Industrial gas-fired boilers are known for their high combustion efficiency, clean emissions, and rapid heat generation. However, to truly realize their cost-saving and environmental benefits, operators must routinely assess thermal efficiency—a key performance indicator that reflects how effectively the boiler converts fuel into usable heat. Neglecting this evaluation can lead to hidden energy losses, higher gas consumption, and unnecessary CO₂ emissions. Measuring thermal efficiency helps maintain optimal operation and long-term reliability.
Thermal efficiency of an industrial gas-fired boiler is calculated as the ratio of useful heat output (in the form of steam or hot water) to the total energy input from natural gas or other gaseous fuels. This can be done using the Direct Method (based on fuel input and heat output) or the Indirect Method (based on accounting for individual heat losses). Accurate measurement requires data on fuel consumption, steam production, flue gas composition, excess air, and combustion temperatures.
Let’s explore how to correctly measure thermal efficiency and use it to optimize boiler performance.

What Is Thermal Efficiency and Why Is It Important for Gas-Fired Boilers?
Gas-fired boilers are widely used in industries for their reliability, lower emissions, and high combustion control—but what truly defines their performance is thermal efficiency. In practical terms, it tells us how effectively a boiler converts the chemical energy in natural gas into useful heat (steam or hot water) without wasting it as flue gas or surface radiation. A boiler that burns expensive fuel but only converts half of it into usable energy is not just inefficient—it’s costly, environmentally unfriendly, and unsustainable.
Thermal efficiency in gas-fired boilers refers to the ratio of useful heat output (in the form of steam or hot water) to the total fuel energy input. It indicates how effectively the boiler converts fuel energy into productive thermal energy. High thermal efficiency means more of the fuel’s energy is used, resulting in lower fuel consumption, reduced operating costs, and lower emissions.
For gas-fired systems, especially those operating continuously or at high load, thermal efficiency is not just a metric—it’s a business driver.
Thermal efficiency determines how effectively a gas-fired boiler converts fuel energy into usable heat.True
A boiler with high thermal efficiency consumes less fuel and emits less CO₂ to produce the same amount of steam.
🔍 How Thermal Efficiency Is Measured (Without Complex Formulas)
While traditional efficiency calculations use enthalpy or calorific value equations, here’s a non-mathematical breakdown:
Fuel Energy Input: Measured by how much natural gas is burned per hour (e.g., cubic meters or BTUs).
Useful Heat Output: Measured by how much steam is generated and at what temperature/pressure.
Thermal Efficiency: Tells you how much of the input fuel was actually used to make the steam, versus lost to the environment.
📊 Typical Thermal Efficiency Values for Gas-Fired Boilers
Boiler Type | Typical Efficiency (%) | Notes |
---|---|---|
Conventional Gas Boiler | 80–88% | Non-condensing, older models |
High-Efficiency Condensing Boiler | 92–98% | Recovers latent heat from flue gases |
Fire-Tube Boiler | 82–90% | Used in small to mid-size process steam systems |
Water-Tube Boiler | 85–92% | Higher pressure and capacity |
Modular Condensing Units | 94–98% | Used for building heating or low-pressure needs |
High-efficiency systems like condensing boilers reduce gas usage significantly, especially when return water temperatures are low.
🛠️ Why Thermal Efficiency Is Critically Important
Reason | Impact on Operation and Business |
---|---|
Fuel Cost Savings | Higher efficiency = less gas used |
Lower CO₂ Emissions | More energy output per unit of fuel |
Better ROI | Efficient systems recover investment faster |
Regulatory Compliance | Meets energy performance targets |
System Longevity | Efficient combustion reduces wear and tear |
Eligible for Incentives | High-efficiency systems qualify for subsidies |
For every 1% increase in thermal efficiency, fuel costs can drop by 1.5–2% annually, depending on plant size and runtime.
🧪 Case Study: Food Processing Plant, 12 TPH Gas-Fired Boiler
Initial Efficiency: 83% (fire-tube, 15 years old)
Upgraded System: Condensing water-tube boiler with economizer
Post-Upgrade Efficiency: 95.2%
Gas Savings: 112,000 m³/year
Annual Savings: ~$47,500
CO₂ Reduction: 230 metric tons/year
Payback Period: 1.9 years
🔧 Strategies to Improve Thermal Efficiency
Strategy | Efficiency Gain Potential | Description |
---|---|---|
Install Economizer | +2–5% | Recovers heat from flue gases |
Use Condensing Boiler | +5–10% | Recovers latent heat from exhaust |
O₂ Trim Controls | +1–2% | Optimizes air-fuel ratio for combustion |
Insulate Boiler Surfaces | +1–3% | Reduces radiation and convection losses |
Blowdown Heat Recovery | +0.5–2% | Recovers heat from boiler blowdown water |
Burner Tuning & Maintenance | +1–4% | Ensures optimal flame and combustion control |
These upgrades may be incremental, but together they can transform a boiler into a high-performance, low-emission asset.
In conclusion, thermal efficiency is the key performance indicator for any gas-fired boiler system, directly affecting fuel costs, carbon footprint, and system viability. As gas prices and environmental regulations tighten, achieving and maintaining high thermal efficiency becomes not just important—but essential. For engineers, managers, and sustainability officers alike, thermal efficiency is the number to watch, optimize, and protect.
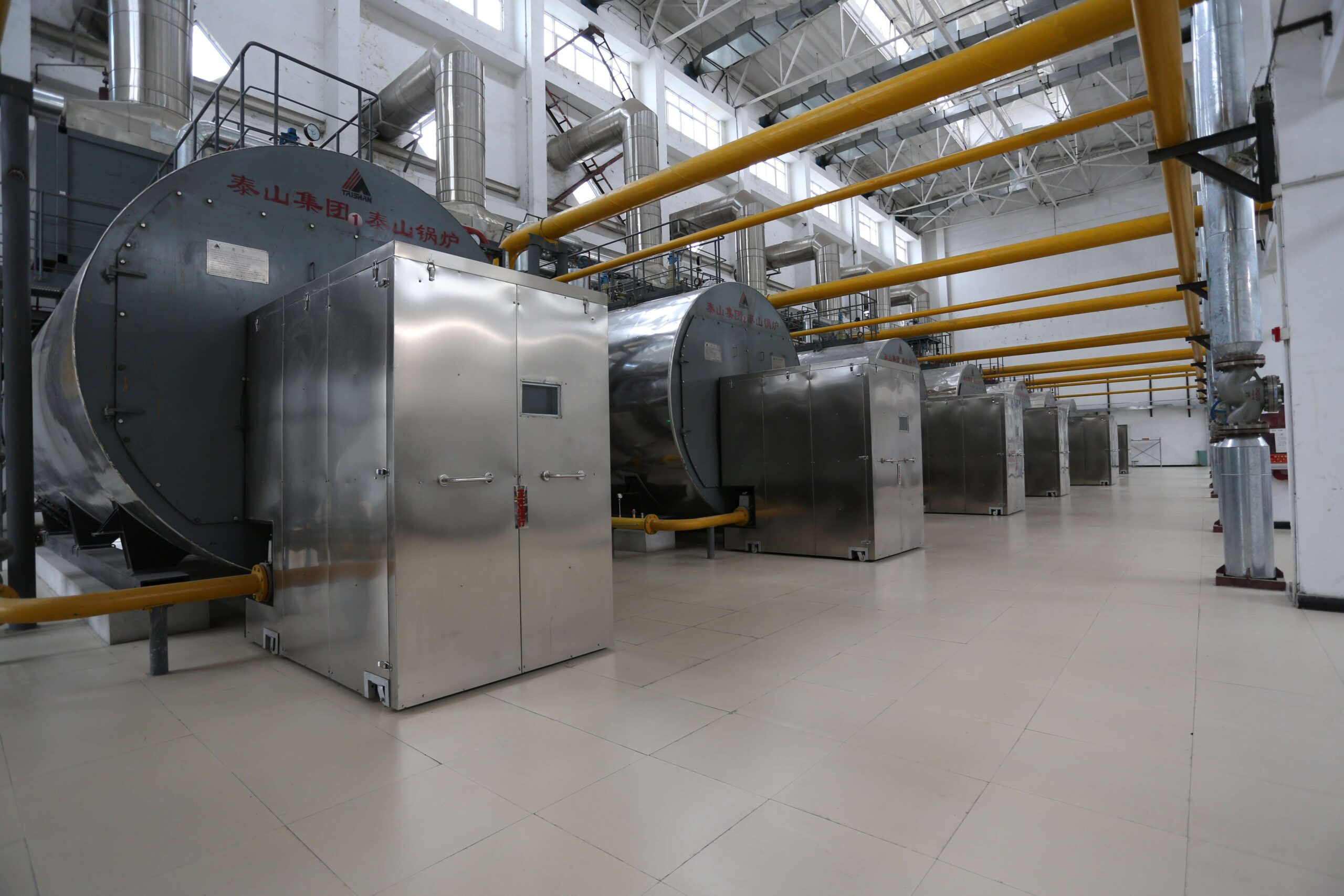
How Is the Direct Method Used to Calculate Boiler Efficiency?
When it comes to evaluating boiler performance, the Direct Method is often the preferred starting point. It’s simple, fast, and gives a reasonably accurate picture of how well your boiler is converting fuel energy into steam. This method is especially useful during on-site energy audits, maintenance checks, or performance benchmarking. It’s commonly used by industries, energy managers, and boiler inspectors due to its ease of use—no complex heat loss breakdowns or theoretical modeling required.
The Direct Method calculates boiler efficiency by comparing the useful heat output (steam generation) directly to the heat input (fuel energy consumed) over a set period. It is calculated using measured steam output, feedwater temperature, and fuel consumption rate. This method helps quickly determine how efficiently a boiler is operating and is useful for identifying underperformance or justifying upgrades.
It provides a practical efficiency percentage that tells operators how much of their fuel cost is going into producing usable steam—and how much is being wasted.
The Direct Method calculates boiler efficiency by comparing steam output energy to fuel input energy.True
This method uses straightforward measurements like fuel consumption and steam generation to determine how efficiently fuel is converted into heat.
🔍 What the Direct Method Measures
Component | Description |
---|---|
Fuel Energy Input | Energy available from the fuel consumed |
Steam Energy Output | Energy delivered in the form of steam |
Boiler Efficiency (%) | Ratio of output energy to input energy |
Instead of identifying individual heat losses (like in the Indirect Method), this approach calculates efficiency directly from input and output data.
📋 Required Data for Direct Method
Parameter | How It’s Measured |
---|---|
Fuel Consumption Rate | kg/hr (solid), m³/hr (gas), or L/hr (liquid) |
Fuel Calorific Value | kcal/kg or MJ/kg (lab-tested) |
Steam Flow Rate | kg/hr (measured via steam flow meter) |
Steam Pressure | bar(g) (needed to estimate steam enthalpy) |
Feedwater Temperature | °C (measured at economizer inlet or tank) |
🔧 Direct Method Efficiency Calculation – Step-by-Step (Without Equations)
Measure the steam flow rate: Use a calibrated steam flow meter to record how much steam is produced per hour.
Determine the heat content of the steam: Use a steam table to find the heat value based on pressure and temperature.
Measure the feedwater temperature: This gives the baseline from which the boiler must heat the water.
Calculate the heat gain per kg of steam: Subtract the feedwater enthalpy from the steam enthalpy.
Multiply by the steam flow: This gives total useful heat output per hour.
Measure fuel consumption: Record the quantity of fuel burned over the same hour.
Use calorific value of the fuel: Get the energy value of the fuel (tested via a bomb calorimeter).
Multiply fuel used by CV: Gives total energy input.
Compare output to input: Divide steam energy output by fuel energy input to get efficiency percentage.
📊 Example: Natural Gas-Fired Boiler (5 TPH)
Parameter | Value |
---|---|
Steam output | 5,000 kg/hr |
Steam pressure (saturated) | 10 bar |
Steam enthalpy | ~665 kcal/kg |
Feedwater temperature | 85°C |
Feedwater enthalpy | ~85 kcal/kg |
Fuel (Natural Gas) consumption | 400 m³/hr |
Calorific value of natural gas | 8,500 kcal/m³ |
Useful heat output = (665 – 85) × 5,000 = 2,900,000 kcal/hr
Fuel input = 400 × 8,500 = 3,400,000 kcal/hr
Efficiency = 2,900,000 / 3,400,000 = 85.3%
This tells us that 85.3% of the gas energy is used to make steam, while 14.7% is lost through flue gas, radiation, and other inefficiencies.
✅ Advantages of the Direct Method
Benefit | Description |
---|---|
Simple and fast | Requires only basic data and tools |
No need for flue gas analysis | Unlike Indirect Method |
Practical and field-friendly | Ideal for routine checks and quick audits |
Good accuracy for stable loads | Especially useful for gas and oil-fired units |
⚠️ Limitations of the Direct Method
Limitation | Why It Matters |
---|---|
No breakdown of losses | Cannot identify where energy is being lost |
Affected by measurement errors | Inaccurate meters or CV values affect result |
Not suitable for transient loads | Best used under steady-state operation |
For troubleshooting, it’s often paired with the Indirect Method to identify specific causes of inefficiency.
In conclusion, the Direct Method is a reliable, fast, and practical approach to calculating boiler efficiency, especially for gas-fired boilers. It gives operators an instant snapshot of performance, helping them evaluate operational health, identify declining trends, or validate the benefits of an upgrade. For businesses aiming to reduce energy costs and emissions, the Direct Method is the first—and most accessible—tool in the boiler performance toolbox.

What Is the Indirect Method and How Does It Identify Heat Losses?
While the Direct Method provides a quick snapshot of boiler performance, it doesn’t tell why efficiency is high or low. That’s where the Indirect Method becomes essential. Often referred to as the Heat Loss Method, it dives deeper by calculating all measurable losses in the system and subtracting them from 100%. This gives not only the efficiency but also actionable insights into where energy is being wasted—such as hot flue gases, unburned fuel, or radiation. It’s the preferred method for in-depth energy audits, boiler tuning, and diagnostic optimization.
The Indirect Method calculates boiler efficiency by measuring and summing all identifiable heat losses—such as dry flue gas loss, moisture loss, radiation loss, and unburnt fuel loss—and subtracting their total from 100%. This approach not only determines overall efficiency but also pinpoints specific inefficiencies, helping engineers optimize combustion settings, insulation, and heat recovery.
Unlike the Direct Method, this technique explains why your efficiency is not 100%, and what you can do to improve it.
The Indirect Method measures individual heat losses to determine boiler efficiency and identify energy waste points.True
By analyzing flue gas composition, temperature, and combustion conditions, the Indirect Method reveals where energy is lost, offering more diagnostic value than the Direct Method.
🔧 Main Heat Losses Identified by the Indirect Method
Heat Loss Type | Description |
---|---|
Dry Flue Gas Loss | Heat carried away by hot exhaust gases |
Moisture Loss (from fuel & air) | Heat used to evaporate water in fuel and combustion air |
Hydrogen Combustion Loss | Heat lost in forming water vapor from fuel’s hydrogen content |
Radiation and Convection Loss | Heat radiated from boiler shell and pipes |
Unburnt Combustibles (in ash or gas) | Energy lost in unburned fuel or carbon monoxide |
Blowdown Loss | Heat loss in draining high-temperature boiler water |
All these losses are estimated using measured parameters like flue gas temperature, oxygen content, and fuel composition.
🧾 Parameters Required for Indirect Method
Parameter | Purpose |
---|---|
Flue Gas Temperature | Calculates dry gas and latent heat loss |
Ambient Air Temperature | Affects flue gas loss calculation |
Oxygen (O₂) or CO₂ in Flue Gas | Determines excess air and gas composition |
Fuel Composition | Needed to estimate hydrogen, moisture, and ash |
Fuel Calorific Value (CV) | Basis for all loss calculations |
Carbon in Ash (for solid fuels) | Calculates unburnt fuel loss |
CO in Flue Gas | Indicates incomplete combustion (optional) |
This method requires combustion analyzers, temperature probes, and accurate fuel data for reliable results.
📊 Typical Heat Loss Breakdown in a Gas-Fired Boiler (85% Efficiency)
Heat Loss Type | % Heat Lost | Improvement Potential? |
---|---|---|
Dry Flue Gas Loss | 5–8% | Yes – via economizer/flue recovery |
Moisture from H₂ in Fuel | 4–6% | No (inherent to gas combustion) |
Radiation & Convection Loss | 1–2% | Yes – via insulation |
Excess Air Loss (linked to O₂) | 2–4% | Yes – via air trim controls |
Unburnt Gas Loss (if any) | 0.1–1% | Yes – burner tuning |
Total Losses | ~15% |
→ Efficiency = 100% − total losses = ~85%
🧪 Case Study: Energy Audit Using Indirect Method
Boiler: 6 TPH natural gas-fired, operating 18 hrs/day
Measured O₂ in flue gas: 6.2%
Flue gas temp: 220°C
Ambient temp: 30°C
Dry flue gas loss: 7.1%
Moisture (H₂ combustion): 5.2%
Radiation & convection: 1.5%
Total losses: 13.8%
Calculated efficiency: 86.2%
Actions Taken:
Added O₂ trim system
Installed condensing economizer
Insulated steam headers
New measured losses: 10.1%
Improved efficiency: 89.9%
Fuel savings: 9.5% (~$24,000/year)
🔍 Why Use the Indirect Method?
Advantage | Description |
---|---|
Diagnostic Power | Shows where energy is lost, not just how much |
Better for Optimization | Enables targeted efficiency improvements |
Detailed Regulatory Reporting | Used for ISO 50001 and compliance audits |
Suitable for Any Fuel Type | Gas, coal, biomass, or oil |
Backed by International Standards | Recommended by BS 845, ASME PTC-4 |
It’s particularly valuable when paired with efficiency monitoring systems, enabling continuous improvement.
In conclusion, the Indirect Method is a detailed, loss-focused approach to calculating boiler efficiency. It not only tells you how efficient your boiler is but, more importantly, why it isn’t more efficient. By identifying specific heat losses, it empowers engineers and operators to make targeted improvements—boosting performance, lowering emissions, and reducing fuel costs. For facilities serious about energy savings and compliance, the Indirect Method is an essential analytical tool.
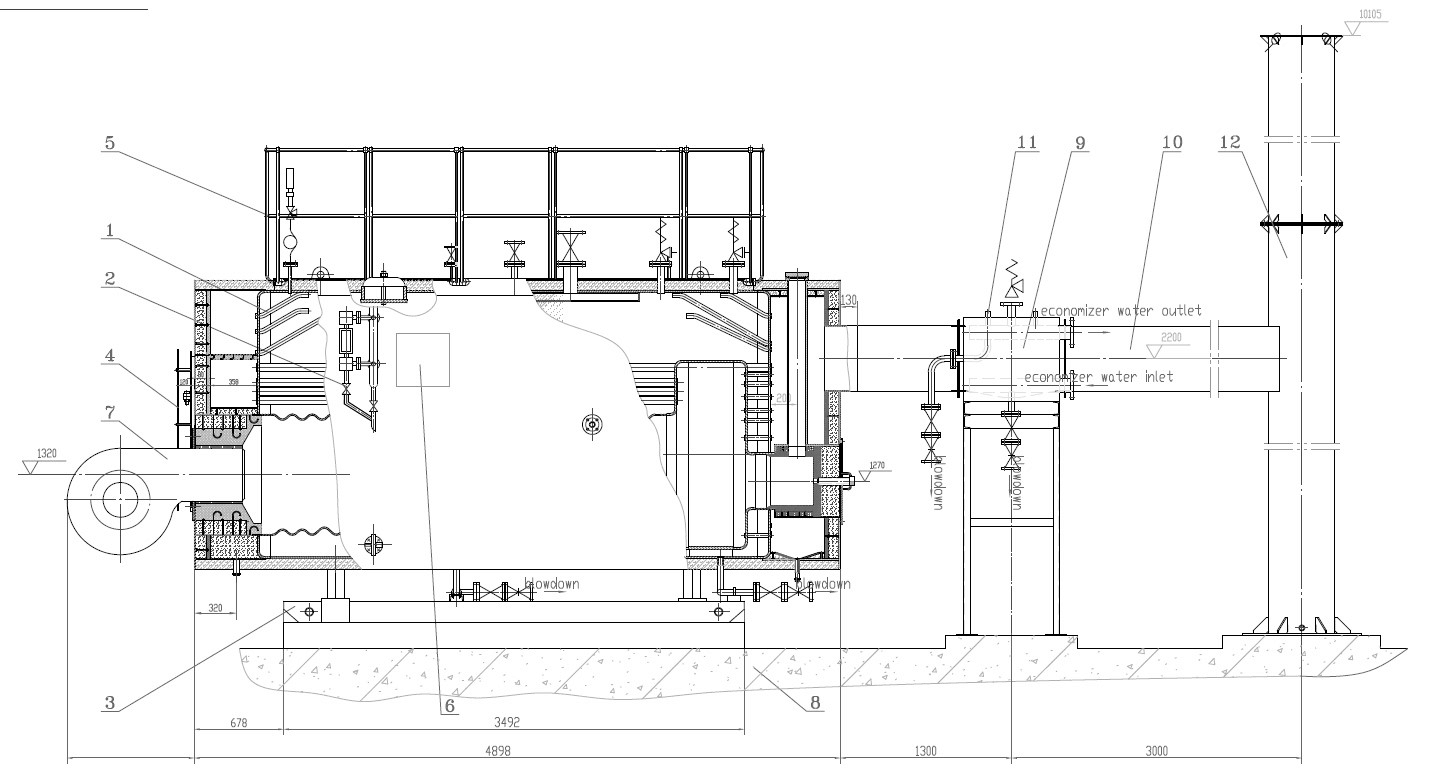
What Parameters Must Be Monitored for Accurate Thermal Efficiency Measurement?
In industrial boiler systems, thermal efficiency is a critical metric—it indicates how effectively fuel energy is converted into useful heat. But thermal efficiency is not a single value pulled from a chart. It’s the result of real-time measurements of multiple interrelated parameters. If any one parameter is inaccurate, the efficiency calculation becomes unreliable, leading to incorrect conclusions, poor fuel management, and regulatory risk. To ensure dependable results—whether using the Direct or Indirect Method—a precise set of measurements must be monitored continuously.
Accurate thermal efficiency measurement requires continuous monitoring of critical parameters including steam output, feedwater temperature, fuel consumption rate, flue gas temperature, flue gas oxygen (O₂) content, and ambient air temperature. Additional measurements such as fuel calorific value, combustion air flow, and CO/CO₂ levels are also essential for Indirect Method calculations. These parameters together provide the data needed to quantify both useful energy output and energy losses.
Boiler efficiency is not guessed—it is measured, monitored, and improved through reliable instrumentation and integrated data systems.
Accurate boiler efficiency measurement depends on monitoring parameters like fuel consumption, steam output, and flue gas conditions.True
Each of these values contributes to either the heat input or heat output of the boiler, making them essential for calculating thermal efficiency.
📋 Essential Parameters for the Direct Method
Parameter | Purpose | Required Instrument |
---|---|---|
Fuel Consumption Rate | Measures the amount of fuel input | Gas flow meter, oil mass meter, or weighing scale |
Fuel Calorific Value (CV) | Converts fuel quantity into energy | Lab test or online gas chromatograph |
Steam Flow Rate | Measures boiler’s useful heat output | Steam flow meter (turbine, vortex, or DP type) |
Steam Pressure and Temp | Determines enthalpy of generated steam | Pressure sensor + temperature sensor |
Feedwater Temperature | Determines energy required to produce steam | RTD or thermocouple at inlet |
Accurate instruments must be calibrated regularly to avoid cumulative errors in energy calculation.
🔍 Additional Parameters for the Indirect Method
Parameter | Purpose | Required Instrument |
---|---|---|
Flue Gas Temperature | Calculates dry flue gas loss | Thermocouple or infrared sensor |
O₂ Content in Flue Gas | Indicates excess air level and combustion efficiency | Zirconia O₂ analyzer |
CO/CO₂ Levels in Flue Gas | Detects incomplete combustion (for CO loss) | Infrared gas analyzer |
Ambient Air Temperature | Needed for accurate stack loss calculations | Digital thermometer |
Combustion Air Flow | Assists in air-fuel ratio control | Air flow meter (pitot tube or vane type) |
Carbon in Ash (solid fuels) | Indicates unburnt fuel in bottom ash | Lab analysis of ash samples |
These inputs allow engineers to compute specific losses and subtract them from 100% to determine net efficiency.
🧪 Case Example: High-Accuracy Monitoring for 10 TPH Gas-Fired Boiler
Parameter | Device Installed | Accuracy Level |
---|---|---|
Fuel flow (gas) | Thermal mass flow meter | ±1% |
Steam flow | Vortex flowmeter | ±1.5% |
Steam pressure/temp | Smart transmitters | ±0.5% |
Feedwater temp | RTD with transmitter | ±0.2°C |
Flue gas temp | Shielded thermocouple | ±2°C |
O₂ in flue | Zirconia sensor with auto-cal | ±0.5% |
Ambient air temp | Digital probe | ±1°C |
→ Resulting in efficiency monitoring resolution of ±0.5%, suitable for audit-grade verification.
🛠️ Recommended Monitoring System Architecture
Component | Role |
---|---|
Centralized Data Logger (DAS) | Collects and time-stamps all parameter values |
Real-Time Efficiency Software | Calculates and displays live efficiency values |
Alarm System | Triggers warnings if O₂, temp, or steam load deviate |
Cloud-Based Dashboard | Enables remote access and trend analysis |
CEMS Integration (optional) | Supports emissions-linked performance tracking |
This setup allows energy managers to optimize efficiency dynamically, not just reactively.
📊 Real Benefits of Monitoring Key Parameters
Impact Area | How Monitoring Helps |
---|---|
Fuel Cost Savings | Detects inefficiencies and excessive air usage |
Emission Compliance | Keeps NOₓ, CO, and SO₂ within limits |
Efficiency Optimization | Helps target blowdown, excess air, and scaling |
Predictive Maintenance | Detects burner degradation or fouling early |
Carbon Reporting Accuracy | Enables real-time CO₂ intensity tracking |
In modern boiler rooms, unmonitored performance is unmanaged performance.
In conclusion, accurate thermal efficiency measurement demands real-time monitoring of multiple critical parameters—from steam output and fuel input to flue gas composition and air flow. Both Direct and Indirect Methods rely on these values for correct analysis. Whether your goal is reducing fuel cost, minimizing emissions, or proving ESG compliance, robust parameter tracking is the foundation of a high-performance, compliant boiler system.
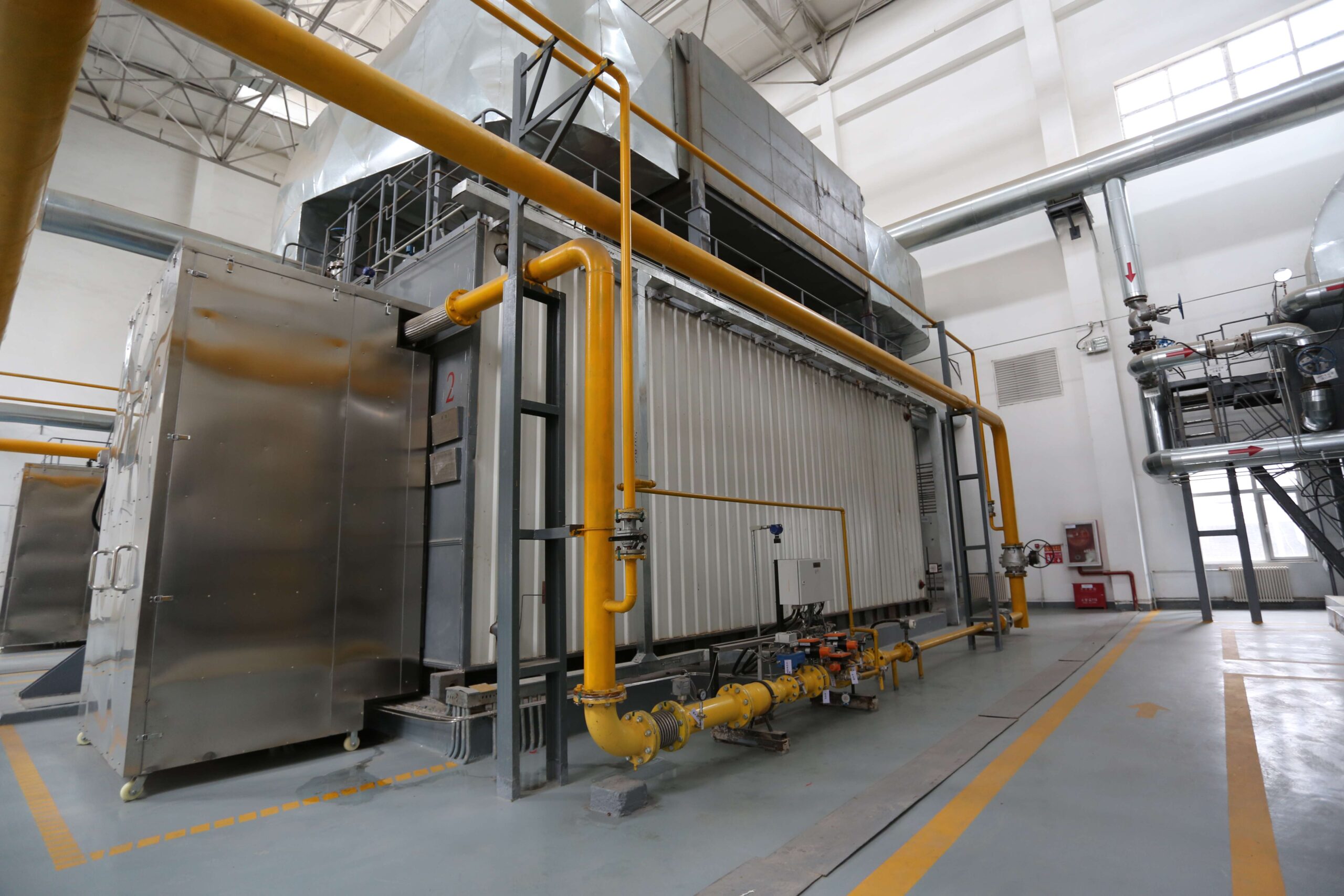
How Do Excess Air, Flue Gas Temperature, and Combustion Quality Affect Efficiency?
In a boiler system, every percentage point of efficiency counts—especially with rising fuel prices and tightening emissions regulations. Yet many industrial boilers suffer avoidable energy losses because of imbalances in excess air, elevated flue gas temperatures, and poor combustion quality. These three factors are tightly interconnected and directly influence how much of the fuel’s chemical energy ends up as useful steam—and how much is lost through the stack or incomplete burning. Understanding their effects is critical for achieving high thermal efficiency, low emissions, and stable boiler performance.
Excess air, flue gas temperature, and combustion quality significantly affect boiler efficiency. Too much excess air cools the flame and increases flue gas losses; high flue gas temperatures indicate unutilized heat escaping up the stack; and poor combustion quality leads to unburned fuel or carbon monoxide. Optimizing air-fuel ratio, reducing stack temperature through heat recovery, and ensuring complete combustion are key strategies for improving boiler efficiency.
Small inefficiencies in these parameters can result in major fuel losses and carbon emissions over time.
Boiler efficiency decreases with excessive excess air, high flue gas temperatures, and poor combustion quality.True
These factors contribute to increased heat loss and unburnt fuel, reducing the amount of energy converted into usable steam.
🌬️ 1. Excess Air and Its Impact
What Is It? | Air supplied beyond what is chemically needed to burn the fuel completely |
---|---|
Why It’s Used | Prevents incomplete combustion and reduces CO emissions |
Why It Harms Efficiency | Extra air absorbs heat and carries it away through the stack |
Optimal Excess Air Levels by Fuel Type
Fuel Type | Theoretical Air (%) | Practical Excess Air (%) | O₂ in Flue Gas (%) |
---|---|---|---|
Natural Gas | 100 | 5–10 | 2–3 |
Light Oil | 100 | 10–15 | 3–4 |
Biomass/Coal | 100 | 20–40 | 5–8 |
Too little air → CO and unburned carbon
Too much air → Flue gas energy loss
🛠 Correction Method: Install O₂ trim system to maintain ideal excess air levels automatically.
🌡️ 2. Flue Gas Temperature and Stack Loss
What It Indicates | Heat remaining in the exhaust gas that was not transferred to water/steam |
---|---|
Why It Matters | Every 20°C rise in stack temp can reduce efficiency by ~1% |
Ideal and Excessive Flue Gas Temperatures
Fuel Type | Normal Range (°C) | High-Loss Threshold (°C) |
---|---|---|
Natural Gas | 160–200 | >220 |
Oil | 200–250 | >270 |
Coal/Biomass | 200–300 | >320 |
Flue gas temp too high? → Consider economizer, air preheater, or condensing heat recovery.
🛠 Correction Method: Install a stack economizer or lower excess air to improve heat exchange.
🔥 3. Combustion Quality and Fuel Utilization
What It Means | How completely the fuel is burned in the flame zone |
---|---|
Why It’s Critical | Poor combustion wastes fuel and produces CO |
Indicators of Poor Combustion
Symptom | Likely Cause |
---|---|
High CO in flue gas | Incomplete combustion (lack of air, poor burner setup) |
Visible soot or smoke | Flame instability, unburned carbon |
Carbon in bottom ash | Unburnt solids in solid-fuel boilers |
🛠 Correction Method: Burner tuning, fuel atomization improvement, flame pattern adjustment.
CO/CO₂ Ratio as Combustion Indicator
Ratio (CO/CO₂) | Interpretation |
---|---|
<0.01 | Excellent combustion |
0.01–0.03 | Acceptable range |
>0.05 | Inefficient, fuel loss |
📊 Combined Impact on Boiler Efficiency – Example (10 TPH Gas Boiler)
Condition | Flue Temp (°C) | O₂ (%) | CO (ppm) | Efficiency (%) |
---|---|---|---|---|
Optimized Combustion | 180 | 2.5 | <10 | 91.5 |
Too Much Excess Air | 190 | 6.5 | <10 | 87.8 |
High Flue Temp (scale on tubes) | 245 | 3.0 | <10 | 85.4 |
Incomplete Combustion | 180 | 1.2 | 180 | 82.7 |
→ Efficiency loss from poor tuning can reach 8–10%.
🛠 Practical Optimization Strategies
Issue | Action |
---|---|
Excess air too high | Add O₂ trim control and tune burners |
Flue gas temperature too high | Install economizer, clean heat surfaces |
CO levels too high | Improve atomization, burner adjustment |
Combustion varies by load | Add PLC-based burner modulation |
✅ Regular audits using flue gas analyzers and thermal sensors can help maintain top efficiency.
In conclusion, excess air, flue gas temperature, and combustion quality are the three pillars of boiler combustion efficiency. By managing these factors through proper instrumentation, tuning, and heat recovery systems, operators can significantly reduce fuel consumption, emissions, and maintenance costs. High boiler efficiency is not accidental—it’s engineered and maintained through consistent control of these variables.
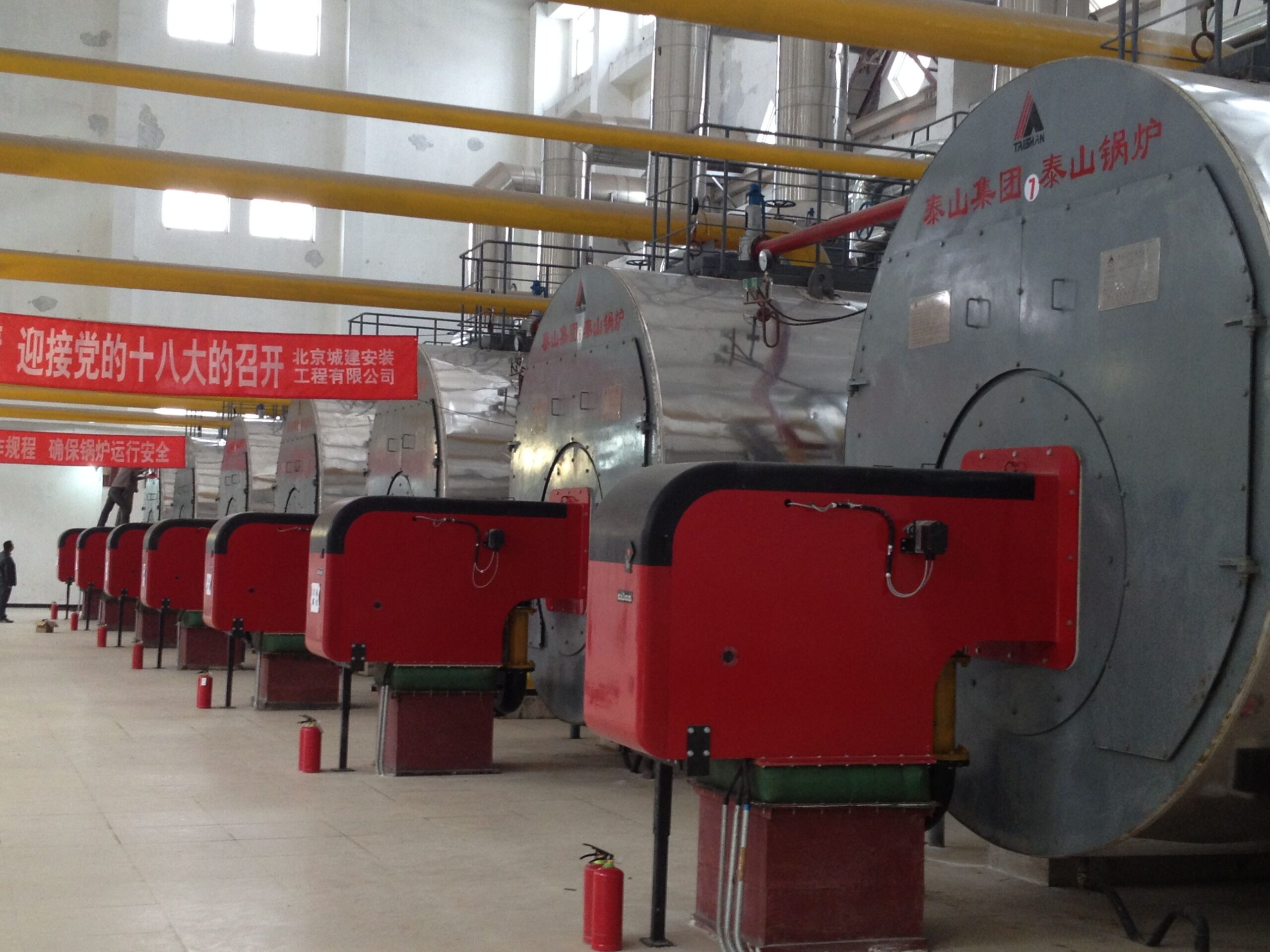
How Can Efficiency Data Be Used to Improve Energy Savings and Reduce Emissions?
In a world where fuel prices fluctuate and carbon reduction targets grow stricter, boiler operators can no longer rely on fixed schedules or assumptions to manage performance. Efficiency data is no longer a passive record—it’s a powerful tool. Capturing, analyzing, and acting on boiler efficiency data allows organizations to identify savings opportunities, prevent energy waste, and prove emissions compliance. Whether you’re burning gas, biomass, or coal, consistent monitoring and optimization based on actual performance data can transform an average boiler into a high-efficiency, low-emissions asset.
Efficiency data improves energy savings and reduces emissions by revealing real-time performance trends, highlighting inefficiencies like excessive flue gas loss or poor combustion, and enabling targeted actions such as burner tuning, heat recovery upgrades, and fuel optimization. When combined with emissions monitoring, efficiency data helps reduce fuel consumption per unit of output and lowers CO₂, NOx, and SO₂ emissions, supporting both cost savings and environmental compliance.
The difference between a compliant, profitable plant and a penalized one is often found in how well its efficiency data is understood and used.
Boiler efficiency data can directly reduce energy costs and lower emissions when analyzed and acted upon.True
Efficiency monitoring reveals energy waste, enabling targeted improvements in combustion, insulation, and heat recovery.
📈 What Efficiency Data Tells You
Efficiency Metric | What It Means | Action Triggered |
---|---|---|
Boiler Thermal Efficiency (%) | Ratio of useful output to fuel input | Overall performance tracking |
Flue Gas Temperature (°C) | Unused energy lost in exhaust | Suggests heat recovery upgrade |
Oxygen (O₂) Level (%) | Indicator of excess air | Suggests burner air-fuel tuning |
CO/CO₂ Ratio | Completeness of combustion | Suggests combustion optimization |
Steam-to-Fuel Ratio | Operational effectiveness | Identifies performance over time |
Fuel Consumption per Hour | Direct cost indicator | Detects leaks or underperformance |
Efficiency Trend (24h/weekly) | Shows when and how performance drops | Enables proactive maintenance |
This data forms the basis for predictive efficiency management.
🔧 How Efficiency Data Drives Energy Savings
Strategy | Efficiency Data Used | Result |
---|---|---|
O₂ Trim Optimization | O₂ %, CO levels | Cuts excess air losses (1–3% fuel saved) |
Heat Recovery System Tuning | Flue gas temperature | Lowers stack loss (2–5% gain) |
Burner Tuning & Modulation | Efficiency %, CO readings | Improves combustion stability |
Fuel Mix Adjustment (Co-firing) | Steam/fuel ratio, emissions trends | Reduces high-carbon fuel consumption |
Load Matching | Efficiency vs. load graph | Avoids low-efficiency part-load operation |
Steam Leak Detection | Fuel use vs. output | Eliminates silent energy waste |
Even minor changes in combustion settings can unlock thousands of dollars in annual fuel savings.
🧪 Real-World Example: Textile Plant with 6 TPH Gas Boiler
Baseline Thermal Efficiency: 82.4%
Installed Monitoring Tools: Steam flow meter, fuel meter, flue gas analyzer
Actions Taken Based on Data:
Tuned burners to lower excess air (O₂ reduced from 5.5% to 2.8%)
Installed stack economizer (flue temp drop: 240°C → 175°C)
Set load-based burner modulation
New Efficiency: 90.1%
Results:
Gas savings: 96,000 m³/year
CO₂ reduction: 190 tons/year
Cost savings: ~$38,500/year
Payback on upgrades: 18 months
🌍 Environmental Impact of Data-Driven Efficiency
Action | Emission Reduced | Efficiency Link |
---|---|---|
Reduce excess air | ↓ NOₓ and CO₂ | Combustion optimization |
Improve heat recovery | ↓ CO₂ and flue temp | Uses more fuel energy, lowers emissions per MWh |
Tune burners | ↓ CO, PM, unburned HC | Complete combustion = cleaner exhaust |
Reduce fuel use per ton steam | ↓ CO₂, SO₂ | Higher efficiency = less fuel burned |
Efficiency is the most cost-effective way to cut emissions—especially in existing infrastructure.
📊 Efficiency Dashboard Example – 10 TPH Biomass-Fired Boiler
Metric | Week 1 | Week 4 | Trend | Action Taken |
---|---|---|---|---|
Thermal Efficiency (%) | 79.2 | 84.3 | ↑5.1% | Replaced insulation |
Flue Gas Temp (°C) | 275 | 198 | ↓77°C | Cleaned heat surfaces |
O₂ Level (%) | 6.4 | 3.1 | ↓3.3% | Burner retuned |
Fuel per ton steam (kg) | 134 | 121 | ↓9.7% | Steam trap audit |
→ Efficiency monitoring translated directly into measurable fuel and emissions savings.
🛠 Tools for Turning Efficiency Data Into Action
Tool | Role |
---|---|
Real-Time Monitoring System | Tracks and trends key metrics continuously |
Flue Gas Analyzer | Provides combustion efficiency insights |
Steam/Fuel Flow Meters | Verifies output/input ratios |
Smart Boiler Controls | Automates air-fuel ratio adjustment |
Cloud Dashboards | Enables energy management benchmarking |
When linked to maintenance and operations teams, this data enables teamwide accountability for performance.
In conclusion, efficiency data is not just a report—it’s an operational asset. When properly monitored and analyzed, it provides clear direction for energy savings, lower emissions, and better boiler performance. For any plant aiming to reduce fuel costs and comply with climate targets, turning efficiency data into action is one of the most impactful and cost-effective steps you can take.
🔍 Conclusion
Measuring the thermal efficiency of an industrial gas-fired boiler is a critical part of effective boiler management. Whether using the Direct or Indirect Method, understanding how much fuel energy is being converted into useful heat allows operators to fine-tune combustion, reduce energy costs, and meet sustainability goals. A systematic approach to efficiency monitoring helps ensure your boiler runs at peak performance with minimal waste.
📞 Contact Us
💡 Need help optimizing your gas-fired boiler efficiency? Our technical team provides on-site assessments, combustion tuning, and real-time monitoring solutions tailored to your facility’s needs.
🔹 Reach out today to boost your gas boiler’s efficiency and fuel economy with expert support! 🔥📊✅
FAQ
What is thermal efficiency in an industrial gas-fired boiler?
Thermal efficiency is the ratio of useful heat output (usually as steam or hot water) to the total heat input from the fuel. In gas-fired boilers, it reflects how effectively natural gas is converted into usable thermal energy.
Which methods are used to measure the thermal efficiency of gas-fired boilers?
The two standard methods are:
Direct Method (Input-Output Method)
Indirect Method (Heat Loss Method)
Both are recognized under standards such as ASME PTC 4 and ISO 16528.
How does the Direct Method work?
The Direct Method calculates efficiency as:
Efficiency (%) = (Steam Output × Enthalpy Gain) / (Fuel Input × Calorific Value) × 100
This method is straightforward and fast but does not provide insights into system inefficiencies.
What is the Indirect Method and when is it used?
The Indirect Method involves calculating various heat losses (e.g., dry flue gas loss, moisture loss, unburnt fuel, radiation losses) and subtracting them from 100%.
Efficiency (%) = 100 – (Total Heat Losses)
This approach helps identify inefficiencies and supports long-term performance optimization.
Why is efficiency monitoring critical for gas-fired boilers?
Regular thermal efficiency measurement helps reduce fuel consumption, lower operating costs, optimize combustion, and ensure compliance with emissions regulations. It’s also vital for predictive maintenance and energy audits.
References
Boiler Efficiency Measurement Standards – https://www.energy.gov
ASME PTC 4 on Fired Steam Generators – https://www.asme.org
Boiler Heat Loss Analysis – https://www.sciencedirect.com
Gas Boiler Combustion Efficiency Guidelines – https://www.epa.gov
Direct vs. Indirect Efficiency Methods – https://www.researchgate.net
Steam Generation and Performance Optimization – https://www.mdpi.com
Industrial Boiler Energy Auditing – https://www.iea.org
Gas-Fired Boiler Operational Best Practices – https://www.bioenergyconsult.com
Automation in Boiler Efficiency Monitoring – https://www.automation.com
Improving Fuel Efficiency in Boilers – https://www.energysavingtrust.org.uk
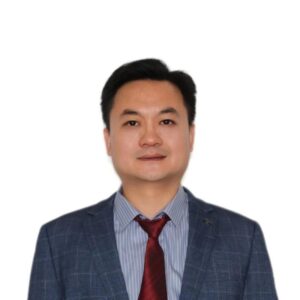