver meaningful insights. When used consistently, it can help detect performance losses early, guide maintenance actions, and maximize fuel economy. In every power plant, knowing your efficiency in real-time is the first step to improving it.
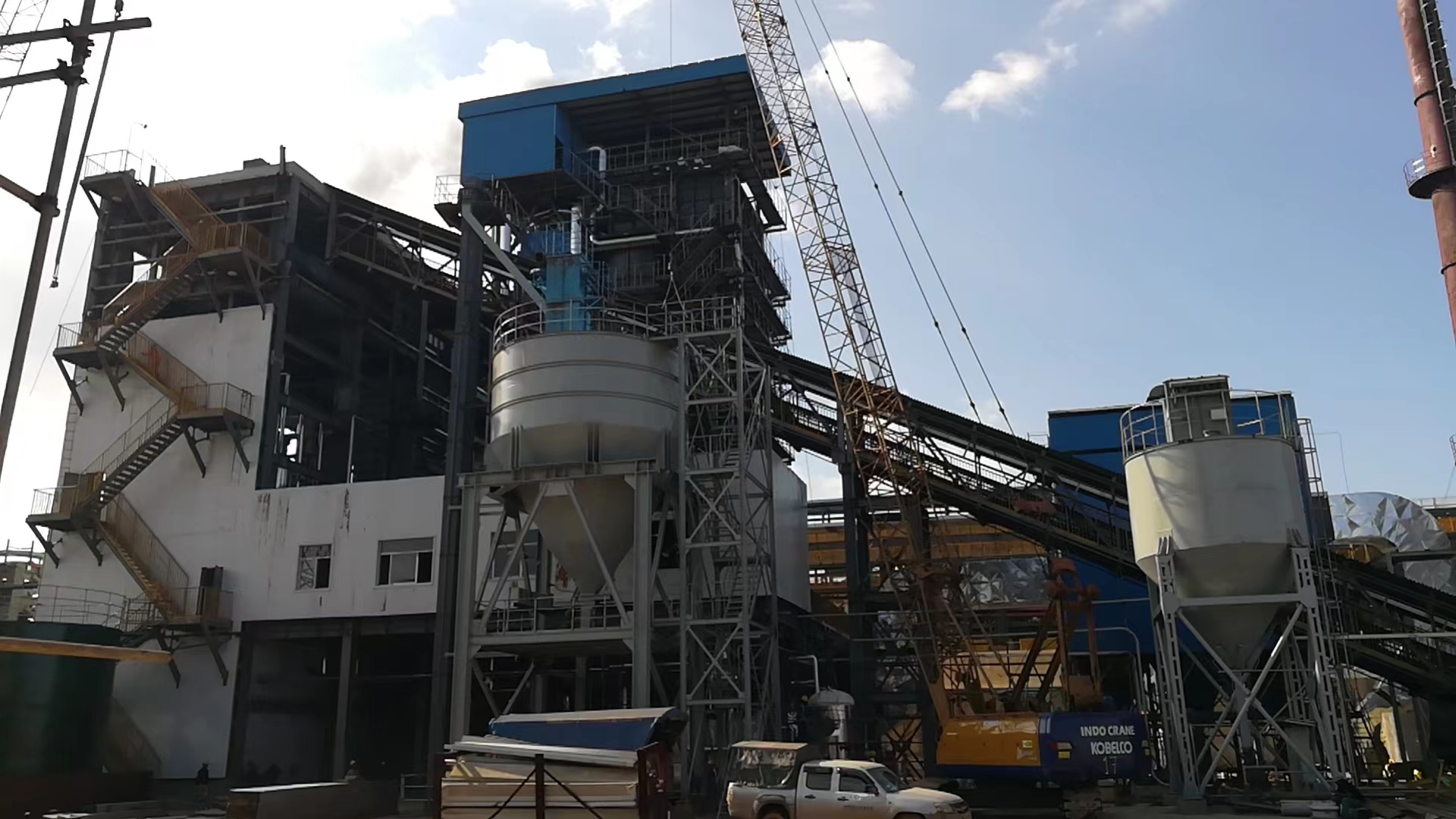
What Is the Indirect Method and Which Heat Losses Does It Account For?
When precision and diagnostic detail are required in power plant boiler performance evaluation, engineers turn to the Indirect Method of boiler efficiency measurement. Unlike the Direct Method, which simply compares input and output, the Indirect Method dissects the boiler’s energy losses—identifying exactly where heat is wasted. By quantifying each form of thermal loss individually (such as flue gas loss, unburned carbon, radiation, and moisture evaporation), this approach allows for deeper insight into inefficiencies, making it a preferred tool for high-capacity, high-pressure boiler systems found in thermal power plants.
The Indirect Method measures boiler efficiency by subtracting the sum of all quantified heat losses from 100%. It identifies where and how heat is lost—including dry flue gas, moisture from fuel and air, unburned carbon, radiation, and combustion inefficiencies. This method provides detailed analysis for optimization by highlighting which loss contributes most to overall inefficiency, enabling corrective actions to improve thermal performance.
In short, the Indirect Method doesn’t just measure efficiency—it explains it.
The Indirect Method identifies individual heat losses to calculate boiler efficiency.True
By accounting for each type of thermal loss, it allows for detailed diagnostics and targeted performance improvements.
🔍 Overview of the Indirect Method
Feature | Description |
---|---|
Efficiency Formula | Efficiency (%) = 100 – Σ (All Heat Losses %) |
Purpose | Pinpoint exact causes of efficiency loss |
Applications | Diagnostic audits, tuning, long-term performance tracking |
Requires | Flue gas composition, temperature, fuel analysis, ash content |
→ The Indirect Method is data-intensive, but highly informative.
📏 Major Heat Losses Considered in the Indirect Method
Heat Loss Type | Description |
---|---|
L1: Dry Flue Gas Loss | Heat carried away by hot combustion gases exiting the stack |
L2: Evaporation of Water in Fuel | Heat used to evaporate moisture content in biomass/coal |
L3: Loss due to H₂ in Fuel | Heat lost from evaporating water formed by burning hydrogen |
L4: Unburned Carbon in Ash (UBC) | Energy left in unburned fuel that is removed as bottom/fly ash |
L5: Radiation and Convection Losses | Surface heat loss from the boiler walls, ducts, and pipes |
L6: Loss due to Incomplete Combustion (CO) | Indicates poor combustion if high CO levels are detected |
L7: Moisture in Combustion Air | Heat used to vaporize humidity in air (minor in dry climates) |
→ Each of these losses is expressed as a percentage of total fuel energy input.
📊 Example: Heat Loss Breakdown in a Coal-Fired Boiler (90 TPH)
Heat Loss Component | Value (%) |
---|---|
L1: Dry Flue Gas Loss | 6.2 |
L2: Moisture in Fuel | 3.4 |
L3: Hydrogen in Fuel | 2.1 |
L4: UBC in Ash | 1.8 |
L5: Radiation/Convection | 1.5 |
L6: Incomplete Combustion (CO) | 0.6 |
L7: Moisture in Air | 0.3 |
Total Losses | 15.9% |
Boiler Efficiency (Indirect) | 84.1% |
→ This breakdown helps target which loss (e.g., dry flue gas or fuel moisture) to reduce first.
🛠 Data Required for the Indirect Method
Measurement/Input | Purpose |
---|---|
Flue Gas Temperature (°C) | Determines stack gas heat loss |
Ambient Air Temperature (°C) | Needed for radiation/convection calculations |
O₂ or CO₂ in Flue Gas (%) | Used to calculate excess air and flue gas volume |
Fuel Analysis (proximate & ultimate) | Moisture, hydrogen, ash, calorific value |
Ash Content and UBC (%) | For estimating unburned fuel loss |
CO in Flue Gas (ppm) | Identifies incomplete combustion |
→ Accuracy of these inputs directly affects the reliability of the results.
🧪 Case Study – Biomass Boiler with 18% Moisture Fuel
Problem: High fuel consumption and ash carryover
Indirect Method Findings:
L1 (Dry Flue Gas) = 5.8%
L2 (Moisture in Fuel) = 6.7%
L4 (Unburned Carbon in Ash) = 2.2%
L5 (Radiation Loss) = 1.3%
Efficiency = 83.0%
Intervention:
Installed biomass dryer → reduced moisture to 10%
Improved grate air distribution for complete burn
Post-change Efficiency: 88.6%
→ Detailed loss analysis guided targeted investments with measurable gains.
📈 Comparison: Indirect vs. Direct Method
Criteria | Direct Method | Indirect Method |
---|---|---|
Data Simplicity | High | Moderate to complex |
Time to Calculate | Fast (minutes) | Slower (requires multiple inputs) |
Identifies Loss Sources | No | Yes |
Preferred Use | Daily monitoring | Auditing, diagnostics |
Accuracy with Varying Fuels | Lower | Higher |
→ Use Direct Method for speed; Indirect for insight.
🔧 How to Use the Indirect Method Effectively
Practice | Purpose |
---|---|
Regular Flue Gas Testing | Tracks CO, O₂, NOx, CO₂, temperature |
Maintain Fuel Quality Records | Tracks changes in moisture, ash, calorific value |
UBC Sampling of Ash | Confirms combustion efficiency |
Calibrate Sensors and Probes | Ensures valid measurement inputs |
Benchmark Monthly Efficiency | Detects degradation trends |
→ A well-executed Indirect Method becomes a strategic performance tool.
In conclusion, the Indirect Method is a comprehensive approach to evaluating boiler efficiency by identifying and quantifying all significant heat losses. It empowers engineers and plant operators to pinpoint exactly where performance losses occur and take targeted corrective action—whether it’s reducing fuel moisture, optimizing air-fuel ratios, or improving combustion quality. In power plant operations, where margins are thin and fuel costs are high, the Indirect Method is not just a diagnostic tool—it’s an investment roadmap.
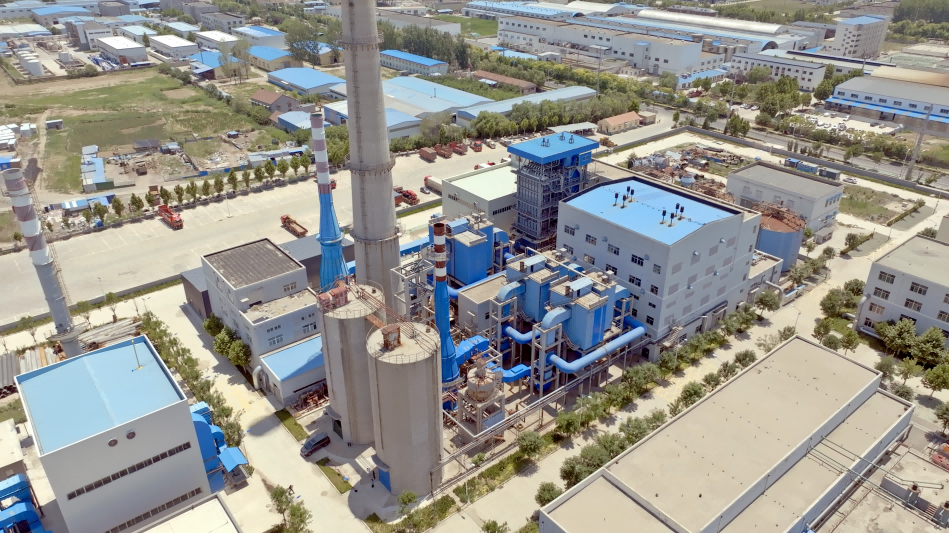
What Key Parameters and Instruments Are Needed for Accurate Measurements?
To evaluate boiler performance and combustion quality, operators and engineers rely on real-time and precise measurements of key process variables. Whether you’re calculating thermal efficiency, emissions compliance, or diagnosing heat losses, the accuracy of the results depends entirely on the quality of the data and instruments used. Poor sensor calibration, incomplete data, or wrong measurement locations can lead to significant errors in boiler diagnostics—leading to inefficient operation, excessive fuel consumption, or failure to meet regulatory limits. A well-instrumented boiler is the foundation of performance optimization.
Accurate measurements of boiler efficiency and combustion quality require key parameters such as fuel flow rate, steam output, flue gas composition (O₂, CO, CO₂), stack temperature, and feedwater enthalpy. These are obtained using precision instruments like steam flowmeters, calorimeters, gas analyzers, thermocouples, and pressure transmitters. Reliable and calibrated sensors, properly installed and monitored, are essential for calculating efficiency using both the Direct and Indirect Methods and for ensuring stable and safe boiler operation.
Good data enables good decisions. In boiler optimization, measurement is the master key.
Accurate boiler efficiency and performance measurements depend on high-quality instrumentation and critical parameter monitoring.True
Key variables like steam output, fuel input, flue gas composition, and temperatures must be measured precisely to enable valid performance assessment.
🔍 Key Parameters Required for Efficiency and Combustion Analysis
Parameter | Why It’s Important | Use in Efficiency Method |
---|---|---|
Steam Flow Rate (kg/hr) | Measures output energy | Direct Method |
Steam Pressure & Temp | Used to determine steam enthalpy | Direct Method |
Feedwater Temperature | Determines feedwater enthalpy | Direct & Indirect Method |
Fuel Consumption Rate | Tracks input energy from solid, liquid, or gas fuel | Direct Method |
Fuel Calorific Value (GCV/NCV) | Quantifies energy content of the fuel | Direct & Indirect Method |
Flue Gas Temperature | Indicates heat loss through exhaust gases | Indirect Method |
O₂ in Flue Gas (%) | Shows excess air and combustion completeness | Indirect Method |
CO/CO₂ in Flue Gas | Indicates incomplete combustion | Indirect Method |
Ash Content & UBC (%) | Reveals combustion quality and unburned fuel losses | Indirect Method |
Ambient Air Temp & Humidity | Used in accurate flue gas loss calculation | Indirect Method |
→ These parameters must be logged continuously or sampled frequently to ensure reliable boiler monitoring.
🛠 Essential Instruments for Accurate Measurement
Instrument / Sensor | Function | Installation Point |
---|---|---|
Steam Flowmeter (Turbine/DP/Ultrasonic) | Measures steam output rate | Steam header |
Thermocouples / RTDs | Measure temperature of steam, flue gas, feedwater | Steam drum, stack, economizer |
Pressure Transmitters | For steam pressure and feedwater inlet pressure | Steam drum, feed lines |
Fuel Flow Meters | Measures gas or oil input (mass or volume-based) | Fuel supply lines |
Coal/Biomass Belt Weighers | Measures solid fuel feed rate | Under feeders or conveyors |
Gas Analyzers (O₂, CO, CO₂, NOx) | Monitors flue gas composition | Flue gas duct (post-combustion) |
Stack Thermometer | Monitors exhaust gas temperature | Chimney or outlet duct |
Water Meters / Flow Transmitters | Measures make-up and blowdown water flow | Feedwater and return lines |
UBC Analyzer / Ash Sampler | Estimates unburned carbon in fly ash | Ash hopper or dust collector |
→ Instrument calibration and proper maintenance are crucial for accuracy.
📊 Example: Instrument Configuration for a 50 TPH Biomass Boiler
Parameter | Value | Measured By |
---|---|---|
Steam Flow Rate | 48,300 kg/hr | Ultrasonic Steam Flowmeter |
Steam Pressure / Temp | 62 bar / 475°C | Pressure transmitter + RTD |
Fuel Input (Wood Chips) | 6,200 kg/hr | Belt Weigher |
GCV of Fuel | 3,200 kcal/kg | Lab-tested proximate analysis |
Flue Gas Temp (Stack) | 235°C | Thermocouple (K-Type) |
O₂ in Flue Gas | 4.1% | Zirconia Oxygen Analyzer |
CO in Flue Gas | 95 ppm | NDIR Gas Analyzer |
Feedwater Temperature | 85°C | RTD + SCADA logging |
→ This setup supports both Direct and Indirect efficiency calculations.
🧪 Calibration and Accuracy Requirements
Instrument | Recommended Calibration Frequency | Accuracy Range Required |
---|---|---|
Steam Flowmeters | Every 6–12 months | ±1–2% of reading |
O₂ and CO Gas Analyzers | Monthly calibration or auto-cal | ±0.5% O₂, ±5 ppm CO |
Fuel Flow Sensors | Every 3–6 months | ±1% for gas, ±3% for solid |
Temperature Sensors | Every 12 months | ±0.2–0.5°C |
Pressure Transmitters | Every 12 months | ±0.25% FS |
→ Inaccurate instruments lead to misleading efficiency results and incorrect decisions.
📈 Real-World Impact: Instrument Accuracy on Efficiency Calculation
Scenario | Efficiency Reported | True Efficiency | Cause of Error |
---|---|---|---|
Steam meter over-reading 5% | 87.5% | 83.0% | Calibration drift |
Fuel GCV overestimated by 10% | 85.0% | 77.5% | Old or unverified lab data |
O₂ sensor reading stuck at 3.5% | 84.2% | 80.1% | Failed flue gas sensor |
→ Errors in a single instrument can distort system-wide performance metrics.
🔧 Best Practices for Measurement Accuracy
Practice | Benefit |
---|---|
Routine Calibration | Maintains data integrity |
Instrument Redundancy (dual sensors) | Avoids false readings from drift or failure |
Automated SCADA/PLC Data Logging | Enables continuous trend analysis |
Operator Training in Instrument Use | Ensures proper use and interpretation |
Cross-check with energy balances | Validates calculated vs. observed efficiency |
→ Accuracy is not just hardware—it’s a system of procedures and people.
In conclusion, accurate boiler efficiency and combustion performance measurement relies on monitoring key parameters with high-precision instruments installed, calibrated, and managed correctly. From steam flow to flue gas composition, every data point contributes to an accurate picture of your boiler’s health and efficiency. With the right tools and discipline, plant teams can maximize output, minimize fuel costs, and maintain emissions compliance. In boiler operation, precision isn’t optional—it’s the difference between efficiency and excess.
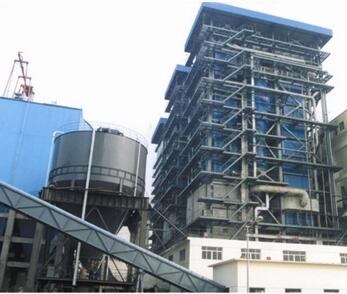
How Do Fuel Type, Excess Air, and Flue Gas Temperatures Affect Efficiency Results?
Boiler efficiency is a dynamic metric—it doesn’t remain constant and is influenced by many operational parameters. Among these, fuel type, excess air level, and flue gas temperature are three of the most significant factors. Each directly impacts how completely combustion occurs, how well heat is transferred, and how much energy escapes through the stack. Incorrect combinations can lead to unburned fuel, excessive emissions, and wasted thermal energy, even if the boiler is mechanically sound. Understanding how these variables interact is essential for tuning your system toward maximum energy conversion and minimal losses.
Fuel type, excess air ratio, and flue gas temperature critically affect boiler efficiency. Fuels with high ash or moisture content reduce combustion quality and increase heat losses. Excess air improves combustion up to a point but too much dilutes flame temperature and increases stack losses. High flue gas temperature indicates poor heat recovery and fouling, lowering thermal efficiency. Efficient operation requires selecting the right fuel, optimizing air supply, and maintaining clean heat exchange surfaces to minimize energy losses and maximize fuel utilization.
Together, these factors determine whether your boiler performs at peak—or falls short.
Fuel type, excess air, and flue gas temperature significantly influence boiler efficiency.True
These parameters determine combustion quality and how much usable energy is retained or lost in the process.
🔍 1. Fuel Type and Its Impact on Efficiency
Fuel Characteristic | Efficiency Effect |
---|---|
Calorific Value (CV) | Higher CV = more energy per kg of fuel |
Moisture Content | Higher moisture absorbs combustion heat → efficiency ↓ |
Ash Content | High ash leads to fouling → reduces heat transfer |
Volatile Matter | Affects ignition, flame stability, and CO formation |
Fuel Type | Moisture (%) | Ash (%) | CV (kcal/kg) | Efficiency Range (%) |
---|---|---|---|---|
Natural Gas | 0 | 0 | ~9,000 | 88–92 |
Coal (Bituminous) | 8–12 | 15–25 | 4,000–6,000 | 84–89 |
Biomass (Wood) | 10–50 | 1–5 | 2,500–4,000 | 70–85 |
RDF | 15–30 | 15–20 | 3,000–4,000 | 68–82 |
→ Lower moisture and ash fuels yield better combustion and higher efficiency.
🔍 2. Excess Air Ratio and Its Efficiency Tradeoff
Excess Air (%) | O₂ (%) in Flue Gas | Combustion Effect | Efficiency Effect |
---|---|---|---|
0–5 | <1.5% | Risk of incomplete combustion (CO ↑) | Efficiency ↓ (CO losses) |
10–20 | 2.5–4.5% | Ideal range for full combustion | ✅ Efficiency Optimized |
25–30 | >5.5% | Flame cooling, more flue gas volume | Stack loss ↑ → Efficiency ↓ |
>35 | >7.5% | Severe dilution of flame temperature | Significant Efficiency ↓ |
→ Excess air must be balanced—not minimized—based on fuel reactivity.
🔍 3. Flue Gas Temperature and Heat Recovery
Flue Gas Temp (°C) | System Condition | Efficiency Impact |
---|---|---|
160–190 | Clean heat surfaces, low excess air | ✅ Optimal heat recovery |
200–230 | Moderate fouling or high excess air | Efficiency ↓ 2–4% |
240–270 | Poor heat transfer or over-firing | Efficiency ↓ 5–8% |
>280 | Severe fouling or tuning errors | Efficiency ↓ ≥10% |
→ Flue gas temperature is a direct indicator of heat loss.
📊 Real-World Example – Effect of Fuel and Air on Efficiency
Condition | Flue Temp (°C) | O₂ (%) | CO (ppm) | Efficiency (%) |
---|---|---|---|---|
Dry wood chips, tuned air | 185 | 3.8 | 60 | 85.6 |
Wet biomass, excess air 30% | 250 | 6.5 | 140 | 73.8 |
RDF, poor combustion air distribution | 270 | 7.2 | 280 | 68.5 |
→ Higher fuel quality + optimized air = 17% gain in efficiency over poor conditions.
🛠 Optimizing These Parameters Together
Parameter | Action for High Efficiency |
---|---|
Fuel Type | Use dry, low-ash, high-CV fuel or pre-dry biomass |
Excess Air | Tune O₂ to 3.0–4.5%, use O₂ trim systems |
Flue Gas Temp | Clean tubes, optimize heat recovery, reduce fouling |
→ Combine control strategies for maximum synergistic benefit.
🧪 Case Study – Coal Boiler Retuned for Efficiency
Initial Issues:
Fuel: Bituminous coal (22% ash, CV 4,200 kcal/kg)
O₂ = 6.8%, CO = 220 ppm
Flue gas temp = 265°C
Efficiency = 76.3%
Actions Taken:
Adjusted excess air to target O₂ of 4.0%
Cleaned superheater and economizer
Installed automatic O₂/CO monitoring
Results:
CO = 80 ppm
Flue temp = 190°C
Efficiency = 86.1% (+9.8%)
📈 Efficiency Loss per 10°C Increase in Flue Gas Temp
Fuel Type | Approx. Efficiency Drop (%) |
---|---|
Natural Gas | 0.5–0.7% |
Coal | 0.8–1.0% |
Biomass | 0.9–1.2% |
→ Fouling that adds 50°C = 5–6% loss in many boilers.
In conclusion, boiler efficiency is deeply influenced by the combination of fuel type, excess air ratio, and flue gas temperature. Each factor individually affects combustion quality and heat loss, but together they define the system’s energy performance. For the highest efficiency, operators must ensure consistent, dry fuel, use precise air control, and keep heat transfer surfaces clean and optimized. In energy systems, efficiency isn’t just about technology—it’s about mastering the variables that drive it.
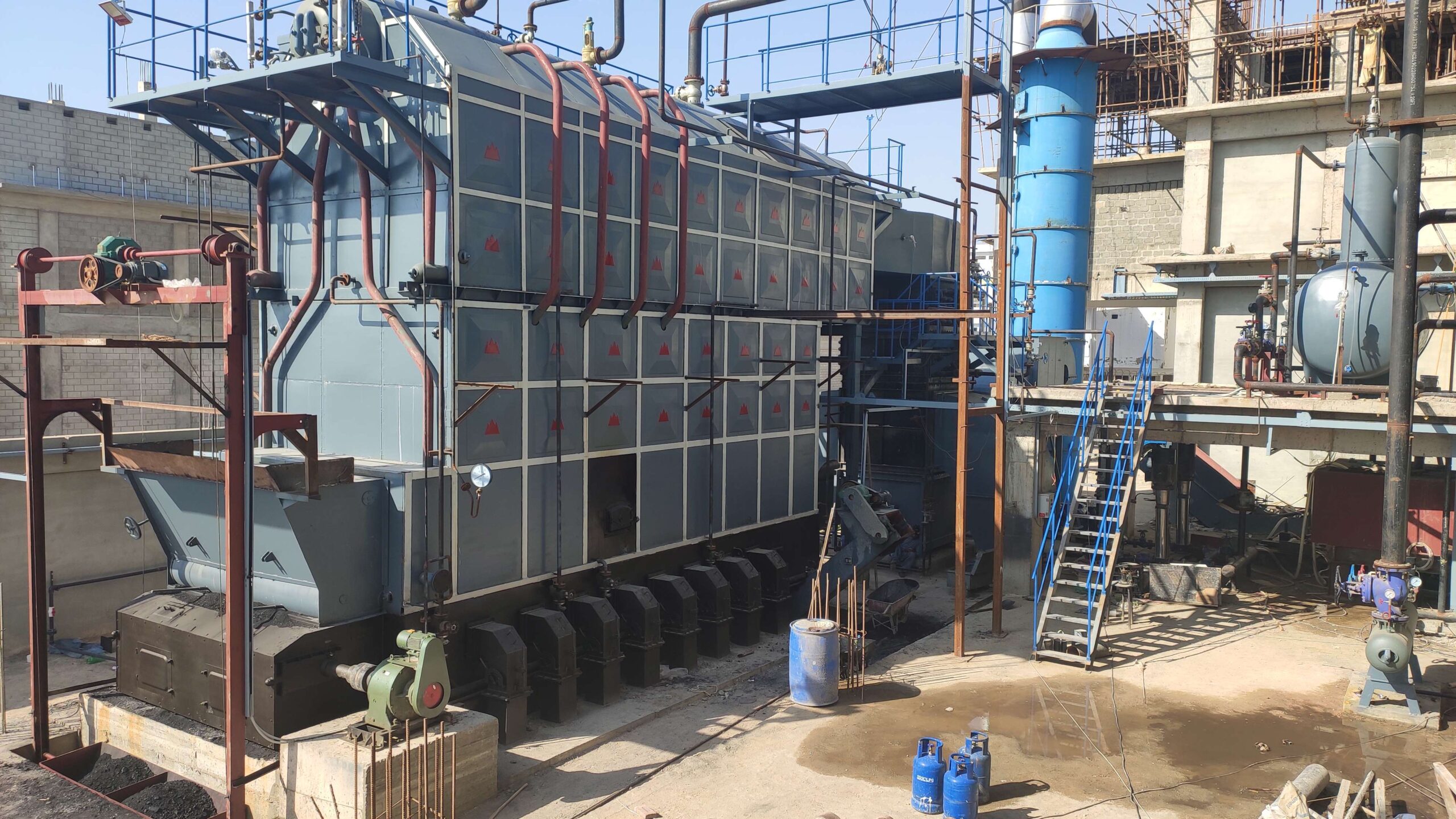
How Can Thermal Efficiency Data Help Improve Power Plant Output and Fuel Economy?
Power plants operate on narrow economic margins where even a 1–2% shift in performance can mean millions in cost or revenue differences over time. In this high-stakes environment, thermal efficiency data serves as both a diagnostic tool and a strategic compass. When accurately tracked and analyzed, this data reveals inefficiencies, predicts maintenance needs, and supports decisions that increase power output per unit of fuel. Without it, operators are flying blind—burning more fuel than necessary, reducing equipment life, and emitting more pollutants. With it, they gain a quantifiable path to optimization, fuel savings, and sustained profitability.
Thermal efficiency data helps improve power plant output and fuel economy by providing real-time insights into how effectively fuel energy is converted into steam or electricity. Monitoring this data enables operators to detect losses, optimize combustion, adjust air-fuel ratios, schedule predictive maintenance, and benchmark performance. Over time, this leads to improved steam generation, reduced fuel consumption, and lower operating costs. Thermal efficiency tracking transforms raw operational data into actionable strategies for continuous improvement.
Your efficiency data isn’t just a number—it’s the roadmap to operational excellence.
Thermal efficiency data is essential for optimizing power plant output and reducing fuel consumption.True
By identifying performance trends and loss sources, it allows targeted actions that improve energy conversion and reduce waste.
🔍 What Is Thermal Efficiency Data in Power Plants?
Metric | Description |
---|---|
Thermal Efficiency (%) | Measures ratio of energy output to energy input (fuel) |
Steam-to-Fuel Ratio | Kg steam produced per kg of fuel burned |
Heat Rate (kJ/kWh) | Inverse of efficiency; shows energy input per electricity unit |
Boiler Efficiency Logs | Daily/real-time records showing combustion and heat transfer performance |
→ These metrics form the core indicators of boiler and turbine effectiveness.
📏 How Efficiency Data Links to Output and Fuel Economy
Efficiency Metric | Operational Impact |
---|---|
Higher Thermal Efficiency | More steam or electricity from same fuel quantity |
Improved Heat Rate | Lower energy cost per MWh |
Consistent Efficiency | Stable generation and reduced maintenance cost |
Decreasing Efficiency | Early warning of fouling, combustion issues, or leaks |
→ Tracking trends in efficiency helps predict problems before they cost money.
📊 Example – Efficiency Improvement Impact on Fuel and Output
Parameter | Before Optimization | After Optimization |
---|---|---|
Fuel Consumption (TPD) | 600 | 540 |
Steam Output (TPH) | 280 | 290 |
Thermal Efficiency (%) | 76.5 | 84.7 |
Heat Rate (kJ/kWh) | 11,800 | 10,400 |
Annual Fuel Savings | – | ~22,000 tons/year |
→ A modest 8.2% increase in efficiency generated millions in fuel savings.
🧪 Case Study – Real-Time Efficiency Dashboard Integration
Plant: 300 MW Coal-Fired Power Station
Problem: Variable generation output, high fuel cost
Intervention:
Installed real-time boiler efficiency dashboard (Direct + Indirect method)
Integrated steam, fuel, flue gas, and O₂ readings
Used heat rate data to trigger soot blower, O₂ trim, and burner adjustments
Result:
Efficiency rose from 82.6% to 89.1%
Fuel usage per MWh dropped by 8.5%
Improved generation availability by 4.3%
→ Efficiency visibility led to actionable changes across O&M departments.
📈 Operational Actions Triggered by Thermal Efficiency Data
Efficiency Indicator | Corrective Action |
---|---|
Flue Gas Temp ↑ | Soot blowing, inspect fouling in economizer |
O₂ > 6% | Adjust excess air and burner dampers |
CO ↑ / Steam ↓ | Tune combustion or check flame alignment |
Steam-to-Fuel Ratio ↓ | Investigate feedwater, check for leaks or scale |
Ash Content ↑ | Modify grate speed, clean slagging zones |
→ Data makes decisions evidence-based, not guess-based.
🛠 Efficiency Monitoring Tools and Systems
Tool/System | Role in Fuel Economy & Output Optimization |
---|---|
SCADA/PLC-Based Monitoring | Real-time tracking of efficiency variables |
Energy Management Systems (EMS) | Analyze trends, suggest optimizations |
O₂ Trim Control | Automated excess air tuning |
Flue Gas Analyzers | CO, CO₂, O₂ → combustion diagnostics |
Digital Twin Models | Simulate performance based on real input data |
→ These tools convert raw data into strategic decisions.
📋 Efficiency Improvement Strategies Informed by Data
Strategy | Efficiency Data Input Used | Benefit |
---|---|---|
Combustion Optimization | O₂, CO, fuel ratio, steam output | Lower fuel per ton steam |
Maintenance Scheduling | Flue temp, ΔP, steam/fuel ratio trends | Fewer outages, optimized timing |
Heat Recovery Enhancements | Flue gas losses | Higher energy recovery |
Fuel Switching Decisions | CV vs. efficiency outcome | Higher output per fuel unit |
Operator Training | Performance deviation from norm | Consistent efficiency behaviors |
→ Efficiency data is the source code for every power plant improvement.
🔧 Best Practices for Using Thermal Efficiency Data
Practice | Purpose |
---|---|
Daily Efficiency Log Reviews | Spot declining trends early |
Baseline Benchmarking | Set targets based on design vs. actual |
Variance Analysis | Compare shifts in output, fuel, or flue gases |
Real-Time Alarms for Efficiency Losses | Immediate operator response |
Efficiency KPI Integration | Tie staff KPIs to boiler performance |
→ Turn data into accountability and results.
In conclusion, thermal efficiency data empowers power plants to operate smarter, cleaner, and more cost-effectively. By identifying performance issues and opportunities, it enables better decisions on fuel management, output optimization, and maintenance planning. With accurate efficiency monitoring, plants can boost generation without burning more fuel—and that’s the hallmark of a high-performance energy operation. In power generation, what gets measured gets improved—and what gets improved gets profitable.
🔍 Conclusion
Measuring the thermal efficiency of an industrial power plant boiler is essential for achieving peak performance, minimizing fuel consumption, and reducing carbon emissions. Whether using the Direct or Indirect Method, accurate monitoring of heat input and output helps identify system inefficiencies and opportunities for improvement. With consistent measurement and analysis, power plant operators can ensure that their boiler systems deliver maximum energy yield and long-term reliability.
📞 Contact Us
💡 Need support measuring or optimizing your power boiler’s efficiency? Our engineering team provides in-depth performance audits, combustion tuning, and energy optimization solutions for power plant boilers of all sizes.
🔹 Contact us today and start maximizing the energy efficiency of your power plant boiler! ⚡🔥📊
FAQ
What is thermal efficiency in an industrial power plant boiler?
Thermal efficiency is the ratio of the boiler’s useful heat output (typically steam for electricity generation) to the total energy input from fuel combustion. It reflects how effectively the boiler converts fuel energy into usable steam or power.
What methods are used to measure boiler thermal efficiency?
There are two widely accepted methods:
Direct Method – Based on output vs. input energy.
Indirect Method – Based on measuring and subtracting various heat losses from 100%.
These methods are compliant with standards like ASME PTC 4 and ISO 16528.
How does the Direct Method work for power plant boilers?
The Direct Method calculates efficiency using:
Efficiency (%) = (Steam Output × Enthalpy Gain) / (Fuel Input × Calorific Value) × 100
It’s fast and straightforward but doesn’t identify the specific areas of loss.
What is the Indirect Method and why is it more diagnostic?
The Indirect Method calculates efficiency by summing all measurable heat losses—such as flue gas loss, radiation loss, blowdown, moisture in fuel, and unburnt fuel—and subtracting them from 100%.
Efficiency (%) = 100 – (Total Heat Losses)
This approach helps pinpoint inefficiencies in combustion, insulation, and fuel quality.
Why is thermal efficiency monitoring essential in power plant boilers?
Monitoring efficiency improves fuel utilization, lowers CO₂ emissions, reduces operating costs, and enhances plant reliability. It’s also a key metric in energy audits and compliance with environmental regulations and carbon reduction goals.
References
Boiler Efficiency Measurement Techniques – https://www.energy.gov
ASME PTC 4: Fired Steam Generators – https://www.asme.org
Heat Loss Analysis in Power Boilers – https://www.sciencedirect.com
Energy Efficiency in Industrial Boilers – https://www.researchgate.net
Thermal Performance and Auditing Guidelines – https://www.epa.gov
Boiler Optimization in Power Plants – https://www.bioenergyconsult.com
Indirect Method for Large Combustion Systems – https://www.mdpi.com
Real-Time Monitoring of Boiler Efficiency – https://www.automation.com
IEA Boiler Energy Efficiency Recommendations – https://www.iea.org
Fuel Quality and Efficiency in Power Boilers – https://www.energysavingtrust.org.uk
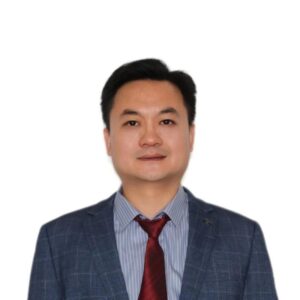