Key Factors Influencing Heat Transfer and Combustion Efficiency in Industrial Biomass Boilers
Industrial biomass boilers are gaining popularity for their sustainability, fuel flexibility, and carbon-neutral benefits. However, achieving high heat transfer and combustion efficiency is not automatic. Biomass fuels vary widely in composition and behavior, and if combustion and heat exchange processes are not optimized, it can result in incomplete fuel burn, low thermal output, fouling, and high emissions. Understanding the variables that affect efficiency is essential for operators aiming to reduce fuel consumption, maintenance costs, and environmental impact.
The heat transfer and combustion efficiency in industrial biomass boilers are influenced by factors such as fuel type and moisture content, particle size, combustion air distribution, boiler design, furnace temperature, flue gas velocity, and the condition of heat exchanger surfaces. Inconsistent fuel properties and poor combustion control can reduce flame temperature, increase unburned carbon, and lead to ash fouling on heat transfer surfaces. Proper fuel preparation, combustion tuning, and maintenance are critical to sustain long-term efficiency.
Let’s examine the key performance variables that determine how efficiently your biomass boiler converts fuel energy into usable heat.
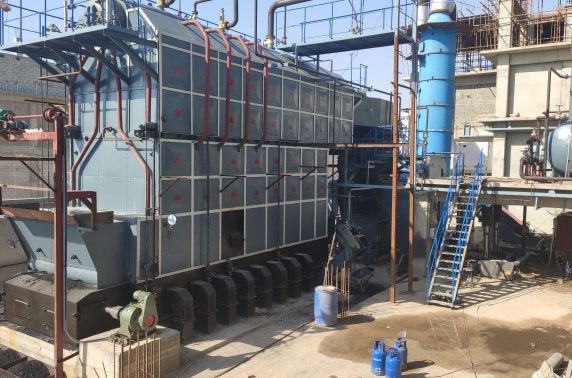
How Does Biomass Fuel Type and Moisture Content Impact Combustion Efficiency?
Biomass is widely promoted as a renewable alternative to fossil fuels in industrial boiler systems, but its combustion performance varies greatly depending on fuel type and moisture content. Unlike standardized fuels like natural gas or oil, biomass feedstocks such as wood chips, pellets, agri-residues, and RDF can differ significantly in energy content, ash behavior, and moisture levels. These variations directly affect combustion stability, flame temperature, and thermal efficiency. High-moisture or low-calorific fuels absorb combustion heat to evaporate water, leading to reduced steam output, increased flue gas temperature, and incomplete burning. Poor fuel selection or unaddressed moisture levels can undermine both performance and emissions compliance.
Biomass fuel type and moisture content impact combustion efficiency by determining the energy density and the amount of heat lost to water evaporation. High-moisture fuels absorb combustion heat to evaporate water, reducing flame temperature and steam generation. Low-quality fuels with high ash or volatile matter may lead to slagging or incomplete combustion. Fuel types like wood pellets offer higher and more stable efficiency due to low moisture and uniform properties, whereas raw agri-residues or wet chips require drying, optimized combustion air, and ash management. Selecting the right fuel and controlling moisture is critical for maintaining high efficiency in biomass boilers.
Fuel quality is not optional—it’s the foundation of combustion performance.
Biomass fuel type and moisture content significantly affect boiler combustion efficiency.True
Moisture reduces effective energy output and low-grade biomass can cause slagging, fouling, and unstable combustion.
🔍 Key Biomass Fuel Characteristics Affecting Efficiency
Parameter | Effect on Combustion Performance |
---|---|
Moisture Content (%) | High moisture absorbs heat, cools flame, lowers efficiency |
Calorific Value (kcal/kg) | Directly affects steam output per kg fuel |
Ash Content (%) | Impacts fouling, slagging, particulate emissions |
Volatile Matter (%) | Influences ignition and flame stability |
Bulk Density (kg/m³) | Affects fuel feeding and storage logistics |
→ Moisture and calorific value are most critical for efficiency.
📏 Comparison of Biomass Fuels by Moisture and Efficiency Potential
Biomass Type | Moisture (%) | CV (kcal/kg) | Ash (%) | Typical Efficiency (%) |
---|---|---|---|---|
Wood Pellets | 6–10 | 4200–4600 | 0.5–1.0 | 85–88 |
Wood Chips (dry) | 15–25 | 3200–3800 | 1–2 | 78–84 |
Rice Husk | 8–12 | 2900–3200 | 15–20 | 70–75 |
Straw Bales | 12–18 | 2800–3200 | 6–10 | 68–74 |
Wet Sawdust | 35–55 | 2000–2500 | 1–2 | 60–68 (if undried) |
→ Dry, low-ash fuels = better efficiency and cleaner combustion.
🛠 Moisture Content and Energy Loss Explained
Moisture Level (%) | Energy Lost to Evaporation (%) | Combustion Effect |
---|---|---|
<10% | Minimal (<5%) | High flame temp, fast ignition |
15–20% | Moderate (5–10%) | Some cooling, manageable loss |
25–35% | High (10–20%) | Slower combustion, lower efficiency |
>40% | Very high (>25%) | Incomplete burn, high flue temp, CO↑ |
→ Each 10% increase in moisture may reduce boiler efficiency by 2–5%.
📊 Performance Impact of Moisture in Wood Chips (Real Data)
Moisture (%) | Flue Gas Temp (°C) | CO (ppm) | Steam Output (TPH) | Efficiency (%) |
---|---|---|---|---|
15% | 185 | 65 | 10.2 | 85.6 |
25% | 210 | 95 | 9.1 | 79.2 |
35% | 245 | 180 | 8.2 | 72.4 |
→ Proper fuel drying or selection leads to dramatic performance improvement.
🧪 Case Study – Rice Husk vs. Wood Pellet Boiler
System: 12 TPH biomass-fired FBC boiler
Fuel A: Rice husk (12% moisture, 16% ash)
Fuel B: Wood pellets (8% moisture, 0.8% ash)
Performance Metric | Rice Husk | Wood Pellets |
---|---|---|
Steam Output (TPH) | 11.4 | 12.0 |
Flue Gas Temp (°C) | 232 | 188 |
CO Emissions (ppm) | 180 | 45 |
Thermal Efficiency (%) | 74.8 | 86.7 |
→ Switching fuel improved efficiency by ~12% and reduced CO by ~75%.
🔧 Operational Adjustments for High-Moisture Biomass
Adjustment Type | Action |
---|---|
Combustion Air | Increase primary air for drying zone |
Grate Speed | Slow down to allow moisture evaporation |
Fuel Feed Rate | Reduce to maintain combustion temp |
Secondary Air Tuning | Promote burnout, reduce CO |
Flue Gas Recirculation (FGR) | Stabilizes temp, lowers excess air |
→ Control strategies must adapt to fuel variability.
📈 Best Practices to Improve Biomass Combustion Efficiency
Practice | Benefit |
---|---|
Pre-drying fuels | Reduces energy loss, improves burn |
Fuel Quality Testing (moisture, CV) | Allows proper boiler tuning |
Feedstock homogenization | Prevents load swings, stabilizes flame |
Soot blowing and ash management | Maintains clean heat transfer surfaces |
Ash fusion temperature monitoring | Prevents slagging and fouling |
→ Combining fuel control with automated combustion tuning yields the best outcomes.
In conclusion, biomass fuel type and moisture content are two of the most critical factors influencing combustion efficiency in biomass-fired boilers. High-moisture or high-ash fuels reduce flame temperature, increase flue gas loss, and impair complete combustion. To maintain high efficiency, it is essential to select low-moisture, energy-dense fuels (like wood pellets) or implement drying and control systems for variable-quality inputs. In biomass combustion, the fuel is not just fuel—it is a process variable that defines your energy performance.
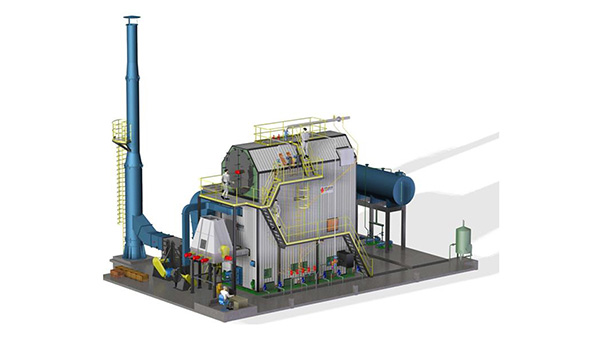
Why Is Fuel Particle Size and Uniformity Important for Stable Combustion?
Stable and efficient combustion in a biomass or coal-fired boiler depends on a wide range of variables—but fuel particle size and consistency are among the most influential. Whether you’re using wood chips, pellets, rice husk, or pulverized coal, inconsistent particle size can cause serious combustion issues. Fine particles ignite too quickly, generating flashback or smoke, while oversized chunks burn slowly or incompletely, creating cold spots, carbon monoxide (CO), and unburned carbon losses. Non-uniform fuel feed also results in flame instability, pressure fluctuations, fouling, and poor heat transfer. Uniformity ensures consistent burning rates, even air-fuel mixing, and balanced heat generation—cornerstones of boiler efficiency and emissions control.
Fuel particle size and uniformity are critical for stable combustion because they directly affect how consistently and completely the fuel burns. Uniform particle size allows for even distribution on the grate or in the combustion chamber, resulting in consistent flame shape, heat release, and air-fuel mixing. Irregular or oversized particles cause incomplete combustion, higher CO emissions, ash carryover, and flame instability. Consistent size also ensures smooth fuel feeding, reduces clinkering, and improves overall thermal efficiency.
Fuel that flows, ignites, and burns uniformly ensures that your boiler operates smoothly and cleanly.
Fuel particle size and uniformity play a vital role in maintaining stable combustion.True
Consistent particle size allows for uniform ignition, steady flame behavior, and complete combustion, reducing emissions and energy losses.
🔍 The Science Behind Particle Size and Combustion Behavior
Particle Size (mm) | Combustion Characteristic | Effect on Performance |
---|---|---|
<3 mm (fine dust) | Fast ignition, flashback risk | High CO, smoke, inconsistent heat |
3–15 mm (ideal) | Steady ignition and complete burn | Stable flame, high efficiency |
>20 mm (chunks) | Slow ignition, incomplete combustion | High unburned carbon, fouling, CO ↑ |
→ Fuels should be pre-processed to the optimal size range for the specific combustion system.
📏 Typical Fuel Size Requirements by System Type
Boiler Type | Ideal Fuel Size Range | Reason |
---|---|---|
Grate-fired biomass | 5–50 mm | Good distribution and burnout on grates |
Fluidized bed (FBC) | 1–6 mm | Prevents bed agglomeration, even mixing |
Pulverized coal system | <0.3 mm (300 microns) | Rapid ignition and high surface area |
Stoker-fired boiler | 10–25 mm | Consistent burn on slow-moving grate |
→ Deviations from these ranges lead to instability, incomplete combustion, or mechanical jamming.
🛠 How Size and Uniformity Affect Key Combustion Parameters
Combustion Factor | Effect of Inconsistent Fuel Size |
---|---|
Ignition Delay | Uneven timing = hot/cold zones, CO spikes |
Flame Shape | Non-uniform = pulsating, off-centered flame |
Air-Fuel Ratio | Uneven fuel = localized excess or deficiency |
Heat Release | Variable = steam pressure swings |
Ash Residue | Higher = fouling, slagging, unburned carbon |
→ These instabilities reduce both efficiency and reliability.
📊 Case Study – Wood Chip vs. Screened Pellet Performance
Fuel Type | Particle Size Uniformity | Flame Stability | CO (ppm) | Thermal Efficiency (%) |
---|---|---|---|---|
Raw wood chips | Poor (5–80 mm) | Unstable | 240 | 74.2 |
Screened pellets | High (6–8 mm) | Stable | 55 | 87.1 |
→ Uniform pellet size produced 40% lower CO and ~13% higher efficiency.
🔧 Operational Challenges with Irregular Fuel Size
Problem | Root Cause | Impact |
---|---|---|
Fuel feeder jamming | Large or sticky particles | Downtime and uneven load |
Grate overloading or clinkering | Large chunks or high fines | Local overheating, slagging |
CO or flame-out alarms | Rapid burn of fines or cold fuel zones | Tripped systems, unsafe operation |
Ash carryover | Incomplete burn of large particles | More PM, strain on baghouse/ESP |
→ Mechanical and combustion issues increase maintenance and emissions risk.
🧪 Solutions for Fuel Size Optimization
Solution | Implementation Detail |
---|---|
Shredding/Chipping | Use biomass chipper to produce 20–50 mm chips |
Pelletizing | Converts fines and dust into uniform pellets |
Screening Systems | Remove oversize and fines before feeding |
Fuel Bunker Agitators | Prevent bridging and flow interruptions |
In-Line Crushers | Pulverize coal or biomass prior to combustion |
→ Equipment must be tailored to both fuel and boiler type.
📈 Efficiency Gains from Uniform Fuel Handling
Before Optimization | After Fuel Size Control |
---|---|
Steam Output = 9.2 TPH | Steam Output = 10.3 TPH |
CO = 210 ppm | CO = 70 ppm |
O₂ = 7.5% (excess) | O₂ = 4.0% |
Efficiency = 76.5% | Efficiency = 86.4% |
→ Uniform fuel = higher output, cleaner burn, and reduced fan/pollution control effort.
In conclusion, fuel particle size and uniformity are critical to achieving stable, complete, and efficient combustion in industrial boilers. Inconsistent fuel causes ignition issues, combustion instability, increased emissions, and equipment failures. Whether burning coal or biomass, selecting the right particle size and ensuring uniform feed gives you control over your flame—and your bottom line. In solid fuel combustion, consistency is not just quality—it’s performance.
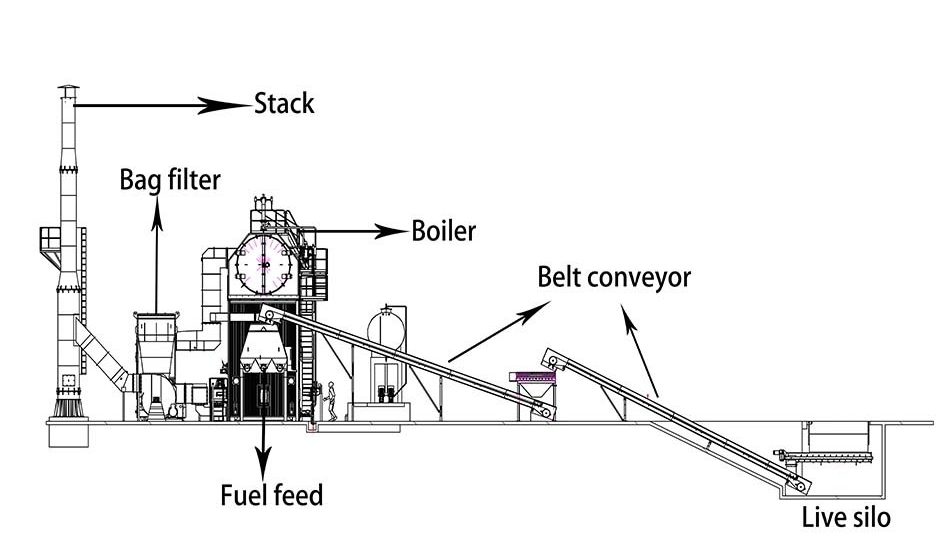
How Does Air Distribution and Excess Air Ratio Affect Combustion Quality?
Efficient and clean combustion doesn’t happen by chance—it depends on precisely how air is introduced and mixed with fuel. In solid, liquid, or gas-fired boilers, both the distribution of combustion air (primary, secondary, and tertiary) and the excess air ratio (air beyond theoretical requirements) determine how completely fuel is burned. Poor air distribution leads to local rich or lean zones, incomplete combustion, high CO, soot, and even flame instability. Too much excess air dilutes flame temperature and wastes energy in the flue gas. Too little, and you get smoke, CO, and unburned fuel. Getting this balance right is essential for stable combustion, low emissions, and high thermal efficiency.
Air distribution and excess air ratio affect combustion quality by controlling the oxygen availability and mixing within the furnace. Proper air distribution ensures that oxygen reaches all fuel particles at the right time and location for complete combustion, while the correct excess air ratio ensures a balance between minimizing CO and NOx emissions and maximizing efficiency. Insufficient air causes incomplete combustion and high CO; too much air lowers flame temperature and increases stack losses. Uniform and staged air introduction helps achieve stable flame, full burnout, and regulatory compliance.
In combustion control, how air enters matters just as much as how much enters.
Air distribution and excess air ratio are key factors in determining combustion quality and efficiency.True
Proper air mixing ensures full combustion while avoiding energy losses and emissions linked to too little or too much air.
🔍 Understanding Air Distribution in Combustion
Air Type | Function | Typical Introduction Location |
---|---|---|
Primary Air | Delivers air for initial ignition and drying | Below the fuel bed or burner |
Secondary Air | Aids in flame shaping and volatile burnout | Mid-furnace or above the bed |
Tertiary Air | Final burnout of CO and hydrocarbons | Near furnace exit or overfire |
Overfire Air (OFA) | Lowers NOx by staging combustion | Above flame zone |
→ Staged and well-distributed air flow supports complete combustion and emission control.
📏 Impact of Excess Air Ratio on Combustion Performance
Excess Air (%) | O₂ (%) | CO (ppm) | NOx (mg/Nm³) | Efficiency Impact |
---|---|---|---|---|
0–5% | <1% | >500 | Low | Incomplete combustion (CO↑) |
10–20% | 2.5–4.5% | <100 | Optimal | ✅ High efficiency zone |
>25% | >5.5% | <50 | High (thermal NOx↑) | Heat loss ↑, NOx↑ |
>40% | >7.5% | <20 | Moderate | Very inefficient |
→ A target excess air range of 10–20% is ideal for most boilers.
🔧 Combustion Quality Indicators Affected by Air Control
Indicator | What Poor Air Distribution Causes |
---|---|
CO Levels | Incomplete combustion in rich zones |
Flame Shape | Off-centered or unstable flame |
Unburned Carbon (UBC) | Residual fuel in ash or emissions |
Flue Gas O₂ | Too low = CO↑, too high = efficiency↓ |
NOx Formation | High flame temp from excess air → NOx↑ |
→ The best combustion occurs when air and fuel are uniformly and proportionally mixed.
📊 Example: Air Distribution Optimization in a Biomass Boiler
Condition | CO (ppm) | O₂ (%) | Stack Temp (°C) | Efficiency (%) |
---|---|---|---|---|
Poor air distribution (manual) | 280 | 6.8 | 245 | 74.2 |
Optimized primary/secondary air | 80 | 3.9 | 190 | 86.3 |
→ Better air distribution cut CO by 70% and improved efficiency by over 12%.
🧪 Case Study – Coal-Fired 30 TPH Boiler with OFA Retrofit
Initial Issue: High NOx (480 mg/Nm³), CO spikes, poor flame control
Diagnostics: Excess air at 25–30%, poor volatile burnout
Actions:
Installed overfire air ports
Staged secondary air and tuned primary airflow
Added real-time O₂/CO monitoring
Results:
NOx reduced to 240 mg/Nm³
CO < 60 ppm
Efficiency rose from 78.4% to 84.7%
🛠 Best Practices for Air Distribution and Excess Air Control
Practice | Benefit |
---|---|
Burner Air Register Adjustment | Optimizes swirl, flame shape |
Air Duct Balancing | Ensures uniform flow to multiple ports |
Use of Flow Nozzles or Dampers | Fine-tunes air per zone |
O₂ Trim Control System | Maintains optimal excess air dynamically |
Periodic Flame Imaging or IR | Identifies air starvation or oversupply |
→ Intelligent controls + proper ducting = clean, consistent combustion.
📈 Air Control Optimization and Performance Gains
Before Optimization | After Tuning Air Distribution |
---|---|
O₂ = 7.2% | O₂ = 3.8% |
CO = 220 ppm | CO = 55 ppm |
Unburned Carbon in Ash = 8% | 1.8% |
Boiler Efficiency = 75.2% | 85.5% |
→ Correct air distribution = better burnout, fewer emissions, and lower costs.
In conclusion, air distribution and excess air ratio are central to achieving high combustion quality, efficiency, and emissions compliance. Poor air control leads to energy waste, unburned fuel, high CO, and unstable operation. By distributing air in stages, tuning for the right excess, and monitoring flue gas in real-time, boilers can achieve a balanced flame, complete combustion, and optimal fuel use. In boiler operation, controlling how air flows is the key to making fuel burn its best.
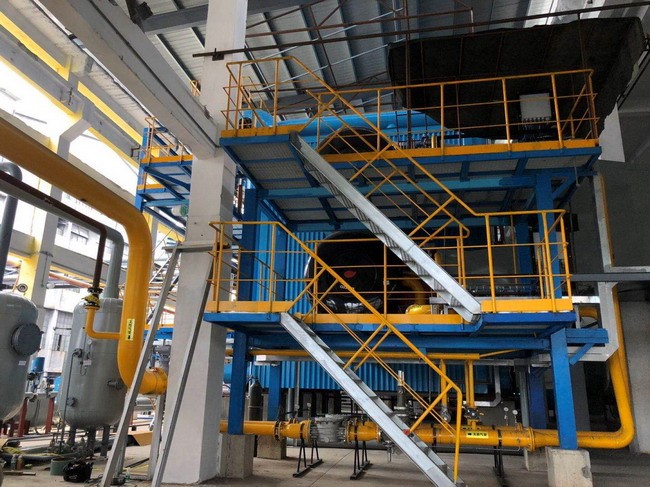
What Role Do Ash Content and Fouling Play in Reducing Heat Transfer Efficiency?
In biomass and coal-fired boiler systems, ash content and fouling are two major performance killers. When fuels contain high levels of mineral residue (ash), these non-combustible particles get carried by flue gases and deposit on internal heat exchange surfaces. Over time, these deposits form insulating layers—called fouling—on water walls, superheaters, economizers, and air preheaters. The result is reduced heat transfer from hot gases to steam or water, increasing flue gas temperatures, reducing steam output, and driving up fuel consumption. Additionally, excessive fouling can lead to corrosion, tube failure, and unplanned downtime. Effective fuel management and cleaning are essential to minimize these losses.
Ash content and fouling reduce heat transfer efficiency by forming insulating deposits on heat exchanger surfaces inside the boiler, which block the flow of thermal energy from the combustion gases to the steam or water. High-ash fuels produce more particulate matter that adheres to tubes, especially at high temperatures. These deposits increase the thermal resistance of heat transfer surfaces, raising flue gas temperatures and requiring more fuel to maintain output. If not cleaned regularly, fouling also leads to metal overheating, slagging, and mechanical failure.
Clean tubes mean better heat absorption—and lower fuel bills.
High ash content and fouling significantly reduce the thermal efficiency of steam boilers.True
Ash deposits act as an insulator, hindering heat transfer and forcing the system to consume more fuel to maintain steam output.
🔍 What Is Ash and How Does It Cause Fouling?
Parameter | Description |
---|---|
Ash Content (%) | Non-combustible mineral residue in fuel |
Fouling | Accumulation of ash/slag on heat exchanger surfaces |
Slagging | Molten ash forming crusts on furnace walls |
Sooting | Carbon-rich fouling from incomplete combustion |
→ Fouling acts like a thermal blanket on boiler surfaces—blocking heat transfer.
📏 Ash Content of Common Fuels
Fuel Type | Typical Ash (%) | Fouling Risk | Comments |
---|---|---|---|
Wood Pellets | 0.5–1.5 | Low | Clean combustion, minimal fouling |
Wood Chips | 1–3 | Low–Moderate | Depends on bark and moisture content |
Rice Husk | 15–20 | High | Very fine ash, silica-related fouling |
Coal (Bituminous) | 10–25 | High | Heavy ash loading and fouling |
Straw and RDF | 8–15 | Moderate–High | Variable ash behavior |
→ High-ash fuels require more cleaning, stronger fans, and durable surfaces.
📊 Impact of Fouling on Heat Transfer Efficiency
Ash Layer Thickness | Effect on Heat Transfer (%) | Fuel Use Increase (%) |
---|---|---|
0.1 mm | ↓ 5–8% | ↑ 2–3% |
0.5 mm | ↓ 15–20% | ↑ 5–7% |
1.0 mm | ↓ >30% | ↑ 10–15% |
→ Even thin ash layers can cost thousands in wasted fuel annually.
🧪 Case Study – Rice Husk Boiler Fouling Impact
Fuel: Rice husk (17% ash), 10 TPH fluidized bed boiler
Symptoms:
Flue gas temperature rose from 195°C to 255°C
CO emissions increased
Steam output dropped by 12%
Findings:
Economizer and superheater coated with 1.2 mm of ash
UBC (unburned carbon) in ash = 7.5%
Action:
Manual offline cleaning
Upgraded soot blowers to high-pressure air
Added ash softening additive (kaolin)
Result:
Flue gas temp dropped to 200°C
Steam output restored to 10.2 TPH
Efficiency rose from 74.2% to 83.8%
🛠 Fouling-Prone Areas in Industrial Boilers
Component | Fouling Type | Cleaning Required |
---|---|---|
Furnace Walls | Slagging, soot | Mechanical scraping, air jets |
Superheater Tubes | Silica, alkali ash | Soot blowers, thermal cleaning |
Economizer | Dense ash, fly ash | Hydroblasting, manual brushing |
Air Preheater | Tar and sticky ash | Offline steam or air cleaning |
Water-side (scale) | Calcium/Mg fouling | Chemical descaling |
→ These areas must be monitored via ΔP, stack temp, and visual inspection.
📈 Flue Gas Temperature vs. Fouling Severity
Flue Gas Temp (°C) | Indicated Condition | Efficiency Impact |
---|---|---|
180–200 | Clean heat transfer | ✅ Optimal zone |
220–240 | Moderate fouling present | ↓ Efficiency 3–7% |
>260 | Severe fouling/blockage | ↓ Efficiency ≥10% |
→ Rising stack temps = thermal red flag.
🔧 Maintenance Best Practices to Combat Fouling
Maintenance Task | Frequency | Purpose |
---|---|---|
Online Soot Blowing | Daily/automatic | Keeps tubes clear of dry ash |
Offline Tube Cleaning | Monthly/quarterly | Removes hardened deposits |
Ash Monitoring (UBC, texture) | Weekly | Indicates combustion/fouling issues |
Flue Gas Analysis (O₂, CO) | Continuous | Detects combustion imbalance |
Stack Temperature Logging | Daily | Tracks fouling and thermal trends |
→ Combining monitoring + cleaning maintains long-term efficiency.
📋 Fouling Prevention Techniques
Strategy | Efficiency Benefit |
---|---|
Fuel Selection (low ash) | Reduces deposit volume |
Additives (kaolin, dolomite) | Raise ash fusion point → fewer clinkers |
Air-Fuel Optimization | Complete burn reduces soot and CO |
Grate/Furnace Design | Improves ash discharge, prevents bridging |
Automated Cleaning Systems | Sustains performance with minimal downtime |
→ Prevention is cheaper than fuel loss or unplanned shutdowns.
In conclusion, ash content and fouling are leading causes of heat transfer loss in solid fuel-fired boiler systems. High-ash fuels generate heavy deposits that insulate heat exchanger surfaces, forcing boilers to consume more fuel to meet demand. Left unchecked, this leads to skyrocketing flue temperatures, falling efficiency, and mechanical degradation. To combat this, fuel selection, regular cleaning, and real-time performance monitoring must be built into the operation strategy. In high-efficiency combustion, clean surfaces mean clean performance.
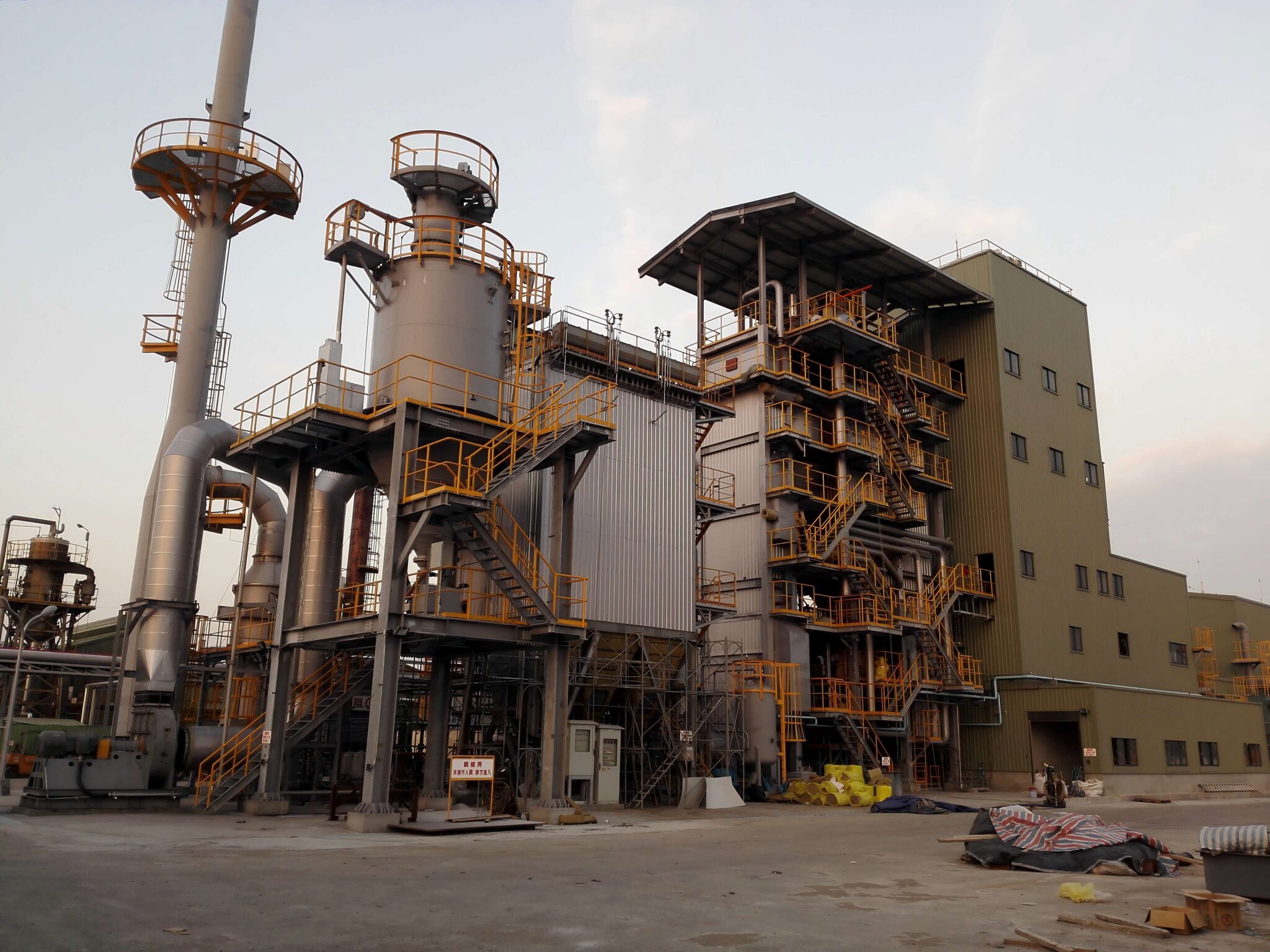
How Do Combustion Temperature and Flue Gas Characteristics Influence Thermal Performance?
In any steam boiler system, combustion transforms fuel into thermal energy. But how efficiently that transformation occurs depends heavily on combustion temperature and flue gas characteristics. The higher and more stable the flame temperature, the more heat is transferred into the working fluid—provided that the boiler is designed to capture it. On the other hand, the composition and volume of the flue gases dictate how much heat is retained or lost through the stack. When combustion temperatures are too low, incomplete burning leads to high CO, unburned carbon, and reduced steam output. If they’re too high, you risk NOx formation, slagging, and damage to furnace tubes. Similarly, the wrong flue gas balance can result in excessive heat loss, low efficiency, and poor regulatory performance.
Combustion temperature and flue gas characteristics influence thermal performance by determining how much usable heat is released and retained during the combustion process. An optimal combustion temperature ensures complete fuel burnout and effective radiant heat transfer, while flue gas composition and temperature indicate how much energy is lost through the stack. High excess air or unburned CO reduces efficiency, whereas stable flame temperatures and controlled gas chemistry maximize thermal output and fuel economy. Properly managed, these factors directly translate into high boiler efficiency and reduced emissions.
Getting the flame and flue gas right means getting the most out of every fuel unit.
Combustion temperature and flue gas composition directly influence boiler thermal efficiency and heat recovery performance.True
These parameters control how efficiently fuel energy is converted into steam and how much is lost in the exhaust.
🔍 Combustion Temperature: The Heart of Thermal Performance
Parameter | Typical Range | Thermal Impact |
---|---|---|
Flame Temperature | 1,100–1,600°C | Primary source of radiant heat |
Combustion Zone Uniformity | Critical for heat distribution | Prevents cold spots and slagging |
High Temp (>1450°C) | Increases NOx, slagging risk | Efficiency drops due to fouling |
Low Temp (<950°C) | Leads to incomplete burn, CO ↑ | Less steam output, more fuel used |
→ Ideal combustion temp = hot enough for complete burn, cool enough to protect surfaces.
📏 Flue Gas Characteristics and Their Impact
Flue Gas Parameter | Effect on Thermal Performance |
---|---|
Temperature | High values = more heat lost in exhaust |
O₂ (%) | Excess O₂ means excess air → stack losses ↑ |
CO (ppm) | High CO = incomplete combustion = efficiency ↓ |
CO₂ (%) | Higher = better combustion = higher efficiency |
H₂O (gaseous moisture) | Absorbs heat = latent loss in stack gas |
→ Flue gas is both a diagnostic tool and a major efficiency variable.
📊 Example – Combustion and Flue Gas vs. Boiler Efficiency
Flame Temp (°C) | O₂ (%) | CO (ppm) | Stack Temp (°C) | Thermal Efficiency (%) |
---|---|---|---|---|
1250 | 4.2 | 75 | 185 | 87.2 |
1150 | 6.5 | 190 | 225 | 78.5 |
1050 | 7.8 | 320 | 260 | 71.0 |
→ A 200°C flame temperature drop can reduce efficiency by 15–20%.
🔧 Interplay of Combustion and Flue Gas in Heat Transfer
System Component | Temperature/Gas Role | Efficiency Impact |
---|---|---|
Furnace Zone | Flame radiates heat → boiler tubes | High flame temp = max radiant gain |
Superheater | Sensitive to ash from hot gases | Fouling reduces superheat efficiency |
Economizer | Uses flue gas to preheat feedwater | Cooler gas = better recovery |
Air Preheater | Recovers stack gas heat to warm air | Reduces combustion fuel demand |
→ Every stage depends on hot, well-composed flue gas to recover energy.
🧪 Case Study – Natural Gas Boiler with Flue Gas Analysis
Issue: Fuel cost rise, declining output
Findings:
Flue gas O₂ = 8.0%
Flame temp = 1050°C
CO = 230 ppm
Stack temp = 240°C
Interventions:
Adjusted excess air to reduce O₂ to 3.6%
Burners reoriented for better flame coverage
Installed O₂ trim control system
Results:
Flame temp = 1280°C
CO < 70 ppm
Stack temp = 185°C
Efficiency improved from 77.6% → 89.2%
📈 Heat Loss Contribution of Flue Gas
Source of Loss | % of Input Energy (Typical) | How It Relates to Temperature/Gas |
---|---|---|
Dry Flue Gas Loss | 5–15% | Higher stack temp = more loss |
Excess Air Loss | 3–10% | More air = more exhaust volume |
Latent Moisture Loss | 2–6% | High fuel moisture increases stack humidity |
Unburned Combustibles (CO) | 1–4% | Poor combustion = energy left in CO |
→ Managing flue gas saves up to 25% of fuel energy.
🔍 Best Practices for Optimizing Combustion and Flue Gas
Action | Effect on Thermal Performance |
---|---|
Burner Tuning (flame shape, swirl) | Ensures even temp, avoids hot/cold zones |
Excess Air Control (O₂ Trim) | Reduces stack losses, CO, NOx |
Fouling Monitoring | Prevents temp rise from dirty surfaces |
Stack Temperature Monitoring | Real-time heat loss indicator |
Condensate Recovery + Economizer | Extracts max heat from exhaust |
→ These actions tie flame quality to energy output and regulatory compliance.
In conclusion, combustion temperature and flue gas characteristics are fundamental to thermal performance in steam boiler systems. A stable, high-temperature flame ensures complete combustion and effective heat release, while flue gas temperature and chemistry reveal how much energy is retained or lost. Managing these parameters through intelligent control and maintenance is key to maximizing efficiency, reducing emissions, and minimizing fuel costs. In combustion, what leaves the stack tells the story of how well the fire burned.
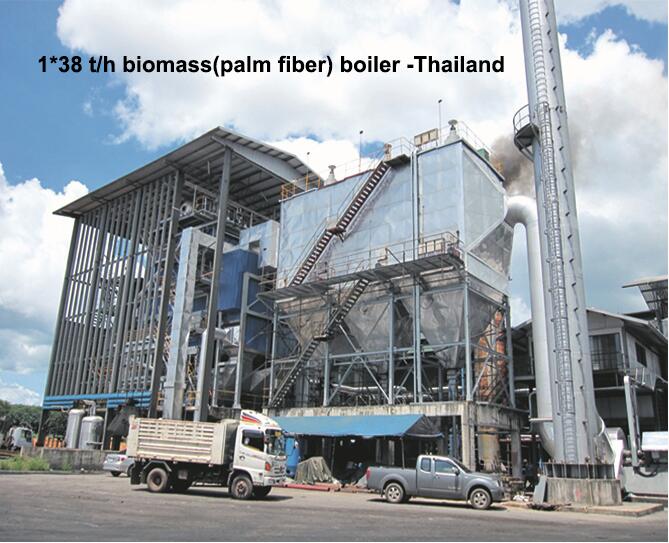
What Maintenance Practices Are Necessary to Sustain High Efficiency in Biomass Boilers?
Biomass boilers promise renewable energy and lower carbon footprints—but only if their efficiency is maintained over time. Unlike fossil fuels, biomass has variable ash content, higher moisture, and more volatile combustion behavior. These factors lead to accelerated fouling, corrosion, slagging, and ash buildup, all of which hinder heat transfer and increase fuel consumption. If maintenance is neglected, performance drops rapidly, emissions spike, and unplanned shutdowns become frequent. To protect your investment and ensure sustainable performance, a systematic, preventive, and performance-based maintenance plan is essential for biomass boiler operation.
Sustaining high efficiency in biomass boilers requires a comprehensive maintenance routine that includes regular soot blowing, ash removal, combustion tuning, fuel system inspection, water-side cleaning, and flue gas monitoring. These practices prevent fouling, slagging, and inefficiencies caused by biomass’s high ash and moisture characteristics. Real-time diagnostics, periodic performance audits, and cleaning of heat transfer surfaces ensure that the boiler operates close to its design efficiency, reduces emissions, and avoids costly downtime.
In biomass systems, efficiency is not set once—it is sustained daily through disciplined maintenance.
Routine maintenance is essential to maintain high thermal efficiency in biomass boiler systems.True
Biomass fuels introduce ash, fouling, and moisture challenges that require regular cleaning, combustion tuning, and system checks to prevent efficiency loss.
🔍 Key Challenges in Biomass Boiler Maintenance
Maintenance Challenge | Biomass-Related Cause | Efficiency Risk |
---|---|---|
Ash Fouling | High ash content (e.g., rice husk, straw) | Insulates heat surfaces → losses ↑ |
Slagging and Clinkers | Low ash fusion temp fuels (e.g., straw) | Blocks air flow, heat transfer ↓ |
Soot Buildup | Incomplete combustion of fines or moisture | Reduces radiant heat transfer |
Fuel Feed Blockage | Uneven particle size or bridging | Load instability, CO ↑ |
Corrosion | Acidic flue gas with high HCl, SO₂ | Tube thinning and efficiency loss |
→ Maintenance must directly address these biomass-specific challenges.
📏 Biomass Boiler Maintenance Schedule (Best Practice)
Maintenance Task | Frequency | Performance Benefit |
---|---|---|
Soot Blowing (online) | Daily/shift-wise | Removes ash and soot from heat surfaces |
Manual Tube Cleaning | Monthly/quarterly | Restores fouled superheaters/economizers |
Fuel Feeder and Silo Inspection | Weekly | Prevents jamming, maintains stable flow |
Ash Handling System Check | Weekly | Avoids hopper clogging and pressure rise |
Burner and Air Damper Tuning | Monthly | Maintains optimal air-fuel ratio |
Water-Side Descaling | Biannually | Prevents scaling, preserves heat transfer |
Flue Gas Analyzer Calibration | Monthly | Ensures accurate efficiency readings |
Performance Audit (CO, O₂, ΔT) | Quarterly | Tracks losses, plans predictive actions |
→ A predictive + preventive hybrid approach delivers best results.
📊 Case Study – 12 TPH Rice Husk Biomass Boiler
Metric | Before Maintenance | After Maintenance |
---|---|---|
Flue Gas Temp (°C) | 260 | 185 |
Stack O₂ (%) | 7.2 | 3.9 |
CO (ppm) | 210 | 60 |
Ash in Superheater Tubes | 1.5 mm | Cleaned |
Efficiency (%) | 73.6 | 86.1 |
→ Routine cleaning and tuning restored 12.5% efficiency and reduced emissions.
🛠 Maintenance Tools and Systems for Biomass Efficiency
Tool/System | Role in Maintenance |
---|---|
Online Soot Blowers | Automated ash cleaning during operation |
Infrared Cameras | Detect cold spots, fouling zones |
Flue Gas Analyzer | Measures CO, O₂, NOx → combustion diagnostics |
Vibration Monitoring | Detects feeder and blower wear |
Stack Temp Logger | Indicates fouling buildup through ΔT trends |
Smart SCADA/PLC Alarms | Triggers cleaning cycles or alerts on performance |
→ Smart maintenance uses data to drive intervention.
📈 Efficiency Losses Without Proper Maintenance
Issue | Efficiency Loss (%) | Root Maintenance Failure |
---|---|---|
1.5 mm of ash on tubes | 10–15% | Missed soot blowing |
Excess O₂ > 6% | 3–6% | Untuned dampers/burner |
Fuel flow inconsistency | 4–8% | Silo bridging not resolved |
High boiler blowdown | 2–5% | No water quality management |
Stuck air preheater seals | 3–7% | Missed mechanical inspection |
→ Maintenance gaps compound quickly into fuel and cost losses.
🔧 Preventive Maintenance Strategy for Biomass Boilers
Strategy | Implementation |
---|---|
Schedule-based cleaning | Calendar for tubes, preheater, filters |
Condition-based alerts | Trigger soot blowing on ΔT or CO spike |
Spare parts planning | Stock grates, nozzles, blowers to avoid downtime |
Root cause failure tracking | Logs linked to fuel condition and operation data |
Staff training | Maintenance team trained in biomass boiler specifics |
→ The goal is zero unplanned shutdowns + sustained high output.
🧪 Performance Indicators for Maintenance Planning
KPI | Threshold | Maintenance Insight |
---|---|---|
Flue Gas Temp (°C) | >200 | Indicates fouling or excess air |
CO (ppm) | >100 | Poor combustion, soot or clogging |
Steam-to-Fuel Ratio | Dropping trend | Efficiency loss, check surfaces |
Stack ΔP (mmWC) | Rising over time | Economizer blockage or ash buildup |
O₂ (%) | >5.5% continuously | Damper tuning or air leaks |
→ These KPIs guide when and where to maintain, not just what to maintain.
In conclusion, biomass boilers require consistent and targeted maintenance practices to maintain high thermal efficiency. Ash and fouling tendencies from variable fuels demand that operators clean, monitor, and tune their systems more frequently than fossil fuel systems. From fuel feed to flue gas, each part of the boiler needs attention to prevent degradation. Efficient biomass combustion isn’t just about good fuel—it’s about ongoing care and operational discipline.
🔍 Conclusion
The efficiency of an industrial biomass boiler depends on carefully balancing fuel characteristics, combustion control, and heat exchange dynamics. Moisture-rich fuels, poor air management, or ash buildup can quickly erode combustion stability and thermal output. By optimizing these key variables, operators can maximize energy conversion, reduce emissions, and extend equipment life—turning biomass into a clean, efficient, and economically viable heat source.
📞 Contact Us
💡 Want to boost the efficiency of your biomass boiler system? Our team offers fuel analysis, combustion tuning, heat transfer audits, and full system optimization to help you get the most out of your biomass fuel.
🔹 Connect with us today to ensure your biomass boiler runs clean, hot, and efficient! 🌿🔥📈
FAQ
How does fuel moisture content impact efficiency in biomass boilers?
High moisture content significantly reduces combustion efficiency. More energy is consumed evaporating water before combustion occurs, lowering the effective heat output and increasing flue gas losses. Optimal biomass fuels have moisture levels below 20%.
What role does biomass fuel type and consistency play in combustion efficiency?
Different biomass fuels—wood chips, pellets, agricultural waste—vary in calorific value, ash content, and volatile matter. Inconsistent fuel size or energy content leads to unstable combustion, uneven heat distribution, and efficiency losses.
How does combustion system design influence efficiency?
Efficient combustion depends on proper air-fuel mixing, grate design, and residence time. Moving grates, fluidized beds, and staged air systems help ensure complete combustion and higher thermal output with minimal unburned material.
What factors affect heat transfer performance in biomass boilers?
Heat transfer efficiency is influenced by:
Boiler surface area and material conductivity
Ash and soot deposition on tubes
Steam/water circulation rates
Flue gas temperature
Regular soot blowing and maintenance of heat exchange surfaces are critical to maintaining high thermal efficiency.
How can combustion and heat transfer efficiency be improved in biomass systems?
Use well-dried, uniform biomass fuels
Optimize air-to-fuel ratios with oxygen trim controls
Implement automated cleaning systems for boiler tubes
Monitor flue gas composition to fine-tune combustion
Design boilers for fuel-specific combustion characteristics
References
Biomass Combustion and Boiler Efficiency – https://www.energy.gov
Effect of Moisture on Biomass Boiler Performance – https://www.sciencedirect.com
Fuel Quality and Combustion Control – https://www.researchgate.net
Boiler Design for Biomass Heat Transfer – https://www.bioenergyconsult.com
Ash Fouling in Biomass Boilers – https://www.epa.gov
Staged Combustion and Air Distribution – https://www.mdpi.com
Soot Blower Operation in Biomass Plants – https://www.energysavingtrust.org.uk
Optimizing Biomass Boiler Efficiency – https://www.iea.org
Combustion System Design Principles – https://www.automation.com
Industrial Boiler Thermal Performance – https://www.asme.org
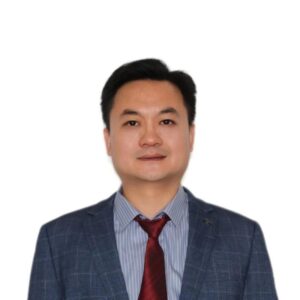