Environmental and Emission Regulations Impacting Circulating Fluidized Bed Boiler Selection
Circulating Fluidized Bed (CFB) boilers are widely used in industrial and power generation applications for their fuel flexibility, low combustion temperature, and inherent emissions control capabilities. However, despite these advantages, CFB boiler selection must still align with increasingly strict environmental and emission regulations that govern pollutants such as SOx, NOx, particulate matter (PM), and CO₂. Failure to comply can result in project delays, fines, retrofit expenses, or legal action, making environmental compliance a top priority during the design and procurement process.
Environmental and emission regulations impact CFB boiler selection by setting pollutant limits that influence furnace design, fuel selection, flue gas treatment systems, and combustion control technologies. Regulations vary by region but typically include standards such as the U.S. Clean Air Act (CAA), EU Industrial Emissions Directive (IED), and national environmental laws. CFB systems are often preferred due to their ability to meet these standards with in-furnace desulfurization, staged combustion, and low-NOx operation—but specific configurations must still be tailored to meet local regulatory limits.
Here’s what you need to know when evaluating regulatory compliance for CFB boiler selection.
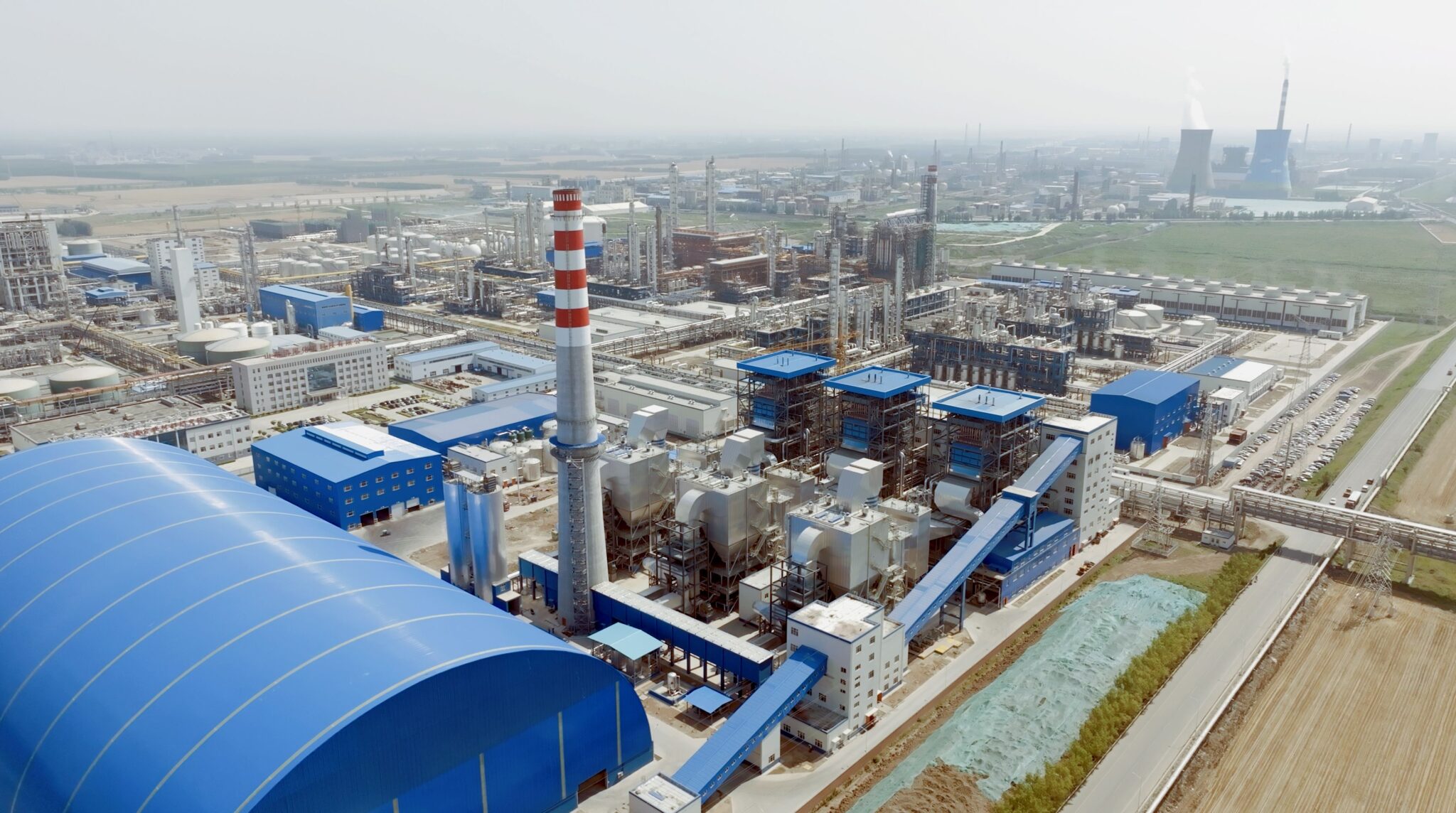
What Key Pollutants Are Regulated for CFB Boiler Emissions?
Circulating Fluidized Bed (CFB) boilers have become a preferred combustion technology for handling diverse solid fuels—including coal, biomass, and waste-derived fuels—thanks to their fuel flexibility and relatively low NOₓ emissions. However, despite their advanced combustion characteristics, CFB boilers are still subject to stringent emissions regulations, particularly as global air quality and climate standards continue to tighten. Whether installed in power generation, industrial processing, or district heating applications, CFB systems must comply with key pollutant limits that affect boiler design, fuel choices, and emissions control integration.
The key pollutants regulated for CFB boiler emissions are particulate matter (PM), nitrogen oxides (NOₓ), sulfur dioxide (SO₂), carbon monoxide (CO), and, in some cases, mercury (Hg), hydrogen chloride (HCl), and carbon dioxide (CO₂). These pollutants are controlled under regional and international standards because they impact human health, air quality, and climate. Compliance requires a combination of in-furnace combustion control, post-combustion treatment systems, and continuous emissions monitoring.
Even though CFB combustion offers inherent emissions advantages (especially for NOₓ), additional controls are still essential to meet modern regulatory standards.
CFB boilers are subject to emissions limits for PM, NOx, SO₂, and other regulated pollutants.True
CFB combustion systems must comply with the same regulated pollutant limits as other large industrial boilers, despite their improved fuel flexibility and combustion stability.
📋 Regulated Pollutants in CFB Boiler Emissions
Pollutant | Regulatory Focus | Typical Control Method |
---|---|---|
Particulate Matter (PM10, PM2.5) | Health hazard, visibility, lung damage | Bag filter, ESP |
Nitrogen Oxides (NOₓ) | Smog, acid rain, respiratory impact | In-furnace control, SNCR/SCR |
Sulfur Dioxide (SO₂) | Acid rain, soil/water acidification | In-bed limestone injection, FGD |
Carbon Monoxide (CO) | Toxic, indicates incomplete combustion | Air-fuel ratio optimization, combustion control |
Mercury (Hg) | Neurotoxin, bioaccumulates in water | Activated Carbon Injection (ACI) + PM filter |
Hydrogen Chloride (HCl) | Corrosive, affects stack and environment | DSI or wet scrubber |
Carbon Dioxide (CO₂) | Greenhouse gas, climate impact | Monitored for carbon tax/ETS compliance |
The specific limits for each pollutant depend on the country, boiler capacity, fuel type, and the industry sector involved.
🌍 Typical Emission Limits for CFB Boilers (by Region)
Pollutant | EU IED BREF (mg/Nm³) | China GB13223/13271 (mg/Nm³) | India CPCB (mg/Nm³) | US EPA MACT (mg/Nm³) |
---|---|---|---|---|
PM | 10–20 | 20–30 | 30–50 | 25–40 |
NOₓ | 150–200 | 200–300 | 300–400 | 150–200 |
SO₂ | 100–200 | 200–400 | 100–600 | 150–250 |
CO | 100–150 | 150–300 | 100–200 | 100–150 |
Hg | <0.03 | <0.05 | <0.03 | <0.01 |
Note: Limits vary based on boiler output, fuel properties, and whether the plant is newly commissioned or existing.
🔧 Why These Pollutants Matter for CFB Systems
1. PM (Particulate Matter)
CFBs inherently produce fly ash due to high turbulence
Ash carryover must be captured via bag filters or ESP
PM10/PM2.5 poses direct respiratory health risks
2. NOₓ (Nitrogen Oxides)
Lower in CFB than in PC (Pulverized Coal) due to lower combustion temps
SNCR with urea or ammonia is commonly used to meet strict standards
3. SO₂ (Sulfur Dioxide)
Controlled in-bed by limestone injection in CFBs
Further polishing via dry FGD or wet scrubbers may be required
4. CO (Carbon Monoxide)
Indicates combustion instability
Controlled by maintaining proper air staging and real-time O₂ trim
5. Hg and HCl
Present in trace amounts, especially when co-firing waste fuels
Controlled using Activated Carbon Injection (ACI) and scrubbing
📈 Real-World Emissions Performance Example: 40 TPH CFB Boiler
Parameter | Raw Emissions (mg/Nm³) | Post-Control (mg/Nm³) | Technology Used |
---|---|---|---|
PM | 115 | 18 | Bag Filter (99.9% removal) |
NOₓ | 310 | 160 | SNCR + Low-NOₓ design |
SO₂ | 420 | 110 | Limestone in-bed + DSI |
CO | 240 | 95 | Combustion tuning |
Hg | 0.06 | 0.018 | ACI + Baghouse |
This performance met EU IED and Indian CPCB standards simultaneously.
🛠️ Monitoring Requirements
Monitoring Method | Pollutants Covered | Regulation Required |
---|---|---|
CEMS (Continuous Emissions Monitoring System) | PM, NOₓ, SO₂, CO, O₂ | Mandatory (EU, India, China) |
Stack Sampling (Manual) | Hg, VOCs, HCl | Required annually or quarterly |
Data Acquisition System (DAS) | Logs and reports emissions | Required for permits and audits |
In conclusion, CFB boilers must meet stringent emissions regulations for PM, NOₓ, SO₂, CO, and in many cases, Hg and HCl, depending on fuel and jurisdiction. While the technology itself reduces some emissions compared to conventional combustion, full compliance requires targeted pollution controls and continuous monitoring. Understanding these regulated pollutants is essential for selecting the right fuel mix, designing appropriate control systems, and maintaining long-term operational and legal compliance. For CFB operators, emissions management is not just a technical issue—it’s a strategic imperative.
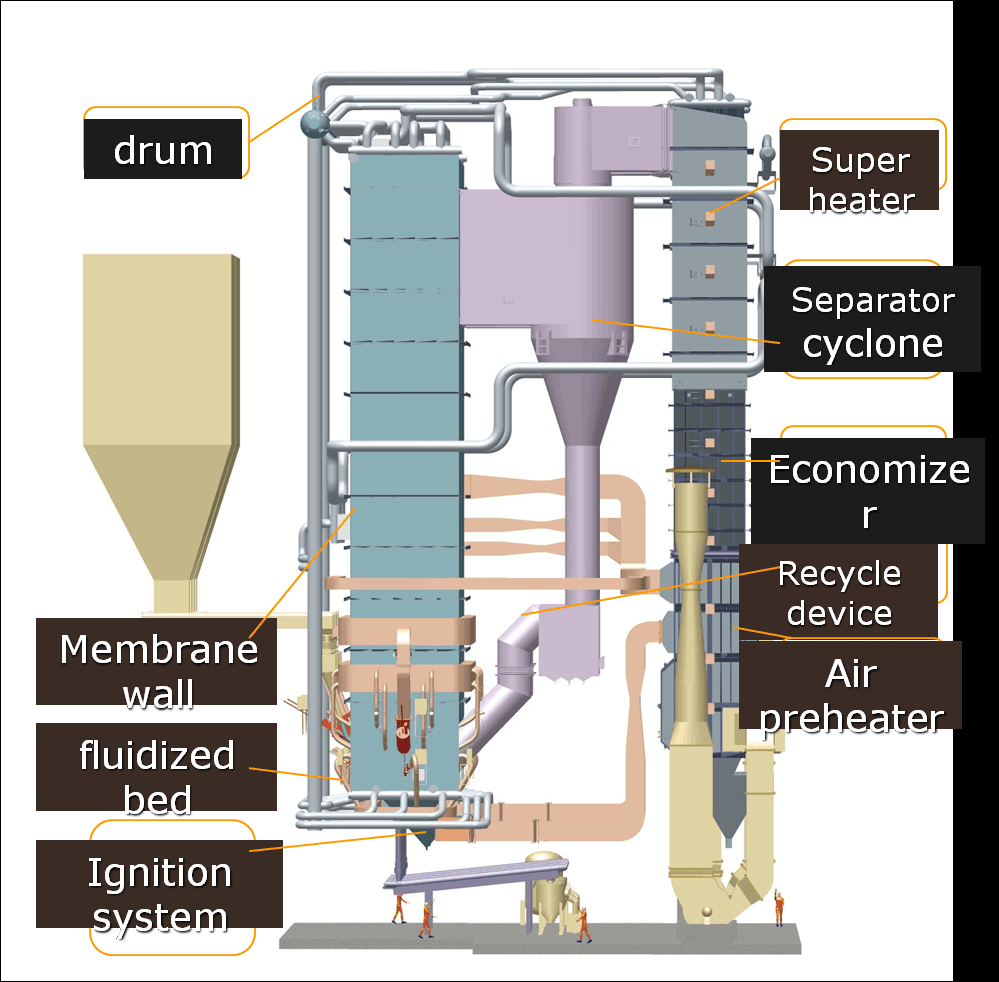
Which Global and Regional Environmental Standards Apply to CFB Boiler Projects?
Circulating Fluidized Bed (CFB) boiler technology is favored for its fuel flexibility, low combustion temperature, and inherent pollutant control capabilities. However, even with these advantages, any CFB project—whether in energy generation, chemical processing, or district heating—must meet strict global and regional environmental standards. These standards dictate design parameters, fuel use, emissions control requirements, and long-term monitoring protocols. Failure to comply doesn’t just delay commissioning—it can block financing, invalidate operating permits, or trigger steep penalties.
Global and regional environmental standards that apply to CFB boiler projects include the EU’s Industrial Emissions Directive (IED), the US EPA’s MACT and NSPS rules, China’s GB13271/13223, India’s CPCB norms, and numerous country-specific environmental laws. These standards define emission limits for key pollutants like NOx, SO₂, PM, CO, Hg, and CO₂, and they require emissions control systems, permitting, and continuous monitoring (CEMS) for legal operation and environmental compliance.
Designing a CFB boiler without referencing these standards is a recipe for costly retrofits or regulatory rejection.
CFB boiler projects must comply with international and regional environmental standards like the EU IED and US EPA MACT.True
CFB boilers are subject to the same environmental rules as other large combustion systems and must meet pollutant limits, monitoring, and reporting requirements.
🌍 Overview of Key Environmental Standards for CFB Boilers
Region/Country | Standard Name / Regulatory Body | Pollutants Regulated | Monitoring Required |
---|---|---|---|
EU | Industrial Emissions Directive (IED 2010/75/EU) + BREF (LCP 2022) | NOₓ, SO₂, PM, CO, VOCs, Hg, HCl | CEMS + QAL1/QAL2 |
USA | EPA MACT (40 CFR Part 63), NSPS (Part 60) | NOₓ, SO₂, PM, CO, Hg, HCl | CEMS + Stack Testing |
China | GB13271-2014 (Industrial Boilers), GB13223-2011 (Power Boilers) | PM, SO₂, NOₓ, Hg, CO | Real-time Monitoring (HJ212) |
India | Central Pollution Control Board (CPCB, 2017 norms) | PM, NOₓ, SO₂, Hg | CEMS for ≥10 TPH |
Canada | Provincial Guidelines + CCME Emission Inventory | PM, SO₂, NOₓ, GHGs | Varies by province |
Australia | National Environment Protection Measures (NEPM) + State EPAs | PM, NOₓ, SO₂, CO | State-level permits |
South Africa | National Air Quality Act (AQA 2004) | PM, NOₓ, SO₂, CO | AEL + reporting |
Many countries also mandate climate-related standards (GHG reporting, ETS participation), which apply even if local pollutant controls are met.
📏 Typical Emissions Limits for CFB Boilers (as per standards)
Pollutant | EU IED (mg/Nm³) | US MACT (mg/Nm³) | China GB13271 (mg/Nm³) | India CPCB (mg/Nm³) |
---|---|---|---|---|
PM | 10–20 | 25–30 | 20–30 | 30–50 |
NOₓ | 150–200 | 150–200 | 200–300 | 300–400 |
SO₂ | 100–200 | 150–250 | 200–400 | 100–600 |
CO | 100–150 | 100–150 | 150–300 | 100–200 |
Hg | <0.03 | <0.01 | <0.05 | <0.03 |
🛠️ How Standards Influence CFB Boiler Design
Standard Requirement | Engineering/Design Impact |
---|---|
Low PM Limits (e.g., <20 mg/Nm³) | Requires high-efficiency bag filter or ESP |
SO₂ Cap (e.g., <200 mg/Nm³) | In-bed limestone injection + FGD or DSI needed |
NOₓ Control (e.g., EU BREF <150 mg/Nm³) | SNCR + staged combustion design |
Mandatory CEMS | Requires analyzer racks, probes, DAS |
Hg Reporting or Capture | Triggers ACI or integrated sorbent traps |
Designers must account for space, utilities, and O&M when incorporating these controls into new projects.
📊 CFB Boiler Compliance Scenario: 35 MWth Project in Poland
Applicable Standard: EU IED + LCP BREF 2022
Emission Limits Required:
PM: <10 mg/Nm³
NOₓ: <150 mg/Nm³
SO₂: <150 mg/Nm³
System Design:
Baghouse for PM
SNCR for NOₓ
In-bed limestone + dry FGD for SO₂
CEMS installed with QAL1 calibration
Outcome:
Full permit approval within 3 months
Approved for EU carbon funding scheme
Operates under ISO 14001 + ETS reporting framework
🔍 Climate Compliance Add-ons
Requirement | Standard / Jurisdiction | Impact on Project |
---|---|---|
GHG Inventory | US, EU, India, Canada | CO₂ measurement and reporting |
ETS Participation | EU ETS, Korea ETS | Cap-and-trade compliance or carbon cost |
Carbon Intensity Cap | World Bank programs | Project selection for green financing |
Science-Based Targets (SBTi) | Global Corporations | Requires low-carbon tech integration |
These policies drive choices toward biomass co-firing, carbon capture readiness, or electrification.
In conclusion, CFB boiler projects must comply with a complex matrix of global and regional environmental standards, covering both air pollutants and greenhouse gases. These standards determine everything from emission control equipment to data reporting infrastructure. For new builds or retrofits, aligning the boiler system design with the appropriate environmental rules is not only essential for legal operation—it’s a prerequisite for financing, stakeholder approval, and long-term sustainability. Compliance begins not at commissioning, but at the design table.
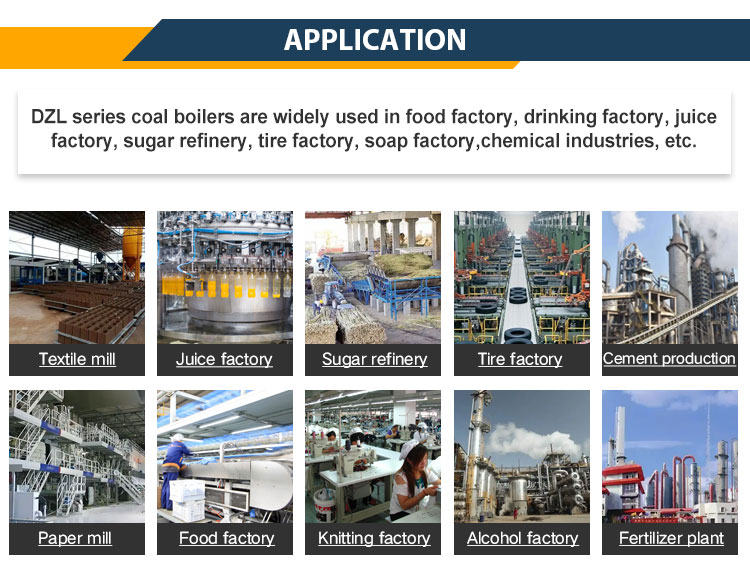
How Do SOx and NOx Limits Influence CFB Combustion Design and Fuel Selection?
Circulating Fluidized Bed (CFB) boilers are widely adopted for their flexibility in burning a broad range of solid fuels—coal, biomass, petroleum coke, and waste materials. However, the ability to burn low-cost or variable-quality fuels comes with a critical requirement: strict control of sulfur oxides (SOₓ) and nitrogen oxides (NOₓ) emissions. Across the globe, environmental agencies have set tight emission limits for these pollutants due to their role in acid rain, smog, and respiratory disease. As a result, CFB combustion system design and fuel strategy must prioritize emissions reduction from the earliest stage, directly affecting furnace geometry, air staging, bed temperature, and sorbent use.
SOₓ and NOₓ limits strongly influence CFB boiler combustion design and fuel selection. To meet SOₓ limits, engineers must integrate in-bed limestone injection and may need to avoid high-sulfur fuels or add external FGD systems. For NOₓ control, staged combustion, low combustion temperatures, and optional SNCR systems are applied. Fuels with high sulfur or nitrogen content require enhanced emissions control, affecting both design complexity and operational costs. Therefore, emissions limits dictate whether a fuel can be used directly, blended, or must be substituted altogether.
Meeting legal emission caps is not just about post-combustion control—it begins inside the furnace.
SOx and NOx limits influence both the design of CFB boiler combustion systems and the choice of fuel.True
Combustion temperature, air staging, sorbent injection, and fuel composition must be optimized to meet emissions limits, requiring design adaptations and fuel quality controls.
🌋 SOₓ and NOₓ: Formation Mechanisms and CFB-Specific Behavior
Pollutant | Formation in Combustion | CFB-Specific Traits |
---|---|---|
SOₓ | Sulfur in fuel reacts with oxygen → SO₂ | CFB allows in-bed sulfur capture using limestone |
NOₓ | N in air/fuel oxidized at high temp → NO + NO₂ | CFB operates at ~850°C, minimizing thermal NOₓ |
CFBs inherently emit lower NOₓ than pulverized coal boilers and are uniquely suited for SO₂ control without external scrubbers.
🔧 How SOₓ Limits Influence Combustion Design
Design Element | Impact/Function |
---|---|
In-Bed Limestone Injection | Captures SO₂ via CaCO₃ → CaSO₄ at 800–900°C |
Bed Inventory Control | Optimizes residence time of sorbent |
High Turbulence Mixing | Improves contact between fuel, air, and sorbent |
Backpass FGD (optional) | Used if sulfur capture in-bed is insufficient |
Sulfur Capture Efficiency vs. Ca/S Molar Ratio
Ca/S Ratio | SO₂ Removal Efficiency (%) |
---|---|
1.5 | ~70–75% |
2.0 | ~85% |
2.5 | >90% |
Higher sulfur fuels (e.g., petroleum coke, lignite) require higher limestone feed rates or external FGD units.
🔥 How NOₓ Limits Influence Combustion Design
Design Feature | Function |
---|---|
Staged Air Supply (Primary/Secondary) | Reduces peak combustion temperature |
Lower Bed Temperature (~850°C) | Minimizes thermal NOₓ formation |
Fuel Feeding Uniformity | Prevents localized over-temperature zones |
SNCR System (Urea or Ammonia Injection) | Converts NOₓ to N₂ at 850–1050°C |
Typical NOₓ Levels from CFB and Reduction by SNCR
Configuration | NOₓ Emissions (mg/Nm³) |
---|---|
Baseline CFB (no SNCR) | 250–350 |
CFB with SNCR (urea) | 120–180 |
Regulatory Target (EU IED) | ≤150 |
SNCR is often included only when ultra-low NOₓ levels are required by regional law.
🌱 Fuel Selection Constraints Imposed by SOₓ/NOₓ Limits
Fuel Type | Sulfur (%) | Nitrogen (%) | Impact on Design |
---|---|---|---|
Bituminous Coal | 0.5–1.5 | 1.0–1.5 | Requires Ca/S ≥2.0, possible SNCR needed |
Lignite | 1.0–2.0 | 1.5–2.2 | High limestone consumption, tighter combustion control |
Petroleum Coke | >2.5 | 1.0–1.5 | Needs external FGD + SNCR, expensive compliance |
Wood Chips | <0.05 | <0.5 | Minimal SOₓ/NOₓ; may avoid SNCR or sorbents |
Rice Husk | 0.2–0.6 | 0.5–1.0 | Moderate control required; fuel uniformity critical |
Fuel selection is directly limited by sulfur and nitrogen content in the context of local emission rules.
📊 Real-World Design Case: 25 TPH CFB Boiler, Multi-Fuel (India)
Primary Fuel: Bituminous coal (1.2% S, 1.1% N)
SO₂ Limit: 200 mg/Nm³ (CPCB 2017)
NOₓ Limit: 300 mg/Nm³
Design Response:
In-bed limestone injection (Ca/S = 2.1)
SNCR with urea for NOₓ control
Two-stage air injection (60:40 split)
O₂ trim and bed temp auto-control
Results:
SO₂: 138 mg/Nm³
NOₓ: 185 mg/Nm³
PM: 22 mg/Nm³ with bag filter
Full CPCB + ISO 14001 compliance
🧭 Strategic Design Recommendations
Condition | Design Recommendation |
---|---|
High-Sulfur Fuel (>1.5%) | Use dual-stage limestone + dry FGD |
High NOₓ Limit (<150 mg/Nm³) | Include SNCR or prep for SCR |
Mixed Fuel Use (Biomass + Coal) | Auto fuel adjustment + bed inventory control |
Variable Fuel Sulfur Content | Install sorbent flow control loop |
CFB systems designed without emissions forecasting can fail stack tests or require expensive retrofits post-installation.
In conclusion, SOₓ and NOₓ emission limits directly influence CFB boiler combustion design and allowable fuel types. These constraints affect everything from air injection geometry and bed temperature to limestone feed rates and post-combustion equipment. Selecting the wrong fuel—or underdesigning the combustion system—can result in non-compliance, penalties, and high retrofit costs. To succeed, CFB systems must be engineered with emissions limits as a core design parameter, not an afterthought.
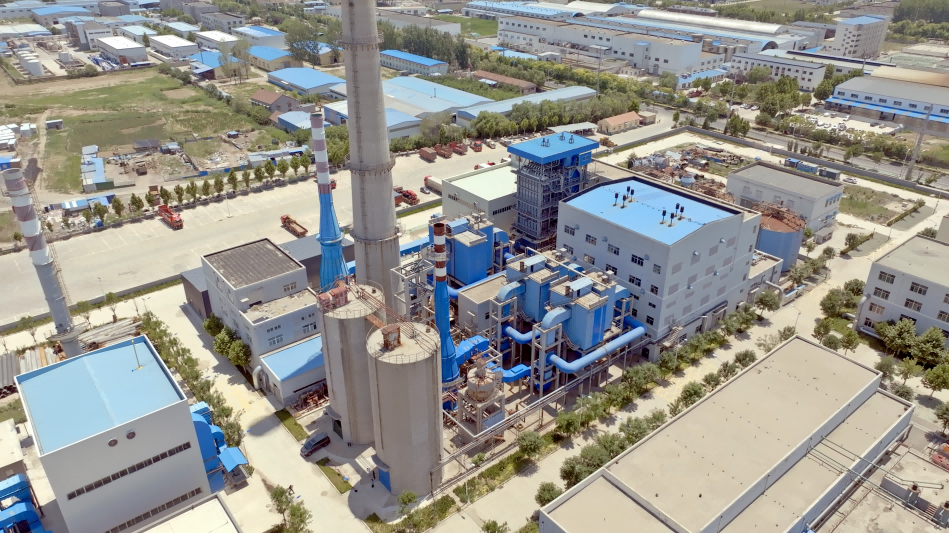
What Emission Control Systems Are Commonly Used with CFB Technology (e.g., SNCR, Fabric Filters)?
Circulating Fluidized Bed (CFB) combustion technology is widely recognized for its ability to handle diverse, low-grade fuels while maintaining high thermal efficiency and inherently low emissions—especially for NOₓ. However, inherent combustion advantages are not enough to meet today’s strict environmental regulations. To comply with emission standards for particulate matter (PM), sulfur dioxide (SO₂), nitrogen oxides (NOₓ), mercury (Hg), and other hazardous air pollutants (HAPs), CFB systems require integrated emission control systems. These technologies are selected and designed to match specific pollutants, regulatory thresholds, and fuel characteristics.
Common emission control systems used with CFB boiler technology include Selective Non-Catalytic Reduction (SNCR) for NOₓ reduction, fabric filters (baghouses) or Electrostatic Precipitators (ESPs) for PM control, in-bed limestone injection and Dry Sorbent Injection (DSI) for SO₂ capture, and Activated Carbon Injection (ACI) for mercury and VOC mitigation. These systems ensure compliance with global emissions limits and are typically designed to work together with the combustion process.
CFB plants benefit from the modularity and compatibility of these controls, allowing tailored emission reduction strategies for both new and retrofit applications.
CFB boilers use SNCR, fabric filters, and sorbent injection systems to meet emissions regulations.True
These emission control systems are commonly integrated with CFB boilers to reduce NOx, PM, and SO₂ levels below legal thresholds.
📋 Key Emission Control Systems Used with CFB Boilers
Pollutant Controlled | Emission Control System | Removal Efficiency (%) | Application Stage |
---|---|---|---|
NOₓ | SNCR (Selective Non-Catalytic Reduction) | 40–70% | Post-combustion (in-furnace) |
SCR (Selective Catalytic Reduction) | 85–95% | Optional (rare for CFB) | |
PM (Particulate Matter) | Fabric Filter (Baghouse) | 99.9%+ | Post-combustion (stack) |
Electrostatic Precipitator (ESP) | 98–99.5% | Alternative (space-saving) | |
SO₂ | In-bed Limestone Injection | 70–90% | In-furnace |
DSI (Dry Sorbent Injection) | 75–90% | Post-combustion | |
Hg and VOCs | ACI (Activated Carbon Injection) | 80–95% | Before baghouse |
HCl/HF | DSI or Wet Scrubber | 70–95% | Post-combustion |
These systems may be used in combination, depending on regulatory compliance levels and fuel sulfur/ash/nitrogen content.
🔧 Technology Function and Integration Overview
1. SNCR (Selective Non-Catalytic Reduction)
Injects urea or ammonia into high-temp zones (850–1050°C)
Converts NOₓ to N₂ and H₂O
Requires precise temperature and mixing control
Ideal for CFBs due to uniform furnace conditions
2. Fabric Filter (Baghouse)
Uses fabric bags to capture fine fly ash and unburned carbon
Achieves <10 mg/Nm³ PM emissions
Often integrated with ACI and DSI systems
Requires periodic cleaning (pulse jet or reverse air)
3. Electrostatic Precipitator (ESP)
Electrically charges particles and collects them on plates
Preferred for fuels with low-resistivity ash (e.g., lignite)
Slightly lower removal efficiency than baghouses
Lower pressure drop, good for large-scale retrofits
4. In-Bed Limestone Injection
Core CFB feature—adds crushed limestone directly into fluidized bed
Captures SO₂ during combustion via CaCO₃ → CaSO₄
Optimal Ca/S ratio: 1.8–2.5
May require DSI for polishing under strict limits
5. Dry Sorbent Injection (DSI)
Injects fine hydrated lime or sodium bicarbonate into flue gas
Captures SO₂, HCl, and other acid gases
Lower capex than wet scrubbers, but less efficient for very high sulfur fuels
6. Activated Carbon Injection (ACI)
Fine powdered carbon injected upstream of baghouse
Adsorbs elemental and oxidized mercury
Effective for Hg compliance in mixed coal/waste-firing applications
📊 Real-World Control Strategy for a 50 TPH CFB Boiler (India)
Emission Target | Compliance Requirement | Control System Applied | Measured Emissions (mg/Nm³) |
---|---|---|---|
PM < 30 mg/Nm³ | CPCB 2017 standard | Baghouse filter | 18 |
NOₓ < 300 mg/Nm³ | CPCB 2017 | SNCR with urea dosing | 175 |
SO₂ < 200 mg/Nm³ | Fuel S = 1.2% | In-bed limestone + DSI | 122 |
Hg < 0.03 mg/Nm³ | Mixed coal + biomass | ACI system | 0.018 |
All systems monitored via integrated CEMS with real-time alerts and cloud reporting.
🧠 Why These Systems Are Preferred in CFB Applications
Technology | CFB-Specific Benefit |
---|---|
SNCR | Works well with CFB’s stable temperature zones |
In-Bed Limestone | Synergizes with fluidized combustion process |
Fabric Filter | Tolerates fly ash variation from biomass/waste |
ACI | Easy retrofit for mercury control |
DSI | Fast response to sulfur or chlorine spikes |
These systems allow tailored emissions packages based on region, fuel blend, and regulation.
In conclusion, emission control systems commonly used with CFB boilers include SNCR for NOₓ, fabric filters or ESPs for PM, in-bed limestone and DSI for SO₂, and ACI for mercury. These technologies are essential not only to meet environmental limits but also to maintain permit validity, avoid fines, and operate sustainably. Their integration with CFB systems offers cost-effective, fuel-flexible, and regulation-ready performance, ensuring compliance in a world of tightening emission standards.
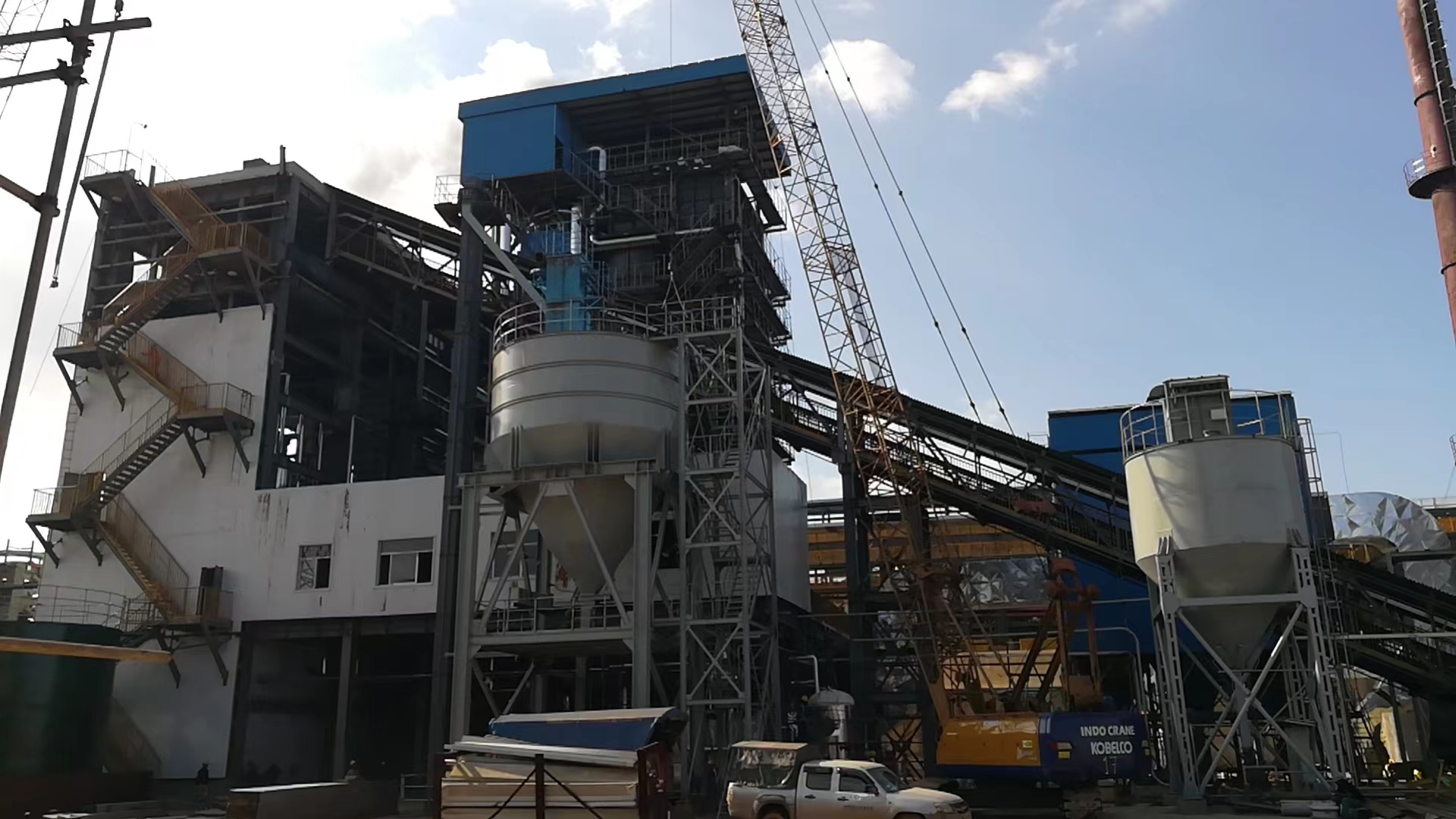
How Do Carbon Emissions and Decarbonization Policies Impact CFB Boiler Viability?
Circulating Fluidized Bed (CFB) boilers are renowned for their fuel flexibility and efficiency—capable of burning coal, biomass, waste fuels, or a combination thereof. But in the age of carbon neutrality and climate accountability, flexibility alone is no longer enough. Global decarbonization policies, net-zero targets, and carbon pricing are transforming how industries evaluate boiler investments. Carbon emissions from fossil-fired systems are becoming a liability, and the long-term viability of CFB boilers increasingly depends on their carbon footprint, fuel choice, and ability to align with decarbonization mandates.
Carbon emissions and decarbonization policies directly impact the viability of CFB boilers by imposing penalties on fossil CO₂ emissions, incentivizing biomass or waste-based co-firing, and demanding future readiness for carbon capture or fuel conversion. Pure coal-fired CFBs face declining support due to carbon taxes and emissions trading schemes (ETS), while biomass or co-fired CFBs gain regulatory and financial favor. Viability today hinges on the system’s capacity to reduce CO₂ intensity and transition toward carbon neutrality.
CFB boiler projects that ignore climate policy risk becoming stranded assets—obsolete, non-compliant, and uneconomical.
CFB boiler viability is affected by carbon emissions regulations and decarbonization policies.True
Fossil-fired CFB systems face increasing compliance costs and operational restrictions, while low-carbon or renewable-fueled CFBs are incentivized under global climate targets.
🌍 Global Decarbonization Trends Impacting CFB Projects
Climate Policy Mechanism | Relevance to CFB Boilers |
---|---|
Carbon Pricing (Taxes/ETS) | Penalizes fossil-fueled systems |
Net-Zero Commitments (by 2050) | Drives shift to biomass, waste fuels |
Renewable Energy Mandates | Favors biomass-fueled CFBs |
Green Taxonomy / Sustainable Finance | Devalues coal-only projects |
Science-Based Targets (SBTi) | Requires emissions disclosure and reduction |
Carbon Border Adjustment Mechanisms (CBAM) | Penalizes exporters using high-carbon boilers |
These frameworks now influence boiler funding, permitting, and operational economics.
📊 Comparative Carbon Intensity by Fuel Type (Used in CFB)
Fuel Type | CO₂ Emissions (kg/MWh thermal) | Climate Policy Impact |
---|---|---|
Bituminous Coal | 340–390 | High carbon tax and ESG penalty |
Lignite | 400–450 | Least favored, high intensity |
Petroleum Coke | >500 | Heavily penalized |
Biomass (Wood Chips) | ~20–50* (biogenic CO₂) | Generally considered neutral |
Refuse-Derived Fuel (RDF) | 50–120** | Often treated as avoided emissions |
Co-firing (Biomass + Coal 50/50) | ~180–220 | Transitional option, moderately viable |
*Biomass CO₂ is counted as carbon-neutral under most climate accounting protocols.
**RDF emissions vary but may qualify for avoided landfill credits.
🔧 Viability Pathways for CFB Boilers Under Carbon Pressure
Design / Operational Strategy | Decarbonization Impact |
---|---|
100% Coal CFB | Poor outlook, high carbon liability |
Biomass CFB | High viability, preferred for carbon neutrality |
Coal + Biomass Co-firing CFB | Transitional compliance path |
RDF/Waste-Fueled CFB | Eligible for circular economy credits |
Hydrogen-Ready or CCS-Ready CFB | Future-aligned, good for new investments |
Long-term viability depends on fuel sourcing, emissions per MWh, and integration with climate strategies.
🧪 Case Study: Retrofitting for Carbon Viability – 35 TPH CFB Boiler (Poland)
Initial Setup: 100% bituminous coal
Carbon Cost Exposure: €54/ton under EU ETS
Emissions: ~25,000 tons CO₂/year
Retrofit Strategy:
Switched to 60% biomass + 40% coal
Added CEMS and fuel blending control
ETS cost reduced to €11/ton net (with biogenic CO₂ exemption)
Outcome:
Emissions down to ~12,000 tons
Carbon cost savings: €702,000/year
Viability restored under SBTi-compliant corporate roadmap
🛠️ Climate Policy Readiness Features in New CFB Designs
Feature | Benefit Under Climate Policy Framework |
---|---|
Biomass or RDF Fuel Flexibility | Enables low-carbon fuel switching |
Carbon Capture Compatibility | Futureproofing for net-zero operations |
Real-Time CO₂ Monitoring | Supports ESG and regulatory disclosure |
Energy Efficiency Enhancements | Reduces CO₂ per MWh |
Automated Co-Firing Controls | Allows dynamic carbon footprint management |
Many banks and climate funds now require these features for financing approval.
In conclusion, carbon emissions and decarbonization policies are reshaping the viability of CFB boilers worldwide. Projects based solely on coal or petroleum coke face rising costs, reduced funding access, and legal pushback. In contrast, systems designed for biomass, co-firing, RDF, or carbon capture readiness are increasingly seen as forward-compatible with global climate goals. The future of CFB boilers lies not in resisting decarbonization—but in enabling it.
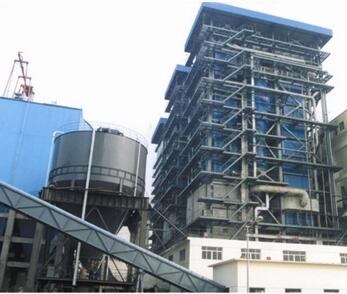
Why Is Continuous Emission Monitoring (CEMS) Critical for Regulatory Compliance in CFB Boilers?
Circulating Fluidized Bed (CFB) boilers are engineered for fuel flexibility and emissions reduction, but even their inherent combustion advantages don’t exempt them from today’s stringent environmental regulations. Governments around the world demand not just low emissions—but proof of compliance through real-time tracking. This is where Continuous Emission Monitoring Systems (CEMS) become essential. CEMS isn’t just a reporting tool—it’s a regulatory requirement and a frontline defense against environmental violations, penalties, or operating permit suspensions.
CEMS is critical for regulatory compliance in CFB boilers because it provides continuous, real-time measurement and recording of key pollutant emissions such as SO₂, NOₓ, PM, CO, and O₂. This data is essential for demonstrating compliance with environmental limits, submitting legal reports to authorities, supporting permit renewals, and avoiding fines. Regulatory bodies in the EU, US, China, and India mandate CEMS for medium- to large-scale CFB boilers, making it a legal, operational, and environmental necessity.
Without CEMS, a plant may be emitting within limits—but still be non-compliant due to lack of verified data.
Continuous Emission Monitoring Systems (CEMS) are mandatory for many CFB boilers to meet regulatory compliance.True
CEMS provides continuous, traceable emission data that is required by law in several jurisdictions, particularly for medium and large industrial boilers.
🧾 Key Regulatory Bodies That Require CEMS for CFB Boilers
Region / Jurisdiction | Regulation / Standard | CEMS Requirement Scope |
---|---|---|
European Union (EU) | Industrial Emissions Directive (2010/75/EU) | Required for boilers >50 MWth |
United States (EPA) | 40 CFR Parts 60 & 75 (NSPS, MACT) | Mandatory for large units with air permits |
China | GB13271-2014 + HJ212 protocol | Real-time monitoring for all ≥10 TPH units |
India | CPCB Norms (2015 onward) | CEMS required for ≥10 TPH industrial boilers |
South Africa | Air Quality Act + Schedule 2 Licensing | Mandatory for AEL facilities |
CEMS is now the international standard for compliance validation and pollutant control transparency.
📋 What Pollutants Does CEMS Measure in CFB Boilers?
Parameter Measured | Relevance to CFB Operation |
---|---|
SO₂ | Reflects sulfur content in fuel and limestone efficiency |
NOₓ | Indicates combustion conditions and SNCR performance |
PM (Particulate Matter) | Measures filter/ESP effectiveness |
CO | Indicates incomplete combustion |
O₂ | Essential for excess air and fuel efficiency |
CO₂ (optional) | Supports climate reporting and carbon audits |
CEMS systems are modular, and analyzers can be added for specific pollutants based on local permit requirements.
🔧 How CEMS Works in a CFB Boiler Setup
System Component | Function |
---|---|
Stack Probe | Extracts representative flue gas sample |
Gas Conditioning Unit | Removes moisture and particulates for analyzer protection |
Gas Analyzers | Measure SO₂, NOₓ, CO, O₂, etc. via spectroscopy or electrochemical methods |
Particulate Monitor | Detects PM levels via light scattering or triboelectric methods |
Data Acquisition System (DAS) | Logs, stores, and transmits emissions data |
Reporting Interface | Generates daily/weekly/monthly legal reports |
This system can be integrated with SCADA or DCS for real-time alerts, trend analysis, and compliance control.
📊 Real-World CEMS Application – 40 TPH Biomass CFB Boiler (India)
Regulatory Compliance: CPCB 2017 Norms
Pollutants Tracked: PM, NOₓ, SO₂, CO, O₂
CEMS Vendor: ENVEA CEM Compact with stack-mounted probe
Integration: Linked to CPCB online portal via GPRS
Operational Benefits:
Auto alarm on PM spike
Data-driven air-fuel optimization
CEMS report accepted for consent-to-operate renewal
Avoided ₹1.5 million in potential penalties
🧠 Why CEMS Is Not Optional for Long-Term Viability
Risk Without CEMS | Consequence |
---|---|
No real-time data | Undetected violations and penalties |
Manual logbooks only | Rejected by authorities |
Failure to report | Treated as non-compliance |
No trend visibility | Missed optimization opportunities |
CEMS audit failure | Shutdown orders or license revocation |
Most environmental laws now state: “No CEMS = No Proof = Non-Compliance.”
🔍 CEMS and Digital Compliance Ecosystems
Digital Compliance Tool | Benefit |
---|---|
Auto-reporting Software | Ensures legal submissions to CPCB, EPA, etc. |
SCADA-CEMS Integration | Enables real-time emission-based control |
Cloud-Based Dashboards | Enables multi-site emissions benchmarking |
Data Validation (QAL2/QAL3) | Required for ISO 14001 and EU permits |
CEMS is increasingly being tied to corporate ESG, carbon reporting, and green finance eligibility.
In conclusion, CEMS is critical for ensuring regulatory compliance in CFB boilers—not just to meet legal requirements, but to operate responsibly, transparently, and efficiently. It forms the foundation of modern environmental accountability, enabling operators to prove their emissions performance in real-time, respond to issues before they become violations, and align with global sustainability goals. In today’s climate-conscious industrial world, a CFB boiler without CEMS is a compliance risk waiting to happen.
🔍 Conclusion
Circulating Fluidized Bed boilers offer a strong foundation for emissions compliance, but success depends on aligning the boiler system design, fuel strategy, and emission control technologies with specific regulatory frameworks. Whether you’re burning coal, biomass, or waste-derived fuels, your CFB boiler must be engineered to meet current—and future—air quality and carbon reduction mandates. Choosing a regulation-ready system ensures sustainability, legal compliance, and long-term operational resilience.
📞 Contact Us
💡 Planning a CFB boiler project? Our team offers expert support in emissions compliance, system design, and technology integration for all major industrial and environmental standards.
🔹 Reach out today and build an emissions-compliant, high-performance CFB boiler system! 🔄🌍✅
FAQ
What environmental regulations affect the selection of a CFB boiler?
CFB boilers must comply with global and regional standards like the EPA Clean Air Act, the EU Industrial Emissions Directive (IED), and local air quality regulations. These rules define strict limits on NOx, SO₂, CO, CO₂, mercury, and particulate matter (PM) emissions, requiring advanced emission control technologies during boiler design and selection.
Why are CFB boilers considered environmentally compliant by design?
CFB boilers operate at lower combustion temperatures (800–900°C), naturally limiting NOx formation. Additionally, they allow in-furnace desulfurization by adding limestone, significantly reducing SO₂ emissions without the need for external scrubbers.
How do NOx emission limits influence CFB boiler configuration?
Due to regulatory NOx limits, CFB boilers incorporate low-temperature combustion, staged air injection, and sometimes selective non-catalytic reduction (SNCR) systems to meet or exceed compliance thresholds with minimal external equipment.
How is particulate matter controlled in CFB systems?
Particulate matter (PM) is managed using cyclone separators, baghouse filters, or electrostatic precipitators (ESPs). Compliance with PM standards is essential, as fluidized bed combustion can generate fine ash and dust, especially when burning high-ash fuels.
What greenhouse gas (GHG) and carbon policies impact CFB boiler use?
CFB boilers are increasingly favored under GHG emission caps and carbon taxation policies because they support fuel flexibility, co-firing with biomass, and high combustion efficiency, enabling reduced CO₂ emissions per unit of energy compared to traditional coal-fired systems.
References
EPA Clean Air Act Boiler Standards – https://www.epa.gov
EU Industrial Emissions Directive for Large Combustion Plants – https://www.europa.eu
NOx and SO₂ Control in Fluidized Bed Combustion – https://www.sciencedirect.com
In-Furnace Desulfurization in CFB Boilers – https://www.researchgate.net
CFB Emission Compliance Guide – https://www.bioenergyconsult.com
Best Available Techniques (BAT) for CFB Boilers – https://www.mdpi.com
Particulate Emission Standards and Control Systems – https://www.energysavingtrust.org.uk
Carbon Policy and CFB Boiler Design – https://www.iea.org
Emission Monitoring in Power Plants – https://www.automation.com
Advanced CFB Technology for Emission Reduction – https://www.sciencedirect.com
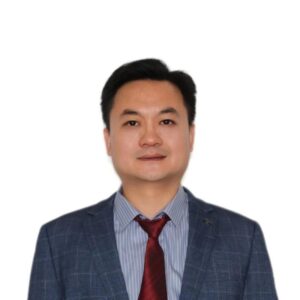