How to Optimize Industrial Coal-Fired Boiler Performance for Lower Operating Costs
Coal-fired boilers remain a cornerstone of energy production in heavy industry, offering high output and fuel flexibility. However, without proper optimization, these systems can become fuel-intensive, emission-heavy, and maintenance-prone, leading to elevated operating costs and environmental penalties. To maintain competitiveness and sustainability, industries must take a proactive, data-driven approach to improve boiler performance while minimizing energy losses and operational expenses.
To optimize an industrial coal-fired boiler for lower operating costs, focus on key strategies such as air-to-fuel ratio control, combustion tuning, efficient ash and slag handling, heat transfer surface cleaning, flue gas heat recovery, and automation. Using real-time data to monitor furnace conditions, excess air levels, and flue gas temperatures enables early detection of inefficiencies. Routine maintenance, better fuel handling, and implementing energy recovery systems like economizers and air preheaters significantly enhance overall efficiency and reduce fuel usage.
Here’s a structured breakdown of how to maximize efficiency and cut costs in coal-fired boiler operations.
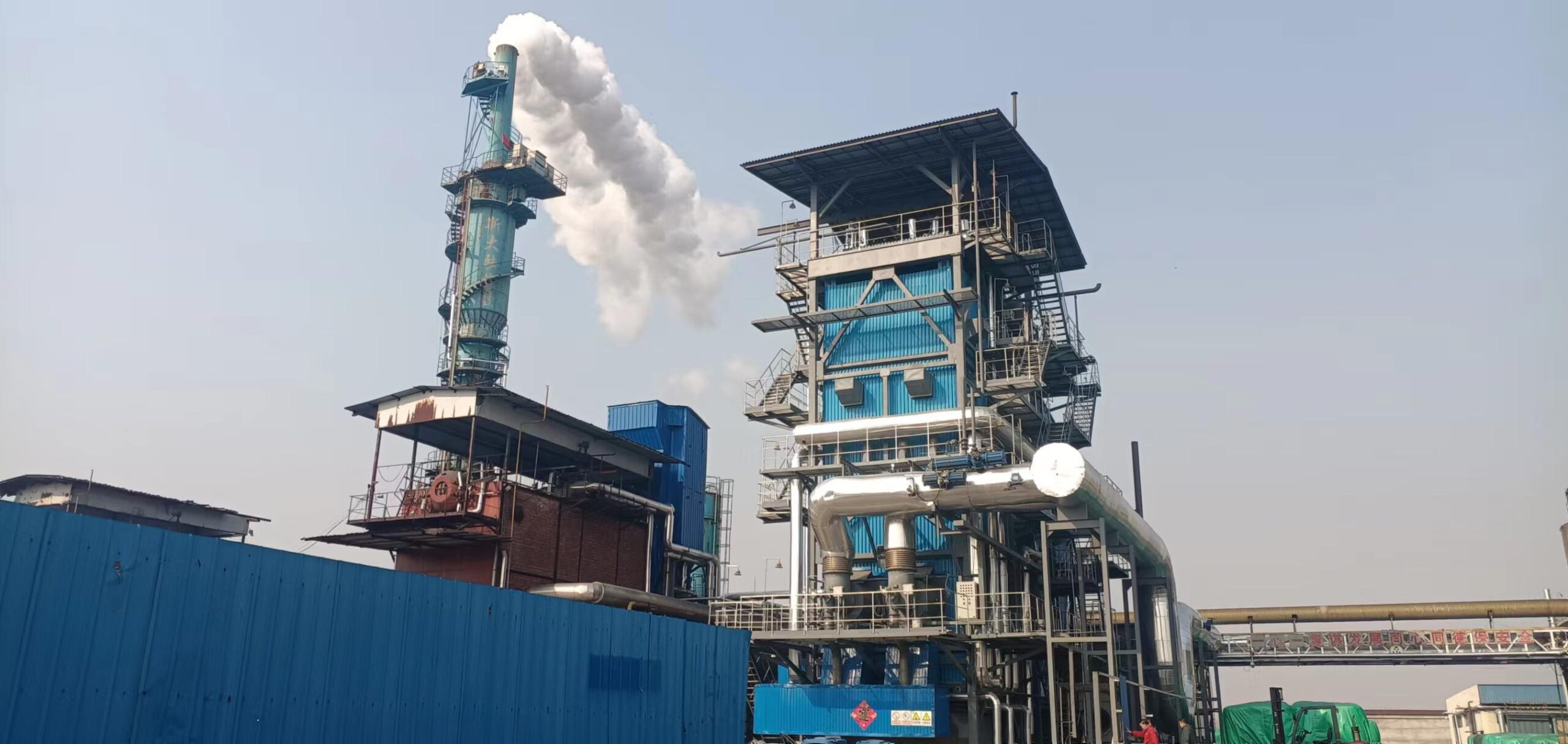
How Does Optimizing the Air-to-Fuel Ratio Improve Combustion Efficiency and Reduce Fuel Waste?
In every combustion system, fuel alone doesn’t create energy—oxygen is equally essential. But not just any amount of oxygen: the air-to-fuel ratio must be precisely controlled to ensure that fuel burns completely, releasing all available energy. If there’s too little air, combustion is incomplete, producing carbon monoxide (CO), unburned hydrocarbons, and soot. If there’s too much air, it dilutes the flame and carries heat away in the flue gas. Both scenarios waste fuel and reduce thermal efficiency. Optimizing the air-to-fuel ratio—using O₂ sensors, flue gas analyzers, and automation—enables boilers to burn cleaner, hotter, and more efficiently.
Optimizing the air-to-fuel ratio improves combustion efficiency by ensuring that the fuel is completely burned using only the necessary amount of air, thereby maximizing heat release while minimizing flue gas losses. With too little air, fuel is wasted through incomplete combustion; with too much air, excess oxygen cools the flame and increases stack losses. Maintaining the optimal ratio—typically 10–20% excess air depending on fuel type—reduces CO emissions, improves flame stability, and saves fuel. Automated trim controls and real-time O₂/CO monitoring help sustain this balance.
Combustion efficiency starts not with more fuel—but with better air control.
Optimizing the air-to-fuel ratio improves combustion efficiency and reduces fuel waste.True
Too little air causes incomplete combustion; too much air increases heat losses. The correct balance maximizes heat output per unit of fuel.
🔍 What Is the Air-to-Fuel Ratio?
Concept | Description |
---|---|
Stoichiometric Ratio | Theoretical minimum air required to completely burn the fuel |
Excess Air (%) | Air supplied above stoichiometric to ensure full combustion |
Flue Gas O₂ (%) | Indicates how much unused oxygen is exiting the stack |
CO Levels (ppm) | Indicator of incomplete combustion due to air/fuel imbalance |
→ In most systems, a controlled excess air range (e.g., 10–25%) is required for full burn.
📏 Ideal Air-to-Fuel Ratios by Fuel Type
Fuel Type | Optimal Excess Air (%) | Target Flue Gas O₂ (%) | Notes |
---|---|---|---|
Natural Gas | 5–10 | 1–2 | Very clean burn, low excess air needed |
Coal | 15–25 | 3.5–5 | Requires more air due to ash and density |
Biomass | 20–30 | 5–6 | Moisture and volatile content need higher air |
Fuel Oil | 10–15 | 2–3 | High energy density, but needs good atomization |
→ These values are not fixed—they should be fine-tuned per boiler system and load.
📊 Combustion Efficiency vs. Air-to-Fuel Ratio
Excess Air (%) | O₂ in Flue Gas (%) | CO Emissions (ppm) | Combustion Efficiency (%) |
---|---|---|---|
0–5 | <1 | >300 | <75% (Incomplete combustion) |
10–20 | 2–4.5 | <100 | ✅ 85–90% (Optimal) |
25–30 | 5–6.5 | <50 | 78–83% (Excess air loss) |
>35 | >7 | <30 | <78% (High stack loss) |
→ The best efficiency occurs at low CO + moderate O₂, indicating complete combustion.
🧪 Case Study – Fuel Savings through Ratio Optimization
System: 20 TPH biomass-fired boiler
Initial Conditions:
Flue O₂ = 6.5%, CO = 35 ppm, Efficiency = 78.1%
Fuel consumption = 6,800 kg/hr
Actions Taken:
Installed flue gas analyzer and O₂/CO control loop
Retuned burners and adjusted secondary air dampers
Target O₂ reduced to 4.1%, CO stabilized at 55 ppm
Results:
Efficiency = 86.4%
Fuel consumption = 5,940 kg/hr
Fuel savings = 860 kg/hr (~12.6%)
Emissions also reduced by 18%
→ Precise air control delivered cleaner burn and lower operating cost.
🛠 How Optimization Reduces Fuel Waste
Air-Fuel Imbalance | Resulting Issue | Fuel Waste Mechanism |
---|---|---|
Too Little Air | Incomplete combustion, CO ↑ | Unburned fuel, lower heat output |
Too Much Air | Flame cooling, flue gas heat ↑ | Heat lost to stack, more fuel needed to compensate |
Variable Air Supply | Flame instability, fluctuating steam | Burner overfire/underfire response |
→ Fuel is wasted either by not burning completely or by losing heat with the flue gas.
🔧 Tools and Techniques for Air-Fuel Optimization
Technology | Role in Optimization |
---|---|
Flue Gas Analyzer (O₂, CO) | Provides real-time combustion data |
O₂ Trim Control System | Automatically adjusts dampers based on O₂ feedback |
SCADA Integration | Displays air-fuel trends and triggers alarms |
Mass Flow Air/Fuel Meters | Ensures consistent ratio at different loads |
Burner Modulation Control | Allows stable operation across turndown range |
→ The best systems combine sensing, control, and automation.
📈 Efficiency Gains Through Proper Air-Fuel Tuning
Improvement Action | Efficiency Gain (%) | Fuel Savings Potential |
---|---|---|
Reduce excess air from 7% → 3.5% | +5–7% | 6–10% |
Eliminate CO peaks through burner tuning | +2–4% | 2–5% |
Auto-adjust dampers with O₂ trim | +3–6% | 3–8% |
Real-time ratio monitoring (SCADA) | +2–4% | 2–6% |
→ Combined, these improvements can deliver 10–15% energy savings.
🚫 Common Pitfalls in Air-Fuel Control
Mistake | Consequence |
---|---|
Manual damper adjustments only | Drift over time; doesn’t respond to load changes |
Ignoring CO data | May appear efficient via O₂, but CO ↑ |
Sensor calibration neglect | Misleads control system, causing imbalance |
One-size-fits-all setting | Fails under different fuels and turndown loads |
→ Optimization must be dynamic, data-driven, and fuel-specific.
In conclusion, optimizing the air-to-fuel ratio is one of the most impactful ways to improve combustion efficiency and reduce fuel waste in industrial boilers. By delivering just the right amount of oxygen for complete combustion without unnecessary excess, you unlock full heat potential from every kilogram or cubic meter of fuel. Combined with real-time monitoring and intelligent control systems, this optimization ensures your boiler burns cleaner, costs less to operate, and performs reliably under all load conditions. In combustion science, the right mix of air is the hidden key to energy efficiency.
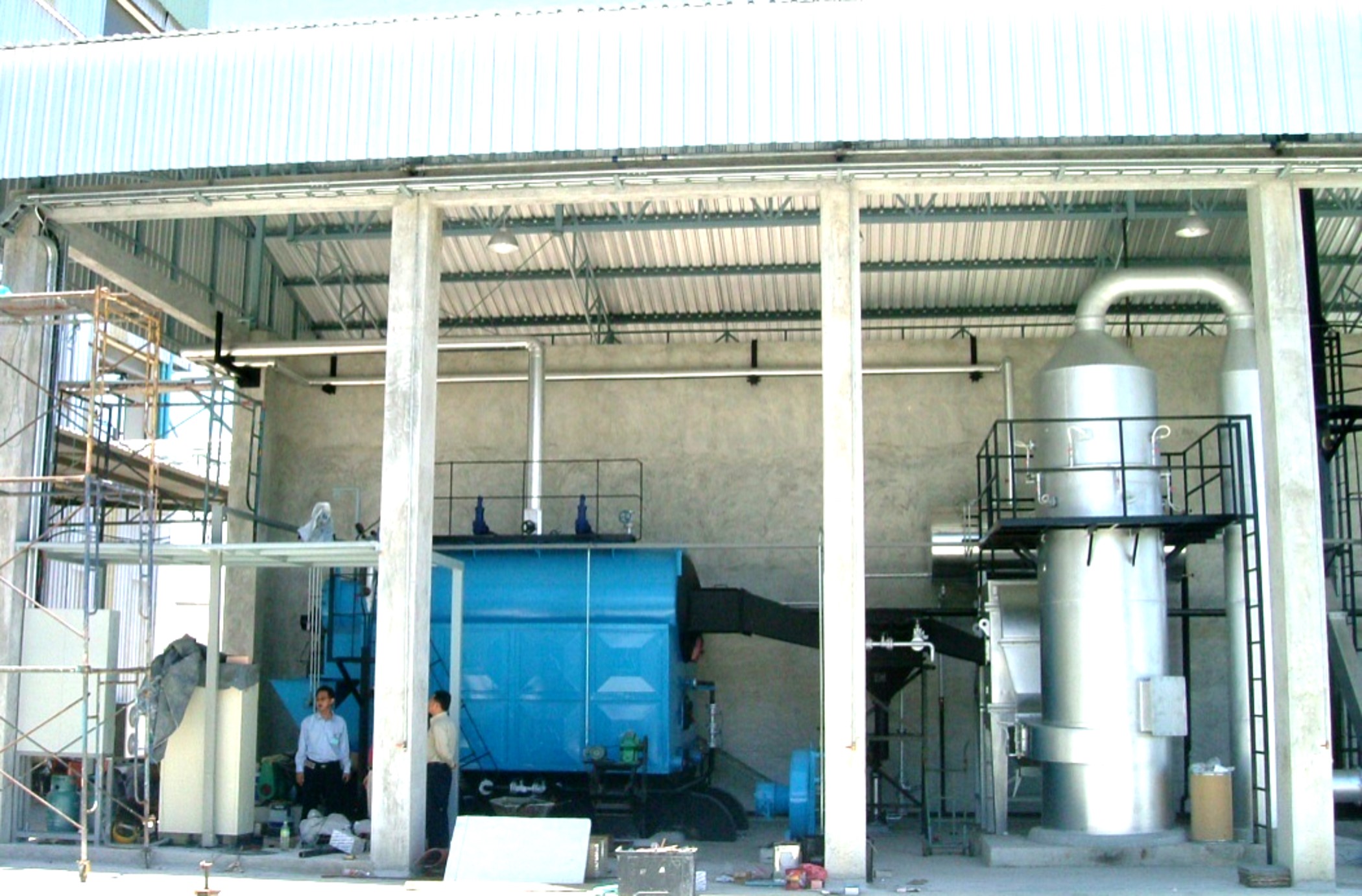
Why Is Soot Blowing and Ash Removal Essential for Maintaining Heat Transfer Performance?
In solid-fuel-fired boilers such as those burning coal, biomass, or petcoke, soot and ash are inevitable byproducts of combustion. Over time, these particles accumulate on heat exchange surfaces—especially in high-temperature zones like superheaters and economizers. This fouling forms an insulating barrier, drastically reducing heat transfer efficiency, increasing flue gas temperatures, and forcing the boiler to burn more fuel to meet the same steam demand. If not addressed regularly, it leads to higher operating costs, boiler derating, emission spikes, and even tube damage. That’s why systematic soot blowing and ash removal are essential maintenance practices in high-performance boiler operations.
Soot blowing and ash removal are essential for maintaining heat transfer performance because they eliminate insulating deposits from heat exchanger surfaces that hinder thermal conductivity. Soot buildup on the superheater, economizer, or air preheater increases flue gas exit temperatures, reduces steam generation efficiency, and requires more fuel to compensate for the loss. Regular cleaning through mechanical or steam soot blowers, rapping systems, or ash conveyors restores optimal heat exchange, reduces fuel consumption, and prevents overheating or pressure instability.
When soot builds up, efficiency burns down.
Soot blowing and ash removal are critical for maintaining boiler heat transfer performance.True
Soot and ash act as insulating layers, increasing flue gas temperatures and reducing thermal efficiency. Regular removal maintains optimal heat exchange.
🔍 Where Does Soot and Ash Accumulate?
Component | Temperature Zone | Fouling Material | Impact on Performance |
---|---|---|---|
Superheater Tubes | 800–1100°C | Fine soot, sticky ash | Heat flux reduction, overheating |
Economizer | 200–400°C | Dry ash, sintered layers | Reduced feedwater heating, backpressure |
Air Preheater | 150–250°C | Dust, acidic condensates | Lower combustion air temps, corrosion |
Furnace Walls | 900–1300°C | Slagging, molten ash | Tube corrosion, poor flame shape |
→ These fouling layers act as thermal insulators, degrading performance.
📏 How Fouling Affects Heat Transfer and Efficiency
Fouling Thickness (mm) | Flue Gas Temp ↑ (°C) | Efficiency Loss (%) | Fuel Consumption ↑ (%) |
---|---|---|---|
0.1 mm | 10–15 | ~2 | ~2–3 |
0.5 mm | 25–40 | ~5–7 | ~6–8 |
1.0 mm | 50+ | >10 | >10–12 |
→ Even a thin layer of soot blocks a large percentage of heat transfer.
🧪 Case Study – Soot Blowing in a Biomass Boiler
System: 25 TPH wood chip-fired boiler
Symptoms: Flue gas temp increased from 185°C to 260°C
Inspection Findings:
0.8 mm ash buildup on economizer and air preheater
Steam production down 9%, CO up 45 ppm
Action Taken:
Performed soot blowing with retractable steam blowers
Manually cleaned economizer inlet section
Activated fly ash conveyor and hopper evacuation system
Results:
Flue gas temp restored to 190°C
Efficiency improved from 77.3% → 85.6%
Steam output recovered to full load
CO down to <40 ppm
→ Regular cleaning prevented permanent derating and reduced fuel costs.
📊 Common Fouling Behavior by Fuel Type
Fuel Type | Ash Content (%) | Fouling Risk | Recommended Cleaning Frequency |
---|---|---|---|
Bituminous Coal | 10–25 | Moderate–High | Daily soot blowing, monthly manual |
Rice Husk | 15–20 | High | Hourly rapping or air blast |
Wood Chips | 1–4 | Moderate | Daily mechanical blower |
Refuse-Derived Fuel (RDF) | 20–30 | Very High | Continuous fly ash evacuation |
→ High-ash, sticky fuels require more aggressive cleaning routines.
🔧 Soot Blowing and Ash Removal Technologies
System | Description | Best Used In |
---|---|---|
Steam Soot Blowers | Blasts high-pressure steam across heat exchanger tubes | Superheater, economizer |
Pneumatic/Air Soot Blowers | Compressed air used for lower-temp surfaces | Economizer, APH |
Retractable Lance Blowers | Programmable, targeted blowing for heavy fouling zones | Biomass and high-ash fuels |
Mechanical Rapping Systems | Vibrates surfaces to dislodge ash | Cyclone walls, economizer |
Ash Screw Conveyors | Transports collected ash to hoppers for disposal | Bottom ash, ESP ash handling |
→ Proper selection and timing of blowers ensures efficiency with minimal wear.
🛠 Best Practices for Heat Transfer Surface Maintenance
Practice | Efficiency Impact |
---|---|
Automate soot blowing based on flue gas ΔT | Cleans only when needed = saves steam/air |
Log fouling trends per fuel batch | Adjust cleaning frequency accordingly |
Inspect surfaces during shutdowns | Detects long-term slagging or corrosion |
Monitor stack temperature daily | First indicator of fouling |
Clean air preheater before acid dewpoint reached | Prevents corrosion and fouling cycle |
→ Maintenance driven by data and inspection yields longer uptime.
📈 Benefits of Routine Soot Blowing and Ash Removal
Benefit | How It Improves Heat Transfer and Efficiency |
---|---|
Lower Flue Gas Temperature | Less heat leaves through stack |
Improved Steam Generation | More energy transferred to water |
Reduced Fuel Consumption | Less fuel needed to meet thermal demand |
Lower CO and NOx Emissions | Stable flame and complete combustion |
Longer Tube Life | Prevents localized overheating |
→ Clean tubes = hotter water, cooler stack, better ROI.
In conclusion, soot blowing and ash removal are non-negotiable for maintaining efficient heat transfer and reliable operation in industrial boilers. Without regular cleaning, ash acts as an insulator that increases flue gas temperatures, reduces energy output, and forces the boiler to burn more fuel to compensate. Automated and manual cleaning systems—combined with data-driven scheduling—ensure that boilers run clean, hot, and efficient. In the world of thermal energy, a clean surface is the most efficient surface.
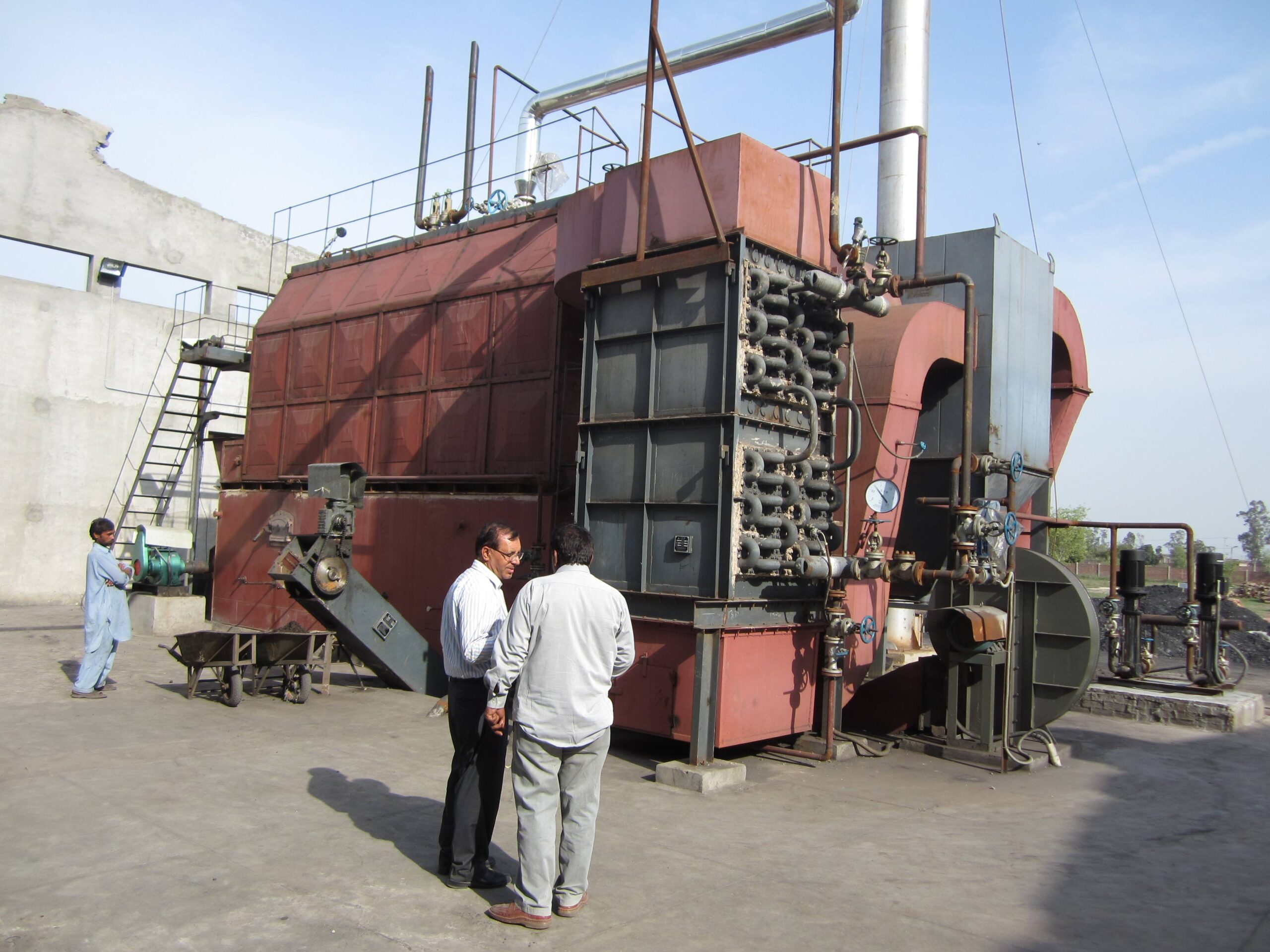
How Can Combustion Tuning and Flame Monitoring Reduce Unburned Carbon and Emissions?
In solid and liquid fuel combustion systems, unburned carbon (UBC)—appearing as carbon in fly ash or soot—is a direct result of incomplete combustion. It signifies wasted fuel, lost efficiency, and higher emissions, especially CO and particulate matter. These losses are often caused by poor burner alignment, fuel maldistribution, unstable flame patterns, or drift in combustion air settings. Combustion tuning and flame monitoring technologies correct these problems in real time, ensuring that every unit of fuel is burned completely, minimizing losses and environmental impact. These practices not only improve thermal performance but also help meet increasingly strict emissions regulations.
Combustion tuning and flame monitoring reduce unburned carbon and emissions by ensuring stable, complete combustion through precise control of fuel-air mixing, flame shape, ignition timing, and combustion zone temperatures. Tuning adjusts burner parameters to optimize flame characteristics, while flame monitoring detects poor combustion zones, misfiring, or instability. This reduces unburned carbon in ash, lowers CO and particulate emissions, and improves boiler efficiency. Automated controls based on flame and flue gas sensors help maintain these conditions continuously, even under load swings or fuel changes.
In combustion, you don’t manage what you burn—you manage how you burn it.
Combustion tuning and flame monitoring reduce unburned carbon and emissions by improving fuel burnout and flame stability.True
Precise burner adjustment and real-time monitoring ensure complete combustion, minimizing CO, soot, and fuel loss.
🔍 What Causes Unburned Carbon and Excess Emissions?
Root Cause | Effect on Combustion | Resulting Emissions / Losses |
---|---|---|
Poor Burner Alignment | Uneven flame, cold spots | Incomplete fuel burn → CO ↑, UBC ↑ |
Incorrect Air-Fuel Ratio | Too rich = CO ↑; too lean = flameout risk | Inefficient combustion, NOx ↑ or CO ↑ |
Flame Instability | Flickering, impingement, misfire | Hot spots, soot, UBC, CO |
Fuel Particle Size Variability | Irregular burnout, delayed ignition | Ash carbon ↑, efficiency ↓ |
Low Combustion Temp | Slow reaction kinetics | CO ↑, unburned hydrocarbons ↑ |
→ These problems are best solved through tuning + real-time diagnostics.
📏 Targets for Combustion Optimization
Metric | Optimal Range | Performance Indicator |
---|---|---|
O₂ in Flue Gas (%) | 3.0–5.0 | Indicates excess air and burn completeness |
CO (ppm) | <100 (gas/biomass); <200 (coal) | High = poor burn, UBC ↑ |
Unburned Carbon (UBC % in ash) | <3.0% | Lower = more complete combustion |
Flame Stability Index | >0.9 (ideal) | Near 1 = stable flame detected |
→ Deviations from these targets often signal poor tuning or burner wear.
🧪 Case Study – Combustion Tuning in a 40 TPH Coal Boiler
Initial Condition:
UBC = 5.8% (fly ash), CO = 230 ppm
Flame scanners detected unstable pattern on burner #3
Efficiency = 77.5%
Actions Taken:
Tuned primary and secondary air dampers
Recalibrated burner tilt and overfire air ports
Synced flame monitoring with O₂/CO loop
Post-Tuning Results:
UBC reduced to 2.1%, CO down to 85 ppm
Flue gas temp reduced by 45°C
Efficiency improved to 85.1%
Emissions compliance achieved without retrofit
→ Tuning plus real-time flame feedback restored combustion quality.
📊 Impact of Tuning on Combustion Performance
Tuning Level | UBC (%) | CO (ppm) | Efficiency (%) | Fuel Use Impact |
---|---|---|---|---|
Untuned | 5.0–6.5 | >250 | 74–78 | Wasteful |
Moderately Tuned | 3.0–4.5 | 120–200 | 79–83 | Improved |
Fully Tuned + Monitored | <2.5 | <100 | 85–89 | Optimal |
→ Even small tuning efforts yield big gains in carbon control and cost savings.
🔧 Combustion Tuning Techniques
Tuning Action | Objective |
---|---|
Burner Tip Inspection and Cleaning | Maintains consistent spray and ignition |
Air Damper Balancing | Ensures even airflow across burner rows |
Overfire Air (OFA) Adjustment | Reduces NOx without causing CO rise |
Fuel Feed Calibration | Ensures steady flow and correct size feed |
Flame Visualization (IR Cameras) | Detects hotspots, misalignment, flame-out |
→ Tuning is not a one-time task—it’s a continuous adjustment process.
🛠 Flame Monitoring Tools for Emission Reduction
Monitoring Tool | Function |
---|---|
IR Flame Scanners | Detect flame presence, size, shape |
Flame Cameras (UV/IR) | Visualize flame zones in real time |
CO/O₂ Analyzers | Validate burn completeness, detect drift |
Combustion Optimization Software | Syncs sensors and controllers |
Ash UBC Analyzers | Measures carbon content in fly ash |
→ Integrated flame + flue gas data closes the feedback loop for tuning.
📈 Emissions Benefits of Tuning and Flame Monitoring
Benefit | Result |
---|---|
Lower CO Emissions | More complete combustion |
Reduced Particulate Matter (PM) | Less soot and carbon carryover |
Stable NOx Output | Controlled burn zone temp and airflow |
Improved Ash Quality | Lower UBC → better cement/feedstock value |
Fewer Shutdowns | Flameout detection → proactive correction |
→ Cleaner combustion = lower emissions + better byproducts.
🔄 Best Practices for Sustained Low UBC and Emissions
Practice | Frequency | Why It Matters |
---|---|---|
Quarterly Burner Tuning | Quarterly | Matches air/fuel balance to real conditions |
Daily Flame Pattern Monitoring | Daily | Early detection of drift or instability |
Monthly Analyzer Calibration | Monthly | Ensures O₂/CO readings remain accurate |
Ash Sampling for UBC | Weekly | Tracks combustion completeness |
Update Tuning for New Fuel Types | On fuel change | Adjusts air profile to new volatility |
→ Preventive tuning is cheaper than corrective downtime.
In conclusion, combustion tuning and flame monitoring are essential tools for minimizing unburned carbon and emissions while improving boiler efficiency. By fine-tuning air-fuel ratios, burner alignment, and flame zones—and reinforcing this with sensor-based feedback—operators can eliminate invisible energy waste, achieve compliance, and lower operational costs. In modern combustion systems, what you don’t burn cleanly, you pay for in emissions and inefficiency.
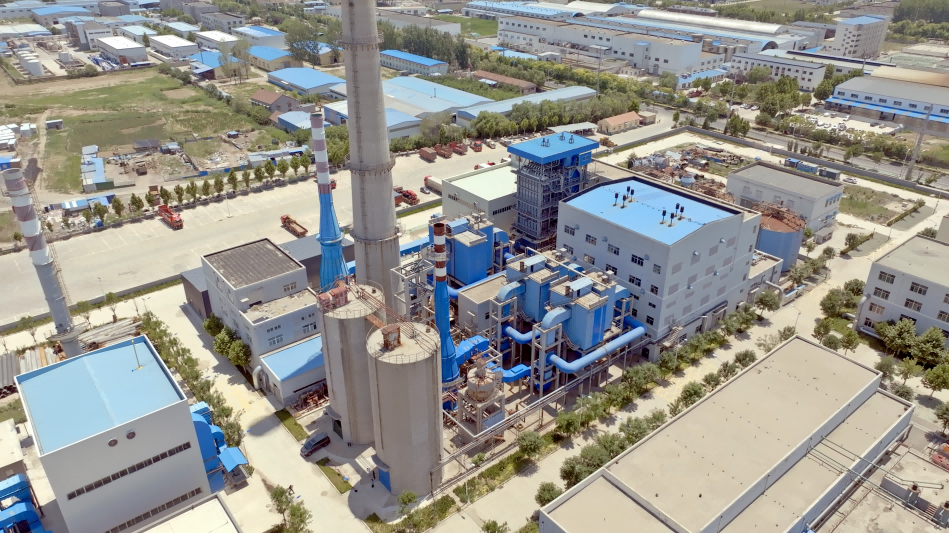
What Role Does Flue Gas Heat Recovery (Economizers, Air Preheaters) Play in Lowering Costs?
In most industrial boilers, a significant portion of the heat generated during combustion escapes with the flue gas. Depending on the fuel and system, 10–30% of input energy may leave through the stack—energy that was paid for but not used. Flue gas heat recovery systems like economizers and air preheaters reclaim this waste heat and return it to the cycle by preheating feedwater or combustion air. This process reduces the fuel required to generate steam or hot water, improves thermal efficiency by up to 10%, and lowers emissions. As a result, these systems directly reduce operational fuel costs and total cost of ownership.
Flue gas heat recovery systems such as economizers and air preheaters reduce costs by capturing thermal energy from exhaust gases and transferring it to feedwater or combustion air, decreasing the fuel required for steam generation. Economizers improve boiler efficiency by 4–7% by preheating incoming water, while air preheaters raise combustion air temperature, enhancing flame stability and reducing fuel demand. These systems significantly cut fuel costs, improve thermal balance, and reduce CO₂ emissions, making them essential for energy-efficient boiler operation.
In thermal systems, recovering what you’ve already paid to heat is the key to saving.
Flue gas heat recovery systems reduce boiler operating costs by reclaiming energy from exhaust gases and lowering fuel consumption.True
By preheating feedwater or combustion air, less fuel is needed to reach required temperatures, improving efficiency.
🔍 What Are Economizers and Air Preheaters?
Component | Function | Energy Transfer Target |
---|---|---|
Economizer | Transfers flue gas heat to boiler feedwater | Feedwater (pre-boil) |
Air Preheater | Transfers flue gas heat to combustion air | Burner inlet air |
Condensing Economizer | Recovers latent heat from moisture in flue gas | Feedwater, return condensate |
→ These devices transform flue gas from waste into a usable energy source.
📏 Typical Efficiency Gains from Heat Recovery
Recovery System | Efficiency Increase (%) | Fuel Savings Potential (%) |
---|---|---|
Standard Economizer | 4–7% | 5–10% |
Air Preheater | 2–5% | 3–7% |
Condensing Economizer | 8–12% | 10–15% |
→ The combined use of economizers and air preheaters can cut annual fuel use significantly.
🧪 Case Study – Economizer Retrofit in a 20 TPH Gas Boiler
Problem: Stack temp = 245°C, feedwater entering at 80°C
Solution: Installed finned-tube economizer
Post-Retrofit:
Stack temp reduced to 170°C
Feedwater preheated to 135°C
Thermal efficiency increased from 79.6% to 87.8%
Fuel savings: ~92,000 Nm³/year (~11% reduction)
ROI achieved in <18 months
→ Economizer investment converted waste heat into cost savings.
📊 Heat Recovery Performance by Application
System Size | Flue Gas Temp Before (°C) | After Recovery (°C) | Efficiency Improvement (%) | Fuel Cost Reduction (%) |
---|---|---|---|---|
15 TPH Biomass | 240 | 165 | +6.5% | ~8–10% |
30 TPH Coal | 255 | 175 | +7.8% | ~10–12% |
25 TPH Gas-Fired | 230 | 160 | +8.2% | ~9–11% |
→ Lower flue gas exit temperature = higher retained thermal energy.
🔧 Technical Role of Each Component
Component | Benefit | Location |
---|---|---|
Economizer | Reduces steam generator duty by heating feedwater | Between boiler and stack |
Air Preheater | Raises combustion air temp → improves flame quality | Before burner or air duct intake |
Condensing HX | Captures latent + sensible heat → feeds low-temp return | After economizer (if used) |
→ Optimizing flue gas cooling recovers both sensible and latent energy.
🛠 Best Practices for Efficient Heat Recovery
Practice | Reason & Impact |
---|---|
Match heat exchanger to flue gas volume | Prevents under-recovery or pressure drop |
Use corrosion-resistant materials | Especially important for condensing systems |
Monitor ΔT across economizer | Detects fouling or underperformance |
Clean heat exchanger surfaces | Prevents insulating ash or soot layer formation |
Log stack temperature trends | Early indicator of recovery performance drop |
→ Maintenance keeps recovery systems running at designed efficiency.
📈 Annual Cost Savings from Heat Recovery (Example)
Boiler Size | Fuel Type | Fuel Cost ($/year) | Post-Recovery Savings (%) | Annual Cost Savings ($) |
---|---|---|---|---|
15 TPH | Biomass | $360,000 | 10% | $36,000 |
20 TPH | Natural Gas | $780,000 | 12% | $93,600 |
30 TPH | Coal | $950,000 | 9% | $85,500 |
→ These savings compound annually, improving ROI and operational margin.
⚠ Risks of Skipping Heat Recovery
Problem | Consequence |
---|---|
High Flue Gas Exit Temp | Lost energy → lower efficiency |
Oversized Burner Loads | More fuel required to achieve steam setpoints |
Increased CO₂ Emissions | Higher fuel use = higher carbon output |
Unstable Combustion Air Temp | Flame instability and efficiency loss |
→ Ignoring recovery burns more fuel, more money, and more carbon.
In conclusion, economizers and air preheaters are essential tools for cutting fuel costs and increasing boiler efficiency by recovering heat that would otherwise be lost. By transferring waste heat from flue gas to feedwater and combustion air, they reduce energy input requirements and operational expenses. Their impact is especially significant in high-load or fuel-intensive systems, where even a few degrees of recovered heat translate into thousands of dollars in annual savings. In thermal energy systems, the cheapest kilojoule is the one you recover.
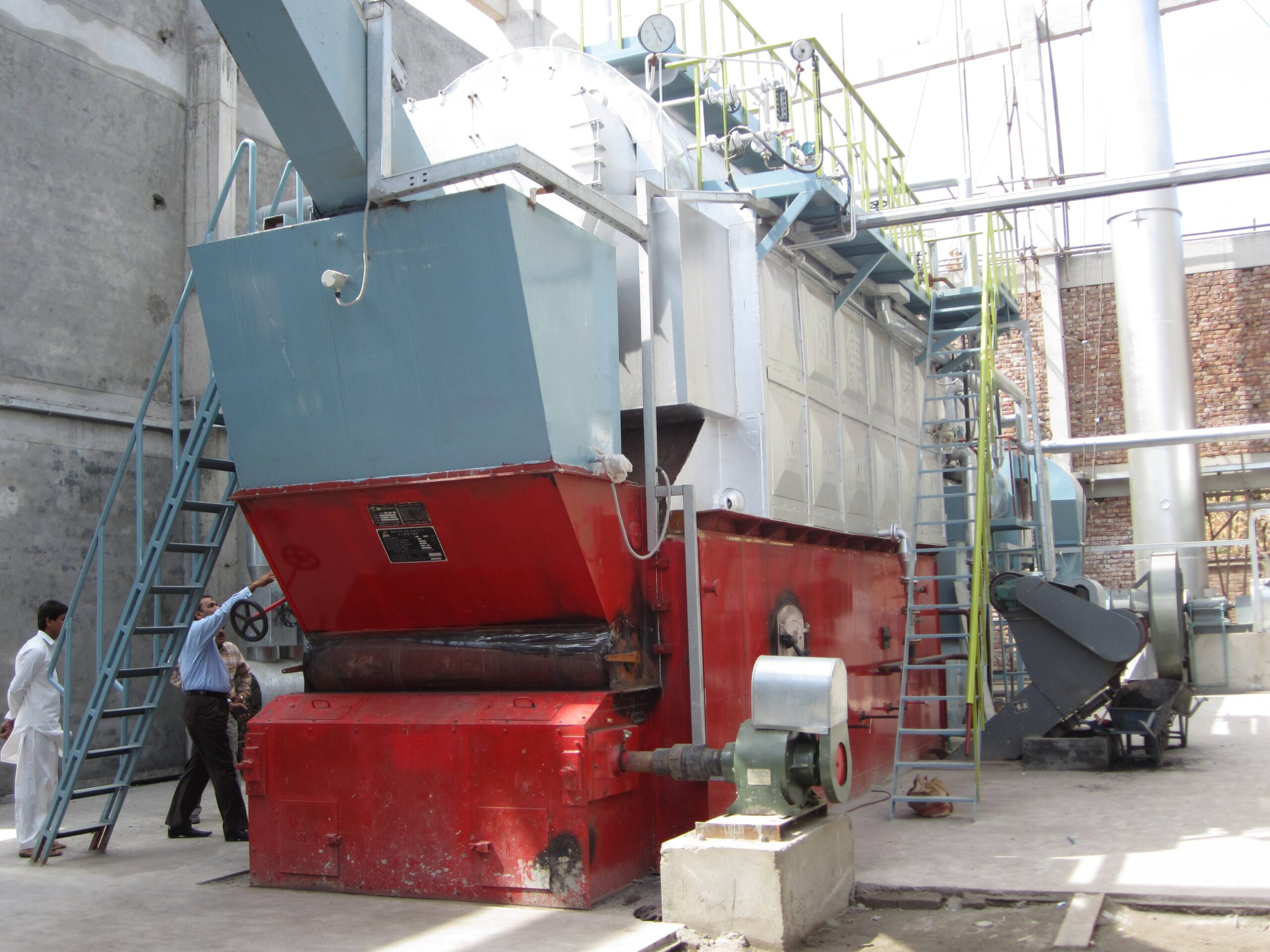
How Can Fuel Quality Management and Coal Sizing Reduce Slagging and Fouling?
In coal-fired boiler operations, slagging and fouling are two of the most damaging thermal performance issues. Slagging refers to molten ash deposits forming on furnace walls and high-temperature tubes, while fouling is the accumulation of dry or sintered ash on downstream heat exchangers. Both reduce heat transfer, cause overheating, and can lead to costly shutdowns. However, these issues often begin at the coal yard—with fuel quality and particle size distribution. By managing ash chemistry, moisture, and coal sizing, operators can reduce the likelihood of slag formation and fouling, resulting in more efficient, reliable, and lower-maintenance boiler operation.
Fuel quality management and coal sizing reduce slagging and fouling by controlling ash fusion behavior, combustion temperature distribution, and particulate transport characteristics. Selecting coal with a higher ash fusion temperature and lower sodium/potassium content helps prevent molten deposits, while properly sized coal ensures uniform combustion and limits localized hot spots that cause slagging. Avoiding overly fine particles reduces carryover and fouling in superheaters and economizers. Together, these measures improve boiler uptime, reduce cleaning frequency, and enhance thermal efficiency.
The path to clean combustion starts before the fuel reaches the flame.
Proper coal quality and sizing reduce slagging and fouling in boilers.True
Correct ash chemistry and particle size distribution help maintain stable combustion and prevent ash deposits on heat surfaces.
🔍 What Causes Slagging and Fouling?
Mechanism | Description | Affected Zones |
---|---|---|
Slagging | Melting and adhesion of ash on hot furnace surfaces | Furnace walls, superheater |
Fouling | Dry ash or sintered deposits on cooler surfaces | Economizer, air preheater |
Fly Ash Carryover | Fine particles bypass combustion zone and deposit | Superheater tubes |
Low Ash Fusion Temp | Causes ash to melt at standard furnace temperatures | All high-temp regions |
→ These issues reduce heat transfer and can damage pressure parts.
📏 Key Fuel Quality Parameters That Affect Slagging/Fouling
Parameter | Ideal Range / Target Value | Impact on Performance |
---|---|---|
Ash Fusion Temperature | > 1250°C | Higher = less slagging |
Sodium (Na₂O) Content | < 1.5% | Lower = fewer sticky, low-melting deposits |
Sulfur (S) Content | < 1.5% | High S can form corrosive, adhesive compounds |
Moisture Content | 8–12% | Affects flame temp and combustion uniformity |
Volatile Matter (VM) | 20–30% | High VM can shift flame zone and ash behavior |
→ Choosing coal with stable chemistry and low fouling indices is essential.
🔧 Why Coal Sizing Matters
Size Fraction (mm) | Combustion Impact |
---|---|
<1 mm (fines) | Burns too quickly, contributes to fly ash and fouling |
1–8 mm (optimal) | Burns evenly, avoids hot spots |
>25 mm (oversized) | Burns slowly, causes localized unburnt fuel and slagging |
| Sizing Goal | 85–90% of particles between 1–8 mm | Oversize/fines < 10% |
→ Proper sizing ensures uniform combustion and minimal deposit risk.
🧪 Case Study – Coal Quality Optimization in 35 TPH Boiler
Problem:
Frequent slagging in furnace walls
Weekly manual cleaning required
UBC = 6.2%, flue gas temp > 270°C
Findings:
Coal ash fusion temp = 1080°C
25% fines <1 mm; 15% oversize >20 mm
Sodium oxide in ash = 2.3%
Action Taken:
Switched to higher-grade coal (fusion temp = 1325°C, Na₂O = 1.1%)
Installed roller crusher and vibrating screen
Rebalanced fuel-air ratios for new VM content
Results:
Slagging incidents reduced by 85%
UBC dropped to 2.4%
Cleaning interval extended from 7 days to 30+ days
Efficiency improved by 7.2%
→ Quality management cut maintenance and improved thermal balance.
📊 Impact of Fuel Quality and Sizing on Slagging Risk
Coal Property | High Slagging Risk | Low Slagging Risk |
---|---|---|
Ash Fusion Temp (°C) | <1100 | >1250 |
Na₂O + K₂O (%) | >2.0 | <1.0 |
Sizing (% fines <1 mm) | >20% | <10% |
Oversize >25 mm | >10% | <5% |
→ Fuel blending and sizing reduce risk by creating a consistent combustion environment.
🛠 Tools and Strategies for Fuel Quality Management
Tool / Action | Purpose |
---|---|
Coal Crusher and Vibrating Screen | Control size distribution |
Ash Fusion Temperature Testing | Predict slagging tendency |
Fuel Blending | Mix low-Na or high-AFT coal with cheaper fuels |
Fouling Index Calculations | Use SiO₂, Al₂O₃, Na₂O ratios to assess risks |
Real-Time Soot Blowing | React to early fouling if it does occur |
→ The best fuel strategy is proactive—not reactive.
📈 Operational Benefits of Quality and Sizing Control
Benefit | Resulting Performance Impact |
---|---|
Fewer Shutdowns for Cleaning | Higher uptime, more predictable output |
Stable Heat Transfer | Improves steam quality and load response |
Lower Flue Gas Temperature | Better energy recovery, less stack loss |
Reduced Unburned Carbon (UBC) | More complete combustion, less ash disposal |
Longer Tube Life | Fewer overheating events, reduced erosion |
→ Clean combustion = clean economics.
In conclusion, fuel quality management and coal sizing are frontline strategies for reducing slagging and fouling in industrial boilers. Selecting coal with favorable ash chemistry and controlling particle size distribution ensure consistent, complete combustion, reduce heat exchanger fouling, and extend maintenance intervals. These practices improve energy efficiency, cut cleaning costs, and prevent operational disruptions. In the combustion process, the quality of your output begins with the quality of your input.
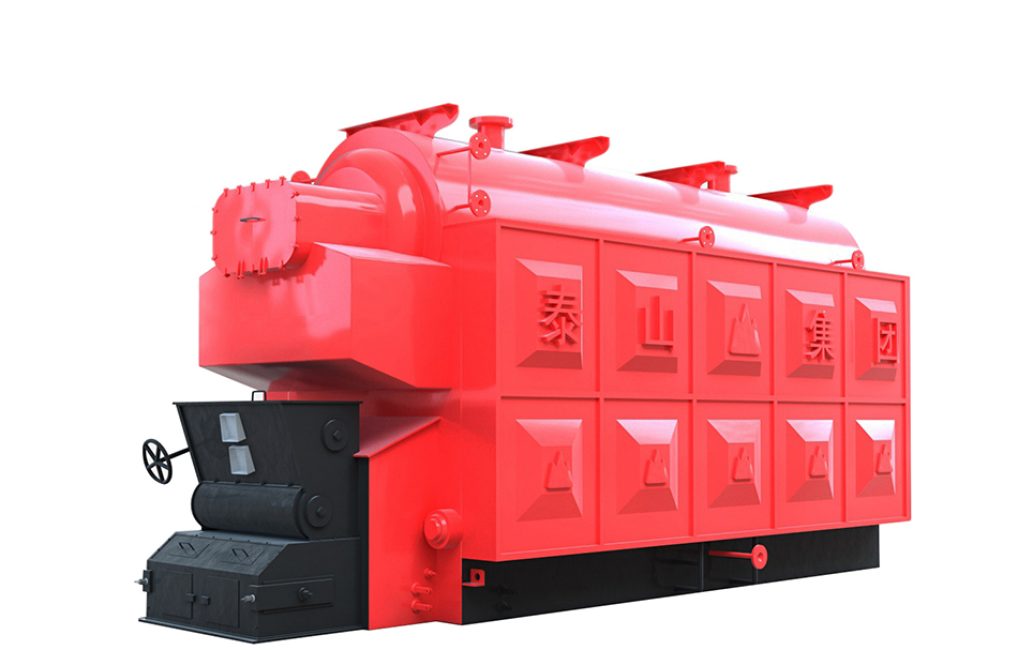
How Does Automation and Real-Time Performance Monitoring Improve Long-Term Efficiency?
In industrial steam systems, maintaining high thermal efficiency over time is a constant challenge. Shifts in fuel quality, load conditions, equipment wear, and operator variability gradually erode performance. Traditional manual tuning and periodic inspections cannot keep up with these changes, often leading to unnoticed efficiency loss, increased fuel consumption, and unplanned downtime. This is where automation and real-time monitoring become game changers. By continuously tracking performance data and dynamically adjusting control parameters, these systems stabilize operations, eliminate drift, and ensure that efficiency targets are sustained—not just occasionally met.
Automation and real-time performance monitoring improve long-term efficiency by continuously analyzing key operating parameters and automatically optimizing combustion, heat recovery, and load management. They detect deviations from setpoints, such as rising flue gas temperatures or O₂ fluctuations, and correct them in real time—avoiding performance degradation. These systems also support predictive maintenance, reduce human error, and optimize energy use across varying conditions. The result is sustained high efficiency, lower fuel costs, reduced emissions, and extended equipment life.
Long-term efficiency isn’t achieved once—it’s maintained through smart, adaptive control.
Automation and real-time monitoring systems improve boiler efficiency by maintaining optimal operating conditions continuously.True
They eliminate performance drift, reduce manual error, and dynamically respond to system changes for better energy use.
🔍 What Is Real-Time Performance Monitoring?
Monitoring Element | Description |
---|---|
Combustion Data | Tracks O₂, CO, flame stability, burner load |
Thermal Efficiency Metrics | Flue gas temperature, steam/fuel ratio, stack losses |
Heat Recovery Performance | Economizer inlet/outlet temps, ΔT tracking |
Load Trends & Demand Curves | Monitors steam output and modulates boiler firing |
Sensor Health and Drift Alerts | Ensures data accuracy and control reliability |
→ All data is processed through automated logic and control algorithms.
📏 Key Performance Indicators Enabled by Automation
Indicator | Optimal Range | Monitoring Outcome |
---|---|---|
O₂ in Flue Gas (%) | 3–4.5 | Adjusts air dampers for max efficiency |
CO (ppm) | <100 | Detects incomplete combustion |
Stack Temperature (°C) | <180 (post-economizer) | Triggers cleaning or air leak checks |
Steam-to-Fuel Ratio | Stable or improving | Directly reflects combustion quality |
Boiler Efficiency (%) | >85 (gas/biomass), >80 (coal) | Confirms real-time performance |
→ These KPIs can be visualized live and used to adjust process control.
🧪 Case Study – SCADA and Automation Upgrade in a 25 TPH Biomass Boiler
Initial State:
Efficiency dropped from 82.5% to 74.2% over 8 months
Manual tuning only done quarterly
Load response delays and high CO spikes
Intervention:
Installed SCADA + real-time combustion analyzer (O₂, CO)
Added auto-O₂ trim control, flue gas temp sensors
Set alarm thresholds for fouling, pressure drop, and steam deviation
Results:
Efficiency stabilized at 86.1% with ±0.5% variance
CO reduced from 180 ppm to 65 ppm
Fuel savings: ~1,750 tons/year
Unplanned downtime reduced by 70%
→ Automation replaced periodic corrections with constant optimization.
📊 Efficiency Improvements Enabled by Automation
Feature | Efficiency Gain (%) | Fuel Cost Reduction (%) |
---|---|---|
O₂ Trim Control | +3–5% | 3–7% |
Auto Soot Blowing (based on ΔT) | +2–4% | 2–5% |
Combustion Air Modulation | +3–6% | 3–6% |
Real-Time Alarm Monitoring | Prevents sudden drops | Avoids unplanned losses |
Integrated SCADA Visualization | Improves response time | Reduces operator error |
→ Automation leads to cumulative, compounding savings.
🔧 Components of an Automated Performance Monitoring System
Component | Role |
---|---|
SCADA Interface | Real-time dashboard for operators and engineers |
Programmable Logic Controller (PLC) | Executes logic for O₂, steam, temperature control |
O₂/CO Analyzers | Inputs for combustion optimization |
RTDs / Thermocouples | Measure flue gas and surface temps |
Steam and Fuel Flow Meters | Input to efficiency and mass balance calculations |
Data Historian / Cloud Logger | Enables trend analysis and reporting |
→ The best systems close the loop between data and action.
🛠 Maintenance Benefits of Real-Time Monitoring
Feature | Benefit |
---|---|
Early Fault Detection | Alerts before efficiency losses become visible |
Sensor Drift Identification | Prevents false control inputs |
Predictive Maintenance Scheduling | Reduces unplanned downtime |
Tube Fouling Monitoring | Based on flue gas temp rise, pressure drop |
Alarm Logging and Analytics | Tracks root cause of performance deviations |
→ Maintenance becomes predictive, not reactive.
📈 Long-Term Results of Automation Adoption
Timeframe | Without Automation | With Automation |
---|---|---|
Year 1 | 85% efficiency → 78% (drift) | 85% → 86.2% (maintained/improved) |
Year 2 | 1–2 unscheduled outages/year | <1 outage/year, with faster diagnosis |
Year 3 | Fuel cost ↑ ~9% | Fuel cost stable or ↓ due to tuning |
Year 4 | Equipment degradation visible | Longer tube, sensor, and pump lifespan |
→ Efficiency is not just about gains—it’s about preserving those gains.
⚠ Risks of Operating Without Automation
Missed Opportunity | Consequence |
---|---|
Unnoticed O₂/CO Drift | Fuel waste, increased CO emissions |
Delayed Soot Blowing | Fouling, higher stack temps, efficiency ↓ |
Manual Error in Load Adjustment | Pressure instability, overfiring |
Infrequent Efficiency Checks | Gradual performance degradation |
→ In the long run, manual-only systems cost more to run.
In conclusion, automation and real-time performance monitoring are essential tools for sustaining high boiler efficiency over the long term. By integrating data acquisition, intelligent control, and predictive response, these systems eliminate guesswork, minimize energy losses, and optimize every part of the combustion and heat transfer process. They reduce fuel consumption, extend equipment life, and provide real-time insight into performance trends. In modern energy systems, continuous optimization is not optional—it’s the foundation of efficiency.
🔍 Conclusion
Optimizing the performance of an industrial coal-fired boiler requires a holistic approach that blends combustion science, thermal engineering, and digital control. By addressing airflow balance, ash management, and heat recovery while leveraging modern monitoring technologies, industries can achieve substantial reductions in fuel costs, maintenance burden, and emissions output. This not only improves profitability but also ensures compliance in a carbon-conscious world.
📞 Contact Us
💡 Looking to reduce your coal-fired boiler’s operating costs? Our experts offer efficiency audits, combustion optimization, emissions control solutions, and system retrofits tailored to coal-based systems.
🔹 Let’s work together to make your coal-fired boiler cleaner, smarter, and more cost-efficient! 🏭🔥📉
FAQ
What are the key ways to improve coal-fired boiler efficiency?
Optimizing a coal-fired boiler involves:
Combustion tuning and air-fuel ratio control
Fuel quality management (sizing, drying)
Improving heat transfer through soot blowing and tube cleaning
Installing economizers and air preheaters
Minimizing unburnt carbon and fly ash losses
How does combustion tuning lower fuel consumption?
By adjusting the air-to-fuel ratio, flame stability, and burner settings, combustion can be made more efficient. Advanced oxygen trim systems and flue gas analyzers help reduce excess air and prevent unburnt fuel, saving up to 5–10% on fuel.
What is the role of ash management in reducing operational costs?
Efficient ash handling and removal systems (e.g., continuous blowdown, slagging control) reduce fouling and corrosion in the furnace and heat exchanger areas. This maintains optimal heat transfer and minimizes wear on boiler components.
Can fuel preparation improve overall boiler performance?
Yes. Consistent particle size, reduced moisture content, and uniform calorific value help stabilize combustion. Proper coal milling and drying before feeding enhances burn quality, reduces slag formation, and improves combustion efficiency.
What technologies enhance energy recovery in coal-fired systems?
Economizers: Recover heat from flue gas to preheat feedwater
Air Preheaters: Use flue gas to warm combustion air
Variable Frequency Drives (VFDs): Improve fan/pump energy use
Online monitoring systems: Ensure real-time performance optimization
References
Coal-Fired Boiler Optimization Techniques – https://www.energy.gov
Combustion Control for Coal Boilers – https://www.sciencedirect.com
Fuel Preparation for Efficiency in Coal Boilers – https://www.researchgate.net
Ash Handling and Boiler Cleaning Solutions – https://www.epa.gov
Economizer and Heat Recovery Systems – https://www.bioenergyconsult.com
Air-Fuel Ratio Optimization in Solid Fuel Boilers – https://www.mdpi.com
Energy Audit Techniques for Industrial Boilers – https://www.iea.org
Boiler Performance Monitoring Systems – https://www.automation.com
Best Practices for Coal Boiler Maintenance – https://www.energysavingtrust.org.uk
Thermal Efficiency Standards in Industrial Boilers – https://www.asme.org
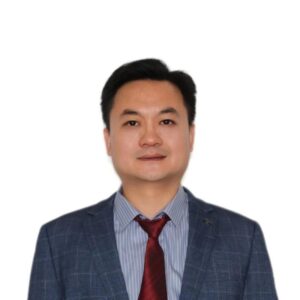